Daily press, 2020-03-10, 03:30 pm
Innovative oxygen technology for the blast furnace process: Sequence impulse process with induced shockwaves (SIP)
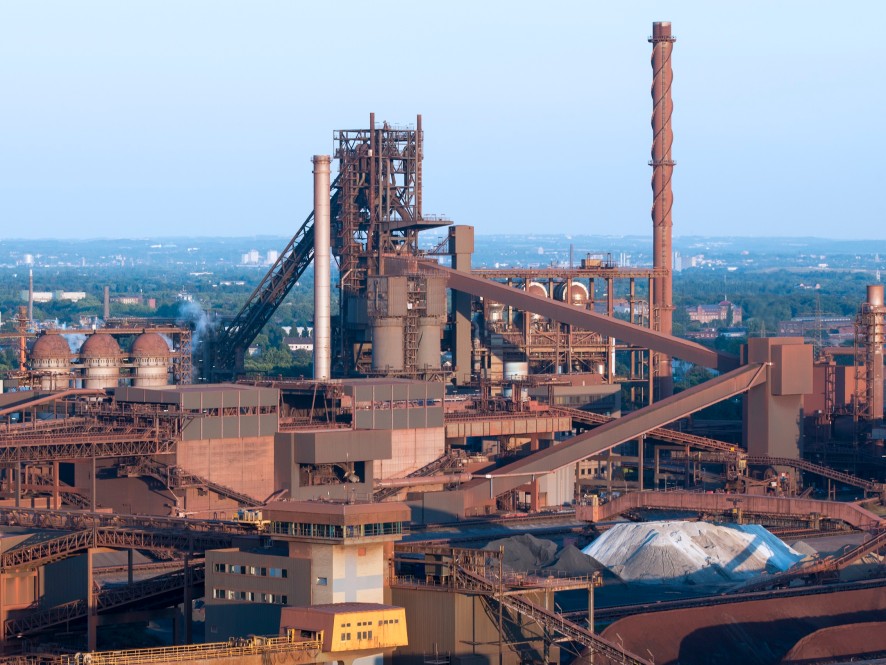
- New process developed by thyssenkrupp
- Blast furnace in Duisburg the world’s first equipped with this technology
- Contribution to climate protection
In Duisburg thyssenkrupp is testing the “sequence impulse process with induced shockwaves”, a new blast furnace technology designed to enhance process efficiency. One of the aims is to help reduce CO2 emissions – both at the company’s own plant and around the world by marketing the technology globally. Following extensive research and development, the world’s first SIP system has now been installed in blast furnace Schwelgern 1 and will serve as a reference plant for marketing.
New process with great potential
The research, carried out by thyssenkrupp AT.PRO tec GmbH, a company of thyssenkrupp Materials Trading GmbH, and thyssenkrupp Steel Europe, has resulted in an innovative oxygen injection process tailored specifically to the blast furnace process.
“Process development work was focused on the “deep action” of the oxygen. The aim is to improve gas and liquid flows in the blast furnace and thus improve efficiency. We based this on our knowledge and the targeted use of various gas-dynamic phenomena in the oxygen injection process,” explains Dr. Rainer Klock, Manager Furnace Metallurgy at thyssenkrupp Steel Europe’s Schwelgern blast furnace plant.
Technically this is realized by fitting each of the 40 tuyeres on blast furnace 1 with an additional lance for oxygen injection. The 40 lances each have their own injection unit or “SIP box”.
“I am delighted that with Schwelgern 1 we have been able to install our SIP technology in one of Europe’s biggest blast furnaces,” says Gerd König, managing partner of thyssenkrupp AT.PRO tec GmbH. “We will soon be able to deliver reference values to demonstrate the profitability of the technology and show how it optimizes blast furnace processes.”
Jörg Glebe, managing director of thyssenkrupp AT.PRO tec GmbH, is optimistic about the results of the research and tests carried out in cooperation with RWTH Aachen University: “Improving the efficiency of the blast furnace process optimizes the consumption of coke and pulverized coal as reducing agents. This lowers CO2 emissions and reduces costs. Replacing five kilograms of coke with pulverized coal per ton of pig iron in blast furnace Schwelgern 1 would already result in potential annual cost savings in the millions.”
Outlook: Global marketing
The technology is already meeting with wide interest. Talks are currently being held with major plant engineering companies. The aim is to launch the process worldwide and support installation in blast furnaces. “We believe our development has great commercial potential and are confident that it will quickly become established on the global market,” says Wolfgang Schnittker, CEO of thyssenkrupp Materials Trading.
Contribution to climate strategy for steel production at thyssenkrupp
thyssenkrupp is aiming to achieve climate neutrality in its steelmaking operations by 2050. As an initial target the company plans to reduce emissions from its own production and processes and from purchased energy by 30 percent versus the base year 2018 by 2030. Carbon direct avoidance (CDA) is one of two routes the company is pursuing with its strategy. In a next step, the blast furnaces are to be converted in part to hydrogen injection. To exhaust all possibilities for optimizing blast furnace technology, thyssenkrupp is testing the new “sequence impulse process with induced shockwaves” oxygen injection system on the Schwelgern 1 blast furnace.