Intelligent and connected processes
Despite digitalization: steel remains steel
The necessary changes are much easier to make in administration than in production, where the introduction of smart IT solutions is often based on the investment cycles of the systems. “The focus in specialist and administrative departments is on increasing the efficiency of business processes. Apps, digital workflows and smart assistants have long been integrated into the digital infrastructure here,” says Lang. One example is the introduction of low-code platforms and citizen development. This approach enables all employees to independently develop simple applications and bots that make their daily tasks easier and thus actively contribute to the digital transformation. “In production, on the other hand, the focus is on stable processes, system availability and quality,” he emphasizes. “And here, too, a lot has already been achieved in recent years through the consistent implementation of numerous digitalization projects.”
However, one thing is clear: the core product steel will remain a physical quantity in the future. And yet digital technologies will play a key role in its production and marketing more than ever before. Lang: “Steel is a proven high-tech material that has been produced at thyssenkrupp Steel for decades in ever more optimized, highly automated production steps.” Thanks to the continuous advance of digitalization, the company is now able to collect and evaluate millions of pieces of data in real time across all sites and plants along the entire value chain using sensors and actuators.
Digitization improves competitiveness
The big data approach is not an end in itself, but contributes directly to transparency. “Today, we offer our customers unprecedented traceability of their orders. The detailed insights give them a clear competitive advantage and enable them to optimize production processes and quality. With the help of data analytics, for example, material properties can be predicted more precisely and tolerances can be set more accurately,” says Lang. The data treasures, which at thyssenkrupp are based on 15 years of data history in some cases, also give engineers and data scientists the opportunity to develop and train new AI models in order to leverage further potential in production. “At thyssenkrupp Steel, we're talking about a huge scale due to our production history. Even small improvements in detail help to achieve an enormous impact in the end.”
The same applies when it comes to meeting regulatory requirements for steel producers. For example, in the area of sustainability, where the carbon footprint of products is becoming increasingly important for customers and end consumers. Volker Lang knows: “Anyone who cannot provide transparency in the form of digital data on CO2 emissions along the value chain will be at a clear competitive disadvantage in the long term.” The steel producer is therefore also involved in the development of so-called data spaces, in which data can be exchanged securely and confidently across company boundaries. This is of great importance for many industries with independent and geographically separate production processes. One example is the Catena-X Automotive Network, a project in which the Fraunhofer Institute for Software and Systems Engineering (ISST) is playing a key role. Here, the targeted collation of data from all participating companies enables automotive manufacturers to meet the documentation requirements of the German Supply Chain Management Act, for example.
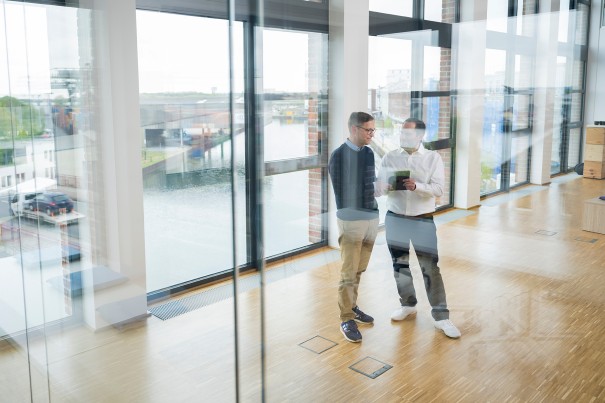
thyssenkrupp Steel is making a decisive contribution to achieving such improvements. This is how Professor Boris Otto from Fraunhofer ISST in Dortmund sees it: “The location in the middle of the Ruhr region offers the opportunity to continue developing and selling physical products. These now need to be successively supplemented with digital services that increase added value for customers.” Otto continues: “The Ruhr region has always been the industrial heart of Germany. But it is also a digital powerhouse: we have various universities within a 50-kilometer radius, where thousands of students are studying subjects such as IT and logistics. This is exactly where the digital services that industry needs are created.” Volker Lang takes a similar view: “We don't have to travel to Silicon Valley or Tel Aviv to see how digitalization works. We can do it here too. We have a strong university scene here and the right use cases.” For the CIO, the next step is for the technologies that are available around the world to arrive at thyssenkrupp Steel and develop their benefits on the ground. “At the core is always the idea of optimizing and improving ourselves - that's what steel production is all about.”