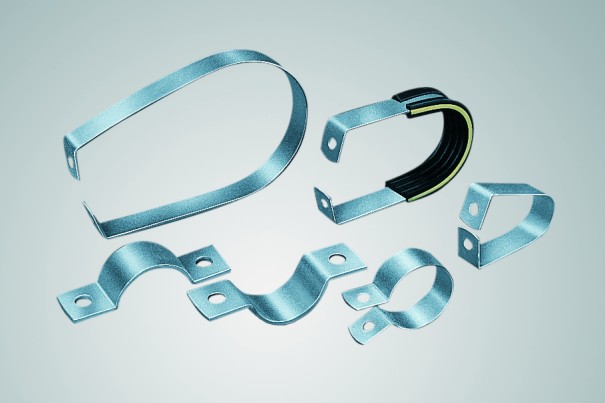
As well as very good coating adhesion and outstanding corrosion resistance, hot-dip galvanized strip offers good forming properties, which are greatly influenced by the thickness of the zinc coating.
Its uses are many and varied: from gutter brackets and profiles with low coating weights and good formability, to roller shutter doors, building hardware, pipe brackets and barrel hoops with normal corrosion resistance and straightforward forming, to lightning conductors and earthing strips with increased corrosion protection and low formability requirements.
Available steel grades
Steel family | Steel grade name |
---|---|
Mild steel for cold forming, DIN EN 10111 | DD11, DD12 |
General structural steel, unalloyed, DIN EN 10025-2 | S185, S235, S275, S355 |
Available ordering groups and zinc coatings
Zinc coating weight in [g/m2] | ||
---|---|---|
Ordering group | Average value | Single spot test |
Z120 | 120 | 95 |
Z160 | 150 | 120 |
Z226 | 225 | 180 |
Z300 | 300 | 240 |
Z400 | 400 | 320 |
Z600 | 500 | 400 |
Sizes
Product form | THICKNESS from_to in mm |
WIDTH from_to in mm |
LENGTH from_to in mm |
---|---|---|---|
Coils | 1.40 – 6.00 | 15 – 200 | - |
Cut lenghts | 1.40 – 6.00 | 15 – 120 | 500 – 7,500 |
Notes on applications and processing
Corrosion protection
Applying a zinc coating to hot-rolled strip provides good general protection and ideal corrosion protection. The advantage of hot-dip galvanized narrow strip is that the edges are also coated. The protective effect is based on the relative positions of zinc and iron in the electrochemical series. As zinc is less noble than iron, it is attacked first by environmental influences such as humidity, sacrificing itself and preventing the oxidation process on the steel surface.
However, overall corrosion behavior depends on various factors, such as temperature, electrical conductivity of the electrolyte, and the thickness of the top coat. Corrosion behavior can only be assessed taking the interaction of all these factors into account separately for each different application.
In general, the thicker the zinc coating, the greater the corrosion protection.
Forming
Hot-dip galvanized narrow strip displays good forming proper-ties. When selecting the coating thickness it should be noted that formability improves with decreasing coating thickness. The choice of material is based on the forming requirements and the final shape of the workpiece. Forming dies need to be adapted because the zinc coating displays different physical properties. Draw-in radii and die clearances must be larger than for uncoa-ted material.
The use of sinter metals or specially treated die surfaces can reduce the risk of cold welding. Drawing lubricants are generally required when forming hot-dip galvanized narrow strip, and machine parameters such as blankholder force must be matched to the different flow properties of the coated material.
Joining
All thermal and mechanical joining methods can be used, as can adhesive bonding. However, the particular properties of the Z coat-ing require the processing parameters to be adapted compared with uncoated materials. Joining techniques which do not impair the surface of the strip and thus preserve the anticorrosion prop- erties of the coating include threaded connections, riveting and hemming. The problem of contact corrosion between different materials must be addressed on a case-to-case basis.
Welding
When using fusion welding processes, the zinc coating burns off locally in the weld zone, exposing the surface areas below, which then have no corrosion protection. Suitable post-treatment of the weld is required to counter environmental influences. Laser weld-ing has proven to be a very good fusion welding process due to its low heat input into the weld zone. Resistance welding methods can also be readily used because the original protection remains largely intact. However, compared with uncoated material, elec-trode force, electrode current and electrode cooling need to be adjusted to take the factors steel grade, strip thickness and zinc coating thickness into account.
Brazing
Hot-dip galvanized narrow strip is readily brazable. The great advantage of brazing is that the corrosion protection is retained in full because the vaporization temperature of zinc is higher than the melting points of soft and hard solder. The zinc coating must be treated with a suitable flux in preparation for brazing. Here too, the increased thickness of the coating must be taken into account.
Coating
An organic coating can be applied to the hot-dip galvanized nar-row strip for enhanced corrosion protection and/or for decorative reasons. The zinc coating provides good adhesion properties, which can be further improved by a chemically passivated sur-face. Thorough cleaning with a special cleaning agent and activa-tion of the surface are necessary to avoid adhesion problems.