Hot rolled steel strip is the raw material for the production of packaging steel. This hot rolled wide strip, also called “hot strip”, is 1.5 mm to 3.8 mm thick. It is supplied in coils weighing between 6 and 28 metric tons.
Process routes
From hot strip to packaging steel
Hot rolled strip is the base material for the production of packaging steel. By cold rolling, it is brought to the required thickness and then finished by applying a coating of tin or chromium by means of an electrolytic process.
The exact process route can be seen from the diagram. By clicking on the individual illustrations you can trace the production flow of rasselstein® packaging steel step by step.
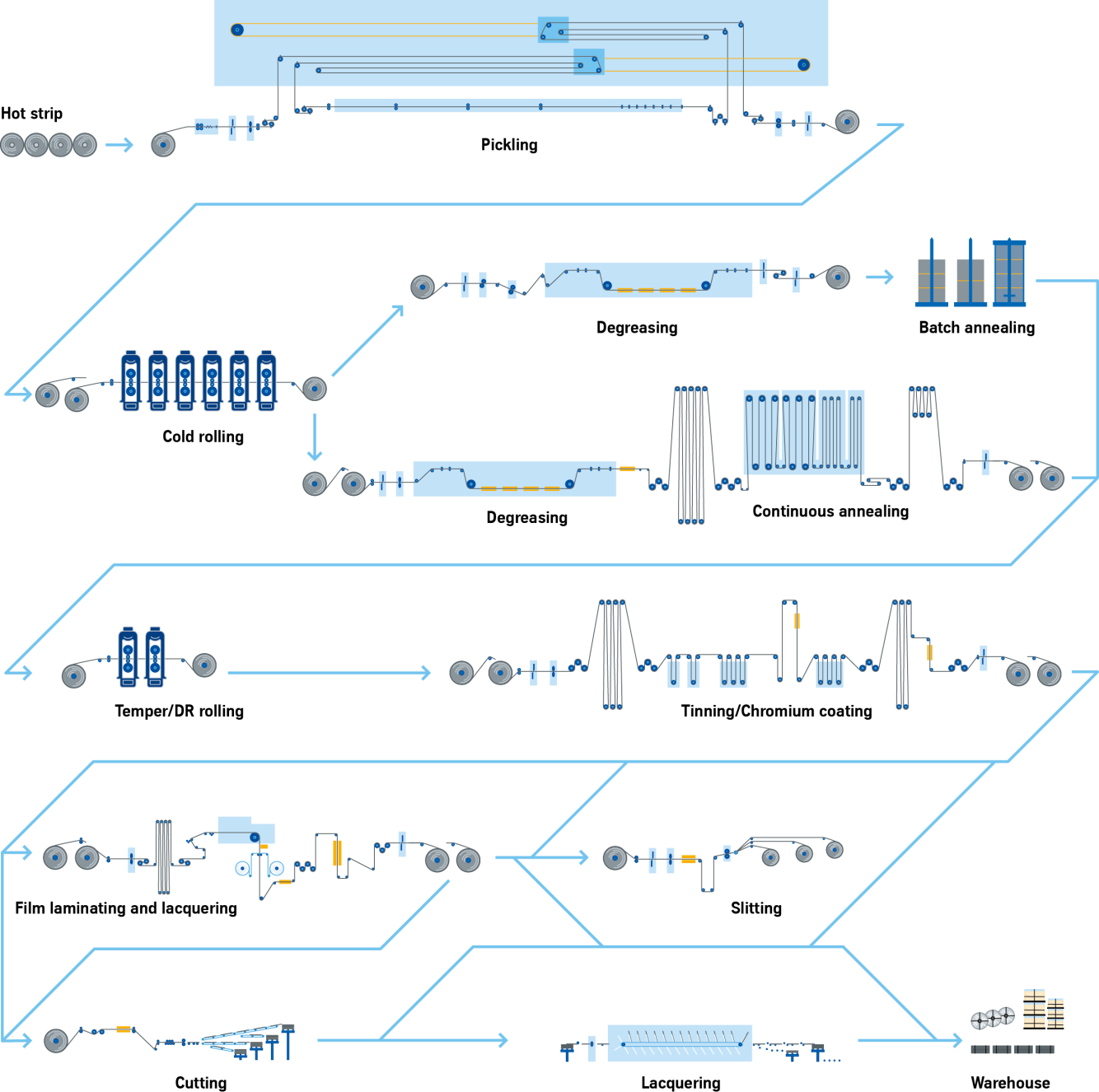
The process begins with pickling of the hot strip. The scale formed during hot rolling is removed in a continuous pickling line.
The pickling agent is sulfuric acid used in concentrations of around 20 percent at temperatures of around 98 °C. After pickling, the endless strip is oiled to prevent corrosion, slit and recoiled before being rolled again in one of the two tandem cold rolling mills.
thyssenkrupp has a five-stand and a six-stand tandem cold rolling mill in Andernach. They consist of five or six four-high stands in tandem, in which the strip is rolled between two work rolls. Because of the high rolling forces the work rolls are supported by large-diameter back-up rolls.
The length of the steel strip increases during cold rolling according to reduction in thickness in the individual stands. To achieve major deformation (thinner thicknesses) at high speed, the roll gap is lubricated with a mixture of rolling oil and water.
During rolling, the strip thickness is often reduced by more than 90 percent. The strain hardening incurred during this process must be removed by annealing.
Before annealing, the strip must be cleaned of contaminations. For this purpose, thyssenkrupp has two degreasing lines.
Recrystallization annealing of the degreased strip restores the necessary ductility. Two processes are available for this purpose. For a given analysis, batch annealing achieves a softer material than the continuous annealing process.
The crystal structure of the strip, which is destroyed during cold rolling, is restored in batch annealing, a treatment lasting several days that includes heating and cooling. Several coils stacked one on top of the other are placed on a base and covered with an inner cover and a furnace cover.
In the continuous annealing process, a continuous strip is rapidly passed through a furnace containing a protective atmosphere. For a given steel analysis, strip annealed in the continuous furnace is somewhat harder than material which has been batch annealed.
The strip passes through the furnace section in vertical loops. The dwell time in the annealing furnace is less than two minutes.
The essential advantage of this annealing process is the uniform grain size across the entire length and breadth of the coil. This is the prerequisite for achieving highly homogeneous material properties and ensuring consistently stable and smooth processing in your production facilities.
Although the crystal structure has been restored by the recrystallization annealing process, the annealed material cannot yet be used for fabrication into steel packages, since this would result in heavy kinks and non-uniform forming behavior (occurrence of Lueders lines).
In order to give the strip the necessary forming properties, the annealing process is followed by dry rolling, also called temper rolling. The overall reduction varies from 0.4% to 2.0%, depending on application purposes.
Two of the three temper rolling mills can also perform wet temper-rolling and are capable of reducing the thickness by up to 43%. For you, this double-reduced steel (DR) means a saving of material, because lower thicknesses are compensated by higher strength.
In the tinning lines, the steel strip passes through a tin-containing electrolyte. It functions as a cathode running between two banks of tin anodes. The tin of the anodes is dissolved electrolytically and is then deposited on the strip. Tin can be electrolytically deposited in any required thickness and, if necessary, with different coating thicknesses on each side. The bright luster of the tin-coated steel is obtained by heating the strip above the melting point of tin and quenching the material in water.
The high adhesion of the tin coating achieved by this reflow process improved the corrosion resistance, which can be optimized still further by a chemical posttreatment called passivation.
Special electrolytically chromium coated steel (TFS) is produced in a similar process to tinning. It can be used in all applications that do not need welding.
In addition to tinned and electrolytically chromium coated material, thyssenkrupp also offers you polymer-coated packaging steel.
The bare strip is then coated with a film of polymer (PET or PP) on one or both sides.
It is also possible to have a single-sided PP film coating combined with lacquer on the other side, or to produce material coated on one side only, allowing you to lacquer or print the uncoated side in your own facilities.
More and more, packaging steel is ordered by customers for delivery in coils. If not, the product is cut to length as desired on cutting lines or cut into scrolled sheets on a scroll cutting line.
Narrow strip in coil form is produced by slitting.
More and more, packaging steel is ordered by customers for delivery in coils. If not, the product is cut to length as desired on cutting lines or cut into scrolled sheets on a scroll cutting line.
Narrow strip in coil form is produced by slitting.
For sheet lacquering, thyssenkrupp has a line that can lacquer up to 6,000 sheets per hour.
It is possible to have single-sided, double-sided, single-layer or multi-layer, partial or full-surface lacquering.
All products are carefully packed before shipment. The favorable location of our Andernach plants allows us to deliver tinplate and blackplate quickly to any destination in the world.