Maximum part reliability with five letters: AS Pro
AS Pro – the next generation of hot forming
With AS Pro, thyssenkrupp Steel is the first steel manufacturer to launch a new, game-changing coating for hot forming ultra-high-strength MBW® steels worldwide – to ensure maximum automobile component reliability.
thyssenkrupp Steel does more than simply deliver the right materials; as a pioneer of hot forming, it also develops solutions that offer the customer the best available benefits. This means the latest innovation, AS Pro, guarantees highly reliable components and processes in automotive manufacturing. The new coating ensures significantly lower process-related hydrogen absorption during the annealing process in hot forming, and also makes the manufacturing process more economical.
“As partners of the automotive industry, we see ourselves as drivers of innovation who know the challenges involved in hot forming and support our customers with solutions,” says Georgios Giovanakis, Head of Sales at thyssenkrupp Steel. “Thanks to our AS Pro-coated hot-formed steels, we can now put an end to energy-intensive, time-consuming extra measures that are normally needed in the hot forming process.”
New alloying concept for hot forming
AS Pro is produced in thyssenkrupp Steel’s modern hot-dip galvanizing lines just like a standard aluminum-silicon coating. Unlike the standard AS coating, a pinch of magnesium is added to the aluminum and silicon in the melt pool, which is then distributed homogenously both in the melt and in the coating. “This little tweak in the chemistry makes a considerable difference in the hot forming process,” says Rüdiger Schorn, Product Manager for Heat Forming at thyssenkrupp Steel.
This is because AS Pro ensures that significantly less diffusible hydrogen is produced during the annealing process, which can force its way into the material. This minimizes the risk of hydrogen-induced cracks forming, which can occur in the event of a worst-case-scenario combination of strength and pressure when the content level of hydrogen is critical.
Demonstrably less hydrogen in the material
“The results produced with AS Pro are impressive,” says Schorn. Tests conducted in series production plants prove that the hydrogen content in a component after hot forming is reduced by 40 percent or more. Hydrogen absorption can even be reduced by up to 70 percent in cold re-rolled material. “Thanks to our new coating for hot forming ultra-high-strength materials, cost-intensive countermeasures to reduce hydrogen will no longer be needed in the future.”
The properties involved in the further processing of AS Pro are also comparable with the standard product. Joining processes such as laser welding and resistance spot welding can be used as usual, while the abrasion properties remain completely unaffected and the component is still easy to paint.
“Materials coated with AS Pro are available to our customers worldwide,” says Schorn. “The failure risk goes down, process reliability goes up, and the energy and manufacturing costs are optimized long-term. And all this without any process adjustments or changes to properties involved in further processing.” In short: MBW® manganese-boron steels from thyssenkrupp Steel in combination with AS Pro are a milestone in the hot forming of weight-optimized structural components whose behavior is critical in the event of a crash in automotive manufacturing.
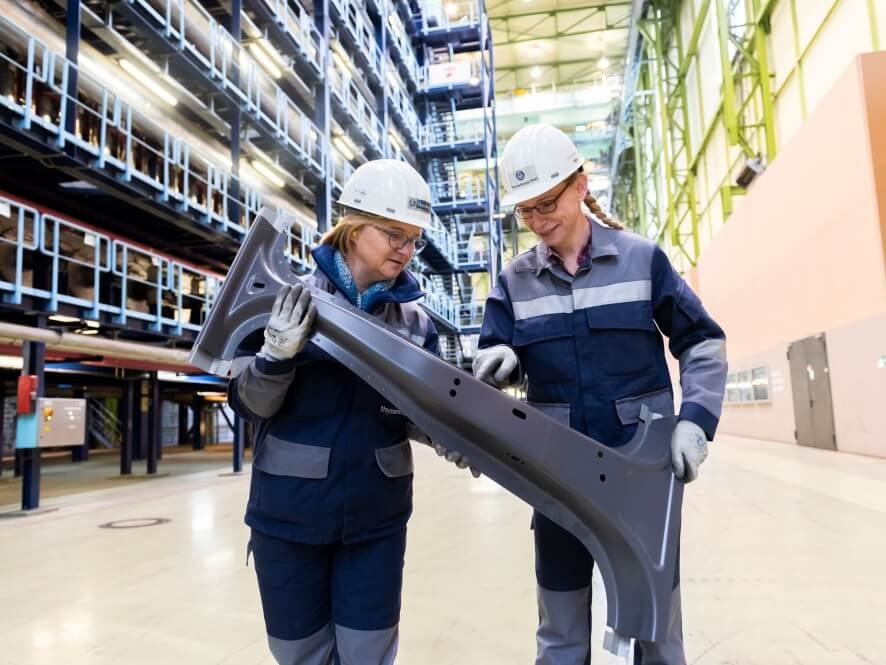
Maximum safety in the process
How do you develop a new, groundbreaking surface for hot forming? You do what thyssenkrupp Steel did with AS Pro.
Anyone who knows anything about hot forming is familiar with this challenge: during the heat treatment of aluminum-silicon-coated (AS) steels, hydrogen can force its way into the material. In the worst-case scenario, this can then lead to the hydrogen-induced failure of the part. The current solution strategies to minimize these failure risks only focus on the process, but these are energy- and cost-intensive.
As a result, thyssenkrupp Steel, as a pioneer of hot forming and partner to the automotive industry, is always looking for ways to solve problems and conducts research for its customers. This resulted in a technical solution that leads to a significant increase in process stability, even under the most critical of conditions. Its name: AS Pro.
In the beginning is the annealing process
“The tendency of hydrogen to embed itself into the steel during the annealing process on the customers’ premises is dependent on the process,” explains Manuela Ruthenberg. She is a Technical Project Manager in Product Development for Steel Coatings at thyssenkrupp Steel, and is responsible for the AS Pro project. “This is because the high temperatures in the atmosphere of the furnace lead to the surface reacting with the steam.”
With standard AS, oxygen reacts with the aluminum and primarily produces aluminum oxide. With AS Pro, excessive magnesium oxide is produced due to the high oxygen affinity of magnesium. “A thin coating of oxygen forms on the surface in both cases.” The crucial difference: “Significantly less hydrogen is produced with AS Pro-coated MBW® steels than with standard AS-coated hot-formed steels while this reaction is taking place. Consequently, less diffusible hydrogen is available to force its way into the material.”
Once hydrogen has forced its way into the material, it also needs to leave it again. This is because exceeding a critical amount of hydrogen combined with high pressures and high strengths can cause failures. Up to this point, the moisture is strenuously reduced from the atmosphere in the furnace using a dew point control.
Another possibility is heating the finished component to the point where it contains very little hydrogen. This requires for more than 30 minutes in a furnace at around 200°C. “This releases the hydrogen that has embedded itself in the microstructure,” say Reimann. “Both options, dew point control and effusion annealing, are energy- and cost-intensive. With our new AS Pro coating, our customers will be able to dispense with both methods in the future.”
Reducing process costs while maximizing component reliability
This is a groundbreaking development in hot forming. Particularly in automotive manufacturing, hot-formed steels in combination with AS Pro represent a milestone in the production of weight-optimized structural components whose behavior is critical in the event of a crash. “If, in the future, the critical phase in the annealing process can be eliminated, the failure rate will fall,” says Ruthenberg. Process reliability for the manufacturers will increase, and, in addition, lasting energy savings can be made. “The process windows will also grow for the processing companies – an advantage that should not be underestimated.”
AS Pro surface coating: confirmation in series production plants
The AS Pro concept was tested in the Technology and Innovation division at thyssenkrupp Steel during the course of many operational tests and checks. In addition, the hot forming processes were recreated on the customers’ premises – including those that required long periods in the furnace, for example.
“We took all the unpredictable factors into account, and can now say, following our comprehensive investigations, that our new AS Pro coating keeps its promise, even in series production plants,” says Ruthenberg. The same goes for further processing. “Our new coating offers at least comparable processing qualities to surfaces treated with the standard AS. Whether this is laser or resistance spot welding, or painting, none of these processing steps require any adjustments to their process on the customers’ premises. AS Pro-coated steels are also corrosion resistant, just like our standard AS coating.”