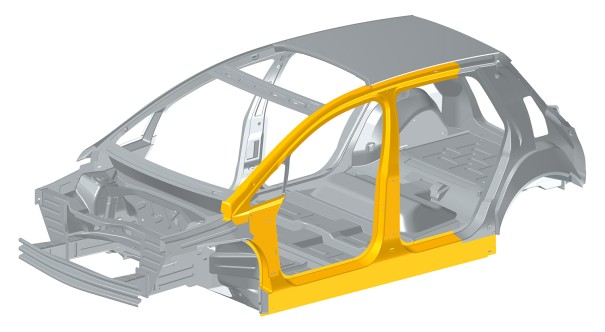
Application examples of hot-stamped components in the car body
Be it hot-stamped door ring concepts in our selectrify® reference structure for electric vehicles or components like A- and B-pillars, front and rear side members, crossmembers, tunnels or seat cross members, thyssenkrupp Steel offers a full-range of grades and dimensions of MBW® steels for hot forming, such as e.g. MBW® 1200 or MBW® 1500, which are ideal for tailored customer production processes like welded blanks, partial press hardening (Tailored Tempering in the die or in the hot forming furnace), flexible rolling or the use of patched blanks.
Wide range of hot forming steels – MBW® product highlights
Our manganese boron steels for hot forming offer strengths from 500 to 2,000 MPa after press hardening. The two AS-coated grades MBW® 500 and MBW® 600 are the perfect materials for customized blanks to obtain a combination of maximum strength and ductility in a component which are tailored to the stresses to which it will be subjected.
The coated standard hot forming grade MBW® 1500 is characterized by a high deformation resistance and is ideally suited for crash-relevant components of the passenger cell. The range of products is rounded off by the also AS-coated MBW® 1200. This new steel grade features an excellent weld point performance in the event of a crash. Cost-intensive tempering treatment in the flange area is therefore not necessary. The MBW® 1200 steel meets higher demands on ductility – the bending angle is significantly increased as compared to MBW® 1500. Moreover, MBW® 1200 is perfectly suited for blanks produced by flexible rolling.
Owing to the increased strength of up to 2,000 MPa after hot forming, MBW-K® 1900 offers maximum potential for saving weight. This grade boasts a high deformation resistance in the event of a crash and is used for bumpers, side impact beams or in laterally stressed crossmembers.
Manganese-boron steel for hot forming based on VDA 239-500
SURFACE FINISHING | ||||||||
---|---|---|---|---|---|---|---|---|
-/UC | ZE/EG | Z/GI | ZF/GA | ZM | AS | AS Pro | ||
Steel grade | Based on VDA 239-500. Version Dec. 2021 |
|||||||
MBW-W® 1500 | HR1500T-MB | |||||||
MBW® 500 | CR500T-LA | |||||||
MBW® 600 | CR600T-LA | |||||||
MBW® 1200 | CR1100T-MB1 | |||||||
MBW® 1500 | CR1500T-MB | |||||||
MBW® 1900 | CR1900T-MB | |||||||
MBW-K® 1500 | CR1500T-MB | |||||||
MBW-K® 1900 | CR1900T-MB |
1 Currently not included in VDA 239-500, version December 2021
-/UC: Uncoated
ZE/EG: Electrolytically galvanized
Z/GI: Hot-dip galvanized
ZF/GA: Galvannealed
ZM: ZM Ecoprotect®
AS: Aluminum-silicon-coated
AS Pro: Aluminum-silicon-coated Pro
Notes on applications and processing
Material characteristics
Manganese-boron steels are quenched and tempered steels. The underlying material concepts in this family of steels exhibit a selected and matched chemical composition that enables curing (hot forming). This ferritic-pearlitic structure which exists in asreceived condition is converted into a purely martensitic structure in the process. Thanks to this process MBW® 1500+AS, for example, can increase its minimum tensile strength from 500 MPa in as-received condition to 1,500 MPa. The TTT diagram illustrates the transformation behavior for austenitizing temperature 900°C, dwell time 5 min, heated in 1 min. Even at low cooling rates a fully martensitic structure can be achieved.
As a partner for hot forming, thyssenkrupp not only offers the best materials but also the facilities needed to determine, for example, the optimum process parameters for hot forming. These facilities include a proprietary test area with state-of-theart hot forming equipment, which allows the processes used in series production to be simulated on a laboratory scale. Vehicle development can thus be accompanied comprehensively from the component design stage through to production readiness with the aid of analyses (thermography, forming, simulation) and troubleshooting. In addition, the process, component feasibility and structure can be studied by means of FEM simulations at thyssenkrupp.
Forming analyses can also be performed on hot-formed components in the same way as for cold-formed steel grades.
Forming
Manganese-boron steels have excellent hot-forming behavior. In the austenitization temperature range the formability of these steels is comparable to that of soft deep-drawing steels at room temperature. This makes it possible to manufacture components with complex geometries using low press forces in a single step. In contrast to classical cold forming, the component properties are mainly achieved by cooling in the tool rather than by forming. Targeted control of cooling in the tool means that components with graded functional properties can also be produced.
Hot forming opens up new options in component manufacturing. Changing the process parameters allows selective adjustment of the desired component properties, for example the strength or the residual elongation, in order to achieve optimum crash behavior, among other things.
Today, both direct and indirect hot forming are common methods. The single-stage process (direct hot forming) is the most commonly used method. It is particularly suitable for processing manganese-boron steel coated with a hot-dipped aluminum surface finish. This coating provides good protection against scaling, which typically occurs during hot forming, and thus ensures a longer service life of the forming tools.
The two-stage process (indirect hot forming) allows processing of hot-dip galvanized material, but is more complex and costly due to the upstream cold-forming and downstream hot-forming steps.
Tailored tempering or partial press hardening is a way of combining partially different properties in terms of strength and elongation in one component. The locally desired component characteristics are produced using selective temperature control in the hot-forming process. The desired mechanical properties can thus be achieved through the choice of different structural transformations.
Hot-worked stamped parts are additionally characterized by extremely low compressibility and recovery, thus enabling the production of highly dimensionally stable components.
Processing instructions for joining
Manganese-boron steels for hot forming are suitable for welding in both as-received and hot-formed (hardened) condition at both same-grade joints and hybrid joints with other common grades of steel.
The precondition is welding parameters matched to the material. In particular, resistance spot welding, shield gas welding, and laser beam welding methods can be used.
Resistance spot welding
Resistance spot welding is the preferred method because it offers several advantages. These include good automation, low component distortion and the ability to do without welding fillers. Compared to lower-strength steels, higher electrode forces and longer welding times must be used in resistance spot welding – optionally as multi-pulse welding in accordance with DIN EN ISO 18278-2. The welding zones are large for this strength class both in same-grade and hybrid joints. Spot welds are relatively ductile. However, they fail in chisel tests, despite the high material strength and hardness in the weld, typically due to mixed fracture with a relatively high detachment component. Joint strengths tend to be on a par with the strengths of the base materials involved, and are naturally influenced by the softer member in hybrid joints.
MIG/MAG arc brazing and welding
In the arc process, some material softening occurs in the heat-affected zone; this should be considered by the designer in addition to the filler which is used. The AS coating is thermally influenced by hot working and can impact arc stability, especially in joints with Z-coated sheet steels.
MIG brazing or the special “Cold Metal Transfer” process show clear advantages with respect to process stability and weld geometry compared to the standard metal active gas welding (MAG) process.
The standard additives typically used, namely G4Si1 (MAG) and copper solder CuAl7 (MIG brazing), usually achieve sufficient bonding strength. In order to exploit the high potential strength of the material, notch-free connections should be made where possible. In special cases, and given the use of suitable fillers, subsequent heat treatment or quenching and press hardening of the component and the weld can avoid local hardness drops in the heat-affected zone, thus leveraging the strength potential of the base material.
Laser beam welding
Laser beam welding of MBW® steels is possible with both CO2 and solid state lasers. Welding with CO2 lasers is performed using typical shielding gases. In unquenched and tempered state, hot-dip aluminum coating should be removed locally prior to welding as it can otherwise result in AlSi inclusions that impact strength. In quenched and tempered condition, the coating is alloyed throughout and need not be removed. It must be noted that a decrease in strength of the base material occurs in the heat-affected zone of the weld. This can be remedied by repeating quenching and tempering.
Fatigue strength and crash performance
Manganese-boron steels are offered specifically for hot forming. It is only by heat treatment during tempering that the material properties are created, which then characterize the load capacity (in terms of strength, durability and crash behavior). Due to the unequivocal major influence of press hardening on the material properties, these properties must be described by the manufacturer. However, it can be said in general that, due to the very high levels of strength, these steels are suitable for components which must not deform in a crash scenario. The SN curve shows the good fatigue strength of MBW® 1500.