to website
Sustainability: packaging steel closes the circle
Steel is an important factor for a climate-neutral Europe. It is the most frequently used and recycled industrial material. The more often steel is recycled, the smaller its ecological footprint. An example of this is tinplate, which is used among other things as food and drink packaging material.
Plastic waste in the oceans, major problems with waste disposal and the general finite nature of natural resources: pressing challenges that make it clear why the circular economy is becoming increasingly important for modern society. That’s why the European Union’s Green Deal includes a new Circular Economy Action Plan. It aims to use products and materials, energy and resources, as well as waste and residual materials sustainably and for as long as possible, for example through reuse and recycling. One material particularly suitable for this is tinplate. But despite its excellent properties, not all consumers are aware of its ecological qualities.
Awareness of recyclability still too low
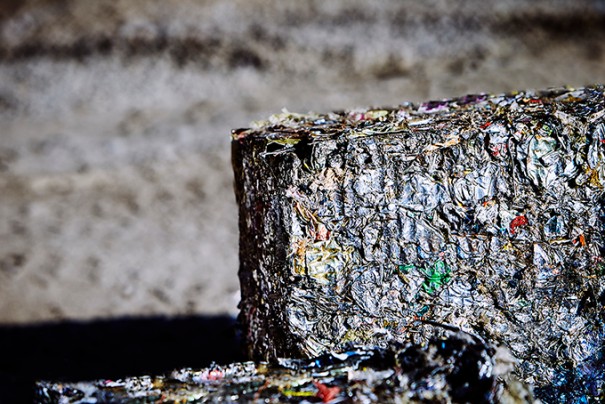
“Unfortunately, consumer awareness of the recyclability and recycling of tinplate is still too low,” explains Carmen Tschage, Head of Communications and Market Development at thyssenkrupp Rasselstein. “This was shown by a representative survey carried out for us in Germany in 2021 by the market research agency YouGov. For example, consumers estimate that the recycling rate for tinplate is only 55 percent, whereas the actual figure is much higher at over 90 percent.” Just a few years ago, public interest in sustainability issues was very low. But that has changed by now. “Today, consumers see that rising mountains of plastic waste and huge garbage patches in the oceans are a real threat to the environment and ultimately to us humans, and they want to change their behavior.”
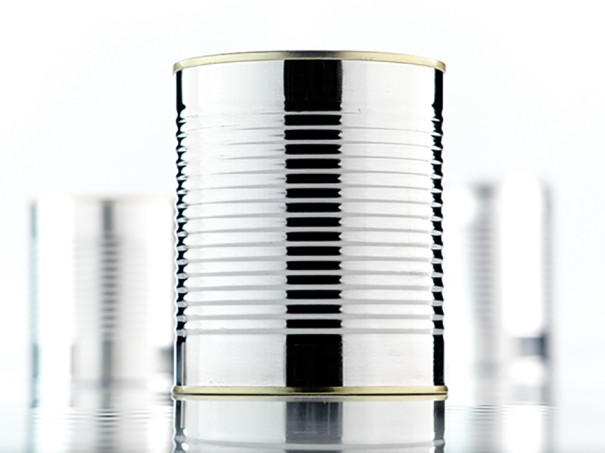
Tinplate can help with the pressing issues of our time: As a packaging material, tinplate scores not only for its good recycling properties but also for its well-functioning recycling systems. If instead of being incinerated after use or dumped in landfills outside Europe packaging is fed back into the manufacturing process, valuable resources are saved. Packaging steel plays a major role in our everyday lives – for example in the form of food and drink cans, packaging for chemical/technical products, spray cans for aerosols, or jar and bottle tops – and so individual consumers are a powerful lever in the circular economy. And by choosing tinplate packaging they can support multi-recycling and the closed material cycle with the flick of a wrist: by throwing tinplate packaging into the recycling bin after use.
The German Federal Environment Agency (UBA)’s findings on the recycling rate of packaging materials consistently reveal that products made from packaging steel are among the recycling champions. According to these figures, in the 2021 survey year, tinplate in Germany has a recycling rate of 90.2% as stipulated by the German Packaging Act. “According to the findings of the most recent survey, tinplate is one of the most recyclable materials, making it an ideal fit for the circular economy. In Germany, we are stable at more than 90%, as we have been for the past 15 years,” said Andreas Knein, General Manager of DWR - Deutsche Gesellschaft für Weißblechrecycling mbH, a subsidiary of thyssenkrupp Rasselstein GmbH.
Every steel mill is also a recycling plant
DWR expects that the recycling rate will remain at consistently high levels in the future, as scrap will be in even greater demand due to its increased use in recycling processes. After processing, the extremely clean tinplate scrap is transferred to the steel plant, where it can be melted down with other steel scrap without losing quality and converted into crude steel using pig iron. It undergoes product-specific additional processing steps before being transformed into a new high-quality steel product, ranging from automobile sheet metal to steel beams and new packaging. Every steel plant may therefore also be considered a recycling plant. The material cycle is closed.
thyssenkrupp Rasselstein is on the way to green packaging steel
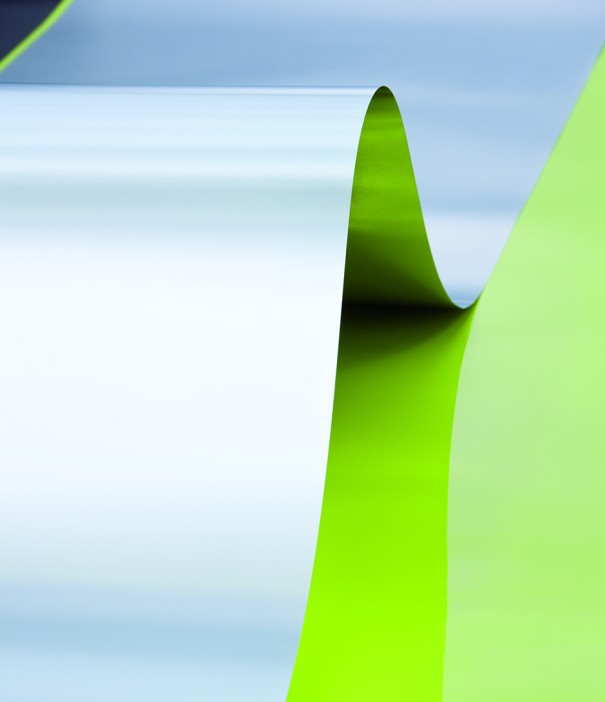
The “Green Deal” is an ambitious goal of the European Union by which the Member States intend to become climate-neutral by 2050. It is also a goal that cannot be achieved without industry cooperation. As a company from the energy-intensive steel industry, thyssenkrupp Steel Europe is therefore gradually converting its steel production so as to be a major contributor to a climate-neutral future: By no later than 2030, the steel producer aims to cut carbon dioxide (CO2) emissions in steel production by 30%. Steelmaking at thyssenkrupp is to be climate-neutral by 2045. The decisive move is the avoidance of CO2 by using hydrogen (“Carbon Direct Avoidance”, CDA), while CO2 is also captured and used (“Carbon Capture and Usage”, CCU). Ultimately, the resulting carbon-neutral steel will not only be used in automobiles and machinery but, in the form of climate-neutral packaging steel, will also become an integral part of the portfolio of thyssenkrupp Rasselstein.
rasselstein® made of bluemint® Steel
Already today thyssenkrupp Rasselstein's portfolio includes tinplate made from CO2-reduced bluemint® Steel. Alternative input materials are used for bluemint® Steel in the steelmaking process. This reduces above all the use of coal for the reduction process in the blast furnace, resulting in a real reduction in CO2 emissions.
bluemint® recycled does not differ from existing steel grades – except in its reduced specific CO2 emissions. The certified steels are produced at thyssenkrupp Steel and processed into packaging steel at the Andernach site.
The product is the first transformation success within thyssenkrupp Steel's climate strategy. In the coming years we will invest intensively in innovations and technologies that will bring our customers gradually closer to the shared goal of climate neutrality and a green steel product.
Ecological packaging is trendy among consumers
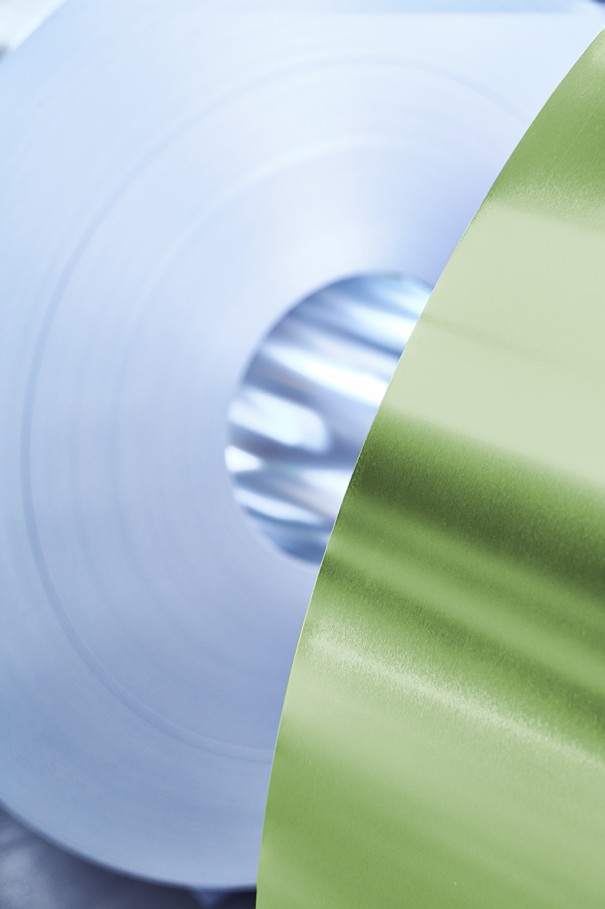
The development of the industry shows that bluemint® Steel and tinplate belong together. “As usual, we will offer our customers a high-quality product range in which bluemint® Steel tinplate has a firm place alongside our other premium products. bluemint® Steel is particularly interesting for our customers because there is a growing need and increasing demand for CO2-reduced packaging options among end users. The fact that sales of organic products have been rising for years shows that consumers want to consume in an ecological and responsible manner,” said Dr. Peter Biele, CEO of thyssenkrupp Rasselstein GmbH.
Ever more European consumers are turning to environmentally friendly and recyclable packaging. They are willing to pay more for packaging if it has an improved environmental impact. CO2-reduced packaging steel closes the last gap, because tinplate is already unbeatable in terms of recyclability. Tinplate is a permanent material in a closed cycle. Thanks to its magnetic properties, packaging steel is easy to collect and recycle as packaging material. It is almost 100% recyclable – again and again and without downcycling, thus without reduction in quality, as its inherent properties are retained. This makes tinplate the perfect material for multi-recycling.
Further information
Occupational Safety and Health
Health and safety are top priorities
One of our most important business objectives is: "Zero Accidents". Occupational health and safety standards have the highest priority at thyssenkrupp Rasselstein.
Principles of Action for Occupational Safety and Health
The following occupational safety and health principles are pursued at thyssenkrupp Rasselstein GmbH in compliance with thyssenkrupp AG’s Management Manual for Occupational Safety and Health and thyssenkrupp Business Area Steel Europe’s OSH master plan:
We aim to have zero accidents
- The occupational safety and health objectives are pursued jointly by the Board, managers, Works Council and staff. Continuous improvement processes aim to maintain a sustainable safety culture.
We are consistent role models
- Prevention of injuries and work-related health hazards as well as the design of the working environment are a management task, particularly in the context of delegated responsibilities and duties.
Targeted risk prevention is achieved by a change in attitude and behavior with a clear focus on the development of new patterns of perception founded on the principle of benevolent responsibility for each other and continuous improvement. The instrument for establishing this new safety culture is the attitude and behavior process “EVprocess A”, which applies at all organizational levels with the aim of creating a community that shares responsibility for safety.
We will not undertake any work that cannot be completed safely
- All employees are responsible for themselves and their colleagues, and are committed to contributing to occupational safety and health to the best of their abilities. The “Red spot on crane systems” concept (a red spot indicates suspended loads) will continue to be rolled out. Tests on distance warning systems on forklift trucks and mandrel carts are also in progress. In support of this, the WE Stop! card will be made available to every employee and partner authorised to stop dangerous actions and conditions in the thyssenkrupp sites.
We do not ignore, we respond
- By adopting forward-looking messages, the organizational and technical aspects of occupational safety and health are continuously improved.
The instrument for making employees aware of potential everyday risks is the permanently installed „Experiencing danger“ occupational safety course. Here the participants experience specific danger situations under realistic working scenarios involving stumbling, slipping, falling and lifting loads, for instance.
We treat also external companies like ourselves
- The same safety standards as for own employees apply to the personnel of partner companies. This is taken into account in selecting and working with partner companies. The change in the safety culture will be communicated outwardly by the safety audits performed jointly at partner company premises. “Quick checks” also aim at increasing safety standards at construction sites.
We want to maintain and promote the health of our employees
- To maintain the health of our employees we take into account physical, psychological and social aspects to equal extent. In pursuit of continuously improving work conditions, we use committees such as the Occupational Health Council and health teams to involve all relevant parties within the company. By offering health promotion and guidance on the issue of “career and family” we ensure that individual factors are taken into account.
We create healthy work conditions
- We attach great importance to the creation of health-focussed working and organisational conditions. With the help of different analytical tools, we systematically investigate the relevant stress factors, continuously working on improvement with the involvement of employees. To this end, we use the tools “Integration of people with disabilities into the working world” (IMBA), staff questionnaires and “Assessment of work content, work organisation, staff management and social relations” (BAAM), and health audits as needed.
We promote health-focussed managerial conduct through basic qualification and regular follow-up training on OSH topics. Managers are consequently provided with the skills to establish healthy work conditions. We counter social conflicts using tools such as coaching and mediation.
We promote the individual’s health
- The comprehensive medical examination not only allows work-related, but also individual health risks to be identified and provides the employees with specific advice on healthy action. In the process, we cooperate with different external bodies, such as physiotherapists, psychologists, psychiatrists and German Pension Insurance (Deutsche Rentenversicherung) in Rhineland-Palatinate. Our employees’ health expertise is promoted via health modules in subject-led group work and health workshops within company training with focus on target group requirements.
We integrate employees whose ability to work has changed
- Company Reintegration Management (BEM) is a cornerstone of our company health management. In the case of incapacity for work of longer than four weeks, the employee concerned will be offered a consultation with the company medical officer above and beyond minimum legal requirements in his or her ‘welcome back’ meeting. In complex BEM cases, we support the employees with fitness for work coaching; a skills-matched job can be found using the IMBA profile comparison system.
Environmental management
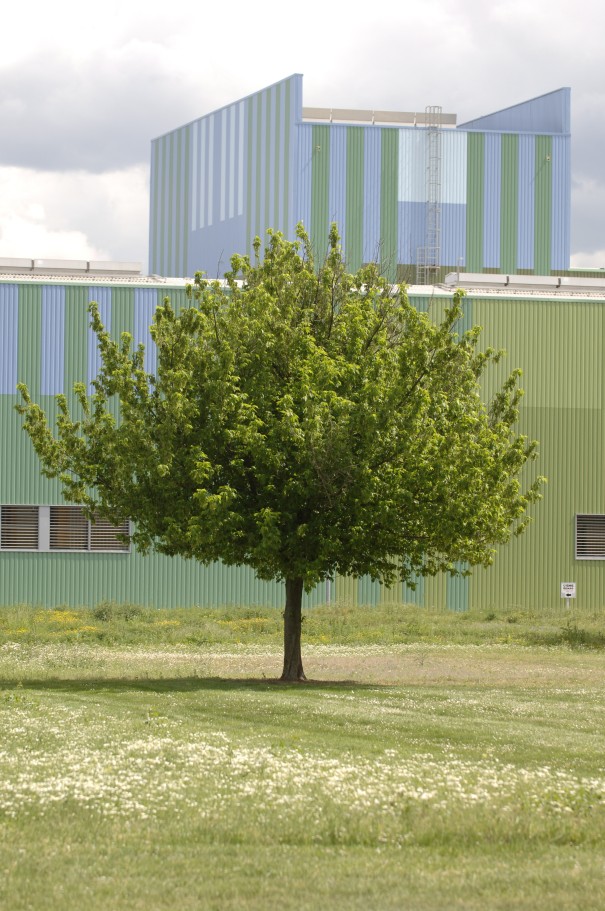
Clear commitment to environmental protection
Protecting the environment is a high priority for us. Modern facilities for the purification of air and water and the efficient use of raw materials and energy are standard practice. Since 2001, we have an environmental management system certified to DIN EN ISO 14001:2015.
All materials used in the production of our products are carefully selected with a view towards the environment and work safety. More than 95 per cent of the arising waste is recycled. Only a very small percentage must be environmentally disposed of in processing or incineration plants.
Action Principles of Environmental Protection
thyssenkrupp Rasselstein GmbH‘s environmental policy has been developed in compliance with the thyssenkrupp Group’s guidelines on environmental and energy management and is implemented by means of the following overarching Action Principles:
We identify which of our business activities have an essential impact on the environment and are committed to continuous improvement
- thyssenkrupp Rasselstein GmbH is committed to identifying, assessing and documenting the essential impact and hazards presented by the company’s activities and products on the environment and to continuous improvement.
We are committed to preventing environmental pollution
- The company is committed to preventing environmental pollution and taking precautions to prevent and limit any incidents which might damage the environment and to implement special procedures to keep environmental impact and other hazards to the minimum possible. This includes in particular:
- Waste avoidance and the eco-friendly disposal of waste.
- Sparing use of energy, materials, air, water and ground.
- Monitoring and measuring compliance with the statutory environmental regulations.
We comply with the law of the land
- Environmental safety is an integral part of all our operational procedures and is incorporated right from the start – even at the planning stage – into technical, economic and social responsibility considerations. This includes observing the relevant legislation, directives, provisions and operational regulations covering these areas. We cooperate with the authorities and external personnel openly and in a spirit of trust. This also applies to preventive hazard control.
We create awareness of environmental and safety issues
- thyssenkrupp Rasselstein GmbH creates and promotes environmental and safety awareness among all its employees. In the course of this, the company will develop a water footprint.
All personnel who work in our organization or act on its behalf are covered by our environment, safety and energy policies
- All suppliers, contractual partners and customers who work on company premises are covered by our current environment, energy and safety policies. We aim to engage capable contractors for our business activities with impact on environment, energy and/or safety.
We provide facts and figures for the public’s information
- thyssenkrupp Rasselstein GmbH provides the public with the facts and figures necessary to gaining an understanding of the environmental impact and hazards of the company’s activities and products.
Plant safety
Action principles of plant safety
thyssenkrupp Rasselstein GmbH’s Action Principles of Environmental Protection are further supplemented by the Action Principles of Plant Safety listed below:
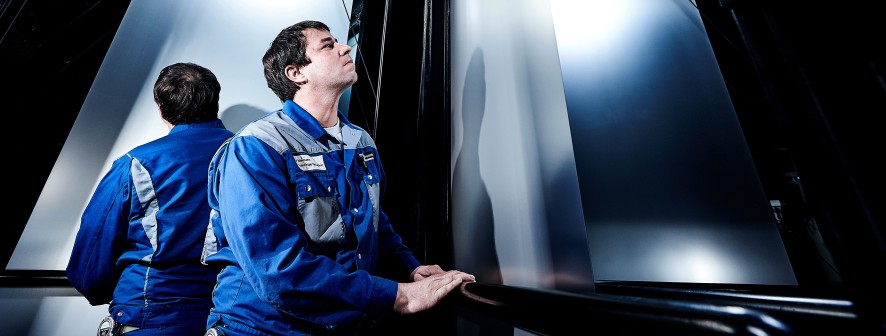
The protection of our employees, partners and the environment from the risks and hazards presented by our systems has top priority over all other corporate objectives
- In order to provide the best possible protection from hazards for our employees, the standard of safety technology is consistently maintained and continuously optimized by means of a suitable safety structure and by selecting plant and equipment accordingly. This includes in particular:
- New sections and/or modifications of plant are planned systematically, professionally installed and operated by trained personnel.
- The handling of hazardous substances is governed by technical and structural measures so that malfunctions in designated operations and incidents that impact on personnel, local community and environment are kept to the minimum possible.
- All the safety features incorporated into our plant and equipment are secured against interference in the event of unauthorized access to our premises.
- Environmental hazards are covered by malfunction precautions.
- A preventive service and maintenance program is scheduled for plant components that are significant for safety.
- The safety report will continue being compiled within the sustainability concept.
- Development of emergency and crisis management is ongoing.
We regularly upgrade our employees’ training
- We train and instruct our employees regularly in issues of plant safety, preventing malfunctions and hazard control, in particular for new staff und reassigned staff.
We review the implementation of corrective and preventive measures
- Safety walkabouts are regularly conducted in operational areas in order to identify deficiencies and areas of weakness and to check on the implementation of corrective and preventive measures where deficiencies and areas of weakness have been identified.
Energy management
Energy management for better efficiency
Natural fuel resources are limited and thyssenkrupp Rasselstein takes a responsible approach to the energy generated from them. In keeping with the commitment to eco-friendly practices at thyssenkrupp Rasselstein, an energy management system conforming to the ISO 50001 standard is to be put in place in addition to the existing environmental management system.
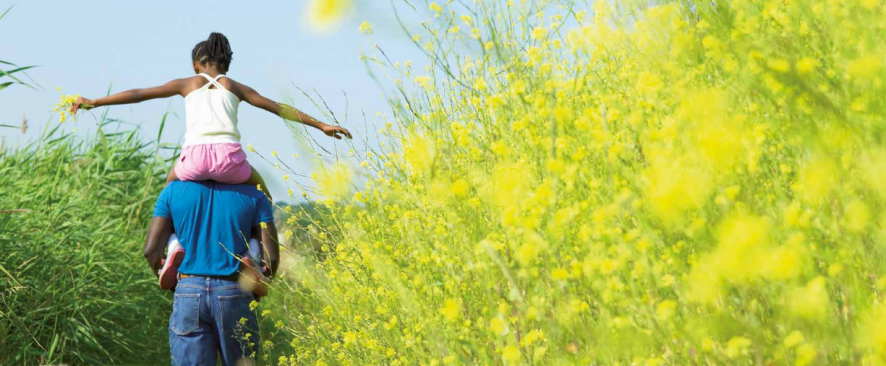
Action Principles of Energy Management
thyssenkrupp Rasselstein GmbH’s Action Principles of Environmental Protection are supplemented by the following Action Principles relating specifically to Energy management:
We are committed to reducing energy consumption
- thyssenkrupp Rasselstein GmbH is committed to reducing its actual energy consumption in the long term and to increasing its energy efficiency in a process of continuous improvement.
An energy management system conforming to DIN EN ISO 50001 is operated with a view to fulfilling these aims. All the requirements of this standard are correctly met and the processes are continuously improved. - Natural fuel resources are limited and thyssenkrupp Rasselstein GmbH takes a responsible approach in utilizing the energy generated.
We aim to increase the energy efficiency of our equipment continuously
- thyssenkrupp Rasselstein GmbH plans its investments with a view to maintaining and modernizing its plants and equipment in order to improve their energy efficiency and ensure that progress is made.
- thyssenkrupp Rasselstein GmbH constantly strives to use energy more efficiently, either by reducing energy consumption or by making better use of the energy consumed.
- thyssenkrupp Rasselstein GmbH seeks to strengthen its future competitiveness by implementing research and development measures to increase energy efficiency.
Every member of staff is accountable for their actions and has a duty to adopt energy-conscious practices
- All employees are accountable for their actions and have a duty to adopt energy-aware practices. All employees are encouraged to be innovative and supportive in respect of energy efficiency initiatives.
- The energy policy also applies to external personnel and companies.
- Energy management factors are integral to all the decisions taken in the company.
Recycling
The perpetual cycle of steel
The perpetual cycle of steel
Packaging steel is a “permanent material” which retains its properties without any loss in quality no matter how many times it is re-used.
In other words, steel can be processed to make packages or other kind of products. When these applications have reached the end of their useful life, the steel they were made of can be recycled and used to make new products, thus closing the material loop. The cycle can be repeated as often as desired without any change in the material properties.
Learn more about how steel packaging can be recycled over and over again.
Since 2003, our subsidiary DWR-Deutsche Gesellschaft für Weißblechrecycling mbH has been operating as a marketer of steel packaging scrap from post-consumer waste. DWR pools the steel packages collected and sorted through the various recovery channels, conditions the material and supplies it as high-grade scrap for high-quality recycling. In other words, thyssenkrupp has taken over the entire product stewardship for packaging steel within the meaning of the German Life-Cycle Resource Management Act.
A collection and recycling system for industrial and commercial steel packaging has also been in existence since 1993: KBS Kreislaufsystem Blechverpackungen Stahl GmbH.
To learn more on this topic, watch the APEAL Recycling film.
Responsible conduct
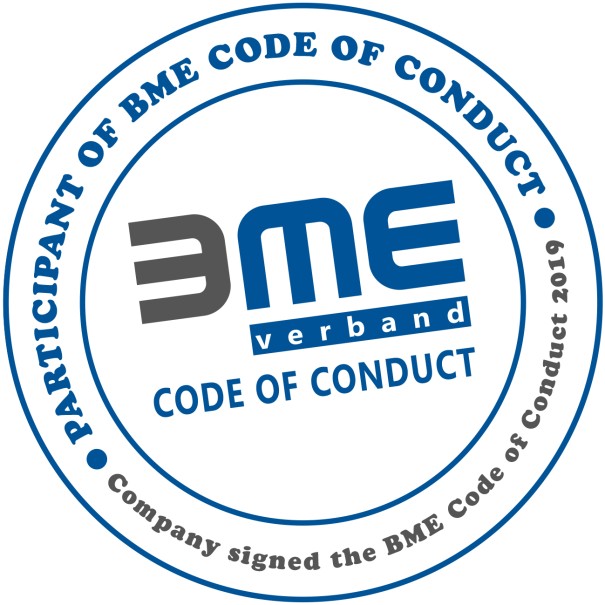
Responsible conduct within the supply chain
BME Code of Conduct
In 2010 thyssenkrupp Rasselstein signed the Code of Conduct of the German association of materials management, purchasing and logistics (BME), which is based on the Global Compact principles, the United Nations Universal Declaration of Human Rights and the conventions of the International Labor Organization (ILO).
The aim is to gain firm acceptance for general ethical principles of fairness, integrity and corporate responsibility in business relations.
thyssenkrupp Rasselstein works best to ensure that its suppliers and their suppliers comply with the following principles:
- prevent corruption
- promote fair competition
- strengthen environmental protection
- ensure health and safety
- protect human rights
- prevent discrimination
thyssenkrupp Rasselstein participates in an annual self assessment process.
thyssenkrupp Conflict Minerals Statement
thyssenkrupp Conflict Minerals Statement
Human rights, fair working conditions, environmental protection and the battle against corruption – these are values that we hold high within our Group and throughout our supply chain. We at thyssenkrupp are committed to the United Nations Global Compact. Acting responsibly is firmly integrated in our procurement processes. When awarding contracts, our decisions are not only based on economic, technological and process criteria. Sustainability also plays a key role in the supplier management of thyssenkrupp Rasselstein. Moreover, we continuously develop our processes. This also means, for example, that we want to further increase transparency regarding the origin of raw materials and so-called conflict minerals to detect risks early.
Compliance with due diligence obligations in the supply chain of tin
The mining of certain minerals in the Democratic Republic of Congo (DRC) and other parts of the world partially contributes to significant human rights violations and to the financing of violent conflicts.
Within the European Union, importers of so-called conflict minerals are now subject to extensive obligations regarding due diligence and inspections across the supply chain in order to curb the financing of violence and human rights violations in areas of conflict or high-risks. The implementing law for EU regulation 2017/821 of 7 May 2020 has been in force in Germany since 1 January 2021.
This affects our company because we are Union importers of tin. Already years ago, we established procedures in our company to review supply chains and identify risks. Our supply chains are transparent and are subject to regular audits, so we fully comply with the legal requirements.
Dodd-Frank Act on Conflict Minerals
Since 2010, thyssenkrupp Rasselstein has been complying with the regulations of the United States of America that is usually referred to as Dodd-Frank Act (full name: “Dodd-Frank Wall Street Reform and Consumer Protection Act”). Section 1502 of the Dodd-Frank Act adopted by the U.S. Securities and Exchange Commission (SEC) require companies who file reports with the SEC to disclose whether the products they manufacture or contract to manufacture contain “conflict minerals” that are "necessary to the functionality or production" of those products. “Conflict minerals” contain tantalum, tin, tungsten (and the ores from which they originate) and gold, regardless of where they are sourced, processed or sold.
thyssenkrupp AG (including all its subsidiary companies) does not file reports with the SEC and therefore has no legislative obligations to comply with the conflict minerals requirements covered in Section 1502 of the Dodd-Frank Act. At the same time we recognize that the SEC final rule for Section 1502 mandates our direct and indirect customers to undertake due diligence across their global supply chains.
Statement
We at thyssenkrupp Rasselstein endeavor not to purchase any material that contains these “conflict minerals” which directly or indirectly finance or benefit armed groups. To this end, we have implemented appropriate processes to understand where “conflict minerals” are being used in our products and to determine the source and the origin within our supply chain. These actions are based on established frameworks of the Organization for Economic Cooperation and Development (OECD) and from other private sector initiatives. We are contacting our direct suppliers to increase the transparency of the materials they provide to thyssenkrupp. We personally conduct inspections on site, or commission third parties to regularly check the situation at our suppliers. We will continue to work closely with customers, suppliers and other stakeholders to secure good approaches and feasible solutions.
Slavery and Human Trafficking Statement
thyssenkrupp AG is a signatory to the United Nations Global Compact and supports the United Nations Universal Declaration of Human Rights and the core labor standards of the International Labor Organization (ILO). thyssenkrupp Group is commited to eradicate slavery and human trafficking in its supply chain and own operations. Our efforts to achieve this are described in the “Slavery and Human Trafficking Statement for thyssenkrupp AG and its Subsidiaries”, which is made pursuant to section 54 of the United Kingdom Modern Slavery Act 2015.
Social responsibility
Social responsibility
thyssenkrupp has been connected to the Andernach-Neuwied region on the Middle Rhine and its people for more than 250 years. We assume the resulting responsibility for the common good and the sustainability of the location in various ways.
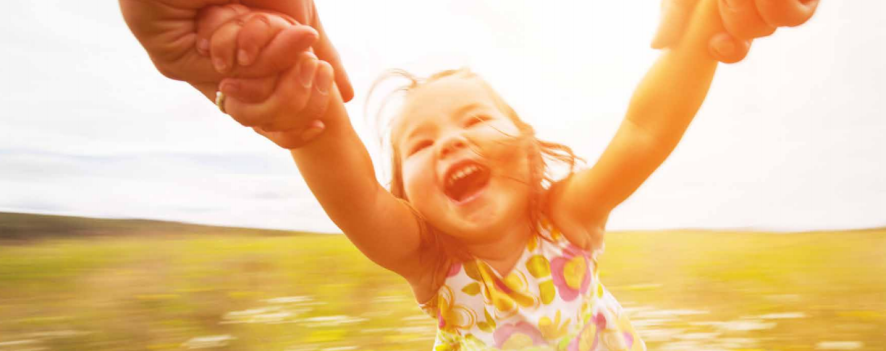
Our social commitment covers e.g. broad vocational training, forward-looking personnel development, health provision and promotion programmes as well as benefits above the general pay scale.
thyssenkrupp offers more apprenticeships in Andernach than necessary to meet its own needs. The reason for this is to give as many young people as possible a solid basis for building their own professional careers. In addition to this, we sponsor schools and projects that inspire young people to take an interest in technology and innovation. thyssenkrupp is a partner to the “Jugend forscht” young researchers competition, offers internships for school students or practical semesters for college students, and supports local sports and athletic competitions.
More information: Corporate citizenship of thyssenkrupp Steel Europe AG