The alloying concept of AS Pro ensures lower process-related hydrogen absorption during hot forming and provides lasting protection against embrittlement. Discover more!
Available steel grades
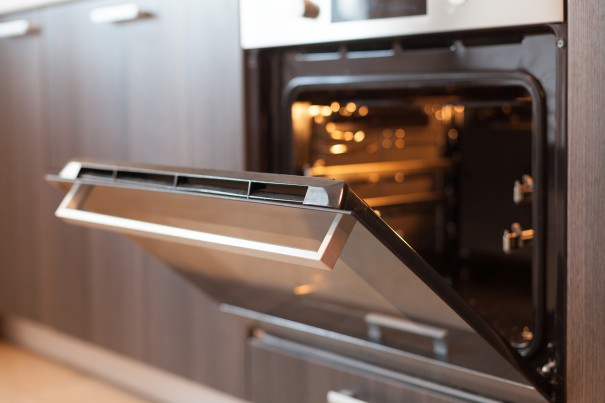
Like hot-dip galvanized sheet, hot-dip aluminized sheet fal LightProtect is produced in a continuous process (furnace, metal bath). The coating typically consists of approx. 10% silicon, 3% iron and 90% aluminum. The proportion of silicon can vary between 8 - 11%. In addition to good corrosion protection, the AS coating offers excellent heat resistance and high-temperature strength.
Deep-drawing steel
DIN EN 10346, VDA 239-100
Surface finishing | |
---|---|
Steel grade | AS |
DX51D / – | |
DX52D / CR1 | |
DX53D / CR2 | |
DX54D / CR3 | |
DX56D / CR4 |
Hot-dip coated structural steel
DIN EN 10346
Surface finishing | |
---|---|
Steel grade | AS |
S220GD |
|
S250GD |
|
S280GD |
|
S320GD |
|
S350GD |
|
S390GD |
Micro-alloyed steel
DIN EN 10346, VDA 239-100
Surface finishing | |
---|---|
Steel grade | AS |
– / CR210LA | |
HC260LA / HX260LAD / CR240LA | |
HC300LA / HX300LAD / CR270LA | |
HC340LA / HX340LAD / CR300LA | |
HC380LA / HX380LAD / CR340LA |
|
HC420LA / HX420LAD / CR380LA |
Serial production
Tolerances
Dimensional and shape tolerances to EN 10 143.
Surfaces
Available surface finishes, aluminum-silicon coated
Minimum coating two-sided sample [g/m2] | Coating on each side of single spot sample | Informative |
||||
---|---|---|---|---|---|---|
Coating |
Specification |
Triple spot sample |
Single spot sample |
Mass [g/m2] |
Thickness [μm]1 |
Typical thickness [μm] |
AS060 | DIN EN 10346 | 60 | 45 | 7 – 15 | 10 | |
AS080 | DIN EN 10346 | 80 | 60 | 10 – 20 | 14 | |
AS30 | VDA 239-100 | – | – | 30 – 65 | 10 – 20 | – |
AS100 | DIN EN 10346 | 100 | 75 | 12 – 23 | 17 | |
AS120 | DIN EN 10346 | 120 | 90 | 15 – 27 | 20 | |
AS45 | VDA 239-100 | – | – | 45 – 85 | 15 – 28 | – |
AS150 | DIN EN 10346 | 150 | 115 | 19 – 33 | 25 |
Type of surfaces
Zinc-aluminum coated sheet galfan® is available in the following surface finishes: A (Normal surface), B (Improved surface), C (Best surface) to DIN EN 10346.
Surface treatments
The following surface treatments are available: Without surface treatment (U), Passivated, covex® T (C), Chemically passivated and oiled (CO), Oiled (O), and Sealed, covex® E (S).
Processing of AS-coated steel
Forming
All known forming processes for cold-formed sheet metal can be used on AS-coated sheet if the tool geometry and surface are adapted to this material.
The aluminization has a decisive influence on the tribology of the forming process. The radii of the tools in particular should be polished and have a surface coating. This can minimize abrasion of the surface and thus reduce the risk of cold welding in the tool.
It should also be noted that aluminum-silicon-coated sheet is sensitive to tensile-compressive alternating stress. This must be taken into account when designing components and planning methods in toolmaking. In addition, the drawing gap and die radius have a considerable influence on the formability of the AS coating and should therefore not be selected too small.
Joining
All thermal and mechanical joining processes as well as bonding and sealing can be used. However, the special physical properties of the aluminum coating require an adjustment of the processing parameters for some joining methods compared to uncoated sheet. It is advisable to use joining methods that are as gentle as possible so as not to impair the corrosion protection.
Processes have been developed that are tailored to the special properties of hot-dip coated sheet. When joining AS-coated sheet with other materials, the potentially different electrochemical behavior must be taken into account, as the corrosion-protective properties of the coating can be impaired by unfavorable metal pairings.
Welding
Due to the strong affinity of copper for aluminum, alloying occurs between the copper material of the welding electrodes and the AS coating during resistance spot and roller seam welding, which complicates the welding process and leads to accelerated wear of the electrodes.
When resistance spot welding, care should therefore be taken to weld with well-cooled electrodes at slightly increased electrode forces using the shortest possible current times in order to reduce the thermal load on the electrodes. The use of a current stepper control has also proven to increase electrode service life. These measures have the effect of extending the intervals for reworking or replacing the electrodes due to wear.
Particularly intensive electrode cooling is required for roller seam welding to reduce the formation of foreign layers on the electrodes. For constant working conditions, the use of a knurled roller drive, the installation of profile rollers or a shearing device is recommended. Roller seam welding with an intermediate wire electrode has proven to be a suitable special process. Here, only the copper wire alloys with the coating instead of the welding roller. However, as the wire is continuously renewed, perfect contact conditions always prevail at the welding point.
The MAG gas-shielded welding process commonly used for uncoated sheet can only be used with restrictions. The heat input must be increased so that the coating is removed before the weld pool due to the heat applied. The welding speed must be reduced to reduce the formation of pores and spatter. Mixed gases are preferable to pure CO2; damage to the coating next to the seam can be minimized by using short arc and impulse technology.
The most favorable welding results are achieved when welding butt joints using the plasma process. Lap joints are welded with filler wire. Plasma welded joints are characterized by uniform, low-porosity and low-spatter seams. The strength values of the welded joints reach the values of the base material. The seam surface and the immediately adjacent material have no or reduced corrosion protection. In the case of high corrosive loads, the seam area should be protected with aluminum-rich paints.
During laser welding, aluminum-silicon inclusions occur in the seam as a result of the weld pool dynamics, both in butt welds and in overlap seams. The resulting loss of strength of the laser welds must be taken into account, particularly in the case of high-strength and ultra-high-strength grades. If necessary, it is recommended to remove the coating in the weld seam area before joining.
Heat resistance
AS-coated sheet can be used in temperature ranges of up to 700°C.
Corrosion behavior
Aluminum-silicon coated sheet offers far greater corrosion protection than conventional zinc coatings with the same coating thickness.