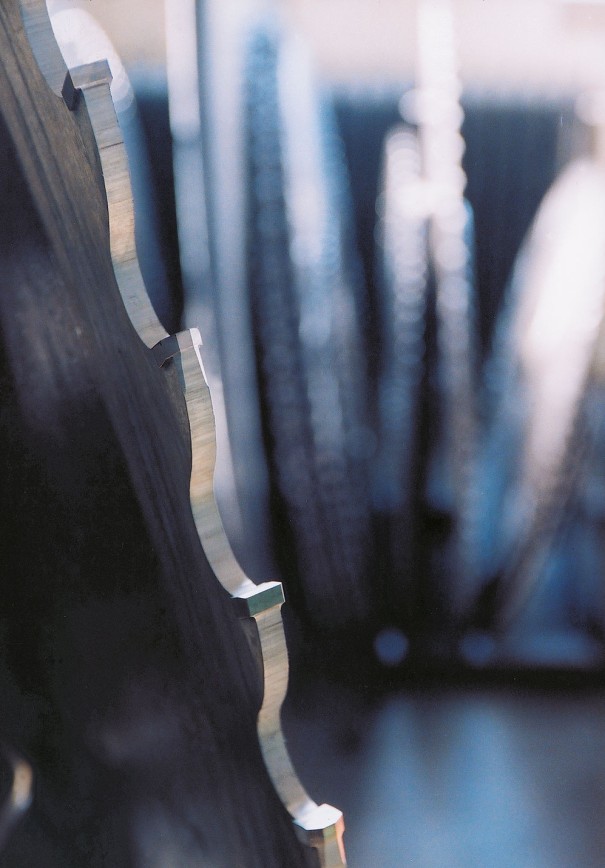
The unalloyed quenched and tempered steels are used for lower loads, whereas the alloyed quenched and tempered steels are suited for high dynamic and static loads. Moreover, the strength and ductility requirements are decisive for the selection of steel grades; the component dimensions must also be taken into account. In many fields of application, the focus is on the maximum possible full quenching and tempering.
There are various fields of application of QT steels: typical applications in vehicle construction are camshafts and transmission shafts, axles, clutch components and fastening elements. In mechanical and plant engineering, quenched and tempered steels are used, for example, in shafts, pinions, gear wheels, chain links and saw blades.
thyssenkrupp supplies the following steel grades as per the product information or the reference steel grades in accordance with the respective standards.
Unalloyed quenched and tempered steel according to DIN EN ISO 683-1 (previously DIN EN 10083-2), DIN EN 10132-3
Steel grade designation | Reference grade | Material no. | THICKNESS1 from _ to in mm |
WIDTH1 from _ to in mm |
---|---|---|---|---|
C22 | C22 | 1.1151 | 2.00 – 13.00 | 50 – 1,630 |
C25 | C25 | 1.1158 | 2.00 – 13.00 | 50 – 1,630 |
C35 | C35 | 1.1181 | 2.00 – 13.00 | 50 – 1,630 |
C40 | C40 | 1.1186 | 2.00 – 13.00 | 50 – 1,630 |
C45 | C45 | 1.1191 | 2.00 – 13.00 | 50 – 1,630 |
C50 | C50 | 1.1206 | 2.00 – 13.00 | 50 – 1,630 |
C55 | C55 | 1.1203 | 2.00 – 13.00 | 50 – 1,630 |
C60 | C60 | 1.1221 | 2.00 – 13.00 | 50 – 1,630 |
Chemical composition of unalloyed quenched and tempered steel
Steel grade | C [%] |
Si [%] max. | Mn [%] |
P [%] max. | S [%] max. | Cr [%] max. | Mo [%] max. | Ni [%] max. | Cr + Mo +Ni [%]max. |
---|---|---|---|---|---|---|---|---|---|
C22 | 0.17 – 0.24 | 0.40 | 0.40 – 0.70 | 0.025 | 0.010 | 0.40 | 0.10 | 0.40 | 0.63 |
C25 | 0.22 – 0.29 | 0.40 | 0.40 – 0.70 | 0.025 | 0.010 | 0.40 | 0.10 | 0.40 | 0.63 |
C35 | 0.32 – 0.39 | 0.40 | 0.50 – 0.80 | 0.025 | 0.010 | 0.40 | 0.10 | 0.40 | 0.63 |
C40 | 0.37 – 0.44 | 0.40 | 0.50 – 0.80 | 0.025 | 0.010 | 0.40 | 0.10 | 0.40 | 0.63 |
C45 | 0.42 – 0.50 | 0.40 | 0.50 – 0.80 | 0.025 | 0.010 | 0.40 | 0.10 | 0.40 | 0.63 |
C50 | 0.47 – 0.55 | 0.40 | 0.60 – 0.90 | 0.025 | 0.010 | 0.40 | 0.10 | 0.40 | 0.63 |
C55 | 0.52 – 0.60 | 0.40 | 0.60 – 0.90 | 0.025 | 0.010 | 0.40 | 0.10 | 0.40 | 0.63 |
C60 | 0.57 – 0.65 | 0.40 | 0.60 – 0.90 | 0.025 | 0.010 | 0.40 | 0.10 | 0.40 | 0.63 |
Alloyed quenched and tempered steel according to DIN EN ISO 683-2 (previously DIN EN 10083-1 and DIN EN 10083-3), DIN EN 10132-3
Steel grade designation | Reference grade | Material no. | THICKNESS1 from _ to in mm |
WIDTH1 from _ to in mm |
---|---|---|---|---|
25CrMo4 | 25CrMo4 | 1.7218 | 2.00 – 13.00 | 100 – 1,630 |
34CrMo4 | 34CrMo4 | 1.7220 | 2.00 – 13.00 | 100 – 1,630 |
42CrMo4 | 42CrMo4 | 1.7225 | 2.00 – 13.00 | 100 – 1,630 |
50CrMo4 | 50CrMo4 | 1.228 | 2.00 – 13.00 | 100 – 1,630 |
51CrV4 | 51CrV4 | 1.8159 | 2.00 – 13.00 | 100 – 1,630 |
58CrV4 | Special mill grade | 1.8161 | 2.00 – 13.00 | 100 – 1,630 |
Chemical composition of alloyed quenched and tempered steel
Steel grade | C [%] |
Si [%] max. |
Mn [%] |
P [%] max. |
S [%] max. |
Cr [%] |
Mo [%] max. / - | V [%] | B [%] |
---|---|---|---|---|---|---|---|---|---|
25CrMo4 | 0.22 – 0.29 | 0.40 | 0.60 – 0.90 | 0.025 | 0.010 | 0.90 – 1.20 | 0.15 – 0.30 | – | – |
34CrMo4 | 0.30 – 0.37 | 0.40 | 0.60 – 0.90 | 0.025 | 0.010 | 0.90 – 1.20 | 0.15 – 0.30 | – | – |
42CrMo4 | 0.38 – 0.45 | 0.40 | 0.60 – 0.90 | 0.025 | 0.010 | 0.90 – 1.20 | 0.15 – 0.30 | – | – |
50CrMo4 | 0.46 – 0.54 | 0.40 | 0.50 – 0.80 | 0.025 | 0.010 | 0.90 – 1.20 | 0.15 – 0.30 | – | – |
51CrV4 | 0.47 – 0.55 | 0.40 | 0.70 – 1.10 | 0.025 | 0.010 | 0.90 – 1.20 | 0.10 | 0.10 – 0.25 | – |
58CrV4 | 0.54 – 0.62 | 0.40 | 0.70 – 1.10 | 0.025 | 0.010 | 0.90 – 1.20 | – | 0.10 – 0.20 | – |