Find out more: bluemint-steel.com
Selected pladur® products for multistory construction
For more information, click on a photo.
Overview of pladur® products by industry
pladur® for multistory construction
pladur® for industrial buildings
pladur® for doors & gates
pladur® for home appliances
pladur® for commercial vehicles
pladur® for energy and solar industry
State-of-the-art coil coating technology: variety of colors and surfaces made of steel
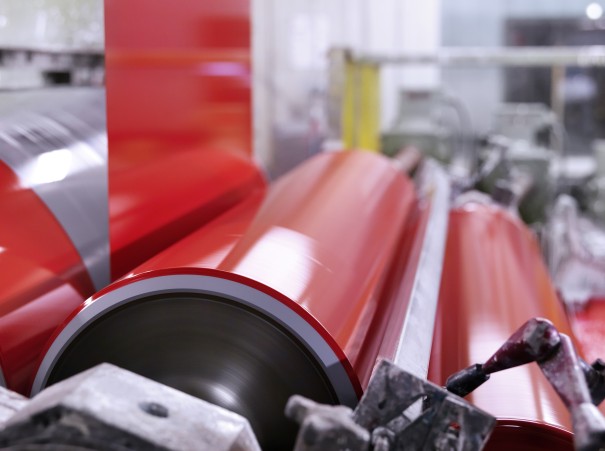
thyssenkrupp Steel has state-of-the-art, organic coil coating lines on which we manufacture our pladur® products in an environmentally friendly and resource-conserving manner. We are constantly expanding our portfolio. In doing so, we attach great importance to customer orientation: In all coil coating developments, we pay attention to the application area and function, and even adapt our products to the manufacturing process of our customers. The spectrum of surface finishes of pladur® ranges from deep matt through high-gloss, smooth, with a light texture modeled on nature down to custom designs. Bending, drawing, press braking, profiling, stamping and roll forming − our organic coil-coated strip and sheet can be shaped without any problems. Moreover, we set great store by protection: pladur® products from thyssenkrupp Steel are optimally protected against corrosion and UV radiation − and EDP-certified.
pladur® coil-coated products: technical information
Base material for pladur®: Mild steel
DIN EN 10130, DIN EN 10346
SURFACE FINISHING | ||||||
---|---|---|---|---|---|---|
Steel grade designation | Standard designation | -/UC | Z/GI | ZM | AS | ZA |
DC01 | DC01 | |||||
DX51D | DX51D | |||||
DX52D | DX52D | |||||
DX53D | DX53D | |||||
DX54D | DX54D | |||||
DX56D | DX56D | |||||
Available -/UC: Uncoated Z/GI: Hot-dip galvanized ZM: ZM Ecoprotect® AS: Aluminum silicium coated ZA: galfan® |
Base material for pladur®: Micro-alloyed steel
DIN EN 10268
SURFACE FINISHING | ||||||
---|---|---|---|---|---|---|
Steel grade designation | Standard designation | -/UC | Z/GI | ZM | AS | ZA |
HC300LA | HC300LA | |||||
Available -/UC: Uncoated Z/GI: Hot-dip galvanized ZM: ZM Ecoprotect® AS: Aluminum silicium coated ZA: galfan® |
Base material for pladur®: High-strength IF steel
DIN EN 10346
SURFACE FINISHING | ||||||
---|---|---|---|---|---|---|
Steel grade designation | Standard designation | -/UC | Z/GI | ZM | AS | ZA |
HX220YD | HX220YD | |||||
Available -/UC: Uncoated Z/GI: Hot-dip galvanized ZM: ZM Ecoprotect® AS: Aluminum silicium coated ZA: galfan® |
Base material for pladur®: Structural steel
DIN EN 10 346
SURFACE FINISHING | ||||||
---|---|---|---|---|---|---|
Steel grade designation | Standard designation | -/UC | Z/GI | ZM | AS | ZA |
S220GD | S220GD | |||||
S250GD | S250GD | |||||
S280GD | S280GD | |||||
S320GD | S320GD | |||||
S350GD | S350GD | |||||
Available Further grades on request. -/UC: Uncoated Z/GI: Hot-dip galvanized ZM: ZM Ecoprotect® AS: Aluminum silicium coated ZA: galfan® |
Coating systems
Substance class | Abbreviation1 | Coating material |
---|---|---|
Liquid coating | EP | Epoxy |
SP | Polyester | |
SP-PA | Polyamide modified polyester | |
HDP-PS | High Durable Polymer Polyester | |
PUR | Polyurethane | |
PUR-PA | Polyamide modified polyurethane | |
FEVE | Polyfluoroethylene / vinyl ether | |
PVDF | Polyvinylidene fluoride | |
Foil | PE (F) | Polyethylene (Foil) |
PET (F) | Polyethylene terephthalate (Foil) | |
PVC (F) | Polyvinyl chloride (Foil) |
Delivery forms and dimensions
THICKNESS from_to in mm |
WIDTH from_to in mm |
LENGTH from_to in mm |
|
---|---|---|---|
Strip | 0.40 − 3.00 | 600 − 1,750 | |
Sheet | 0.40 − 3.00 | 600 − 7,750 | 450 − 6,00 |
Special dimensions | 0.25 − 2.00 | 100 − 640 | 100 − 7,000 |
Slit strip | 0.40 − 3.00 | 20 − 599 | |
Special dimensions on request. Not all thickness and width combinations are possible. |