Hot-dip galvanized pallet racks.
Availabe steel grades
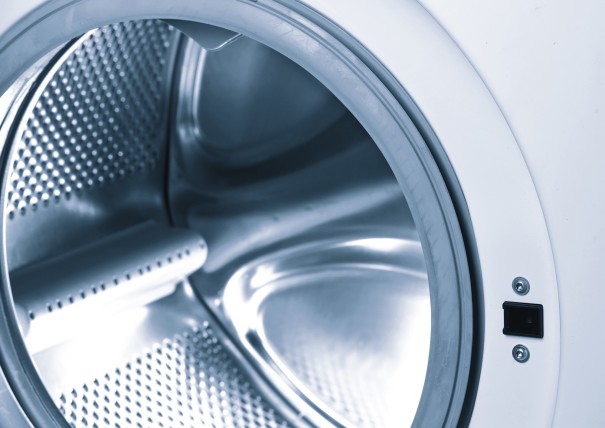
Hot-dip coated sheet (Z/GI) is available in different grades of deep-drawing steels, general structural steels, micro-alloyed steels, and multi-phase steels.
For the automotive sector, we supply hot-dip coated sheet (GI) in accordance with VDA 239-100.
Deep-drawing steel
DIN EN 10346
SURFACE FINISHING | |
---|---|
Steel grade | Z |
DX51D | |
DX52D | |
DX53D | |
DX54D | |
DX56D | |
DX57D | |
DX58D |
Hot-dip coated structural steel
DIN EN 10346
SURFACE FINISHING | |
---|---|
Steel grade | Z |
S220GD |
|
S250GD |
|
S280GD |
|
S320GD |
|
S350GD |
|
S390GD | |
S420GD | |
S450GD |
High-strength IF steel
DIN EN 10346
SURFACE FINISHING | |
---|---|
Steel grade | Z |
HX160YD | |
HC180Y / HX180YD | |
HC220Y / HX220YD | |
HC260Y / HX260YD |
Bake hardening steel
DIN EN 10346
SURFACE FINISHING | |
---|---|
Steel grade | Z |
HC180B / HX180BD | |
HC220B / HX220BD | |
HC260B / HX260BD |
Micro-alloyed steel
DIN EN 10346
SURFACE FINISHING | |
---|---|
Steel grade | Z |
HC260LA / HX260LAD | |
HC300LA / HX300LAD | |
HC340LA / HX340LAD | |
HC380LA / HX380LAD |
|
HC420LA / HX420LAD | |
HC460LA / HX460LAD | |
HC500LA / HX500LAD |
Dual-phase steel
DIN EN 10346
SURFACE FINISHING | ||
---|---|---|
Steel grade | Reference grade DIN EN 10346 |
Z |
DP-K® 290Y490T |
HCT490X | |
DP-K® 330Y590T |
HCT590X | |
DP-K® 330Y590T DH | – | |
DP-K® 440Y780T | HCT780X | |
DP-K® 440Y780T DH | – | |
DP-K® 440Y780T HHE | – | |
DP-K® 500Y780T | – | |
DP-K® 590Y980T | HCT980X | |
DP-K® 700Y980T | HCT980XG | |
DP-K® 780Y1180T | – | |
DP-K® 900Y1180T | – |
Complex-phase steel
DIN EN 10346
SURFACE FINISHING | ||
---|---|---|
Steel grade | Reference grade DIN EN 10346 |
Z |
CP-W® 660Y760T | HDT760C | |
CP-W® 800 | - | |
CP-K® 570Y780T | HCT780C | - |
CP-K® 780Y980T | HCT980C | |
CP-K® 900Y1180T | - |
Chassis steel
DIN EN 10346
SURFACE FINISHING | ||
---|---|---|
Steel grade | Reference grade DIN EN 10346 |
Z |
CH-W® 660Y760T | HDT760C |
Retained-austenite steel (TRIP steel)
DIN EN 10346
SURFACE FINISHING | ||
---|---|---|
Steel grade | Reference grade DIN EN 10346 |
Z |
RA-K® 400Y690T |
HCT690T |
Ferritic-bainitc-phase steel
DIN EN 10346
SURFACE FINISHING | ||
---|---|---|
Steel grade | Reference grade DIN EN 10346 |
Z |
FB-W® 300Y450T | HDT450F | |
FB-W® 460Y580T | HDT580F |
Hot-dip galvanized flat product with very close thickness tolerances
DIN EN 10346
SURFACE FINISHING | |||
---|---|---|---|
Steel family | Steel grade | Standard name | Z |
Mild steel for cold forming |
scalur®+Z DX51D | DX51D | |
scalur®+Z DX52D | DX52D | ||
Hot-dip coated structural steel | scalur®+Z S220GD | S220GD | |
scalur®+Z S250GD | S250GD | ||
scalur®+Z S280GD | S280GD | ||
scalur®+Z S320GD | S320GD | ||
scalur®+Z S350GD | S350GD | ||
scalur®+Z S390GD | S390GD | ||
scalur®+Z S420GD | S4250GD |
||
scalur®+Z S450GD | S450GD | ||
Microalloyed steel | scalur®+Z HX260LAD | HX260LAD | |
scalur®+Z HX300LAD | HX300LAD | ||
scalur®+Z HX340LAD | HX340LAD | ||
scalur®+Z HX380LAD | HX380LAD | ||
scalur®+Z HX420LAD | HX420LAD | ||
scalur®+Z HX460LAD | HX460LAD | ||
scalur®+Z HX500LAD | HX500LAD | ||
Complex-phase steel | scalur®+Z HDT760C | HDT760C |
Serial production
Tolerances
Dimensional and shape tolerances to EN 10 143.
Surfaces
Available surface finishes, hot-dip coated
Minimum coating two-sided sample [g/m2] | Auflage je Seite an Einflächenprobe [μm] | ||||
---|---|---|---|---|---|
Coating | Specification | Triple spot sample | Single spot sample | Thickness1 | Typicl thickness |
Z100 | DIN EN 10346 | 100 | 85 | 5 – 12 | 7 |
Z140 | DIN EN 10346 | 140 | 120 | 7 – 15 | 10 |
Z200 | DIN EN 10346 | 200 | 170 | 10 – 20 | 14 |
Z225 | DIN EN 10346 | 225 | 195 | 11 – 21 | 16 |
Z275 | DIN EN 10346 | 275 | 235 | 13 – 27 | 20 |
Z350 | DIN EN 10346 | 350 | 300 | 17 – 33 | 25 |
Z450 | DIN EN 10346 | 450 | 385 | 22 – 42 | 32 |
Z600 | DIN EN 10346 | 600 | 510 | 29 – 55 | 42 |
Processing of hot-dip coated sheet (Z)
Forming
All common forming processes used for cold rolled sheet can be used for hot-dip coated sheets if the die geometry and die surface are matched to these materials. The hot-dip galvanization (coating) of sheets in conjunction with the surface topography exerts a decisive influence on the tribology of the forming process.
The characteristic parameter is the friction coefficient μ. At thyssenkrupp Steel, the friction coefficient is determined in the drawing test between plane parallel tools. Compared with uncoated sheet (0.14 ≤ μKB ≤ 0.18), hot-dip galvanized sheet has a lower mean friction coefficient (0.08 ≤ μZ ≤ 0.12). The scatter band results from the roughness spectrum, which is set in production to customer requirements. When changing over from a different surface finish (coating) to hot-dip galvanized sheet, the blank shape, blankholder forces or the geometry of the drawing bead may have to be adapted to the flow behavior of the material in the flange area. The only exception is the changeover from zinc-aluminum coated galfan® sheet to hot-dip galvanized sheet.
To avoid coating abrasion, which tends to occur more when forming with short cycle times, the die surface must be completely smooth. thyssenkrupp Steel measures abrasion using the draw-bead test. Hot-dip galvanized sheet displays almost comparable measurable abrasion rates (0.2 to 0.8 g/m2) to uncoated sheet on which abrasion can also be measured (0.5 to 1.0 g/m2).
Processing instructions for joining
All thermal and mechanical joining techniques can be used, as can adhesive bonding and sealing. However, the particular properties of the hot-dip zinc coating require the processing parameters for some joining techniques to be adapted from those used for ungalvanized cold rolled sheet. Joining techniques which do not impair the surface, i.e., which preserve the anticorrosion properties of the coating, such as clinching and adhesive bonding are continually gaining in importance. However, resistance spot welding, inert gas, and laser welding remain the most frequently used joining processes. The first of these, in the form of spot, projection and roll seam welding, has largely come to dominate in automobile manufacturing. These processes are easy to automate, cause little surface damage or component distortion and do not require weld fillers.
In comparison with uncoated cold rolled sheet, a higher welding current and higher electrode force must be applied when resistance spot-welding galvanized sheets, as the coating has a lower contact resistance. The higher thermal and mechanical loads and the tendency to electrode pick-up with the zinc coating reduce the tool life in terms of components processed.
These factors can be counteracted by the use of a suitable electrode material, e.g. CuCrZr, an adapted electrode geometry and adequate electrode cooling coupled with optimized process control. For example, a stepper control is used to increase the welding current in stages and so considerably increases the number of components that can be processed by a set of electrodes. Milling the electrodes after a specific number of weld points has also proved effective in this respect.
When fusion welding is used, the coating metal in the area of the weld seam burns. A fusion welding process that does not introduce much heat to the weld seam area should therefore be selected in order to produce the minimum possible degradation of the corrosion protection.
Laser welding has proven to be the ideal fusion welding method. A slower welding speed than that used with cold rolled sheet improves degassing of the weld pool and avoids the formation of pores. Fumes containing Zn oxides arise when welding galvanized sheet. The quantity of these fumes is largely determined by the coating thickness and the welding process. Adequate ventilation and extraction is essential in any event. Under unfavorable conditions, e.g., in small rooms, an extraction system should be fitted as close as possible to the source of the welding fumes.
Corrosion protection
The assignment of the protective effect of hot-dip galvanized sheet according to DIN EN 55634-1 to the corrosivity categories/corrosion loads C1 to C5 is given as C2(L) and C2(M) for coating Z100 with a coating thickness of 7 μm and as maximum C3(L) for coating Z275 with a coating thickness of 20 μm. In general, the corrosion protection increases with increasing zinc coating.