DH stands for more ductility
A new class of dual-phase steels from thyssenkrupp Steel now offers around 30 percent more elongation compared to conventional grades in this steel family. They bear the designation DH – Ductility High. Materials with strength classes of 600 and 800 MPa are currently being used successfully for series production; grades with strength of 1,000 and 1,200 MPa are in an advanced testing stage. They will open up completely new possibilities of cost-effective lightweight construction both in combustion-engine vehicles and in hybrid and electric vehicles.
Higher yield strength improves crash performance
If crash performance is a key factor in the design of a component, grade variants with increased strength can provide a plus in energy absorption capacity. These products are marked with HY and complement the wide portfolio of AHSS steels at thyssenkrupp Steel, alongside classic dual-phase steels and ductility-high variants.
Dual-phase also in the outer skin
High-strength dual-phase steel DP-K® 290Y490T is also interesting for use in outer skin applications. The steel grade is characterized by a high dent resistance combined with reduced sheet thickness. It is available with all standard corrosion protection coatings in outer panel quality. Thicknesses down to 0.55 millimetres also open up maximum lightweight construction potential in the area of doors and closures in particular.
Product range, DIN EN and VDA
thyssenkrupp supplies the following steel grades as per the product information or the reference steel grades in accordance with the respective standards.
Dual-phase steel
SURFACE FINISHING | ||||||
---|---|---|---|---|---|---|
Steel grade | Reference grade DIN EN 10338, 10346 |
Reference grade V DA 239-100 |
-/UC | Z/GI | ZF/GA1 | ZM |
DP-W® 300Y530T | – | – | ||||
DP-W® 330Y580T | HDT580X | HR330Y580T-DP | ||||
DP-W® 300Y580T | – | – | ||||
DP-K® 290Y490T |
HCT490X | CR290Y490T-DP | * | * | ||
DP-K® 330Y590T |
HCT590X | CR330Y590T-DP | ||||
DP-K® 330Y590T DH | – | CR330Y590T-DH | ||||
DP-K® 420Y590T | – | – | ||||
DP-K® 440Y780T | HCT780X | CR440Y780T-DP | ||||
DP-K® 440Y780T DH | – | CR440Y780T-DH | ||||
DP-K® 440Y780T HHE | – | CR440Y780T-DP | ||||
DP-K® 500Y780T | – | CR500Y780T-DP | ||||
DP-K® 590Y980T | HCT980X | CR590Y980T-DP | ||||
DP-K® 700Y980T | HCT980XG | CR700Y980T-DP | ||||
DP-K® 780Y1180T | – | CR780Y1180T-DH | ||||
DP-K® 900Y1180T | – | – |
1. With different mechanical properties on request.
Serial production for unexposed applications
Serial production for unexposed and exposed applications
* as well as exposed applications in primetex® finish
-/UC: Uncoated
Z/GI: Hot-dip zinc coating
ZF/GA: Galvannealed
ZM: ZM Ecoprotect®
DH: Steel grades with improved formability
HHE: Steel grades with improved hole expansion
Notes on applications and processing
Material characteristics
Hot and cold-rolled dual-phase steels offer a particularly attrative combination of high strength, low yield point, good cold formability and weldability due to their concerted microstructure of ferrite and martensite components.
This high strain-hardening capacity reduces the risk of local constriction of the material during the forming process and induces a strong increase in the component’s yield point in the worked areas even at low degrees of deformation..
The microstructure consists predominantly of a soft ferrite matrix, in which a second, hard, mainly martensitic phase is embedded in pockets. The ferrite content is up to 90%. In addition to martensite, austenite and bainite components can also exist, thus improving formability. In nital etching, the grain boundaries are well contrasted. Color etching according to Klemm contrasts the grain surfaces. The grain surfaces of the ferrite appear in brown or blue hues; martensite is brown; structurally weak martensite and austenite are shown in white.
Structural example of cold-rolled DP steels
Forming
Hot-rolled dual-phase steels DP-W® are particularly suitable for weight-saving production of wheels, chassis parts, profiles, body reinforcements, etc. Cold-rolled dual-phase steels, steels DP-K® are suitable for both complex structural parts, e. g., side members and cross members, as well as stretch-formed exterior parts with special requirements in terms of buckling strength (doors, roofs, trunk lids). The choice of the right type for a given strength level must also be made with a special focus on the actual anticipated forming stresses. This allows optimum leveraging of specific benefits so that the steels can also be used for difficult drawn parts.
Due to the good strain-hardening behavior, expressed by a relatively high n-value, dual-phase steels exhibit high resistance to local constriction, as a larger area of material is involved in the deformation zone due to greater strain hardening. The microstructure of dual-phase steels, composed of hard martensite and soft ferrite, which promotes strain hardening, as well as the distinct cutting-edge hardening in mechanical cutting substantially impact the good forming potential in the trim cutting-edge area. For engineering design, e.g., in case of through-hole extensions or the height of drawn flanges in corner areas, this must be taken into consideration. Small bending and drawing radii relative to the respective thicknesses should thus be avoided. In such cases, it is recommended to choose the yield-optimized variants. Plasticization must be designed to be as homogeneous as possible in order to improve the dimensional accuracy of the worked components. The presses should have high pressing and hold-down force potentials. As a guideline, the tensile strength level should be considered here, compared with known materials. Upstream straightening equipment must also be designed accordingly. Special attention must be paid, as the strength level of dual-phase steels increases, to the design of the forming and cutting tools. Tool requirements are exacting, especially in cutting. In addition to a sufficient hardness of> 60 HRC, it is important to select suitable tool materials to simultaneously ensure high ductility, thus preventing premature breaking of the cutting-edges. By means of specific rounding of the cutting edge in the order of about 50 μm, the edge strength of the tools can be optimized. The cutting gap must be designed to take the material thickness into account and should be (as a guideline) ≥ 10% of the sheet thickness.
A sufficient supporting hardness must be achieved for the forming tools. A segmented structure of the forming tools is common today. In highly stressed areas, the use of high speed steels may be necessary. These include 1.3343 or equivalent materials produced by powder sintering. In addition, tool coatings such as CVD (TiC-TiN coating) can minimize tool wear.
Processing instructions for joining
DP steels principally support welding well in same-grade joints or in hybrid joints with other common steel grades. The precondition is welding parameters matched to the material.
Resistance spot welding
For spot welding of dual-phase steels, the same equipment can be used as for welding unalloyed deep drawing steels. Compared to same-thickness steel grades of lower strength, the welding zone tends to shift toward lower currents. At the same time, the setting range narrows slightly, but this can be largely compensated for by increasing the electrode force and welding currents. An extension of the current flow times, or for example the use of multi-pulse welding in line with SEP 1220-2, can also have a favorable effect on the width of the welding zone.
In resistance spot welding of galvanized sheets, the welding currents must be increased due to the higher conductivity of the coating compared with the base material (substrate). In addition to this, increasing the electrode force and welding time has a favorable effect on the welding zone. In addition to the sheet type, surface and thickness combination, other factors, e.g., the type of electrode used, play an important rolein determining optimum joining parameters.
MIG arc brazing
Information sheet DVS 0938-2 “Arc brazing” describes brazingof steels up to a tensile strength of approximately 500 MPa. As the material described is above this tensile strength, it is advisable to check the component-specific suitability of brazing.
Fatigue strength and crash performance
As already described in the product information, dual-phase steels have a high strain-hardening capacity combined with high yield point values. The high yield point and high tensile strength are evidenced by high fatigue limits. Fine and dispersed distribution of martensite and ferrite avoids any adverse effect on the fatigue limit on account of the strength difference between the structural components of ferrite and martensite. Higher strength values due to work hardening as an effect of deformation, including the bake-hardening effect, contributeto the advantageous material behavior. The high level of strength and the high strain-hardening capacity make dual-phase steels ideal for crash energy absorbing components.
Competence team: We have internalized what dual-phase steels need to achieve
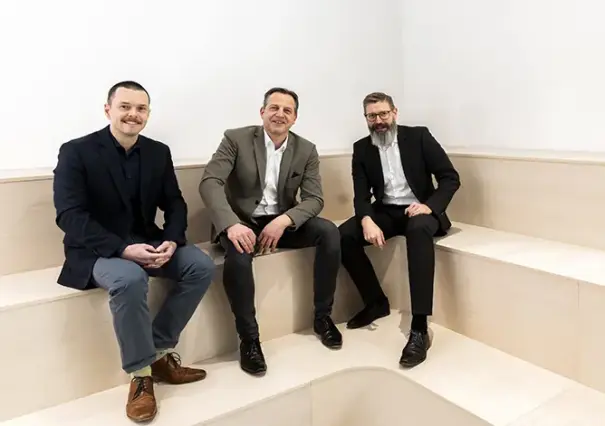
The interdisciplinary competence team behind the dual-phase steels consists of Research and Development, Application Technology and Product Management. The team's specialists understand market requirements, leverage the potential of specific customer benefits and deliver customized solutions.
Dual-phase steels are like the Swiss Army knife in thyssenkrupp Steel's product portfolio. As classic universal grades for crash-relevant structural components in car body construction, they show their potential when a balance is required between high and ultra-high strengths, and good forming and joining properties. This is why they play an important role in lightweight construction, and especially in electric mobility in which the demands for crash safety and battery protection are extremely high. Their share among multiphase lightweight structural steels for cold forming has been rising for years, and currently stands at an impressive 90 percent. There is nothing to suggest that demand will weaken. On the contrary: steel not only has an excellent price/performance ratio, but also represents the simplest way of saving weight efficiently in lightweight vehicle construction. As a product manager for multiphase steels at thyssenkrupp Steel, Dr. Patrick Kuhn has also been the direct contact for all questions relating to the product portfolio for several years now. He raises customer awareness of efficient and sustainable lightweight construction solutions: "The most sustainable material, is always the one that is not produced in the first place. Here, we are not only talking about the basic material but also alloying elements, of course, which can all be saved as resources. That's why steel – and dual-phase steels in particular – are unavoidable in lightweight construction."
Correct answers to complex questions
The team's secret of success with DP steels is to respond precisely to the requirements of the market, and to work out what is essential in the development of a successful product. "What makes the grade?" or: "Which properties are critical?" These are just a few of the many questions on which Product Management, Application Technology and Steel Development work closely together to find the right answers. It is a general rule: Complex component geometries continue to set limits on the use of ever higher strengths for weight optimization in the automotive industry. Whereas forming operations can still be carried out without problems at 600 MPa, doing this might no longer be readily feasible if a higher strength is used. DP steels provide a remedy here: "We have internalized what dual-phase steels need to achieve, and we are now able to supply the right DP steel for every application. There are even three different variants for each strength class. This gradation of the portfolio is something really special on the market," explains Dr. Patrick Kuhn. Targeted development work forms the basis for creating such a differentiated product range. This is where Nicholas Winzer, among others, comes in. He has been working at thyssenkrupp Steel for eight years now, and conducts important fundamental research into dual-phase steels. "It's about balancing material concepts in such a way that efficiency and stable processing generate added customer value." His core topics include, for example, investigating and optimizing the edge cracking sensitivity of multiphase steels. "Compared to other steel grades, DP grades are more prone to cracking at the punched edges during the forming processes. The better we can get a handle on this problem, the better a material can be formed into the desired shape."
Efficient improvements for perfect products
Winzer and his colleagues have many years of experience under their belts, thanks to which grades from the 600 to the 1,200 strength class score particularly well when processed in the stamping shop. The hole expansion ratio, which is decisive for edge cracking sensitivity, has been significantly increased in all classes. "Our main attention is always on developing our products efficiently and optimally. In this case, we were able to achieve the desired edge cracking sensitivity by changing the annealing process, for example. We did not have to intervene at the chemical level."
The pursuit of high-performance products is positively fueled within the company by the Application Technology department. Here, the team has to put itself in the customer's shoes and understand exactly what their colleagues need. Thorsten Beier from the Forming Technology department explains: "Crash safety plays a particularly important role when building a car body. Then, a key question is: Which material do we need to use where, and with which properties? Our analyses can provide us with important impetus for the further improvement of materials in research and development." Our customers' requirements are also becoming increasingly specific. Understanding local properties such as robustness to edge cracking plays an important role in addition to familiar global properties.
Beier, who has called thyssenkrupp Steel his professional home for more than two decades now, is involved with virtual methods for designing forming processes and components, among other things. These are used to investigate the local and global behavior of the materials – for example, how far a material can be deformed until necking or cracking occurs. "Through our investigations, we ensure that the material will flow into the component and come out of the press as desired, even before it is used at the customer's site." In addition, Beier and the Application Technology team provide advice and support to Product Management and customers on detailed questions: for example, in issues relating to material approval or at shop floor level if irregularities occur during processing. Dr. Patrick Kuhn: "Providing close support to our customers on the wide range of topics relating to multiphase steels is an essential part of our understanding of service."