Steel solutions for electromobility
Potential applications of steel
In keeping with this principle, employees in the Application Technology Center use their decades of processing experience to keep revising and improving the company’s products to incorporate the latest technological possibilities and ensure that they meet the standards required of the materials.
“Our expertise smooths the way for our customers, helping them with the practical use of our material in a way offered by no other steel manufacturer.” This process includes both in-depth, individual consulting and a holistic approach to the technological and financial concept – for customers in any industry.
Automotive application example: innovation drivers
Large-scale concept studies focusing on the topic of mobility always find their way into the spotlight. It doesn’t matter if it’s the NSB® NewSteelBody report published at the start of millennium, which was superseded by the InCar® Group-wide innovation package years later, or InCarplus, which then followed one car generation later.
Crucially, none of these concepts is limited to a specific manufacturer, and the sample applications, proposed solutions, and processing recommendations they contain for innovative steel goods always offer scope for customization and scaling. One example of this is the selectrify® initiative, the company’s latest automotive electromobility concept.
“The automotive industry’s influence on technological development is unrivalled by any other sector,” Eiden explains. “Thanks to our technological expertise and consulting skills, we have acted as a development partner to this sector for years: We worked with Porsche on the first fully galvanized car body back in 1975, and were one of the first companies to switch to press hardening for our structural components.”
How will we use steel in the future?
“Never stand still and never stop thinking about tomorrow – or even the day after!”
That’s the Application Technology motto. You can’t change everything overnight – especially not with production cycles that run for several years at a time. thyssenkrupp Steel’s service as a provider of high-quality flat steel gives its customers new ideas and works with them closely to develop these concepts.
Over the last 50 years, the company has continued to actively evolve in terms of its own processes and products. The automotive industry is often the driving force behind innovations. But both the energy and the construction and packing sectors have also proven influential, be it in the areas of technology, design, or sustainability.
As the decades have passed, the company has grown to become a technological expert that both produces and coats steel, working to order, and always showing its customers the best way to use and work the high-tech, flexible material.
Processes are also decisive when it comes to using steel
To this end, each of the Group’s business units has its own on-site Research and Development department. thyssenkrupp’s steel experts can adjust entire process chains, such as the production process used for hot forming at automotive pressing plants.
thyssenkrupp Steel’s Application Technology Center has helped a huge range of customers in a variety of industries and locations across Germany, from Duisburg and Dortmund to Gelsenkirchen, Bochum, Hohenlimburg, and Andernach.
The company has long since grown beyond its role as a producer of materials, and now also acts as a provider of solutions and services for its customers’ process and product development structures – right up to the series production stage.
Keep moving, keep questioning yourself, and keep evolving – that is the key to long term success. The best way to prepare for the future is to shape it yourself.
Benchmarking – learning from the best
Through its own on-site benchmarking in application technology, thyssenkrupp Steel identifies current industry trends and provides best-practice examples for the advanced use of materials. Steel customers benefit from the pooled knowledge – a classic win-win situation.
"I never guess. It is a capital mistake to theorize before one has data." The quote from the famous English writer Sir Arthur Conan Doyle would be the perfect motto for the Benchmark team formed around graduate engineer Erik Hilfrich. Based in the Duisburg Technical Center in the middle of the plant site, this thyssenkrupp Steel department was launched just two years ago and focuses on analyzing structural parts and their materials. "Our goal is to find out which materials and processes are currently in particular demand among companies and on the market," Hilfrich explains. The results are used to review and optimize the company's own offering and to further develop it in an application-specific manner. The approach is also known as requirements engineering or requirements management.
Material use under the microscope
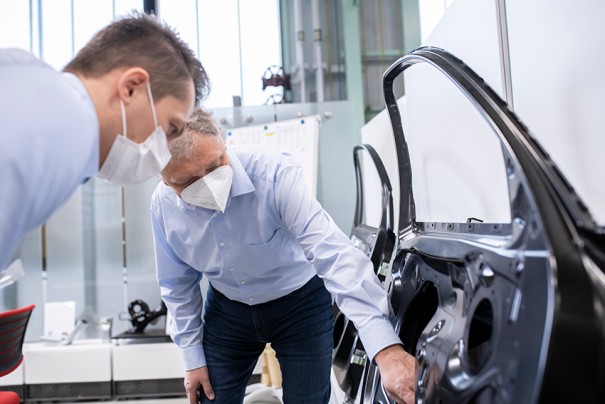
Before thyssenkrupp Steel took over the direction of benchmarking independently in 2019, the job was done by various external service companies from which the required data had to be commissioned and purchased. Even then, the feedback from customers was positive. Now we have all the reins in our own hands and can align the engineering detective work according to our own standards. The focus is on automotive components. Chassis parts, electric motors, vehicle doors, but also structural elements are just a few of many possible examples. In the first step, these are measured, weighed and scanned in the application technology laboratories, among other things, before they are then disassembled and put through their paces in detailed examinations.
The results obtained through benchmarking not only give the experts a more accurate picture of the market, but also help thyssenkrupp Steel's developers gain a deeper understanding of specific requirement profiles. Especially when the company's own materials competencies and analysis capabilities are linked within the steel group. Thus, the material steel is analyzed, evaluated and tested by internal experts in everything from chemistry to processing and specific applications. In the course of the knowledge exchange, the Materials department then receives information from the Innovation department as to which strengths are currently determining the competition in chassis development. In this way, the benchmark professionals set important impulses across departments and throughout the company. In some cases, the investigations even lead to new, more suitable products being recommended to customers. For this purpose, the Application Technology department in Duisburg also conducts targeted workshops for customers – in these times, of course, taking into account all hygiene rules and the currently valid COVID protection regulations.
Application Technology offers workshops for the automotive industry
The interactive workshops are characterized by an inspiring atmosphere and follow a practical concept. Depending on the event, various components are presented in the specially equipped seminar area, which are analyzed together with the clients. Together, they can look at details and discuss best-practice solutions. An example of this is the use of new steel grades for vehicle structures in the automotive industry. This opens up entirely new possibilities for OEMs with regard to the weight and safety challenges associated with electric mobility. "During the workshops, we quickly get into a very fruitful exchange with our contacts about the pros and cons of solutions and can also very efficiently counter any reservations and fear of addressing certain topics," says Kai-Uwe Jentsch, who is primarily responsible for benchmarking in the department. The graduate engineer continues: "We're pleased that companies that had previously avoided steel in certain series have returned to steel after the events."
Optimizing and further developing material use
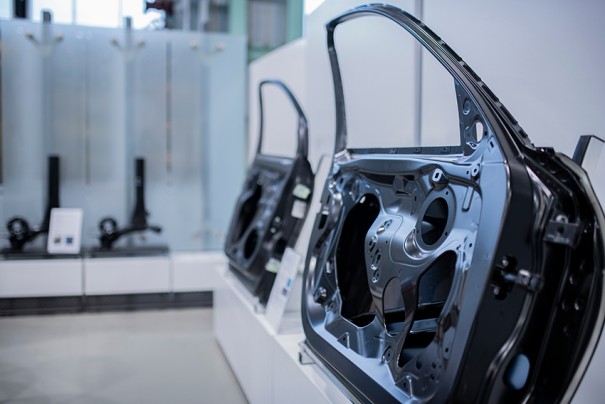
The benchmark workshops provide ample space away from the hustle and bustle of everyday business to highlight industry trends, share research results, and provide customers with application concepts geared to the future. In this way, individual challenges can be solved – such as reducing process costs in the manufacture of components or increasing performance. Graduate engineer Helmut Mebus: "Our benchmarking services are open to both internal specialist departments and our clients, and are missing nothing in terms of quality." Also because the offer addresses the needs of companies in a holistic way. "We can optimize and develop components with both the right materials, innovative technologies and viable concepts."