The highest demands are placed on the performance and efficiency of modern traction motors.
To achieve this, the electrical steel strip must have the lowest possible core losses, as well as high magnetic polarization and strength. Some of these requirements are mutually exclusive – but thyssenkrupp Steel has resolved the conflicting interests with a newly developed top grade for electric mobility, using an optimized alloy concept.
The newly developed top grade for electric mobility 025-125Y420 – which is particularly thin at just 0.25 millimeters – features minimum core losses and a high mechanical strength (Rp0.2) of at least 420 MPa thanks to an optimized alloy concept. It has proven possible to reduce core losses from max. 14 W/kg (027-140Y420) to max. 12.5 W/kg (at 400 Hz and 1 T) compared to the previously best grade, in the same strength class from thyssenkrupp Steel.
With these values, the new grade is one of the leading contenders among all options available in Europe, making it the top grade in the electric mobility segment.
New premium grade achieves top magnetic and strength properties
Improved efficiency for electric motors: Greater range or smaller battery with 025-125Y420
Core losses are significantly influenced by the sheet thickness, alloy and material production process. It determines how efficiently a motor can utilize electrical energy and convert it into rotational energy.
In an electric motor, a low core loss is synonymous with high efficiency. If the efficiency increases, an electric vehicle can cover more miles on one battery charge or the battery capacity can be reduced while maintaining the same range. This saves weight and costs. Our new development, powercore® traction 025-125Y420, is characterized by a very low core loss of max. 12.5 W/kg (400 Hz, 1 T).
High-speed drive motors in modern electric vehicles not only require excellent magnetic properties, they also place exacting demands on the mechanical properties of the electrical steel – primarily on the strength of the material. The high strength of 420 MPa offers the necessary reserves of strength even for highperformance drives, with the possibility of positively influencing the motor design, for example in terms of compactness.
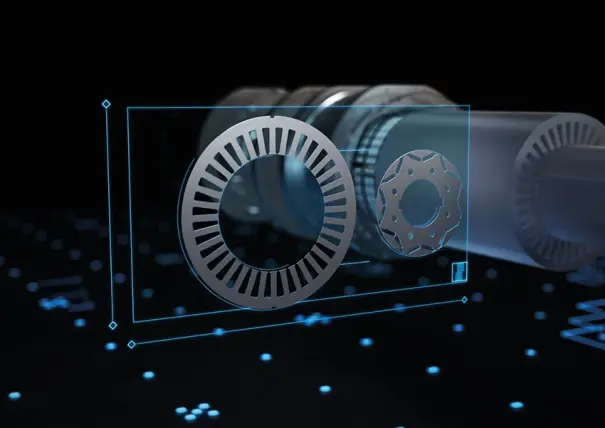
High-speed drive motors in modern electric vehicles not only require excellent magnetic properties, they also place exacting demands on the mechanical properties of the electrical steel – primarily on the strength of the material. The high strength of 420 MPa offers the necessary reserves of strength even for highperformance drives, with the possibility of positively influencing the motor design, for example in terms of compactness.
The combination is the trick: maximum efficiency with our adhesive insulating varnishes
In addition to the quality of the electrical steel grade used, its processing into rotor and stator stacks plays a decisive role in gaining maximum efficiency from the electric motor.
Whereas methods such as interlocking and lamination welding are commonly employed in large-scale production, adhesive stacking ensures that the material properties of the electrical steel strip are optimally retained for the end product, namely the motor: bonding systems avoid the disadvantageous effects of mechanical joining of laminations, which include material damage and short circuits. With adhesive stackings, losses due to unwanted current paths and disturbances in the magnetic flux can be minimized, making it possible to build electric motors with significantly higher efficiency and power density.
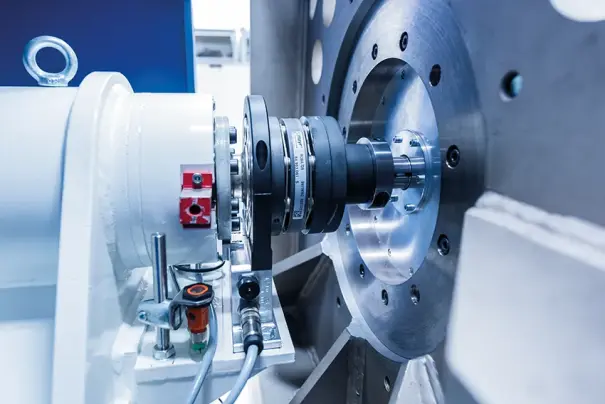
All in all, motor losses can be significantly reduced through adhesive stacking compared to interlocking. Tests with prototypes developed in-house on our own motor test bench have demonstrated that, depending on the operating point, motor losses can be reduced by up to 16 % through adhesive stacking. Further potential for improvement is possible.
Top grade for electric mobility in high-volume series production – Made in Europe
The bar is set high for our modern production facilities to achieve the demanding product characteristics and the high quality of the electrical steel strips.
This is why thyssenkrupp Steel is investing in a state-of-the-art double reversing stand and a coupled annealing and isolating line at its Bochum site. With this configuration, thin electrical steel strips can be rolled with great flatness and the tightest thickness tolerances. They will be manufactured with particularly homogeneous mechanical and magnetic properties. The series ramp-up of the new NO25 grade will take place on new lines at the Bochum site starting in early 2025. Sampling and homologation inquiries can be made immediately.
With the modern and energy-saving units, thyssenkrupp Steel is expanding its capabilities in the production of non-grain-oriented electrical steel so as to meet the increasing demand for thinner and highly silicized materials in the best possible way.
And with the "Made in Europe" cachet – the best quality with topnotch local advisory service and a reliable supply chain for the whole of Europe.