Slag granulation is a process used in the steel industry to process the slag generated during steelmaking. In the process, the hot molten slag is quickly cooled and granulated. The granulated blast furnace sand produced in this way can be used as a valuable raw material in the cement industry.
bluemint® Steel – CO2-reduced steel at the cutting edge.
As Germany's largest producer of high-quality flat steel, we bear a great deal of responsibility. Consequently, we are resolutely pursuing our goal of producing our steel using a completely carbon-neutral pathway by 2045 at the latest.
How we see the future: Following the planned commissioning of our new direct reduction plant, we will increase the available supply of CO2-reduced bluemint® Steel to up to 3 million tons per year. We want to reduce our emissions by more than 30 percent by 2030.
Already saving CO2 today with bluemint® Steel –
RIGHT HERE. RIGHT NOW.
With our bluemint® Steel brand, we are already offering our customers all the proven steel grades with reduced CO2 intensity – without compromising quality, and with the aim of saving as much CO2 as possible RIGHT HERE and RIGHT NOW.
That is why we have developed initial measures that are already reducing CO2 emissions from the existing blast furnace route. We are replacing some of the iron ore that is usually added by high-quality steel scrap, meaning that less coal is needed and CO2 emissions are reduced. When the balance sheet is subsequently drawn up, we see that the product's CO2 emissions are as much as 64 percent lower – something that benefits our customers' Scope 3 balance sheet as well.
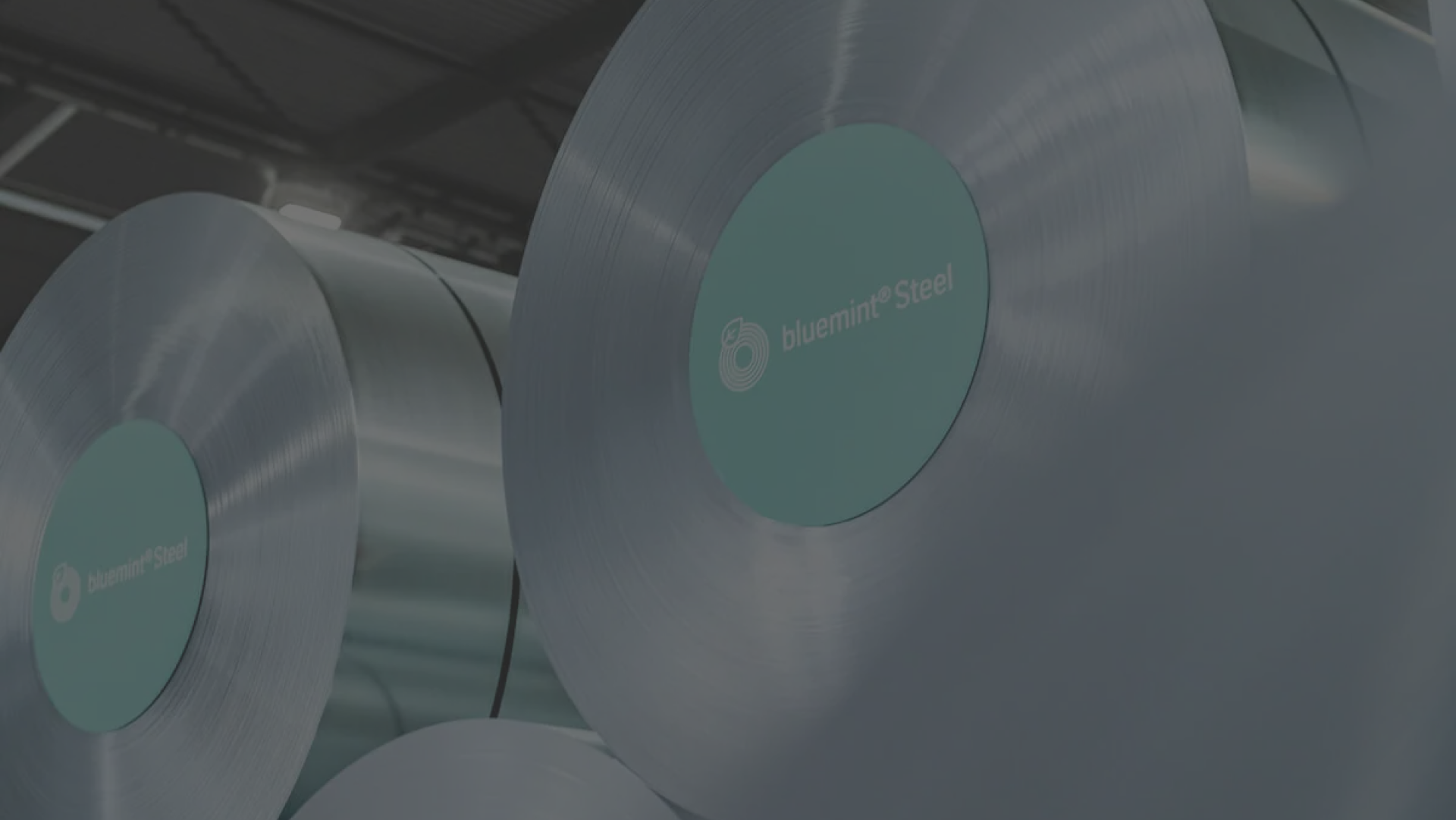
Reducing CO2 today – with bluemint® recycled.
The concept of steels manufactured with reduced carbon
dioxide emissions is of significant interest to many
processing and end-use industries. With bluemint® recycled,
we are already offering precisely that.
By 2045 at the latest: complete decarbonization of our primary steel route.
Until we completely replace our production via the blast furnace route, the use of steel scrap in particular will play an important role for bluemint® Steel. However, the availability of steel scrap will by no means be sufficient to meet the demand for steel over the coming years and decades. A secondary or recycling route can consequently only represent a partial solution. Instead, we need an efficient and carbon-neutral primary steel route, and we are working flat out to achieve this.
Demonstration model DR plant.
An important step for the transformation of the steel industry: construction of the first hydrogen-based direct reduction plant at the Duisburg site with a capacity of 2.5 million metric tons of directly reduced iron (DRI), and an annual saving of up to 3.5 million metric tons of CO2. Construction of the plant on an EPC (engineering, procurement and construction) basis by the SMS group.
Further information about our climate strategy can be found at: https://www.thyssenkrupp-steel.com/climate-strategy
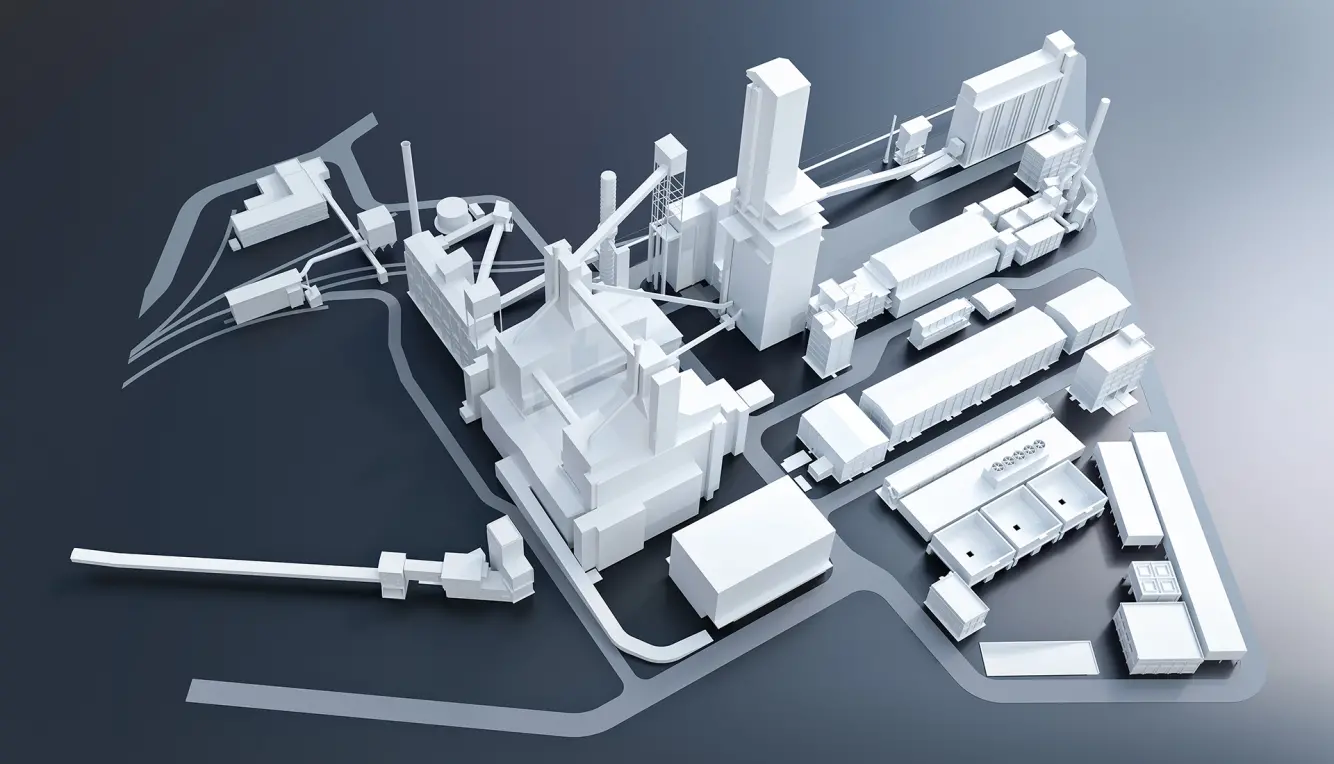
The cast house is the area where the molten hot metal from the melter is poured into what are called transfer ladles, which in turn are transported for further processing in the BOF meltshop.
The melter, also known as Submerged Arc Furnace (SAF), is characterized by its use of a melting process in which the metal is melted openly in a bath, as opposed to closed melting furnaces such as the Electric Arc Furnace (EAF). The SAF enables an efficient heat, which means it plays an important role in the metallurgy.
The direct reduction tower is the central unit of a reduced-CO2 steel production plant that replaces the conventional blast furnace processes. This tower is where the direct reduction of iron from iron ore takes place with the help of reduction gases such as hydrogen (H2). The result is solid, spheroidal iron that is liquefied in the melters before further processing in the steel mill.
The process gas required for the reduction is generated in the reformer.
The reduction gas is reformed at high temperatures from a variable mixture of hydrogen, natural gas and process gases.
The essential raw material, iron ore in the form of pellets, for the direct reduction process is stored in the direct reduction plant's pellet and raw material store. The store is designed to provide a continuous supply to the plant to ensure seamless running of the direct reduction process.
With the construction of our new hydrogen-based direct reduction plant, one of the biggest industrial decarbonization projects worldwide, we will significantly expand the role of bluemint® Steel as a series product. With a capacity of 2.5 million metric tons of directly reduced iron (DRI), we are already able to save up to 3.5 million metric tons of CO2 annually with this first step. By 2045 at the latest, we will be producing exclusively carbon-neutral bluemint® Steel.
Contact
Sales Automotive
Bernhard van Acken
Sales Automotive, thyssenkrupp Steel Europe AG
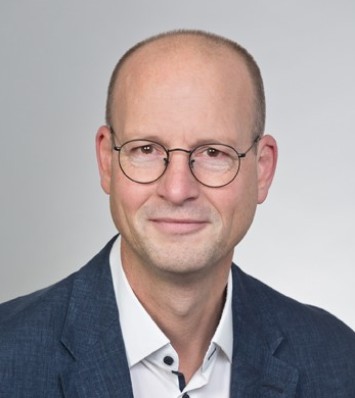
Telephone: +49 203 52-40663
Send emailSales Industry
Axel Pohl
Head of Sales Industry Original Equipment Manufacturer and Steel Service Center, thyssenkrupp Steel Europe AG
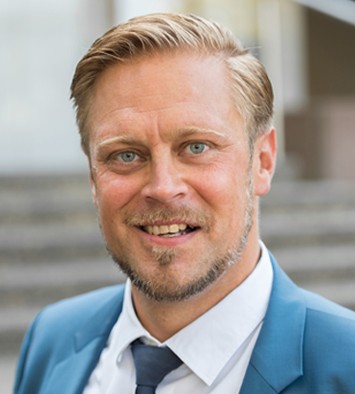
Telephone: +49 2732 599 4578
Send emailSales Industry
Dr. Franz Domenic Boos
Head of Sales SSC HRC & cut to length, Sales Industry
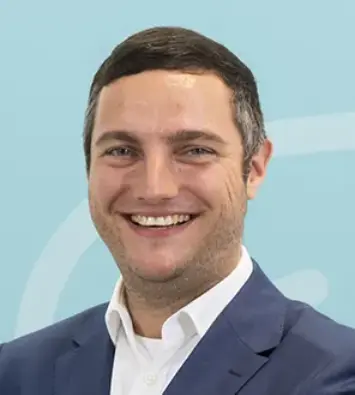
Precision Steel
Dr. Henner Diederichs
Head of Sales, thyssenkrupp Hohenlimburg GmbH
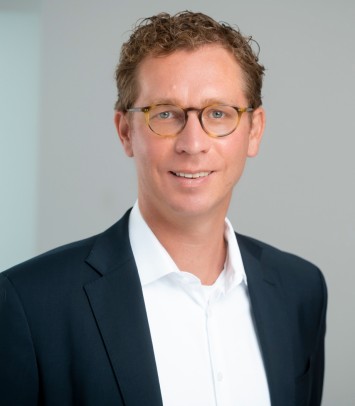
Telephone: +49 2334 91-2758
Send emailPackaging Steel
Thomas Denkel
Vice President Sales, thyssenkrupp Rasselstein GmbH
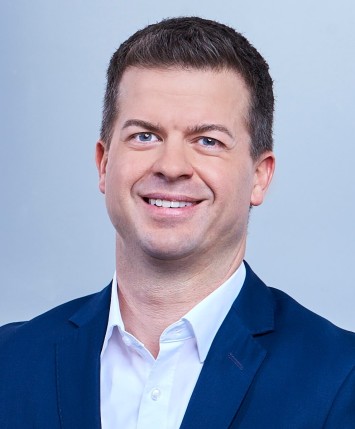
Electrical Steel
Marcel Hilgers
Vice President Customers, Markets & Technology
thyssenkrupp Electrical Steel GmbH
Kurt-Schumacher-Str. 95
45881 Gelsenkirchen
Germany
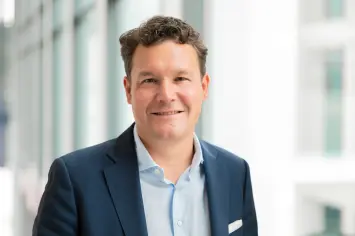
Telephone: +49 209 407 50 - 510
Send emailMark Stagge
Head of Public & Media Relations, thyssenkrupp Steel Europe
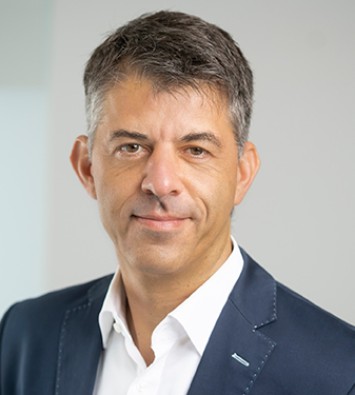
Hannah Kloppert
Business Development bluemint® Steel, thyssenkrupp Steel Europe AG
Telephone: +49 (0)203 52-44126
Send email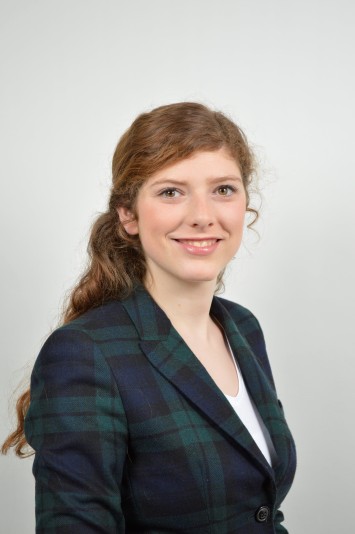