Trade press, Daily press, 2015-11-03, 01:58 pm
Modern fabric filter will further improve environmental situation in Duisburg – NRW environment minister Remmel gives official starting signal for beginning of construction
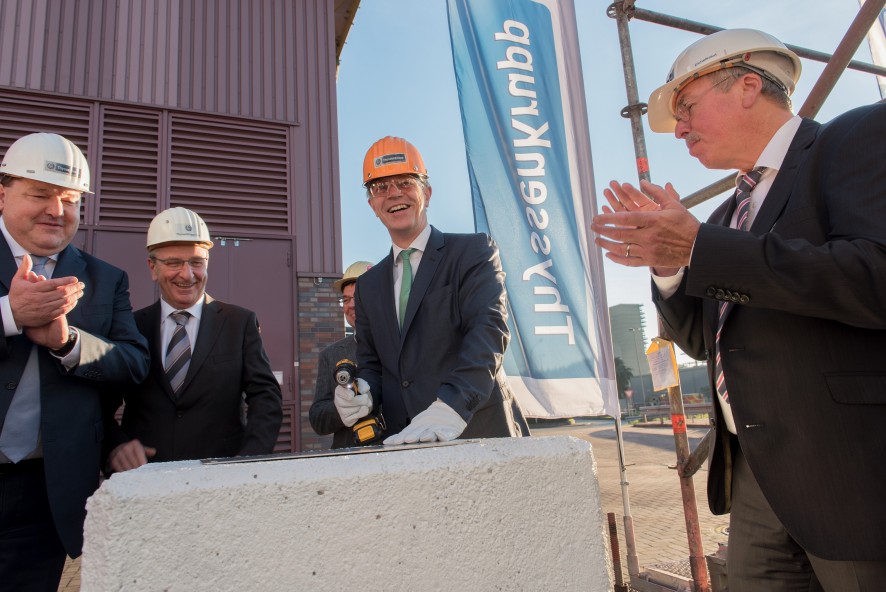
ThyssenKrupp Steel Europe recently began construction of a further modern fabric filter for the Schwelgern sinter plant. The filter will remove additional dust and further improve the environmental situation in Duisburg. “We expect this measure to have a big impact on air quality,” says Andreas Theuer, Head of Environmental and Climate Protection at ThyssenKrupp Steel Europe. The official starting signal for the beginning of construction was given by North Rhine-Westphalia environment minister Johannes Remmel. “These investments are an active contribution to protecting the health of Duisburg’s citizens and protecting the environment. The new filter units are a clear commitment to steel production in Duisburg and an ecological and economic opportunity to prepare for the future,” said Remmel during his visit to the construction site in Duisburg. The new filter unit will go into operation in March 2017 at the latest. ThyssenKrupp Steel Europe is investing around 46 million euros in this project to further significantly reduce dust emissions. In 2014 the steel producer already emitted around 20 percent less dust than in 2010.
In a sinter plant, fine iron ores are mixed with coke and other materials such as lime, heated and baked together. The “cake” is crushed and then cooled. Because of its high gas permeability the finished sinter is ideal for charging in the blast furnace, where it is melted together with other materials to produce pig iron. To make the cake, air is sucked through the ore/coke mix, picking up dust. The dust is captured by several conventional electrostatic precipitators and prevented from escaping into the atmosphere. “Our electrostatic precipitators are already very efficient but we can still improve,” says environmental expert Theuer. The smallest of the three belts in the Schwelgern sinter plant already has a downstream fabric filter. Air that has passed through the electrostatic precipitator flows through around 15,000 three-meter-long extremely fine fabric bags that capture even very fine dust particulates. This filter went into operation in fall 2011 and cleans up to 450,000 cubic meters of waste air per hour. These modern fabric filters can further reduce dust pollution in the air. “We can capture almost 99.99 percent of the sinter dust this way. The air downstream of the filters is really clean, and that means less dust in Duisburg and the surrounding area,” explains Theuer.
Encouraged by the good experience with the first fabric filter, ThyssenKrupp Steel Europe is now installing filters using the same technology for the other two sinter belts. Building work on the filter for the biggest sinter belt has now begun and is set to be completed in early 2017. The new filter will be the biggest of its kind in the world and will capture large additional amounts of dust. “The new filter unit marks another big step towards improving air quality in Duisburg,” says Theuer. The third fabric filter is planned to go into operation by the year 2020.
Iron ore and coke are baked into a sinter “cake” for the blast furnace
Before charging in the blast furnace, fine iron ores first have to be converted into lump form in a sinter plant. In the sintering process a mixture of fine ores, coke and additives such as lime is placed on a sinter belt, ignited under a furnace at temperatures of around 1,200 degrees, and sintered. The combustion air required for the process is sucked through the mixture by large fans to burn the coke. At the end of the sinter belt the “cake” is removed, cooled and crushed to an average particle size of around 20 millimeters. From the Schwelgern sinter plant with its three sinter belts the material is supplied to the four blast furnaces of ThyssenKrupp Steel Europe in the north of Duisburg.