Daily press, 2019-12-13, 02:55 pm
When customers control the rolling mill: thyssenkrupp Hohenlimburg wins award for digitization project
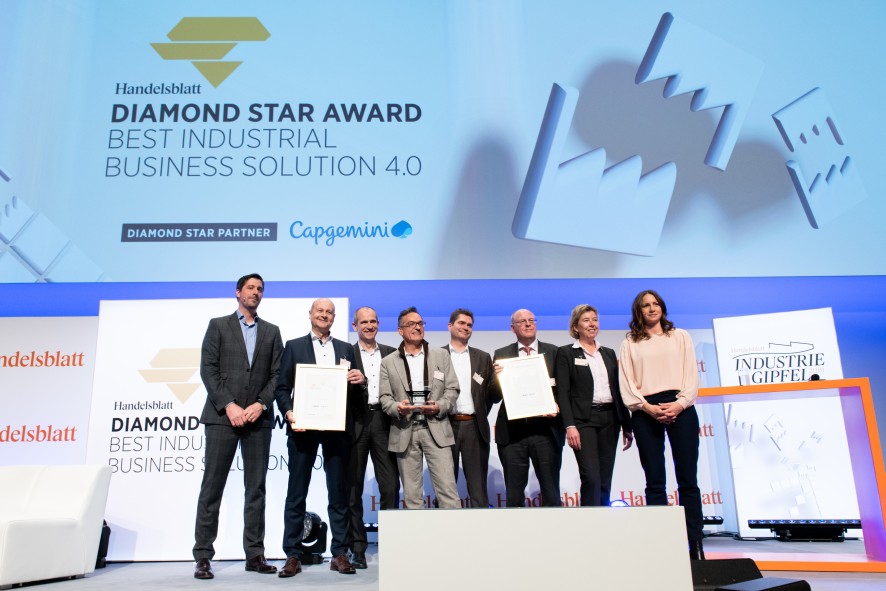
With its digital transformation thyssenkrupp Hohenlimburg has won 2. prize in the “Smart Factory” category of the Handelsblatt newspaper Diamond Star Awards 2019: Customers can log into a system and directly influence the production of their orders. With a lead time of 48 to 72 hours they can define when their precision strip should be rolled at the Hohenlimburg hot rolling mill. At the same time they can modify and update the material properties of the ordered product within technical limits up to just a few hours before rolling. Once final scheduling has taken place they can track the status of production online or via an app, and can for example see whether the starting material is already on the way from Duisburg to Hohenlimburg, what the next production step is and the current shipping status. Another advantage is that customers only receive the material they currently need for their production and can place further orders when necessary – also via app using “one-click ordering”.
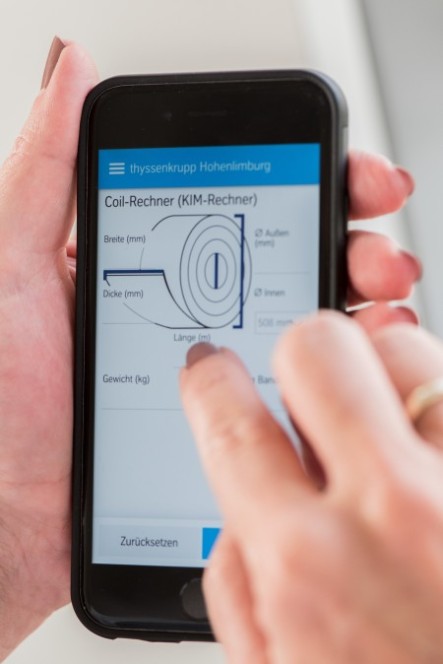
“Rolling as a Service” is unique in the steel sector
Digitizing the order and manufacturing processes in this way enables the business model to be expanded to allow direct customer influence over the business and production process for their materials. This makes production in Hohenlimburg the first step in the joint value chain with the customer who, based on requirements, can schedule their own orders, define material specifications and determine when production should start. 40,000 tons of material have already been produced and shipped in this way. thyssenkrupp Hohenlimburg is bringing digitization to life with its customers, placing them at the center of everything it does: “Rolling as a Service”.
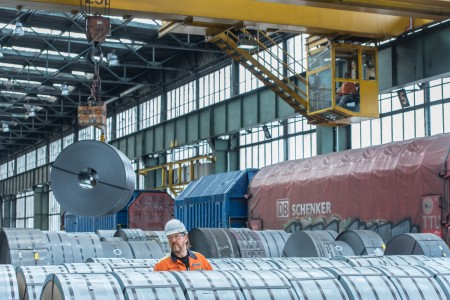
Digital journey beyond company boundaries
The digital connection of machinery and processes at the thyssenkrupp Hohenlimburg hot rolling mill in the spirit of Industry 4.0 goes far beyond the company itself. “Commercial, administrative and technical data are exchanged and linked intelligently,” says Ulrich Schneppe, Head of Information Technology at Hohenlimburg and project manager. “This forms a reliable data basis for business intelligence, digital twins, production apps and much more. We’re on a very exciting digital journey.” And it’s not just customers who can influence production, thyssenkrupp Hohenlimburg also directly controls the continuous caster at its starting material supplier to ensure a reliable starting point for delivery performance and flexibility. “This digitization of the order and manufacturing process integrates us even more closely with customers,” says Norman Baltrusch, CFO of thyssenkrupp Hohenlimburg, emphasizing the importance of the project. “We aren’t just ensuring greater benefits for our customers, we are also improving value creation in our organization.”