The special supplier of hot rolled strip steel
The way to Hohenlimburg leads along the Lenne, a tributary of the Ruhr. To the left and right rises a densely wooded, hilly landscape, which rests on a foundation of natural limestone rocks. Here, where the Ruhr Region and the Sauerland meet, space is scarce, especially for commercial premises. And yet numerous companies – including thyssenkrupp Steel’s digital factory – are headquartered in the Hagen district.
Always keeping an eye on material properties
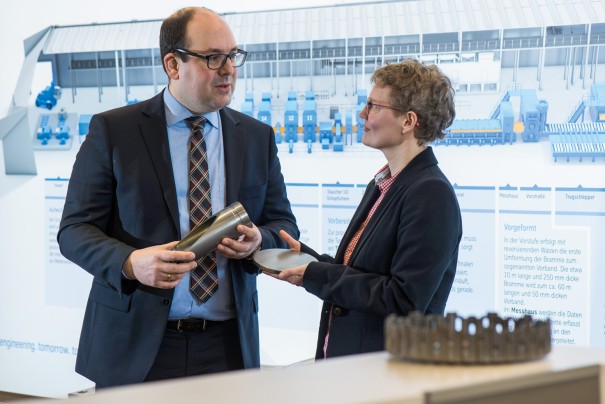
The company produces precision strip in widths of up to 720 millimeters and thicknesses from 1.5 to 16 millimeters. The Hohenlimburg site can supply coil sizes of up to 20.5 kilograms per millimeter of strip width, or batch sizes of a single coil as required. “For us, the focus is clearly on single coil production,” says Matthias Gruß, technical customer consultant at the Precision Steel business unit. The high level of pressure in the machines ensures the perfect mechanical properties: “Because we produce a narrower product, the rolling stands can exert greater pressure, allowing us to roll even high-strength materials with extremely tight tolerances and very homogeneous material properties. Customers can choose between pickled, unpickled, or annealed steel products. Depending on customer requirements, we cut the strip lengthwise or crosswise or supply it with a solidification-free natural edge.
Customers can also decide whether the company cuts the strip lengthwise or crosswise, or supplies it with a solidification-free natural edge. Most of the grades produced in Hohenlimburg are sold to the cold rolling industry or directly to automotive suppliers. Gruß continues: “According to our estimates, around 85 percent of our material ends up in cars.”
Precision strip is used for nearly all car parts
The precision strip steel made in the digital factory is used in nearly all car parts, apart from the chassis. For example, it is used in the processing of:
- Shift forks for transmissions
- Clutch springs
- Brake pistons
- Vibration dampers
- Airbag components
- Axle tubes
- Backrest adjusters for car seats
Digital factory with custom production
Between 25,000 and 30,000 metric tons of structural steel slabs can be stored on site in Hohenlimburg, despite the cramped conditions. thyssenkrupp Steel delivers approximately the same amount of material to its customers every week. Customers also have a say in the processing of final characteristics of the materials – a key advantage. “Our customers can request us to roll out a specific slab at short notice,” says Dr. Anastasia Viviana Höhne, a product developer in Hohenlimburg who designs new steel grades. “Our rolling programs are much smaller and cover a wider quality portfolio than the steel mill in Duisburg. This allows us to be extremely flexible.”
The future has already come to the Hohenlimburg site: Thanks to the digital integration of customers, the production process is even more agile. Digitalization allows all parties to view the progress of an order and stock levels. This enables employees on site to control the production of the primary material and scheduling. “We plan the casting programs based on customer orders and pass them on to HKM, Hüttenwerke Krupp Mannesmann, in Duisburg,” says Gruß of the smart factory. The company recently received an award from Focus Money for this intelligent Industry 4.0 solution.
Sturdy steel through austempering
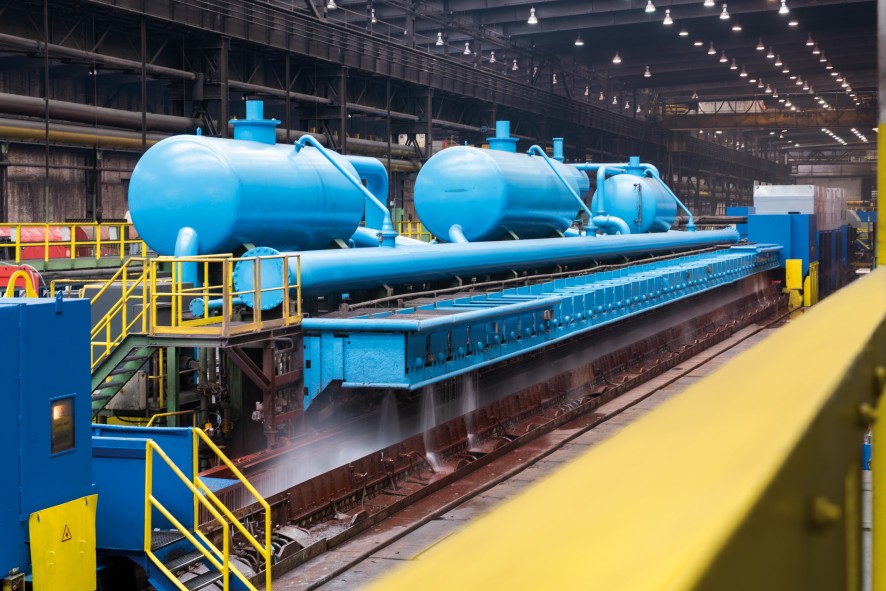
The thyssenkrupp Steel digital factory produces a wide range of materials, including soft, unalloyed steels, microalloyed, low-pearlite fine grain steels, alloyed carbon steels, stainless steel, and numerous other grades. The Hohenlimburg-based company has also been making bainitic steels for some time now. Steels produced through austempering represent a relatively young steel group whose first generally applicable standard was only published in 2015. Precision Steel’s HBS steel is available in mid- to high-level strengths: HBS 600, HBS 800, HBS 900, and HBS 1.000. These grades are ideally suited for the low-weight production of high-strength chassis and structural parts in vehicles – since these are crash-relevant safety components, the steel used to make them needs to be very sturdy. Material innovations and optimized planning and production never represent an end in themselves for our steel experts – instead, they lay the crucial groundwork for making our everyday lives safer and more comfortable.