Spezialist für wamrgewalzten Bandstahl
Der Weg nach Hohenlimburg führt entlang der Lenne, einem Nebenfluss der Ruhr. Zur linken und zur rechten Seite erhebt sich eine dicht bewaldete, hügelige Landschaft, die zumeist aus natürlichen Kalkfelsen besteht. Hier, wo Ruhrgebiet und Sauerland aufeinandertreffen, ist der Platz knapp, besonders für Gewerbeflächen. Und doch haben in dem zu Hagen gehörenden Stadtteil zahlreiche Unternehmen ihren Sitz – so auch die digitale Fabrik von thyssenkrupp Steel.
Materialeigenschaften immer im Blick
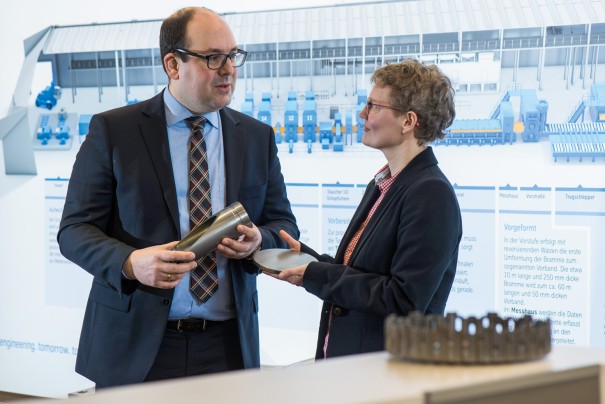
Das Unternehmen stellt Mittelband in Breiten bis 720 Millimeter und Dicken von 1,5 bis 16 Millimeter her. Die Hohenlimburger können Coilgrößen bis zu 20,5 Kilogramm pro Millimeter Bandbreite liefern oder bedarfsgerechte Losgrößen von nur einem Coil. „Für uns steht die Einzelcoilfertigung klar mit im Fokus“, sagt Matthias Gruß, technischer Kundenberater bei der Business Unit Precision Steel. Für die perfekten Materialeigenschaften sorgt der hohe Druck in den Maschinen: „Weil wir schmaler produzieren, haben wir mehr Druck in den Walzgerüsten und können daher auch höherfeste Materialien mit engsten Toleranzen und sehr homogenen Werkstoffeigenschaften walzen.“
Die Kunden wählen bei ihrer Bestellung zwischen gebeizten, ungebeizten oder geglühten Werkstoffen. Außerdem können sie entscheiden, ob das Unternehmen diese mit verfestigungsfreier Naturkante, längs- oder quergeteilt liefert. Die in Hohenlimburg hergestellten Güten gehen zum Großteil in die Kaltwalzindustrie oder direkt an die Autozulieferer. Gruß: „Wir gehen davon aus, dass rund 85 Prozent unseres Materials am Ende im Auto verbaut werden.“
Mittelband fast überall im Automobil
Das Mittelband der digitalen Fabrik steckt eigentlich in fast allen Fahrzeugteilen, außer in der Karosserie. Zum Beispiel wird es verwendet für die Herstellung von:
- Schaltgabeln für Getriebe
- Kupplungsfedern
- Bremskolben
- Schwingungsdämpfern
- Airbagkomponenten
- Achsrohren
- Lehnenverstellern für Pkw-Sitze
Digitale Fabrik mit Fertigung nach Maß
Zwischen 25.000 und 30.000 Tonnen Brammen lassen sich in Hohenlimburg lagern, trotz der beengten Verhältnisse. Etwa die gleiche Menge Material liefert thyssenkrupp Steel wöchentlich an seine Kunden aus. Welcher Art die Werkstoffe sind, kann von ihnen mitbestimmt werden – das bietet einen wertvollen Vorteil. „Unsere Kunden können spontan sagen, wenn sie kurzfristig eine bestimmte Bramme ausgewalzt haben möchten“, sagt Dr. Anastasia Viviana Höhne, die als Produktentwicklerin in Hohenlimburg an der Entwicklung neuer Stahlgüten arbeitet. „Unsere Walzprogramme sind viel kleiner und beinhalten ein größeres Gütenportfolio als in der Hütte in Duisburg, deshalb können wir so flexibel sein.“
Auch die Zukunft hat in Hohenlimburg bereits Einzug gehalten: Denn dank der digitalen Vernetzung zum Kunden läuft der Prozess in der Produktion noch agiler. Durch die Digitalisierung lassen sich der Verlauf eines Auftrags und die Lagerbestände einsehen. Das ermöglicht den Mitarbeitern, Einfluss auf die Herstellung des Vormaterials und die Terminierung zu nehmen. „Anhand der Kundenbestellungen planen wir bei uns im Hause die Gießprogramme und geben diese zu HKM, den Hüttenwerken Krupp Mannesmann, nach Duisburg weiter“, so Gruß über die Smart Factory. Für die intelligente Industrie 4.0-Lösung wurde das Unternehmen vor kurzem von Focus Money ausgezeichnet.
Fester Stahl durch Bainitisieren
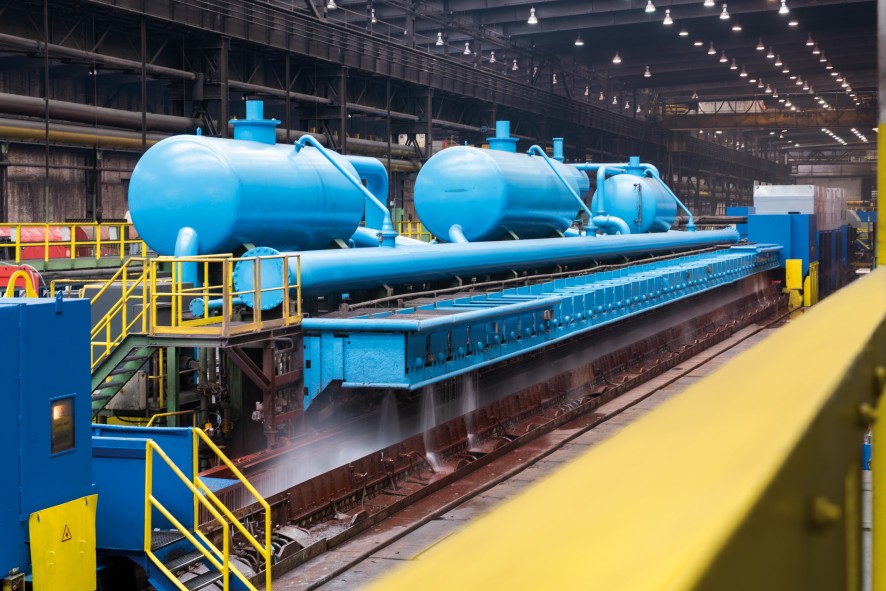
Die digitale Fabrik von thyssenkrupp Steel hat zahlreiche Werkstoffe im Portfolio: darunter weiche, unlegierte Stähle, mikrolegierte, perlitarme Feinkornstähle, legierte Kohlenstoffstähle sowie zahlreiche weitere Güten. Seit einiger Zeit bieten die Hohenlimburger auch bainitische Stähle an. Durch Bainitisieren erzeugte Stähle sind eine relativ junge Stahlgruppe, deren erste allgemein geltende Norm erst 2015 veröffentlicht wurde. Der HBS-Stahl von Precision Steel liegt im mittelfesten bis hochfesten Bereich und ist in unterschiedlichen Festigkeiten verfügbar: als HBS 600, HBS 800, HBS 900 und HBS 1.000. Diese Güten sind bestens für die gewichtssparende Herstellung hochfester Chassis und Strukturteile in Fahrzeugen geeignet. Die feste Qualität ist entscheidend, da es sich dabei um crashrelevante Sicherheitsbauteile handelt. Denn Werkstoffinnovationen und eine optimierte Planung und Produktion sind für die Stahlexperten nie Selbstzweck – sondern eine wichtige Basis, um unseren Alltag angenehmer und sicherer zu gestalten.