Trade press, Daily press, 2015-10-05, 02:04 pm
Tinplate manufacturer ThyssenKrupp Rasselstein investing in efficiency, strengthening its Andernach site
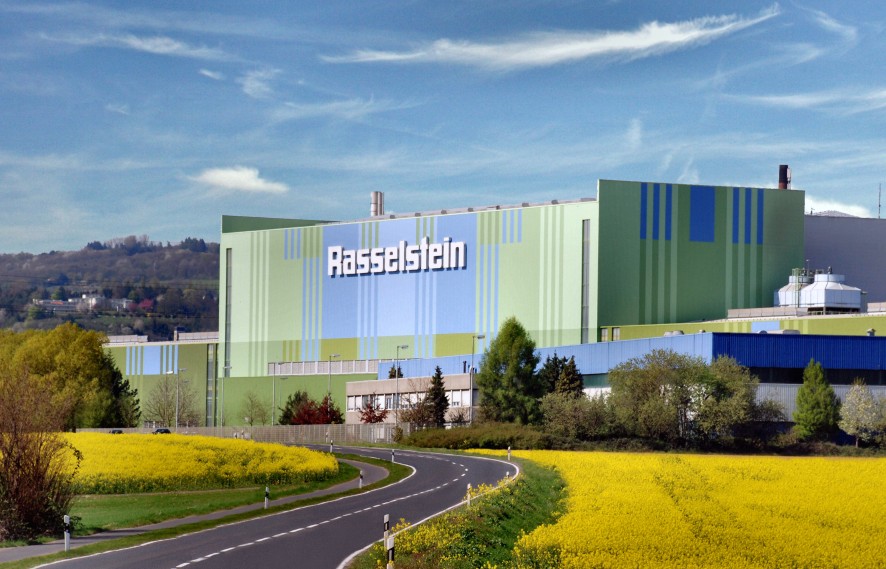
ThyssenKrupp Rasselstein is carrying out extensive modernization projects to increase the efficiency of its production lines and improve its competitive position. The projects concern three central units operated by the tinplate manufacturer: one of its two cold rolling mills, a continuous annealing line, and a pickling line. To allow the work to be carried out the units concerned will be temporarily shut down in November and also partly in October. At times, several hundred specialists from external contractors together with Rasselstein employees will be busy around the clock carrying out the work. The projects are scheduled for completion by the end of the year. The modernization efforts will further strengthen ThyssenKrupp Rasselstein and secure the sustainability of the Andernach plant. In making this investment, parent company ThyssenKrupp Steel Europe is underlining its commitment to highly attractive specialized areas of application like the packaging steel sector.
After over 50 years of operation the first of the two cold rolling mills will be fitted with a completely new cooling water circuit. This will involve the construction of two new buildings and a cooling system as well as the installation of a new technical infrastructure. Together with investments in previous years it will mean that tandem mill 1 has been practically fully refurbished. In operation for around 30 years, continuous annealing furnace 4, a further core unit, will be equipped with a new power supply system. A large part of the work including the installation of a new distribution station and the preparation of the connections has already been carried out during the last few months while production continued. In addition to the electrical revamp, a number of mechanical modifications will increase the line’s capacity by 60,000 to around 430,000 tons per year. At the same time the switch from DC to three-phase power will contribute to lowering the line’s energy consumption.
The third major project, increasing the capacity of the pickling line, is a consequence of the transfer of production from the Neuwied plant. As well as supplying the sheet mill, the pickling line in Neuwied provided around 200,000 tons of pickled hot-rolled strip for the production of packaging steel in Andernach. The rebuild of the Andernach pickling line will enable it to meet all the plant’s needs on its own. While Neuwied employees gradually began preparing from 2013 for new roles in the Andernach plant, initial measures were carried out to increase the performance of the pickling line. After the rebuild is completed in November and the line is restarted in the weeks thereafter, the Neuwied pickling line will be closed.
“These projects now being executed simultaneously will involve a total investment of around 40 million euros,” says Oliver Hoffmann, COO of ThyssenKrupp Rasselstein. “ThyssenKrupp is strengthening its packaging steel business and securing the sustainability of the Andernach plant, the world’s biggest site manufacturing this quality product,” he adds. The concentration of tinplate business at the Andernach plant was part of the ThyssenKrupp Steel Europe optimization program “Best-in-Class Reloaded” and involved the closure of the sheet mill in Neuwied, which will be completed at the end of the year with the transfer of the pickling operation. The majority of the around 400 Neuwied employees found jobs in Andernach, while socially acceptable solutions were found for the others. “We are proud that thanks to the joint efforts of all employees we have succeeded in securing an attractive future in the company for our colleagues in Neuwied,” says Hoffmann.
Raw material for ThyssenKrupp Rasselstein comes from Duisburg
The starting material for tinplate production is hot-rolled steel strip. ThyssenKrupp Rasselstein obtains it in coils weighing between six and 28 tons from ThyssenKrupp Steel Europe in Duisburg. The hot-rolled steel is 1.5 to 3.8 millimeters thick. Processing at ThyssenKrupp Rasselstein begins in the continuous pickling line, where the scale produced during hot rolling is removed. Annealing takes place by passing the strip at high speed through a system of annealing furnaces. ThyssenKrupp Rasselstein has three continuous annealing lines. The entire process including annealing and cooling takes only a few minutes. The furnaces are specially designed to process packaging steel. Precise temperature control gives the steel exactly the mechanical properties required by the product’s end use.
ThyssenKrupp Rasselstein GmbH has a history stretching back more than 250 years. The Andernach-based company is today a subsidiary of ThyssenKrupp Steel Europe. It produces tin-coated and chromium-coated blackplate (cold-rolled steel in thicknesses of 0.100 to 0,499 mm) at the world’s biggest packaging steel production site. Supplied with or without organic coating (paint, film) the material is suitable for diverse packaging solutions. ThyssenKrupp Rasselstein is one of Europe’s three biggest packaging steel producers. It currently employs around 2,400 people and produces roughly 1.5 million tons of packaging steel a year, serving 400 customers in 80 countries.
More than 90 percent of the material produced by ThyssenKrupp Rasselstein is used in the packaging sector, e.g. for the packaging of food, drinks and chemical/technical products such as aerosol cans or paint tins. The material is ideal for these uses. Tinplate is a highly efficient, strong and safe packaging material. It provides 100-percent product protection against light and oxygen. It is also particularly eco-friendly and the most recycled material in Europe. Tinplate can be recycled endlessly with no loss of quality, making it a thoroughly modern packaging material.