Trade press, 2019-11-05, 04:30 pm
World first from thyssenkrupp Steel at Blechexpo 2019: New AS Pro coating for hot forming provides greater process and part reliability and saves costs
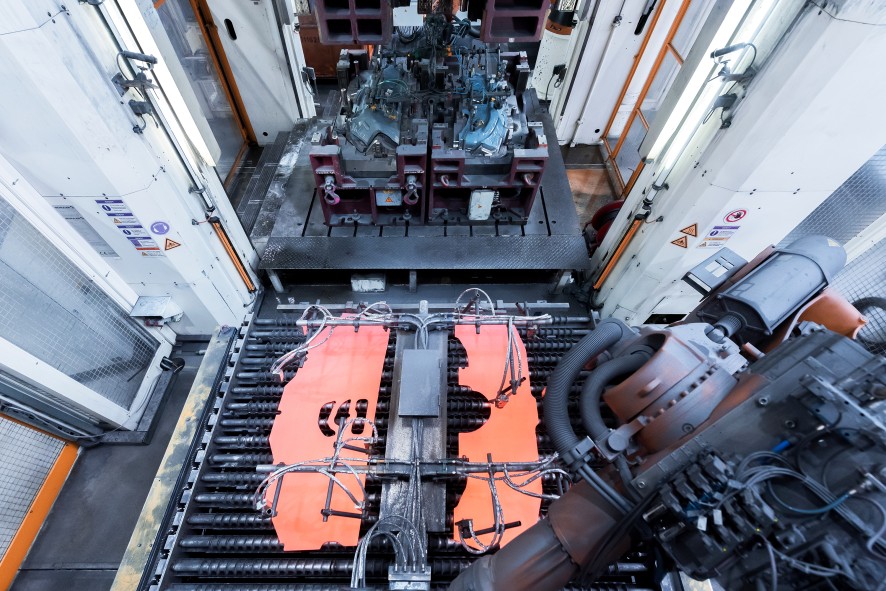
thyssenkrupp as a pioneer of hot forming has been a partner to the automotive industry for many years. The Duisburg-based company is now presenting a further groundbreaking innovation that represents the next generation of hot forming. The new AS Pro coating minimizes detrimental process-related hydrogen absorption during the annealing process. This significantly improves the reliability of the hot forming process and the parts produced, in particular structure-relevant components, which in turn means greater safety for car occupants. The innovation will be presented at the 14th Blechexpo exhibition in Stuttgart from November 5 to 8 and available to customers in the near future.
Process-related challenge in hot forming
AS Pro addresses a longstanding challenge in hot forming: the abbreviation AS stands for an aluminum/silicon coating that protects hot-formed parts against scaling and corrosion. During the hot forming of manganese-boron steels with an AS coating, the critical point arises during annealing in the furnace when the aluminum in the coating reacts with the oxygen in the water vapor. This also produces hydrogen, which diffuses through the coating into the material due to the high temperatures. In combination with high strengths and high stresses in the part this can lead to hydrogen embrittlement. To date this has been countered by control of the furnace atmosphere dew point or subsequent heat treatment. Both processes are energy-intensive and expensive.
The solution: AS Pro – the next generation of hot forming
thyssenkrupp Steel’s experts have come up with a modified alloying concept for the coating that prevents hydrogen embrittlement. AS Pro – like standard AS coatings – is produced on the company’s modern hot-dip coating lines. In addition to aluminum and silicon, a targeted amount of magnesium is added to the molten bath. The optimized alloy takes effect during the annealing process: Seen at atomic level, a magnesium oxide is now formed on the material surface that produces significantly less diffusible hydrogen than a standard AS coating. thyssenkrupp’s experts validated these findings in extensive tests on production equipment. The results are impressive: After hot forming, the hydrogen content of parts is reduced by 40 percent and more, and a reduction in hydrogen absorption of as much as 70 percent is possible with flexible-rolled material.
Milestonefor customers in process stability and part safety
For automotive OEMs, reliable processes for part manufacture are a key production factor. All post-processing measures cost time and money. With the new AS Pro coating thyssenkrupp Steel offers manufacturers an innovative development at a sensitive point in the production process for hot-formed parts. “As a partner to the automotive industry we see ourselves as innovation drivers who know the challenges involved in hot forming and offer solutions to support our customers,” says André Matusczyk, CEO of the Automotive business unit at thyssenkrupp Steel. “Our AS Pro-coated hot forming steels mean an end to the energy- and time-consuming additional measures normally required in the hot forming process. This allows our customers to further optimize their processes and reduce their costs. We are delighted to be launching the next generation of hot forming with AS Pro.”