Die Digitalisierung ist bei thyssenkrupp Steel auf dem Vormarsch. Hunderttausende smarte Sensoren sorgen in den Anlagen für reibungslose Prozesse.
Trotz Digitalisieriung: Stahl bleibt Stahl
Die notwendigen Umstellungen gelingen in der Verwaltung wesentlich einfacher als in der Produktion, wo sich die Einführung von smarten IT-Lösungen oft an den Investitionszyklen der Anlagen orientiert. „Der Fokus in den Fach- und Verwaltungsabteilungen liegt auf der Steigerung der Effizienz von Geschäftsprozessen. Hier sind Apps, digitale Workflows und smarte Assistenten längst in die digitale Infrastruktur integriert“, so Lang. Ein Beispiel ist die Einführung von Low-Code-Plattformen und Citizen Development. Dieser Ansatz ermöglicht es allen Mitarbeitenden, einfache Anwendungen und Bots, die ihre täglichen Aufgaben erleichtern, selbständig zu entwickeln und so aktiv zur digitalen Transformation beizutragen. „In der Produktion hingegen stehen stabile Prozesse, Anlagenverfügbarkeit und Qualität im Vordergrund“, betont er. „Und auch hier ist in den letzten Jahren durch die konsequente Umsetzung zahlreicher Digitalisierungsprojekte bereits viel entstanden.“
Klar ist dennoch: Das Kernprodukt Stahl bleibt auch in Zukunft eine physische Größe. Und trotzdem spielen digitale Technologien bei seiner Herstellung und Vermarktung mehr denn je eine Schlüsselrolle. Lang: „Stahl ist ein ausgewiesener Hightechwerkstoff, der bei thyssenkrupp Steel seit Jahrzehnten in immer weiter optimierten, hochgradig automatisierten Produktionsschritten hergestellt wird.“ Dank der kontinuierlich vorangetriebenen Digitalisierung hat das Unternehmen heute die Möglichkeit, entlang der gesamten Wertschöpfungskette über Sensoren und Aktoren standort- und anlagenübergreifend Millionen von Daten in Echtzeit zu erheben und auszuwerten.
Digitalisierung verbessert Wettbewerbsfähigkeit
Der Big-Data-Ansatz ist dabei kein Selbstzweck, sondern trägt unmittelbar zu Transparenz bei. „Wir bieten unseren Kunden heute eine nie dagewesene Nachvollziehbarkeit ihrer Bestellungen. Die detaillierten Einblicke bieten ihnen einen klaren Wettbewerbsvorteil und ermöglichen es, Produktionsprozesse und Qualitäten zu optimieren. Denn mithilfe von Data Analytics lassen sich beispielsweise Materialeigenschaften präziser vorhersagen und Toleranzen genauer treffen“, sagt Lang. Die Datenschätze, die bei thyssenkrupp auf stellenweise 15 Jahren Datenhistorie beruhen, geben Ingenieuren und Data Scientists zudem die Möglichkeit, immer neue KI-Modelle zu entwickeln und zu trainieren, um weitere Potenziale in der Produktion zu heben. „Wir sprechen bei thyssenkrupp Steel aufgrund unseres Produktionsvorkommens über einen riesigen Maßstab. Hier helfen bereits kleine Verbesserungen im Detail, um am Ende eine enorme Wirkung zu erzielen.“
Gleiches gilt, wenn es für den Stahlproduzenten darum geht, regulatorische Vorgaben zu erfüllen. Etwa im Bereich Nachhaltigkeit, wo der Carbon Footprint von Produkten für Kunden und Endverbraucher immer wichtiger wird. Volker Lang weiß: „Wer keine Transparenz in Form digitaler Daten zu den CO2-Emissionen entlang der Wertschöpfungskette zur Verfügung stellen kann, hat langfristig einen klaren Wettbewerbsnachteil.“ So wirkt der Stahlproduzent auch an dem Aufbau sogenannter Dataspaces mit, in denen Daten über Unternehmensgrenzen hinweg souverän und sicher ausgetauscht werden können. Dies ist für viele Branchen mit voneinander unabhängigen und geographisch getrennten Produktionsprozessen von großer Bedeutung. Ein Beispiel ist das Catena-X Automotive Network, ein Projekt, an dem das Fraunhofer-Institut für Software- und Systemtechnik (ISST) maßgeblich beteiligt ist. Hier führt das gezielte Zusammentragen von Daten aller beteiligter Unternehmen dazu, dass Automobilhersteller beispielsweise die Dokumentationsanforderungen des Lieferkettensorgfaltspflichtengesetzes erfüllen können.
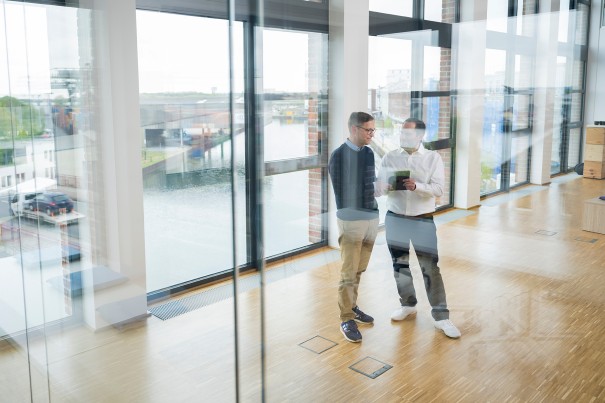
thyssenkrupp Steel trägt entscheidend dazu bei, solche Verbesserungen zu erreichen. So sieht es Professor Boris Otto vom Fraunhofer ISST in Dortmund: „Der Standort mitten im Ruhrgebiet bietet die Möglichkeit, weiterhin physische Produkte zu entwickeln und zu verkaufen. Diese gilt es nun sukzessive mit digitalen Diensten zu ergänzen, die den Kundenmehrwert erhöhen.“ Otto weiter: „Das Ruhrgebiet war immer das industrielle Herz von Deutschland. Hier ist aber auch ein digitales Powerhouse: Wir haben in einem Umkreis von 50 Kilometern unterschiedliche Universitäten, wo sich tausende Studenten mit Themen wie Informatik und Logistik auseinandersetzen. Hier entstehen genau die digitalen Dienste und Dienstleistungen, die von der Industrie benötigt werden.“ Volker Lang sieht das ähnlich: „Wir müssen nicht ins Silicon Valley oder nach Tel Aviv reisen, um uns anzuschauen, wie Digitalisierung funktioniert. Das geht auch hier. Wir haben hier eine starke Hochschulszene und auch die richtigen Anwendungsfälle.“ Im nächsten Schritt bedeute dies für den CIO, dass die Technologien, die in der Welt zur Verfügung stehen, bei thyssenkrupp Steel ankommen und in der Fläche ihren Nutzen entfalten müssen. „Im Kern steht immer die Idee, uns zu optimieren und zu verbessern – das macht die Stahlproduktion aus.“