Das selectrify®-Batteriegehäuse aus Stahl für Elektroautos
Die Batterie ist das bestimmende Element im Elektrofahrzeug und zugleich das empfindlichste und kostspieligste Bauteil. Die Autohersteller gehen davon aus, dass der Energiespeicher 30 bis 50 % der Gesamtkosten eines E-Autos ausmachen wird. Weltweit arbeiten Autoproduzenten derzeit an Strategien, um Produktionskapazitäten und Lieferinfrastrukturen über die gesamte Wertschöpfungskette aufzubauen.
Sicher und wirtschaftlich: Ein Batteriegehäuse aus Stahl bewahrt im Crashfall das Herzstück des Elektroautos
An der Schnittstelle zwischen Antrieb und Strukturelement stellt die Batterie sowohl Hersteller als auch Werkstofflieferanten konzeptionell vor eine komplexe Aufgabe. Oberstes Gebot dabei: die Kernkomponente der Elektromobilität bestmöglich zu schützen. Das Anforderungsprofil ist vielschichtig: Die Batterie muss crashsicher und korrosionsbeständig sein, elektromagnetisch abgeschirmt und gekühlt werden.
Das selectrify®-Batteriegehäuse ist ein neu entwickeltes Konzept aus Stahl mit exzellenter Performance. Es besteht aus einer Einhausung mit einem Rahmen, einem Anbindungsprofil, Abstützträgern oben und unten, Unterfahrschutz und Deckel. Seine vielfältigen, patentierten Bauweisen können die Anforderungen annähernd gewichtsneutral gegenüber Aluminium erfüllen. Das selectrify®-Batteriegehäuse beweist: Leichtbau, Sicherheit und Brandschutz lassen sich verbinden – und ermöglichen dabei noch hohe Kosteneinsparungen.
Bis zu 50 % geringere Produktionskosten
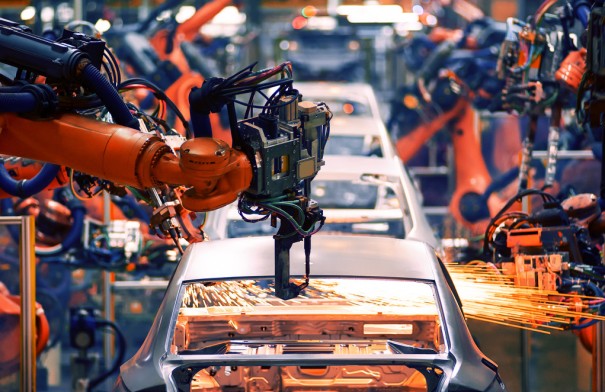
Bei gleicher Sicherheit im Crash und annähernd gleichem Gewicht ist das Konzept aus Stahl in der Leistungsklasse 70 kWh im Vergleich zu Lösungen aus Aluminium bis zu 50 % günstiger in der Herstellung. Perfekt für die Großserie.
Das hat eine Analyse ergeben, die sich auf ein Szenario von 200.000 Fahrzeugen/Jahr und eine Laufzeit von sieben Jahren bezieht. Sie enthält Material- und Fertigungskosten, Werkzeug-Investitionen für die Bauteilfertigung, Rohbaufertigung inkl. Dichtprüfung sowie den Korrosionsschutz.
„Im Klartext reden wir hier von Kosteneinsparungen im Bereich von Hunderten Euros ohne Sicherheitsverlust“, so Nierhoff. „Das ist im Bereich der Autoentwicklung – wo es auch schon einmal um Cent-Beträge geht – eine ganze Welt.“ Wie die Referenzstruktur ist auch das Batteriekonzept skalierbar und passt sich flexibel den unterschiedlichen Plattformen der OEMs an.
Bis zu 50 % weniger CO2-Emissionen*
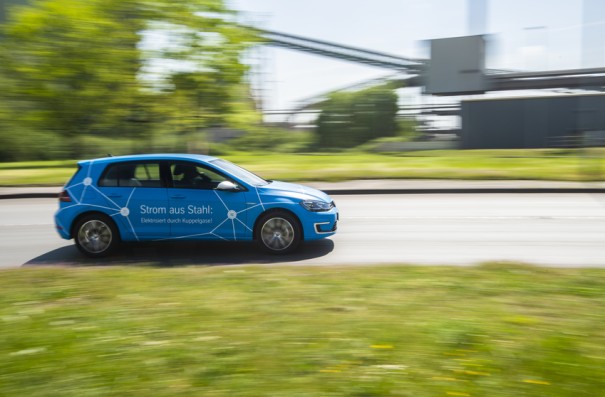
Bei der CO2-Bilanz von Elektrofahrzeugen über den gesamten Lebenszyklus verschieben sich – verglichen mit Verbrennungsmotoren – die Hotspots von der Nutzung in die Produktionsphase. Das ganzheitliche Life-Cycle-Assessment zeigt: Stahl ist das nachhaltigste Material für Batteriegehäuse.
Bis zu zwei Drittel weniger Treibhausgasemissionen entstehen bei der Produktion eines Stahl-Batteriegehäuses im Vergleich zur Aluminium-Referenz. In der Nutzung sind Batteriegehäuse aus Stahl oder Aluminium hinsichtlich der CO2-Emissionen nahezu gleich zu bewerten. Über den gesamten Lebenszyklus hinweg lassen sich durch den Einsatz von Stahl statt Aluminium rund 50 % CO2 einsparen.*
* Gilt für eine Gesamtlaufleistung von 150.000 km und die Verwendung von Primäraluminium (EU-Consumption-Mix) für die Produktion und den EU-Strommix (2019) für die Nutzung.
Nr. 1 im Brandschutz
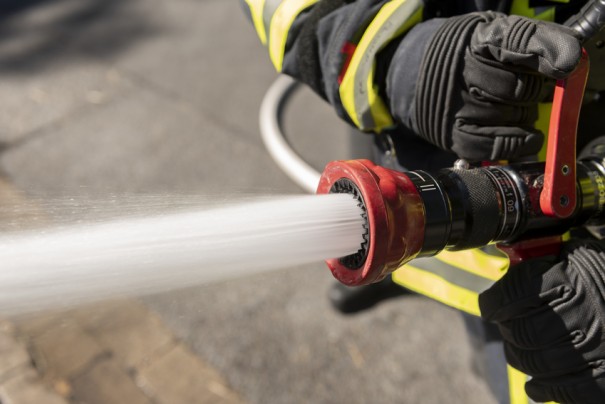
Brandschutz von Batteriegehäusen ist ein entscheidendes Kriterium, wenn es um die Sicherheit von Elektrofahrzeugen geht. Das Gehäuse muss im Brandfall die Passagiere schützen. Denn geraten die Akkus einmal in Brand, ist ein Löschen nicht mehr möglich. Ein Batteriegehäuse aus Stahl bringt im Fall eines Batteriebrandes entscheidende Minuten für Passagiere und Unfallteilnehmer.
Der Schmelzpunkt von Stahl (0,8 mm)1 liegt bei 1.410 °C. Im Brandversuch werden am Deckel des Batteriegehäuses auch nach 20 Minuten kaum höhere Temperaturen als 1.000 °C erreicht, was für die erheblichen Sicherheitsreserven von Stahl spricht. Aluminium (1,1 mm)2 erreicht dagegen im Brandversuch bereits nach 15 Sekunden seinen Schmelzpunkt von 660,3 °C. Nach 30 Sekunden kollabiert das Material – die Fahrgastzelle ist dem Brand ungeschützt ausgesetzt.
1 Schmelzpunkt von DP-K Stahl
2 Schmelzpunkt von EN AW-6016
Mehr Sicherheit und Reichweite
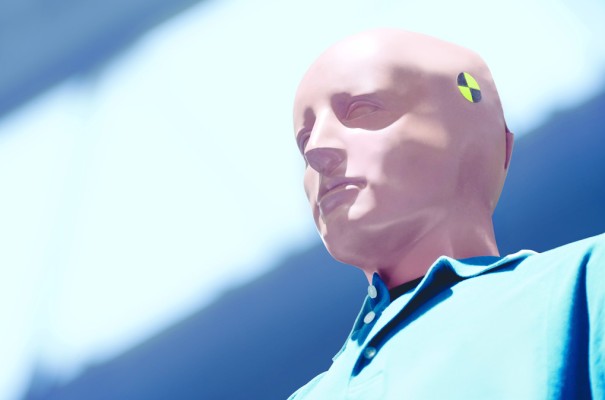
Durch den Einsatz höchstfester Stähle können effiziente Crash-Strukturen besonders schlank und dünnwandig ausgeführt werden. Das spart Bauraum und schafft Platz für große Batterien.
Hoch stabile Sicherheitsbatteriegehäuse sind ein Bestandteil in der Initiative selectrify®, mit der thyssenkrupp Steel seine Forschungs- und Entwicklungsaktivitäten rund um das Thema Elektromobilität bündelt. Heutige Lithium-Ionen-Akkus sind extrem leistungsfähig, aber gleichzeitig auch äußerst empfindlich. Bei Beschädigungen drohen verheerende Brände, die Passagiere und Retter nach einem Unfall gefährden können.
Schutz der Batterie in Elektroautos ist Schutz der Insassen
Ein umfassender Schutz der Batterie vor Crash-Einflüssen dient daher in erster Linie dem Schutz von Personen und wird von den Automobilentwicklern entsprechend auf höchstem Niveau betrieben. „Um die Insassen eines Fahrzeugs bestmöglich zu schützen, ist die sichere Einhausung der Batterie oberstes Gebot“, sagt Dr. Daniel Nierhoff aus dem selectrify®-Projektteam. Das Gehäuse darf weder durch einen Seitenaufprall, noch wenn das Fahrzeug aufsetzt oder ein Fremdkörper von unten gegen die Hülle prallt, auch nur im Geringsten nachgeben. Andererseits soll es so leicht und kompakt wie möglich sein, um den zur Verfügung stehenden Bauraum so effizient wie möglich zu nutzen und so mehr Platz für noch größere Batterien, die eine höhere Fahrzeugreichweite bieten, zu schaffen.