Im Pellet- und Rohmateriallager der Direktreduktionsanlage wird der wesentliche Rohstoff für den Direktreduktionsprozess gelagert: Eisenerz in Form von Pellets. Das Lager ist so konzipiert, dass es eine kontinuierliche Versorgung der Anlage gewährleistet, um einen reibungslosen Betrieb des Direktreduktionsprozesses sicherzustellen.
Nachhaltig
zu einer neuen Zeitrechnung in der Stahlproduktion.
Mit der Transformation zum klimaneutralen Stahlerzeuger schreiben wir bei thyssenkrupp Steel ein weiteres Mal Industriegeschichte. Denn vom Erfolg eines der weltweit größten industriellen Dekarbonisierungsprojektes – des Baus unserer neuen Direktreduktionsanlage, die ab 2027 in Betrieb gehen soll – profitieren alle.Unser Stahl: Ausgangspunkt für die Zukunft der industriellen Wertschöpfung, das Gelingen der Energie- und Klimawende und für viele zukunftsfähige Arbeitsplätze in Deutschland und Europa.
-
Nachhaltige Stahlproduktion, die im ersten Schritt bereits bis zu 3,5 Mio. Tonnen CO<sub>2</sub> spart.
-
Nachhaltiger Stahl für Deutschlands Unabhängigkeit und Wirtschaftskraft.
-
Nachhaltiger Stahl, der den Aufbau der Wasserstoffwirtschaft beschleunigt.
-
Nachhaltiger Stahl, der Arbeitsplätze und Wohlstand sichert.
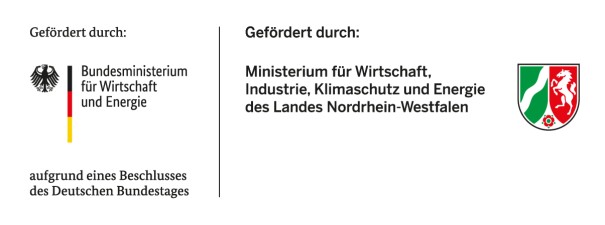
Blaupause für die Dekarbonisierung der Industrie. Motor der europäischen Wasserstoffwirtschaft. Eine wichtige Entscheidung für den Klimaschutz und den Industriestandort Deutschland.
Die zu 100 Prozent wasserstofffähige Direktreduktionsanlage mit zwei Einschmelzern und einer Produktionskapazität von 2,5 Mio. Tonnen direkt reduziertem Eisen pro Jahr ist in dieser technologischen Konzeption die erste Anlagenkombination ihrer Art weltweit. Dadurch wird thyssenkrupp Steel zum Wegbereiter für die Dekarbonisierung der Stahlwertschöpfungskette in Europa und garantiert unter anderem unverzichtbare Spezialwerkstoffe für das Gelingen der Energie- und Mobilitätswende.
Anschauungsmodell DR-Anlage
Ein wichtiger Schritt für die Transformation der Stahlindustrie: Bau der ersten wasserstoffbasierten Direktreduktionsanlage am Standort Duisburg mit einer Kapazität von 2,5 Millionen Tonnen direkt reduziertem Eisen (DRI) und einer jährlichen Einsparung von bis zu 3,5 Millionen Tonnen CO2.
Errichtung der Anlage auf EPC-Basis (Entwicklung, Beschaffung und Bau) durch die SMS group.
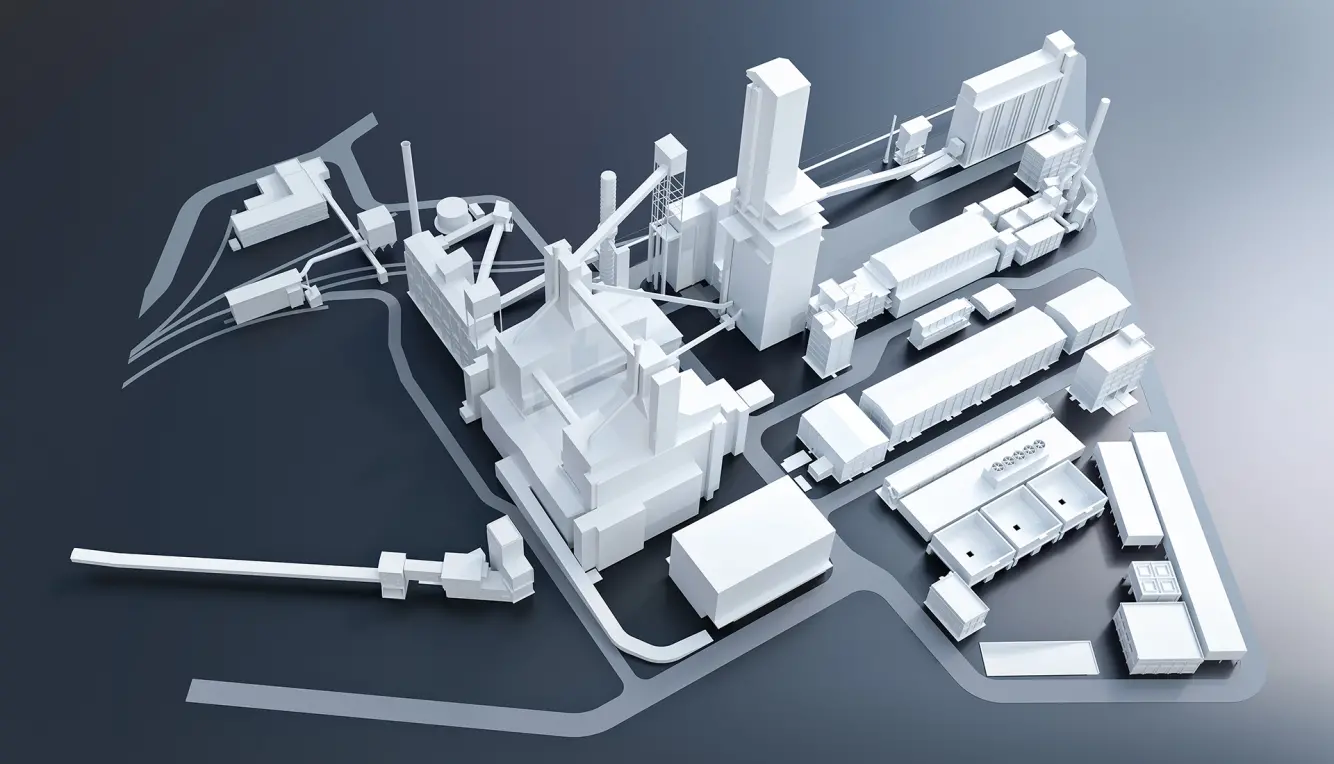
Der Direktreduktionsturm ist das zentrale Aggregat einer CO2-ärmeren Stahlproduktionsanlage, die die herkömmlichen Hochofenprozesse ersetzt. In diesem Turm erfolgt die Direktreduktion des Eisens aus Eisenerz mithilfe von Reduktionsgasen wie Wasserstoff (H2). Das Ergebnis ist festes, kugelförmiges Eisen, das vor der Weiterverarbeitung im Stahlwerk in den Einschmelzern verflüssigt wird.
Das für die Reduktion benötigte Prozessgas wird im Reformer erzeugt.
Aus einer variierbaren Mischung von Wasserstoff, Erdgas und Prozessgasen wird unter hohen Temperaturen das Reduktionsgas reformiert.
Der Einschmelzer, auch bekannt als Submerged Arc Furnace (SAF), zeichnet sich dadurch aus, dass er einen Schmelzprozess verwendet, bei dem das Metall offen in einem Bad geschmolzen wird – im Gegensatz zu geschlossenen Schmelzöfen wie dem Elektrolichtbogenofen (EAF). Der SAF ermöglicht eine effiziente Schmelze, wodurch er eine wichtige Rolle in der Metallurgie spielt.
Die Gießhalle ist der Bereich, in dem das flüssige Roheisen aus dem Einschmelzer in sogenannte Transportpfannen gegossen wird, die wiederum zur Weiterverarbeitung in das Oxygenstahlwerk gefahren werden.
Die Schlackengranulierung ist ein Verfahren, das in der Stahlindustrie eingesetzt wird, um die bei der Stahlherstellung entstehende Schlacke zu verarbeiten. Dabei wird die heiße flüssige Schlacke schnell abgekühlt und granuliert. Der so erzeugte Hüttensand kann in der Zementindustrie als wertvoller Rohstoff benutzt werden.
Nachhaltige Stahlproduktion,
die im ersten Schritt bereits bis zu 3,5 Mio. Tonnen CO2 spart.
Weg von der Eisenerz-Reduktion durch Kohlenstoff im Hochofen. Hin zur Roheisenherstellung durch den Einsatz von Wasserstoff in der Direktreduktionsanlage mit neu entwickelten Einschmelzern. Ein gigantischer Umbau, der schon im ersten Schritt 3,5 Mio. Tonnen CO2 in der Stahlproduktion einsparen wird. Das entspricht rund 2 Prozent der Emissionen in NRW.
Doch das ist erst der Anfang. Spätestens 2045 werden wir am Standort Duisburg klimaneutral Stahl produzieren. Zum Vergleich: Mit dem herkömmlichen Stahlerzeugungs-Prozess in unseren Hochöfen sind wir jährlich für 20 Mio. Tonnen CO2 und somit für etwa 2,5 Prozent von Deutschlands CO2-Last verantwortlich. Mit der neuen Anlage ersetzen wir bereits einen Hochofen.
Nachhaltiger Stahl
für Deutschlands Unabhängigkeit und Wirtschaftskraft.
Stahl ist ein unverzichtbarer Basiswerkstoff für die Energie- und Mobilitätswende. Und das perspektivisch auch in Grün.
Deutschlands größter Erzeuger von Flachstahl zu sein, heißt, eine immense Bedeutung für die Zukunft der heimischen Wirtschaft zu haben. Denn eine gelingende Transformation von thyssenkrupp Steel trägt maßgeblich dazu bei, ganze Wirtschaftszweige in der Erreichung der Klimazielsetzungen zu unterstützen. Nachhaltiger Stahl mit geringer CO2-Last ist der Werkstoff, den es jetzt braucht. Um Wertschöpfung in Deutschland weiter zu ermöglichen.
Nachhaltiger Stahl,
der den Aufbau der Wasserstoffwirtschaft beschleunigt.
So gigantisch der Umbau unserer Roheisenherstellung ist, so riesig ist der Bedarf an klimaneutralem Wasserstoff. Die Direktreduktionsanlage wird alle zwei Stunden mehr Wasserstoff benötigen, als z. B. in den Oberhausener Gasometer passen.
So unvorstellbar große Mengen H2 verkaufen zu können, heißt für europäische Hersteller von Wasserstoff, jetzt mit großer Planungssicherheit massiv investieren zu können. Als einer der ganz bedeutenden Abnehmer in der Zukunft beschleunigen wir so den Hochlauf der Wasserstoffökonomie.
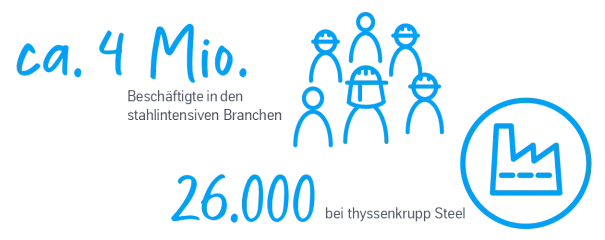
Nachhaltiger Stahl,
der Arbeitsplätze und Wohlstand sichert.
Wir stärken den Industriestandort und sichern attraktive Arbeitsplätze in der Region – 26.000 sind es direkt im Unternehmen, 150.000 in nachgelagerten Industrien in NRW und bundesweit gilt es sogar, 4 Mio. Arbeitsplätze in stahlintensiven Branchen zu erhalten. Unsere Transformation wird zu einer Vielzahl neuer Berufsbilder führen, einen Qualifizierungsschub leisten und zukunftssichere Jobs schaffen.
Kurz: Nicht nur die Qualitätsansprüche an unsere Stahlgüten werden wir erhalten. Sondern es werden auch Beschäftigte in unseren Betrieben, bei Zulieferern und Verarbeitern im Ruhrgebiet und darüber hinaus davon profitieren. Somit ist unser Stahl Ausgangspunkt für die Zukunft der industriellen Wertschöpfung, das Gelingen der Energie- und Klimawende und für viele gute Arbeitsplätze in Deutschland und Europa.
Servicebereich
Das könnte Sie auch interessieren
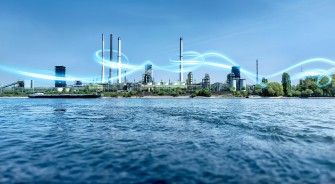
tkH2Steel® – unsere Klimastrategie
Alles rund um unsere klimaneutrale Zukunft lesen Sie hier
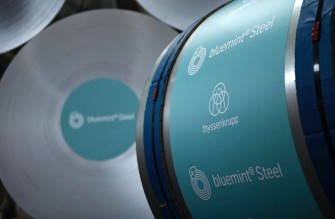
bluemint® Steel
Unser hochwertiger Flachstahl mit reduzierter CO2-Intensität
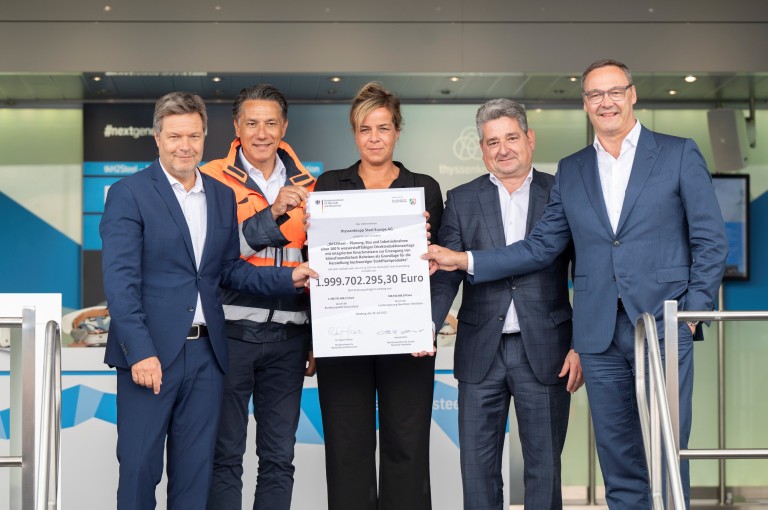
Pressemitteilung
Bundesminister für Wirtschaft und Klimaschutz Robert Habeck besucht thyssenkrupp: thyssenkrupp Steel erhält Förderung in einer Gesamthöhe von rund zwei Milliarden Euro durch Bund und Land
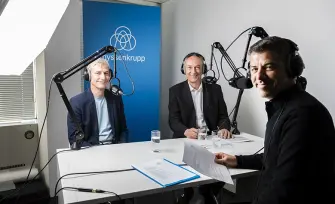
Podcast „gekocht, gewalzt, veredelt“
„Wir starten in die Wasserstoff-Ära“
Kontakt
Mark Stagge
Leiter Public & Media Relations, thyssenkrupp Steel Europe
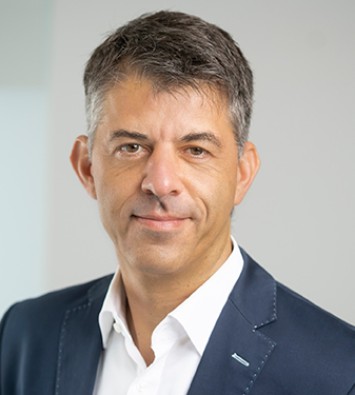
Roswitha Becker
Pressesprecherin, thyssenkrupp Steel Europe
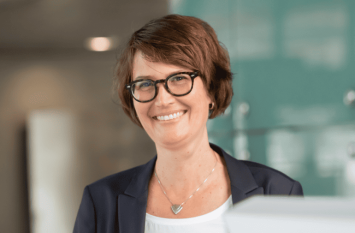