In drop tests with drop heights of up to 10 meters and drop speeds of up to 50 km/h, FE simulations are validated and the energy absorption behavior of components and materials is investigated.
Services for internal and external customers
We offer consulting and support in the analysis of materials and production processes according to your individual requirements:
We are happy to advise you
Materials testing
Surface analysis and corrosion
Metallurgy and metallography
The process in detail – from the request to a test report
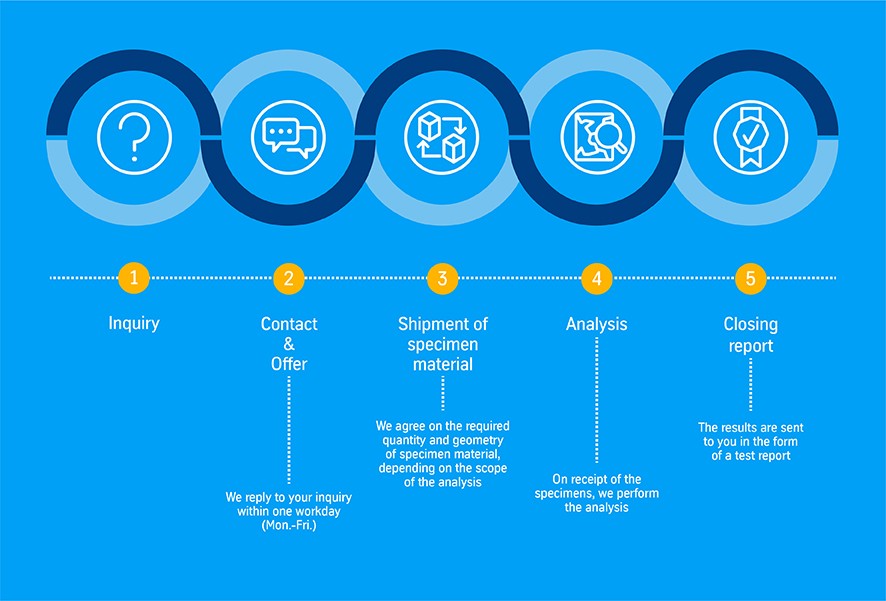