Chronology
1811 – Foundation of the cast steel factory by Friedrich Krupp

Friedrich Krupp establishes a company on November 20, 1811 for the manufacture of cast steel in accordance with the English quality standards and the products manufactured from it.
1850 – Invention of steel casting

Jacob Mayer, co-founder of the Bochum Association of Mining and Cast Steel Fabrication, invents steel casting. Advantage of the process: Products can be created from liquid steel in their final shape. ThyssenKrupp Steel Europe continues with its production at the Bochum site even today.
1852 – Invention of the seamless railroad tire

In the middle of the 19th century, the railroad becomes a means of transportation for the masses. Krupp helps to push this mobility revolution while profiting from it. From 1847 on, axles and springs are produced, followed in 1852 by a groundbreaking invention: the seamless forged and rolled railroad tire, which is now unbreakable. This becomes a worldwide bestseller. The second string to the bow of the Group becomes the production of guns made of cast steel.
1871 – Foundation of several iron and steel companies in the Ruhr Area

In Dortmund, Leopold Hoesch and other members of this family of entrepreneurs from the Eifel region found the Hoesch iron and steel works. In the same year, the firm SA des Aciéries du Rhin (Rheinische Stahlwerke) put a Bessemer steelworks into operation in Duisburg-Ruhrort. Also in 1871, August Thyssen establishes the firm Thyssen & Company, which is initially an iron strip rolling mill, together with his father in Mülheim/Ruhr. 1871 is not considered to be the year in which the subsequent Thyssen Group was founded. These are the works premises where the Mannesmannröhren-Werke are located today.
1875 – Krupp trademark

In 1875 Alfred Krupp decides that the three tires placed one above the other should become his company logo, which then becomes world-famous.
1878/79 – Thomas Process in Germany
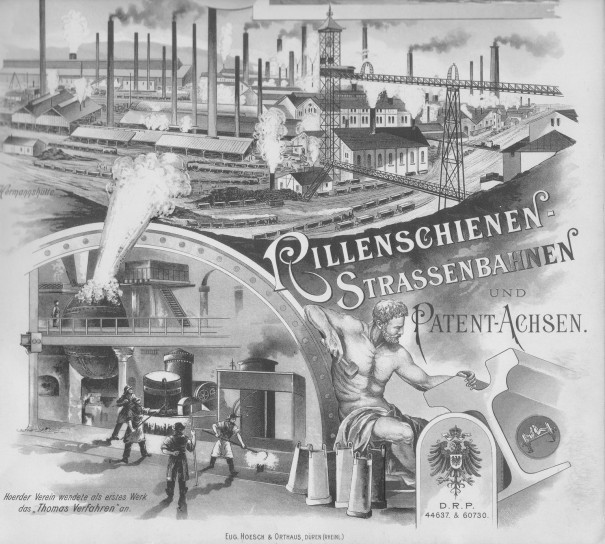
The technical manager of the Hoerder Mining and Metallurgy Association in Dortmund, Joseph Massenez, acquires the patents for the Thomas process in Germany in 1878. Together with the Rheinische Stahlwerke, the Hoerder Association succeeds in 1879 in introducing this steel production process in Germany. With the Thomas process it was also possible to use phosphorus-containing ores for steel production. The Hoerder Association in Dortmund, which was incorporated in the 1960s into the Hoesch Group, becomes one of the leading German steel manufacturers due to the Thomas process.
1889/90 – Introduction of the pig iron mixer

Gustav Hilgenstock, engineer at the Hoerder Association in Dortmund, introduces the pig iron mixer to continental Europe (desulphurization of pig iron). This was an important prerequisite for the practical and economical implementation of carbon steel processes (Thomas steel). From 1893 on, he manages the Dr. C. Otto & Company (a predecessor company of ThyssenKrupp Industrial Solutions) in Bochum, where he helped to develop the bottom burner coke oven.
1891 – Formation of the Thyssen Group
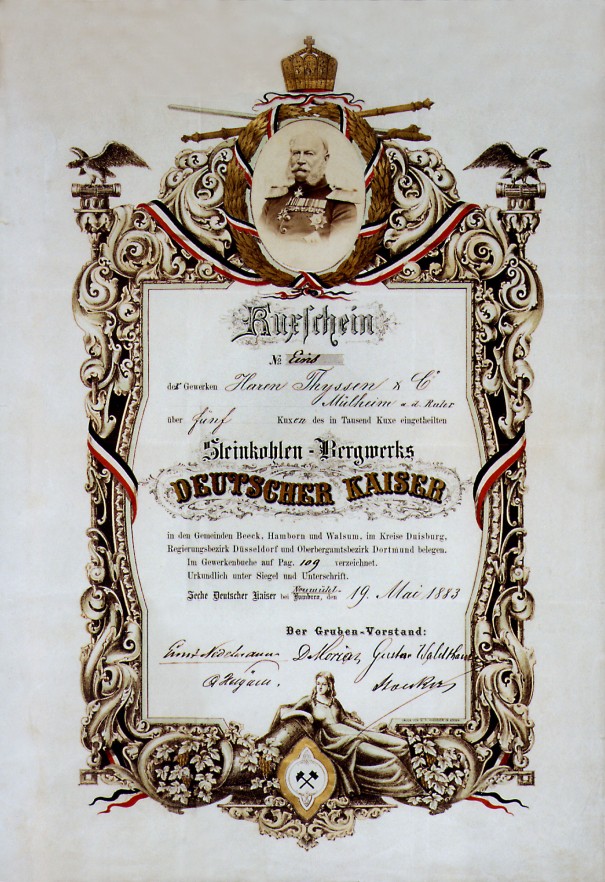
In 1891 August Thyssen announces that he is in possession of all shares of the Gewerkschaft Deutscher Kaiser trade union in Bruckhausen near (Duisburg-)Hamborn. The expansion of the Gewerkschaft Deutscher Kaiser trade union to become a metallurgical plant with its own coal base begins. The first steel is tapped in the Siemens-Martin steelworks. These two events in the year 1891 are later considered to be the date of the foundation of the Thyssen Group. ThyssenKrupp Steel Europe still produces steel in the same location today. In the following years, August Thyssen rationalizes, modernizes and extends the production of iron and steel and systematically expands both the raw material base and the subsequent processing capacity of his companies. On the basis of shareholdings in ore mines and transportation companies abroad, the first internationalization of the Thyssen Group occurs.
1892 – Development into a horizontally structured Group

Friedrich Alfred Krupp continues with the expansion of the company into a horizontally and vertically structured group. The incorporation of the Gruson Works in Magdeburg in 1892 lays the foundation stone for Krupp plant construction. The takeover of the Germania shipyard in Kiel in 1896 opens up access to shipbuilding. With the integrated metallurgical plant in Rheinhausen, the pig iron and steel base of the Group is expanded in 1897.
1902 – Foundation of the “Aktiengesellschaft für Hüttenbetrieb” (stock corporation for iron and steel production), which today is a landscape park
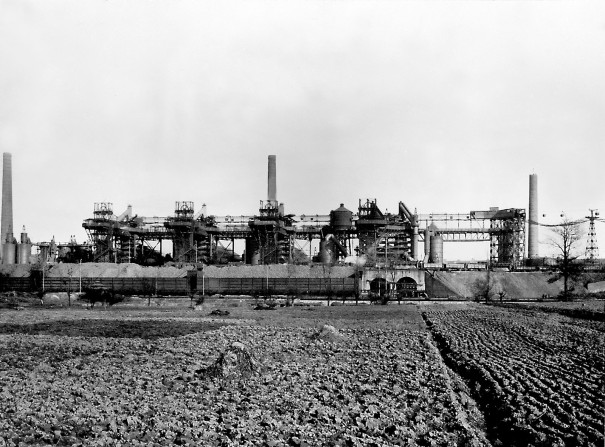
In 1902 August Thyssen establishes the “Aktiengesellschaft für Hüttenbetrieb” in the then still independent suburb of (Duisburg-)Meiderich in order to cover the pig iron requirements of his Siemens-Martin steelworks in Mülheim an der Ruhr and Duisburg-Hamborn. After the closure of the works in 1985, the blast furnace plant is converted into a landscape park as part of the Emscherpark International Building Exhibition, as well as on the basis of private initiatives.
1903 - start of construction of the Schwelgern port
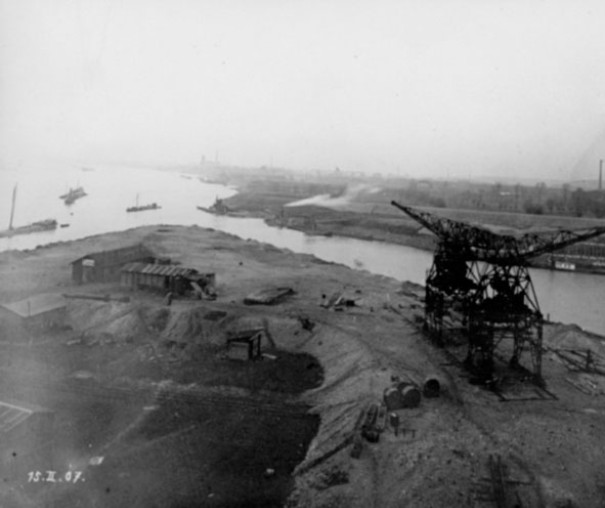
Between 1903 and 1907, the Gewerkschaft Deutscher Kaiser trade union builds a new factory harbor with modern loading facilities in Schwelgern to supplement the existing factory harbor in Alsum. The Schwelgern port, which also enabled the cost-effective transportation by ship of the company’s finished products, is still in use today.
1907 – Hoesch acquires the plant in Hohenlimburg

With the merger of Hoesch and the Limburger Fabrik- und Hütten-Verein, the Dortmund steel company finds a regular buyer for its semi-finished products. The rolling mill in Hohenlimburg subsequently develops into an eminent specialist for spring steel, medium strip and cold rolled products.
1912 – Development of stainless, acid-resistant steels

After intensive research, Krupp succeeds this year in developing stainless, acid-resistant steels. NIROSTA and V2A quickly find a wide range of applications, above all in the chemical and food industry, in medicine and construction. All over the world these steels become synonymous with quality. Even the spire of the Chrysler building in New York, which was completed in 1929, is covered with this material.
1914 – First World War
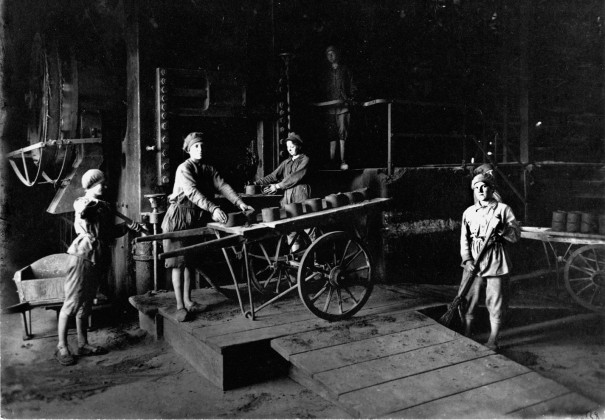
The First World War becomes a turning point. After an initial fall in production there is – not only at Thyssen and Krupp – a massive expansion in production, with the main products produced being armaments, including guns, artillery shells, rail systems for light railroads etc. As in the German war economy in general, the Gewerkschaft Deutscher Kaiser trade union also employs women, Belgian civilians and prisoners of war due to labor shortages.
1919 – Changeover to peacetime production

After the war, Krupp changes its production over as a consequence of the Versailles Treaty and begins with the construction of locomotives, trucks, agricultural machinery and excavators, among other things. In the following years it is possible to stabilize the company. Now the focus is on streamlining the further processing operations and expanding the production of stainless steel.
1926 – Vereinigte Stahlwerke AG
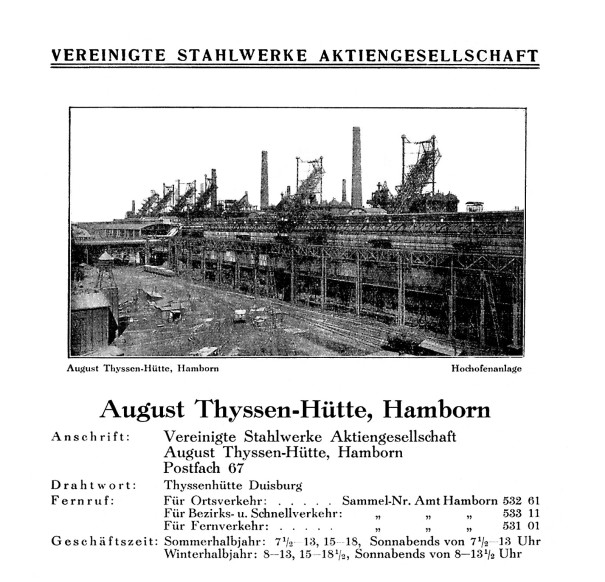
Incorporation of the Thyssen firms into the Vereinigte Stahlwerke AG, to which – with the exception of Hoesch, the Gutehoffnungshütte, Mannesmann, Klöckner und Krupp – all of the mining companies in the Ruhr Area belong. A few weeks after August Thyssen’s death (April 4, 1926), his son Fritz and his nephew Hans agree to the incorporation of their Thyssen companies into the Vereinigte Stahlwerke AG.
1926 – WIDIA is launched onto the market

This year, Krupp launches the cemented carbide metal WIDIA (like diamond) on the market. Due to its hardness and wear-resistance, it represents a major advance in tool technology. WIDIA soon becomes the synonym for cemented carbide metal bar none.
1933 – The period of National Socialism

As part of the rearmament of Germany, and especially during the Second World War, the room for maneuver with respect to entrepreneurial decision-making is restricted. The Rhenish-Westphalian coal, iron and steel corporations are – like other companies working in large-scale industry, too, – involved in the armaments and war policy, which also includes the employment of foreign workers. The war ends with heavy bombardment and destruction, occupation and the confiscation of firms, followed in part by extensive dismantling.
1953 Re-establishment of August Thyssen-Hütte AG

In 1950 the reconstruction work on the Thyssen-Hütte begins. The first blast furnace is fired up in 1951, with a Siemens-Martin plant also starting up again. As part of the breakup of the West German coal, iron and steel industry, the Thyssen-Hütte is removed from the Vereinigte Stahlwerke AG Group and (re-)established in 1953 as August Thyssen-Hütte AG.
1953 – Separation of the coal, iron and steel companies by order of the Allies

The steel and mining activities of Krupp are outsourced and are to be sold. The Rheinhausen steelworks soon achieves production records in the reconstruction boom of the Federal Republic of Germany. No purchaser for the businesses can be found until 1968. The “divestment requirement” is abolished.
1955 – First hot strip mill in the Federal Republic of Germany
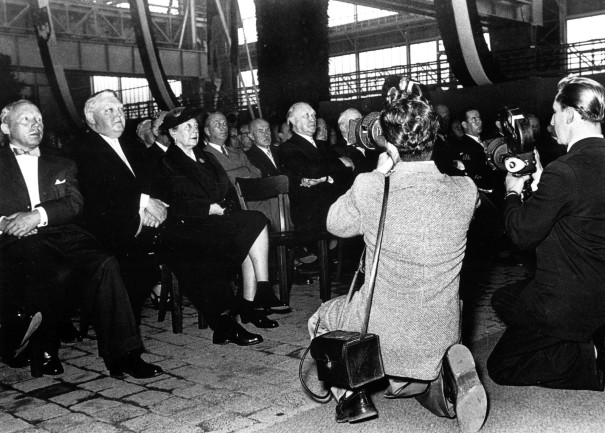
In 1955 the first continuous hot strip mill installed in Germany after the Second World War goes into operation. It forms the core of the flat steel-oriented production at the Thyssen-Hütte. This provides the company with new opportunities in the field of sheet steel. German Chancellor Konrad Adenauer takes part in the official commissioning of the hot strip mill.
1957 – First Sendzimir rolling mill goes into operation

In 1957 the Deutsche Edelstahlwerke AG plant in Krefeld, a predecessor company of ThyssenKrupp Nirosta GmbH, puts the first Sendzimir rolling mill for the cold rolling of stainless steel in Germany into operation. This revolutionizes the production of cold-rolled steel. The Sendzimir mill stand, named after its developer Tadeusz Sendzimir, is a multiple roller mill stand with 20 rollers for the cold rolling of wide steel strips. The two thin working rollers are held in the housing by numerous backup rollers.
1958 Thyssen acquires a stake in Rasselstein

The firm August Thyssen-Hütte-AG acquires a stake in the Rasselstein Steel and Rolling Mill, which was founded as long ago as 1760. This gives Thyssen access to the market for surface-finished blackplate. Today, Rasselstein is the only manufacturer of tinplate in Germany. At the world’s largest production site for packaging steel, ThyssenKrupp Rasselstein today produces blackplate and ECCS for a wide variety of packagings.
1958 – RH vacuum method

The demands of steel consumers for improved material properties lead to the development of the so-called RH vacuum process. Together with the firm W. C. Heraeus, the Henrichshütte of Ruhrstahl AG, which subsequently became the Thyssen Henrichshütte, develops this important steel post treatment process. The Ruhrstahl-Heraeus process for the treatment of steel under a vacuum enables the production of a particularly homogeneous and pure steel of high quality.
1960-1964 – Beeckerwerth plant – a steelworks on a greenfield site

In order to meet the growing demand for steel as a material, August Thyssen-Hütte AG builds a completely new factory on the “greenfield site” between 1960 and 1964. Thanks to the farsighted real estate policy of August Thyssen, the company had a large enough area available in Beeckerwerth. This is an area of 1.5 million square meters. The initial part of the new factory was a steel plant, which was to produce steel in accordance with the new oxygen method. It is put into operation in June 1962 with two 150-ton converters. However, the design of the new factory also comprises a wide strip rolling mill with subsequent cold rolling mill. The hot strip mill begins work in April 1964, with the cold rolling mill beginning its production two months later.
The Beeckerwerth factory is awarded the gold medal at the “Industry in the Landscape” national competition in 1971 because the Technical Director Alfred Michel had placed particular emphasis on the external and architectural design of the plant directly on the River Rhine. During a tour by the press in 1963, Michel emphasizes that “a steelworks does not need to be a factory that is shrouded in soot and dust, but can certainly be attractive and pleasing to the eye in terms of its architecture and if it is embedded in landscaped grounds”.
Today the factory produces almost 6 million tons of crude steel a year with three converters with a capacity of 265 tons each. The entire equipment used in the converter shop, secondary metallurgy and continuous casting is regularly adapted to the state of the art by making extensive investments. Among others, one of the most up-to-date vacuum facilities goes into operation in 2001.
1965 – Acquisition of the Bochum Association for cast steel fabrication

After the acquisition of the majority shareholding in the Bochum Association for Cast Steel Fabrication, this is followed in 1965 by the merger with the Rheinhausen steelworks to form the Hütten- und Bergwerke Rheinhausen AG. With its site in Bochum, Krupp has a strong stainless steel base at its disposal at this time.
1972 – Krupp builds the roof of the Olympic Stadium in Munich

As a technology corporation, Krupp also takes over spectacular steel engineering projects. For example, Industrie- und Stahlbau Rheinhausen designs the steel mesh roof of the new Olympic Stadium in Munich. The entire steel mesh roof construction is suspended from twelve mighty pylons which are up to 80 meters high and anchored at many angles in the ground. The high-quality steel for the pylons comes from the Duisburg steel mills of today's thyssenkrupp Steel Europe AG.
1973 – Expansion of Thyssen to form a conglomerate

After the merger of August Thyssen-Hütte AG with Rheinstahl AG, the four newly formed corporate divisions of Capital Goods and Manufacturing, Trade and Services, Stainless Steel and Steel are created.
1973 – Black giant in Duisburg

Commissioning of the blast furnace Schwelgern I at the August Thyssen-Hütte AG in Duisburg. With a hearth diameter of 14 meters and 42,000 m³ of working volume, the “Black Giant” is the largest blast furnace at the time in the Western world. Many years of planning and development work preceded the blowing-in in February. Architect Professor Fritz Schupp was responsible for the design, after having designed the architecture of the Zeche Zollverein in Essen in the 1930s. In 1993 the second blast furnace in Schwelgern goes into operation. With a hearth diameter of almost 15 meters, it is considerably larger than the “Black Giant” of 1973. For comparison: The first blast furnace which went into operation in 1897 at Thyssen had a daily production of 250 tons. In the 1950s, maximum daily production levels of 1,000 tons were the maximum output. The two blast furnaces in Schwelgern achieve a capacity of 10,000 and 12,000 tons a day of pig iron, respectively.
1977 – New training center

Official inauguration of the training center at Thyssen AG, formerly August Thyssen-Hütte in Duisburg-Hamborn with Federal President Walter Scheel.
1980 – Reorganization of the Steel Division

The steel crisis and the competition for subsidies in the European Community force a realignment of the Steel Division. Under the umbrella of Krupp Stahl AG, founded in 1980, the production of ordinary low-carbon steel is reduced and the focus placed on quality and stainless steels. A radical measure in the following years: The closure of the almost 100-year-old Rheinhausen plant in 1993.
1983 – Foundation of Thyssen Stahl AG

The Steel Division of the Thyssen Group is spun off in 1983 to form Thyssen Stahl AG. The reason for this, among others, were the negotiations (moderator discussions) on collaboration with the firm Krupp Stahl AG, although this is not implemented at this time.
Even before this, Thyssen had closed down uneconomical capacity. Now further cuts are required, including the shutdown of the blast furnace plant for steel mill operation and the shutdown of the heavy plate mills in Hattingen and Oberhausen.
1983 – First Thyssen tailored blanks at Audi

Tailor-made, laser-welded blanks (tailored blanks), put together from individual sheets of varying thicknesses, coating or steel quality, ensure that the finished component possesses the ultra high strength wherever the strongest forces occur. This reduces the weight of the cars and thus their fuel consumption. This innovation of Thyssen Stahl introduces a “revolution” in the automotive industry in the middle of the 1980s. Wilfried Prange, Head of the Research Department for Application Technology, is considered to be the “inventor” of the tailored blanks, which were first used in 1983 in the Audi 100.
The sale of ThyssenKrupp Tailored Blanks to Wuhan Iron and Steel Corporation (WISCO) was completed in 2013.
1992 – Merger of Fried. Krupp AG with Hoesch AG to form Fried. Krupp AG Hoesch-Krupp

After the merger between Fried. Krupp AG and Hoesch AG, the group is restructured: The business segments are organized in five divisions: Plant Engineering, Automotive, Trade, Mechanical Engineering, Steel and Processing.
1995 – Collaborations between Thyssen and Krupp in the field of steel
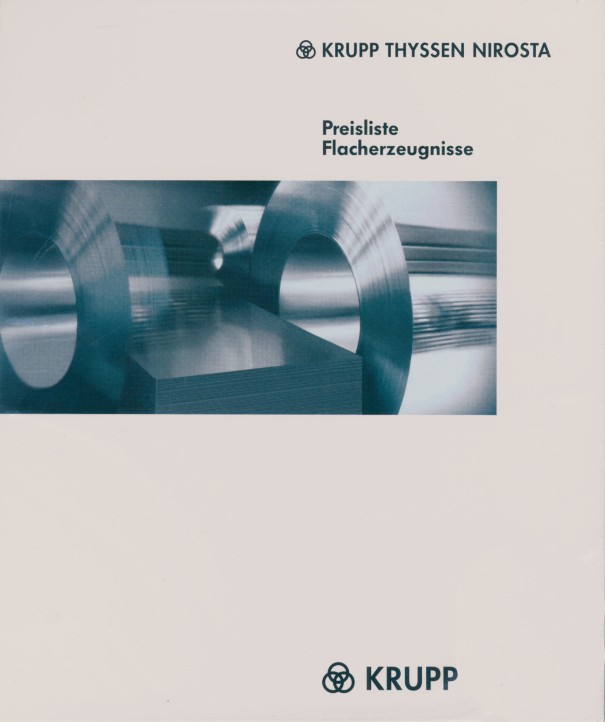
In the 1990s the collaboration discussions between Thyssen and Krupp are resumed. In 1995 these result in joint ventures in the fields of tinplate (Rasselstein Hoesch GmbH), electrical steel (EBG Elektroblech Bochum GmbH) and stainless flat products (Krupp Thyssen Nirosta GmbH).
1997 – Merger of the quality steel flat business areas of Krupp and Thyssen to form Thyssen Krupp Stahl AG
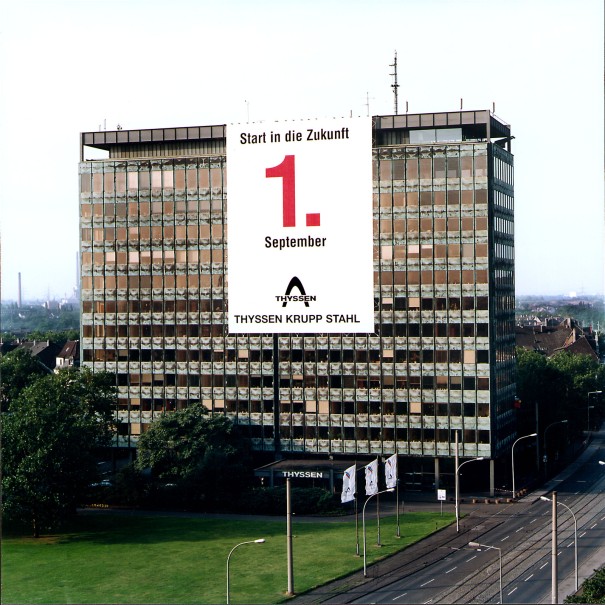
In March 1997 it becomes known that Fried. Krupp AG Hoesch-Krupp intends to acquire a majority shareholding in the Thyssen Group. After the takeover plan is abandoned, the two companies enter into intensive consultations on the industrial concept of a joint flat steel company, into which Thyssen Stahl AG and Krupp Hoesch Stahl AG would incorporate their flat steel activities. On September 1, 1997 the firm Thyssen Krupp Stahl AG starts its business operations; it is one of the world’s largest flat steel producers.
During the course of the steel merger, the two companies agree to examine further fields in which they can work together (see 1999).
1999 – Milestone in flat steel development: Casting rolling line

After around 24 months of construction, ThyssenKrupp Stahl AG puts a state-of-the-art casting rolling line in Duisburg-Bruckhausen into operation – the first of its kind in Europe. Immediately after the liquid stages of pig iron/oxygen steel, hot strip is manufactured with the thinnest dimensions in a single production step.
1999 – The new ThyssenKrupp Group
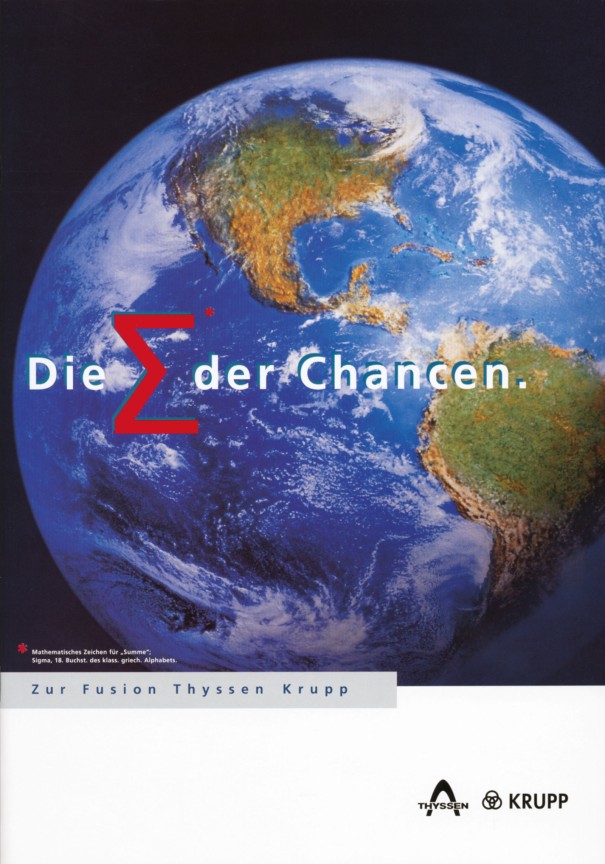
In August 1997 Thyssen and Krupp start talks on further forms of cooperation after the foundation of a joint venture in the field of high-grade flat steel is completed. The strategic opportunities identified and the synergistic potentials of a full merger are extremely large. With its entry in the Commercial Register on March 17, 1999, ThyssenKrupp AG begins its work with economic effect as of October 1, 1998.
2000 – Colored facades at ThyssenKrupp Steel Europe

From the desire to operate “environmental protection for the eyes”, new buildings of ThyssenKrupp Steel Europe have been designed in color since the year 2000. The color schemes are produced by the designer Friedrich Ernst von Garnier. The industrial buildings are supposed to be more closely adapted to their surroundings and harmonize with them. The DOC Dortmund OberflächenCentrum (Dortmund Surface Center) represents the start of a long series of colored buildings. This is followed by the hot-dip galvanizing plant 8 in the same location, while in Duisburg the Schwelgern coking plant, the Hamborn power station and other purpose-built buildings are designed in color.
2003 – New coking plant in Schwelgern in operation

After a construction period of three years, the new coking plant in Schwelgern is put into operation in March 2003. This supplies the coke for the large blast furnaces at ThyssenKrupp Steel Europe AG. It is the replacement for the coking plant in Duisburg-Bruckhausen, built in 1895 and modernized several times during the following decades, which after more than 100 years of operation was closed down at the Bruckhausen site.
2005 – Decision to build a steelworks in Brazil

The global rise in the demand for steel, exploding commodity prices and increasingly global competition between the steel producers induce ThyssenKrupp Steel to consider setting up an integrated iron and steel mill in Brazil. Regional cost advantages and the proximity to the raw materials (ore reserves) speak in favor of this location. This is intended to take advantage of the growth opportunities in the NAFTA region, as well as in the enlarged EU market. Changing economic framework conditions and technical problems during the construction of the new iron and steel plant in the years 2006 to 2010 in the Bay of Sepetiba, however, result in increasing construction costs and problems with long-term profitability.
2007 – A new blast furnace in operation

In 2007, blast furnace 8 is put into operation in Duisburg. This replaces blast furnace 4, which was constructed in 1963. One special feature is the color design of the blast furnace, in which the black in the upper section first merges to orange and then yellow. The gradual change in colors is intended to represent the temperature distribution within the plant. ThyssenKrupp Steel Europe operates a total of four blast furnaces of its own – the blast furnaces 8 and 9 in Duisburg-Hamborn, as well as blast furnaces 1 and 2 in Duisburg-Schwelgern.
2010 – Introduction of the health shift

From the summer of 2010, employees can take part during their working hours in a Health Day. As a result of the across-the-board, company-wide introduction as part of further training, all employees are made increasingly aware of health topics irrespective of their previous access to that subject. In December 2010, Thyssen Krupp Steel Europe received the “Corporate Health Award” in the “Heavy Industry and Mechanical Engineering” category for its exemplary health management.
2013 – Company daycare center for children at ThyssenKrupp Steel Europe starts operation in Duisburg

2013 – Since May 2013, the 800-square-metre facility with adjacent sand and play areas has been in operation. Children from the age of four months until the time they start school are looked after there almost all the year round.