Structure-borne-damping composite material with customized properties
bondal®: noise-deadening material for electric motors
bondal® from thyssenkrupp Steel is a sandwich material for noise reduction in vehicle construction that has been proven for many years. The latest application tests with the innovative composite in battery vehicles also show considerable potential for optimizing the acoustics of electric motors and their power control units.
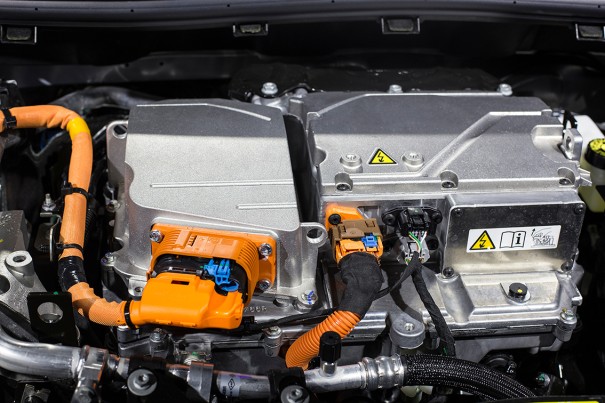
Less is more: When it comes to electric vehicles, this applies not just to emissions of harmful greenhouse gases but also to a significant reduction in noise. Electric motors are simply quieter than conventional internal combustion engines. However, this does not necessarily mean that they and their power control units are less of a nuisance to passengers and the environment. Drive-related noise emissions in electric vehicles occur primarily in a frequency band that people find particularly unpleasant.
bondal® is the quiet revolution
In an initial study, a cover made of bondal®, in this case variant CB40, has been found to reduce noise emissions from the inverter – a central component in every electric powertrain that converts direct current from the battery into alternating current for the motor and, depending on load condition, produces high-frequency sound emitted via the cover of the inverter housing. This is an unpleasant noise and represents a problem that cannot currently be satisfactorily solved with monolithic materials and without secondary noise deadening.
To optimize the acoustics of the inverter, bondal® makes use of a property of the steel-polymer-steel composite that has so far been given little attention: In addition to the structure-borne sound damping properties typical of the material, components formed from bondal® also offer air-borne sound damping properties. The latter are effective at higher frequencies above 300 hertz. Together, structure-borne and air-borne sound attenuation reduce the sound pressure level at close range by up to 20 db(A) – reducing noise to a quarter of its original level. Compared with current all-steel or all-aluminum solutions in conjunction with further noise deadening measures such as heavy-layer and spring-mass elements, bondal® is also a highly attractive alternative for weight reasons. In addition, the product offers good electromagnetic shielding and can be easily recycled.
Ideal acoustic material
But there is another reason why bondal® is the ideal acoustic material for a wide range of applications in the body in general and in the powertrain of electric vehicles in particular: The sandwich material has the same good genes as high-quality steel sheet and largely the same application-oriented properties of the leading lightweight material for the automotive industry. Like high-quality galvanized body panels, bondal® offers effective cathodic protection against corrosion, provides the electromagnetic shielding so important in the electrified powertrain and is of course fully integrated into the steel recycling loop. Processing is carried out on existing equipment, while forming behavior is determined by the steel cover sheets and therefore holds little risk of unpleasant surprises in component manufacture.
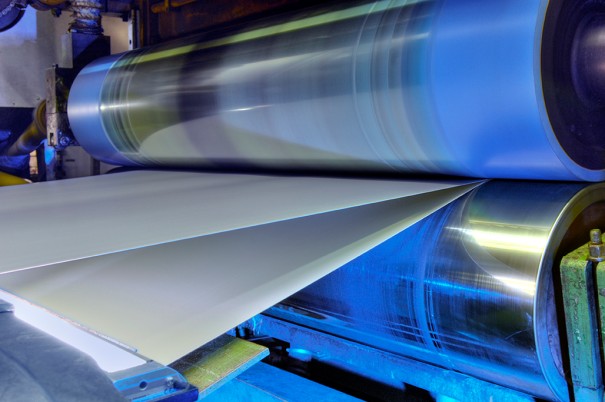
Effective back and forth movement
bondal® owes its outstanding acoustic properties to its typical sandwich structure. It consists of an upper and a lower steel face sheet of variable thickness, bonded into a laminate by a permanently viscoelastic polymer core layer only 0.03 mm to 0.04 mm thick. When subjected to structure-borne noise, the shear-compliant bond allows the steel face sheets to move back and forth very slightly but effectively, converting vibration energy into heat and reducing structure-borne noise.
Thanks to advances in knowledge and measurement techniques it has now also been possible to demonstrate air-borne sound damping at higher frequencies in bondal® components, thus extending the applications of the established composite to include hybrid and all-electric vehicles.
Taking back of transport packaging in accordance with Section 15 of the German Packaging Act (VerpackG)
Pursuant to Section 15 (1) sentence 5 of the German Packaging Act (VerpackG) we point out that, on request, we take back the transport packaging of our products in accordance with the provisions of Section 15 (1) VerpackG. However, you are under no obligation to return the transport packaging to us.
The return of our transport packaging is handled via the take-back system operated by the recycling company Kreislaufsystem Blechverpackungen Stahl GmbH (KBS). If you wish to return transport packaging, please do so using the KBS take-back system. To register for the first time, please contact us by e-mail at [email protected]. If you are already registered with us, you can contact KBS directly via the service number +49 211 239228 or by e-mail at [email protected] for information regarding the place to which the packaging is to be returned for collection.
The transport packaging in which our products are delivered must not be disposed of via any municipal waste collection service (e.g. plastic bag, trash bin, etc.).