All-round protection for the car body
With our hot-dip galvanized and electrogalvanized sheet, we offer a range of products tailored to the specific processing requirements of the automotive industry. With functional properties including reliable corrosion protection and outstanding paint finish, our coated products are suitable for all common forming and joining processes and support the development of cost-efficient lightweight solutions.
Steel is the number-one material for sustainable mobility: In addition to its weight reduction potential, it offers outstanding recycling properties. Modern coatings strengthen these advantages while at the same time meeting increased demands for resource-friendly, cost-efficient design.
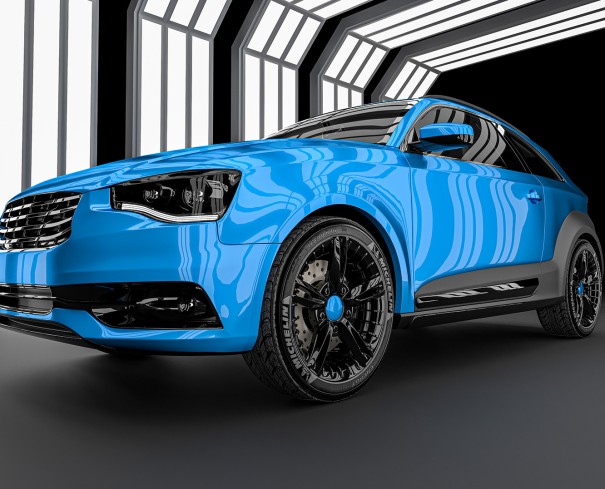
A prime example is the innovative zinc-magnesium coating ZM Ecoprotect®, which thyssenkrupp Steel has been supplying to OEMs in outer-panel quality for several years. The aim was to further improve the established hot-dip zinc coating with its good welding, bonding and anti-corrosion properties, while guaranteeing customers high process reliability. Both goals were achieved: In the press shop, ZM Ecoprotect® displays lower coefficients of friction and improved forming behavior. Stick-slip effects also occur much later, resulting in reduced tooling wear. This enhances efficiency and increases the number of parts produced between cleaning.
Improved corrosion protection
Compared with pure zinc coatings, ZM Ecoprotect® also offers significantly improved corrosion protection. As a result, coating thickness can be reduced by 30 percent with the same corrosion performance. Corrosion protection around cut edges and scratches is also measurably improved. Last but not least, thinner coatings reduce the use of zinc – an advantage for sustainability.
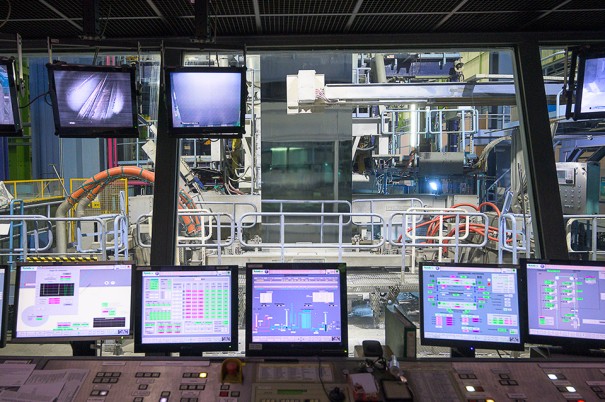
The introduction of primetex® has helped further optimize the suitability of hot-dip coated sheet products for visible outer paneling. The innovative rolling process and precisely matched production process give the coated sheet a surface texture so accurate that no additional fillers are needed before painting. This saves material and energy costs and is good for the environment.
Capacity expansion
In response to growing cost pressure in the auto industry and the resultant rise in demand for hot-dip galvanized steel, thyssenkrupp Steel is expanding its capacities: When it opens in 2022, FBA10 will be the second ultra-modern hot-dip galvanizing line at the Westfalenhütte site in Dortmund. In combination with the neighboring FBA8 coating line, it will increase the site’s annual output of hot-dip galvanized products to around one million tons. In the future the plant will be able to produce both zinc-coated and zinc-magnesium coated products. In total, thyssenkrupp will then operate ten hot-dip coating lines and three electrogalvanizing lines.
From zinc to zinc-magnesium: Coating overview
Depending on the required product properties, we supply steels for car body outer panels with four different coatings:
Electrolytic galvanizing (EG)
In this process, the cleaned sheet is coated with zinc from a sulfate-acid electrolyte. The method enables a very precise surface coating. Additional phosphating improves formability.
Zinc Magnesium (ZM)
Our product ZM Ecoprotect® belongs to the segment of zinc-magnesium surfaces (ZM). Compared to standard zinc coating, ZM has a better forming behavior in the press shop. In addition, the most recently developed product in the hot-dip coating segment offers significantly improved corrosion protection, allowing the coating thickness and thus also the amount of zinc used to be reduced by 30 percent, while providing enhanced protection of cut edges.
Hot dip galvanizing (GI)
In the field of hot-dip coating processes, zinc coating is the most frequently used option with a long tradition. Zinc-coated steels feature excellent paint adhesion, weldability and formability.
Galvannealed (GA)
In this variant of hot-dip galvanizing, the zinc coating of the thin sheet is converted into a zinc-iron coating with a defined microstructure by a targeted heat treatment. This allows to produce a superior surface quality. Moreover, galvannealed coatings also outmatch pure zinc coatings in terms of welding properties.