Trailblazer for innovations
thyssenkrupp Steel Europe stands for innovations in steel. The company takes over a pacemaker role in the further development of high-tech steels and processes. For this, we combine our technical know-how and develop customer-oriented solutions.
selectrify® – project shows steel solutions for electromobility
The History and Future of Steel Technology
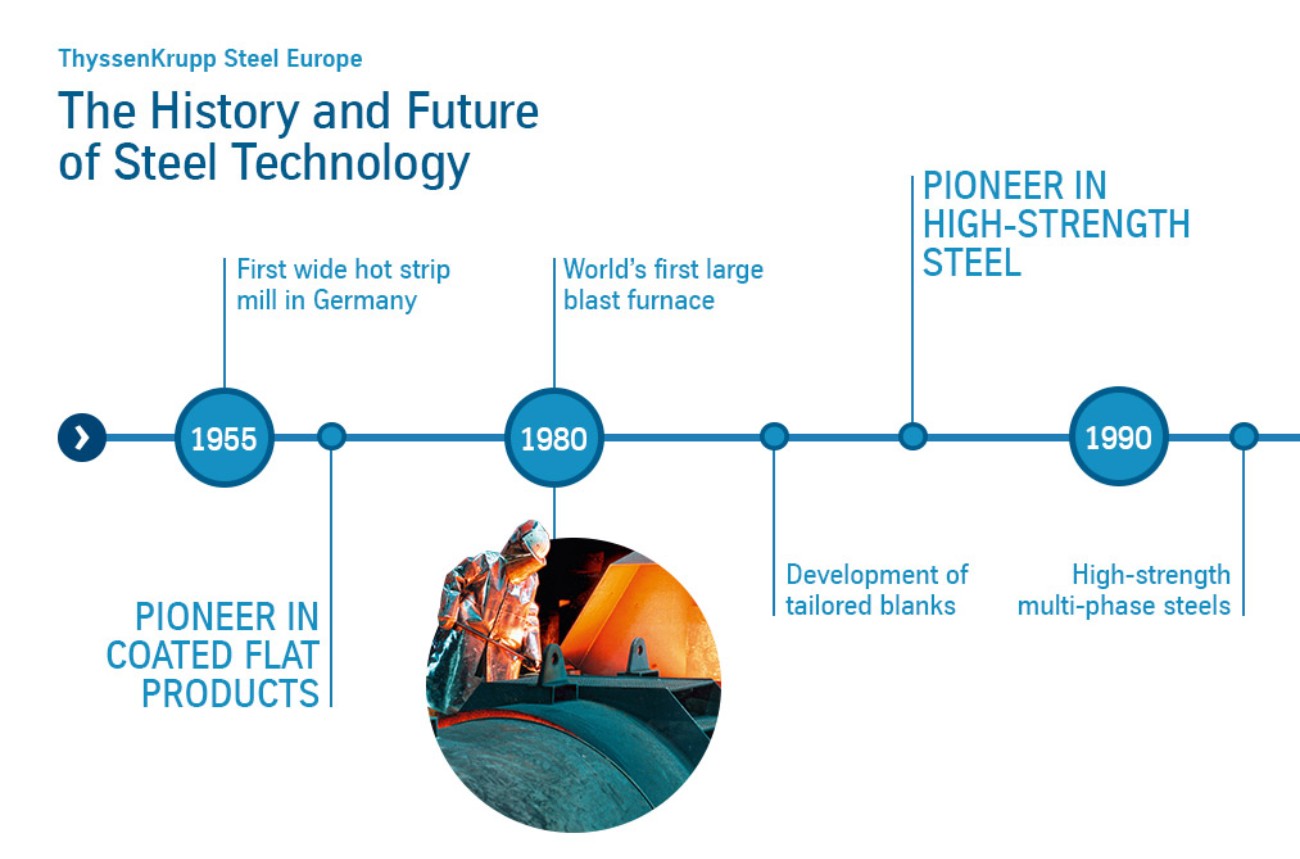
© thyssenkrupp Steel Europe Usage hints 300dpi JPG
The History and Future of Steel Technology (1 of 4)
Usage hints
We gladly provide free of charge the images included in our media library for use within daily use in the press (including magazines published weekly or monthly). In any case, condition precedent for this is that when using them, you refer to our company as the source in the immediate vicinity of the image material used and in the customary manner (© thyssenkrupp Steel Europe). If a different author is indicated, this must be stated. You are only authorized to process images to the extent that this is technically mandatory for the specific publication (e.g. black/white instead of in color in a monochromatic daily newspaper) and/or to the extent you only change the size proportionally, without using only part of the image, or to stretch, compress or modify it in any other way or to deform it. Every other processing and use is only admissible after prior written approval (email to: [email protected]). We request to be provided with an author’s copy free of charge and promptly after the respective publication of print media, with films with a digital version in a customary playback format on a generally readable data carrier. Where the image material is used online, you shall provide us with the detailed URL of the respective website and make this website accessible to us. close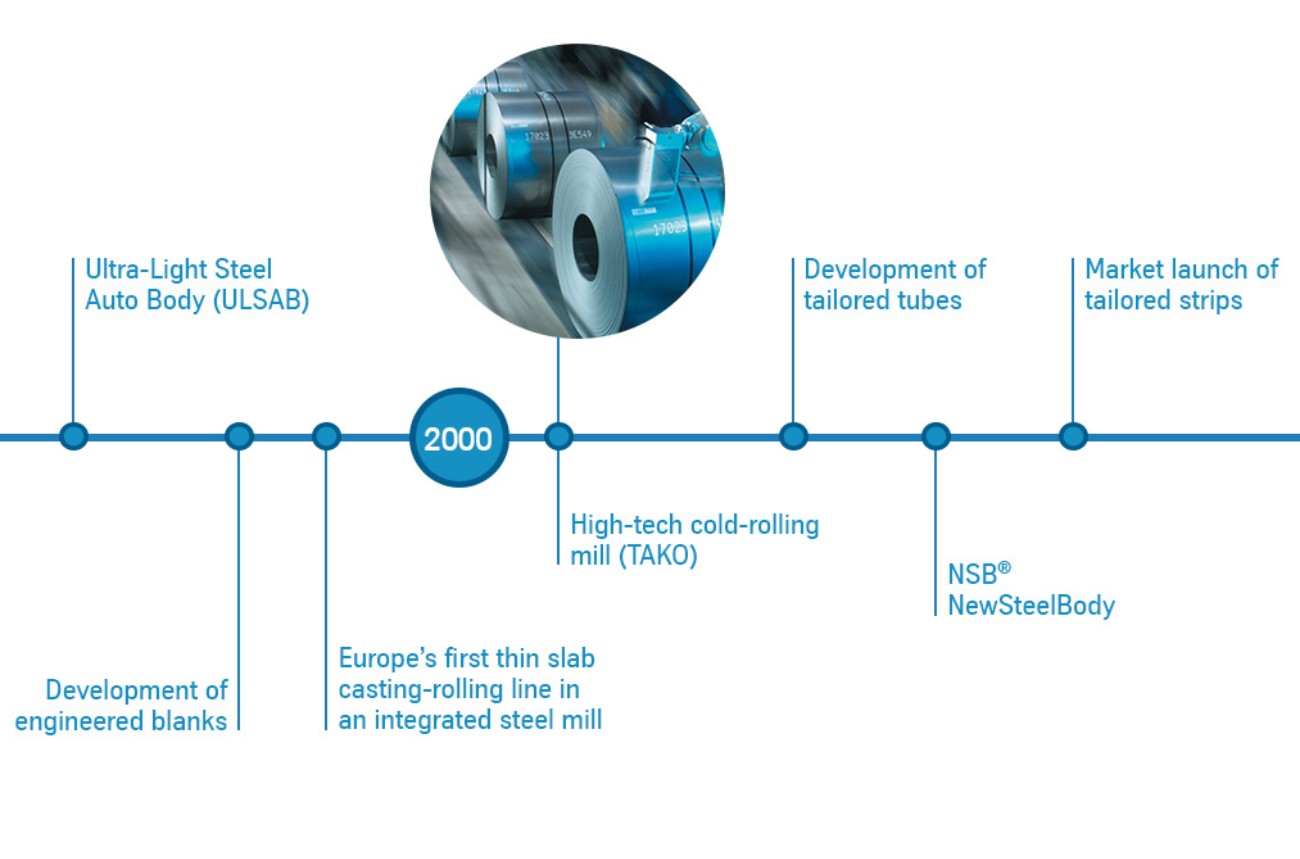
© thyssenkrupp Steel Europe Usage hints 300dpi JPG
The History and Future of Steel Technology (2 of 4)
Usage hints
We gladly provide free of charge the images included in our media library for use within daily use in the press (including magazines published weekly or monthly). In any case, condition precedent for this is that when using them, you refer to our company as the source in the immediate vicinity of the image material used and in the customary manner (© thyssenkrupp Steel Europe). If a different author is indicated, this must be stated. You are only authorized to process images to the extent that this is technically mandatory for the specific publication (e.g. black/white instead of in color in a monochromatic daily newspaper) and/or to the extent you only change the size proportionally, without using only part of the image, or to stretch, compress or modify it in any other way or to deform it. Every other processing and use is only admissible after prior written approval (email to: [email protected]). We request to be provided with an author’s copy free of charge and promptly after the respective publication of print media, with films with a digital version in a customary playback format on a generally readable data carrier. Where the image material is used online, you shall provide us with the detailed URL of the respective website and make this website accessible to us. close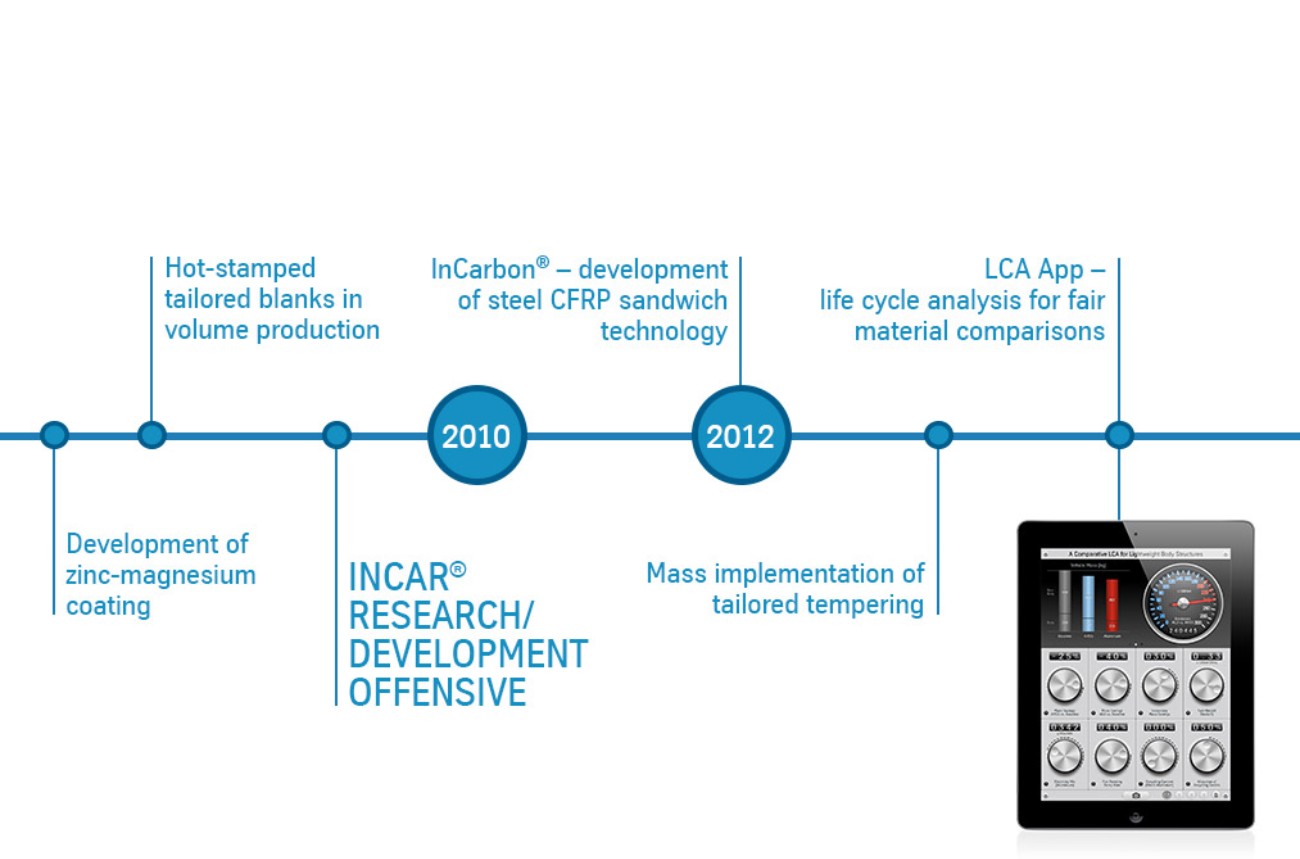
© thyssenkrupp Steel Europe Usage hints 300dpi JPG
The History and Future of Steel Technology (3 of 4)
Usage hints
We gladly provide free of charge the images included in our media library for use within daily use in the press (including magazines published weekly or monthly). In any case, condition precedent for this is that when using them, you refer to our company as the source in the immediate vicinity of the image material used and in the customary manner (© thyssenkrupp Steel Europe). If a different author is indicated, this must be stated. You are only authorized to process images to the extent that this is technically mandatory for the specific publication (e.g. black/white instead of in color in a monochromatic daily newspaper) and/or to the extent you only change the size proportionally, without using only part of the image, or to stretch, compress or modify it in any other way or to deform it. Every other processing and use is only admissible after prior written approval (email to: [email protected]). We request to be provided with an author’s copy free of charge and promptly after the respective publication of print media, with films with a digital version in a customary playback format on a generally readable data carrier. Where the image material is used online, you shall provide us with the detailed URL of the respective website and make this website accessible to us. close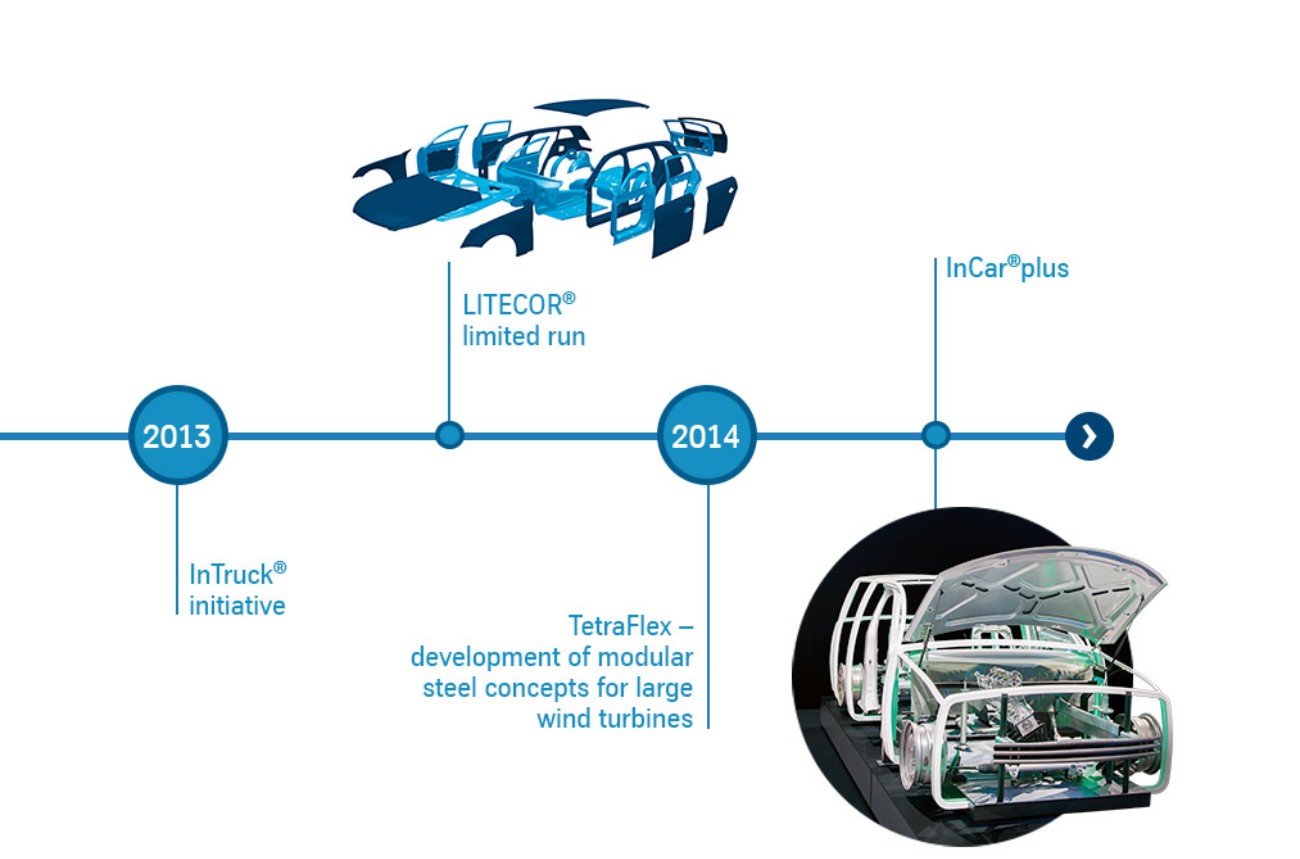
© thyssenkrupp Steel Europe Usage hints 300dpi JPG
The History and Future of Steel Technology (4 of 4)
Usage hints
We gladly provide free of charge the images included in our media library for use within daily use in the press (including magazines published weekly or monthly). In any case, condition precedent for this is that when using them, you refer to our company as the source in the immediate vicinity of the image material used and in the customary manner (© thyssenkrupp Steel Europe). If a different author is indicated, this must be stated. You are only authorized to process images to the extent that this is technically mandatory for the specific publication (e.g. black/white instead of in color in a monochromatic daily newspaper) and/or to the extent you only change the size proportionally, without using only part of the image, or to stretch, compress or modify it in any other way or to deform it. Every other processing and use is only admissible after prior written approval (email to: [email protected]). We request to be provided with an author’s copy free of charge and promptly after the respective publication of print media, with films with a digital version in a customary playback format on a generally readable data carrier. Where the image material is used online, you shall provide us with the detailed URL of the respective website and make this website accessible to us. close