Significant reduction of silicate deposits on the weld seams
Welding method: processing in focus
These impairments led to ungalvanized sheets still being predominantly used in the chassis. The reason is that what is called metal active gas (MAG) welding has become established worldwide. "On the one hand, the MAG welding process is extremely easy to automate, and on the other hand it allows significantly higher tolerances than other welding processes," says Marco Queller from the Innovation department at thyssenkrupp Steel. "In combination with galvanized steel sheets, however, there is significantly more rework. Pores and binding defects in the seam can only be found and reworked with considerable effort. As a result, processing takes more time and processes are more susceptible to disruption overall."
Research project: combining materials expertise
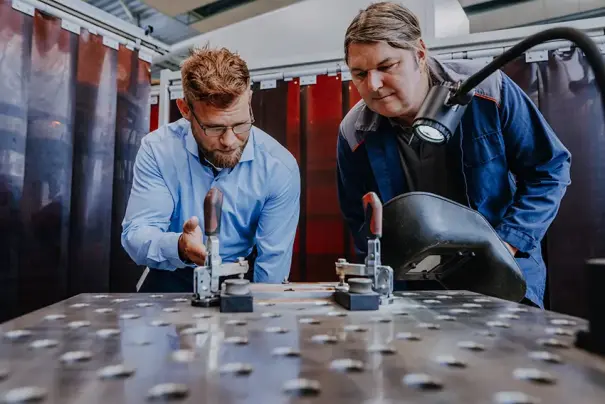
Against this background, it was an obvious step for thyssenkrupp Steel to investigate the influences of different zinc coating systems with regard to weldability and corrosion properties. This resulted in a practical research project that the development engineers from Duisburg carried out together with their long-standing customer, the internationally positioned supplier Kirchhoff Automotive. "The decisive factor for the cooperation was above all promising further developments in the field of process control and regulation of welding processes," recalls Marco Queller.
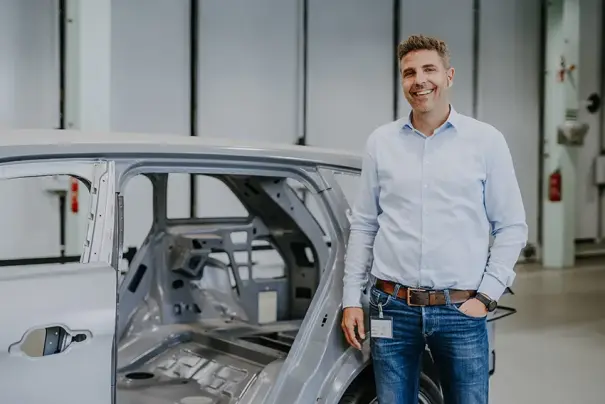
This cooperation was nothing new for the companies: they had already developed a process in 2019 to reduce silicate deposits during MAG welding. Dr. Jan Stuhrmann, R&D manager at Kirchhoff Automotive says: "Based on the positive cooperation in the past, we thought it made sense to pool competencies in a further collaboration with the joining specialists from thyssenkrupp Steel on the subject of 'practically oriented welding of galvanized steels' and carry out the investigations together." The new cooperation was therefore planned and implemented jointly from the outset as well.
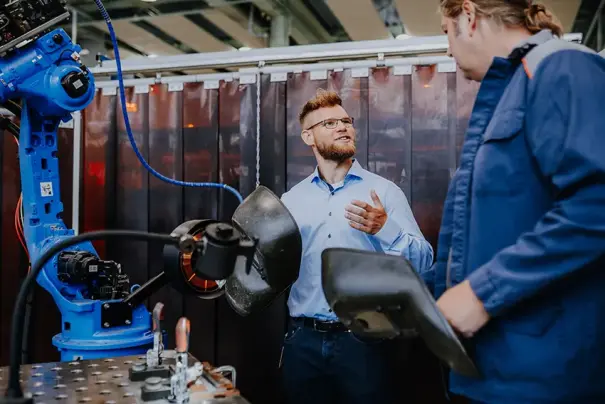
Over a period of two years, the engineers tested different zinc surface coatings as well as various influences and process optimizations in the process parameters. The investigations were carried out on microalloyed and multiphase steels such as DP600 and CP-W800 in thicknesses of 1.5 and 3.0 mm. Because the tests were carried out in parallel in the welding laboratory in Duisburg and in the Attendorn welding technology center of Kirchhoff Automotive, equipment from various manufacturers was also used in the process. In the end, the research partners reached a positive conclusion: "By choosing a high quality coating in conjunction with specific changes in the welding process, we have succeeded in improving the quality of the weld seam of zinc-coated sheets while at the same time maintaining the good corrosion properties. Decisive improvements in the process were also brought about by the use of modern electrical power sources, with which the heat input and thus also the current and voltage curves can be controlled in a more targeted manner. This resulted in significantly fewer pores and splashes," says Marco Queller.
"With ZM Ecoprotect®, we have been able to achieve the best arc stability," reports Marco Queller. The positive results and knowledge gained from the investigations will enable the research partners to significantly improve the welding qualities of galvanized materials in the future and to reduce rework rates by making process-related adjustments. At the same time, corrosion protection is ensured.