Daily press, Trade press, 2016-12-01, 12:54 pm
Electric mail deliveries: thyssenkrupp supports development of “StreetScooter” for Deutsche Post and supplies materials and components for new electric vehicle
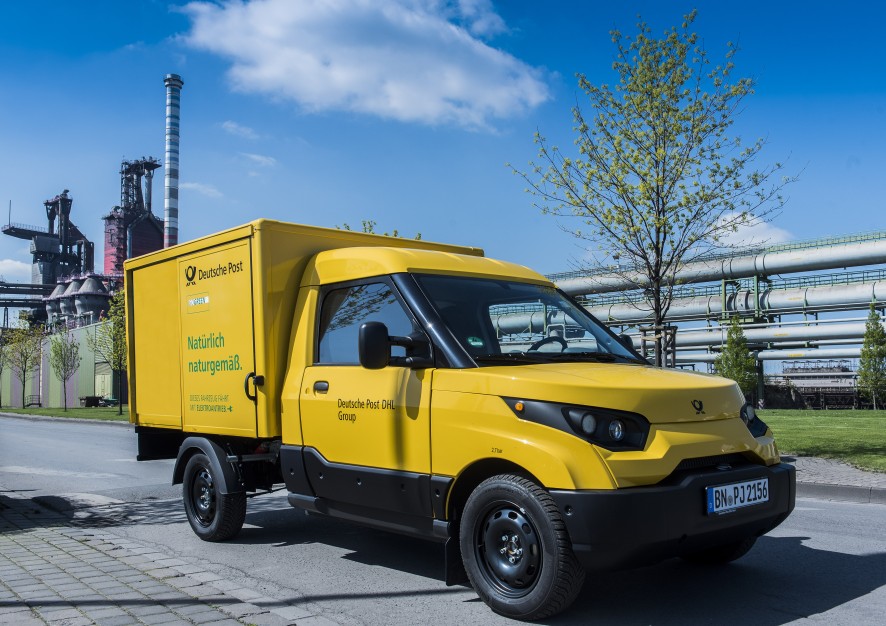
The period leading up to Christmas is a busy one for the mail service, in particular when it comes to delivering parcels and packages. The new “StreetScooter” – a smart, practical electric car – is proving a great help. The aim was to develop an eco-friendly electric vehicle that is also economically attractive even in low-volume production. Aachen-based StreetScooter GmbH is now a subsidiary of Deutsche Post DHL Group, the world’s biggest logistics operator, and produces electric vehicles for its parent company. thyssenkrupp is also engaged in e-mobility and has had links with the “StreetScooter” for some time – its steel and components divisions were involved in development from the early stages. For example, a cost-efficient production method for the floor structure was developed using lightweight steel elements. Today thyssenkrupp delivers its own “package” to Deutsche Post: Materials for the “StreetScooter” are provided by thyssenkrupp Steel and the shock absorbers come from thyssenkrupp Bilstein.
Low-cost minivan adapted to mail delivery needs
Deutsche Post acquired StreetScooter GmbH in 2014 to produce delivery vehicles for letters and packages. This resulted in the development of the “Work” model, a zero-emission vehicle adapted to the rigors of everyday deliveries. For example, the yellow van with its “green” drive system has to handle up to 200 stops and starts a day, needs to offer sufficient space to carry letters and packages and must operate reliably 300 days a year. On the other hand the vans do not need to be fast and are used almost exclusively on short-distance tours. The first 2,000 vehicles will roll off the production line in Aachen this year, rising to up to 10,000 per year from 2017. Under its “GoGreen” initiative, Deutsche Post is aiming to replace its conventional fleet with eco-friendly electric vehicles in the medium term.
Steel sandwich floor assembly protects battery in event of crash
thyssenkrupp was part of the network of companies that developed various components and modules for the electric vehicle. For example its steel division was one of the strategic partners that designed the body structure of the “StreetScooter”. The developers chose an economical lightweight solution comprising a steel body structure clad with plastic panels. High-strength steels make up 57 percent of the steel structure, allowing parts to be made thinner and lighter without sacrificing safety. The hot-forming steels used for the bumpers and A- and B-pillars likewise offer high part strength and major weight savings. Both the materials used and the tube-intensive design add to the cost efficiency of the “StreetScooter”. The tubular design also allows model variants to be developed at significantly lower cost than with conventional stamped parts.
thyssenkrupp’s steel division also developed the floor assembly for the “StreetScooter”, comprising a sandwich structure with compartments for up to three batteries. The main task of this module is to accommodate the batteries in such a way that they are not damaged in a crash, which could otherwise cause them to burn or leak. thyssenkrupp’s developers in Duisburg based their design and choice of materials on this requirement. The two-shell longitudinal members of the floor structure, between which the battery modules are positioned, are made from high-strength dual-phase steel and are so stable that they do not yield in the event of a crash, thus preventing damage to the batteries. The rockers are made from cold-rolled dual-phase steel and dissipate part of the impact energy in a controlled manner. The material not only displays high strength, it also has sufficient forming capacity to absorb crash energy. The seat structure and vehicle tunnel are mounted on the floor assembly.
Shock absorbers need to handle big weight differences
The “StreetScooter” also offers highly practical features such as a four cubic meter-plus cargo space that can hold up to 650 kilograms of payload. The enormous weight spread between the empty and fully laden vehicle places high requirements on the shock absorber set-up. That’s why the manufacturers put their faith in the expertise of thyssenkrupp’s damper specialists as early as the pre-production run of 150 vehicles.
The weight of a fully laden “StreetScooter” is 2,130 kilograms, but at the end of a long day of deliveries it can be more than half a ton less. Ensuring balanced damping over the entire spectrum calls for very careful tuning – otherwise the suspension may be overly hard or soft, depending on the situation, which would impair both comfort and safety. The components supplied by thyssenkrupp Bilstein for the trial phase proved successful, and as a result the company is also providing the shock absorbers for full production.
Over its long history, Deutsche Post has looked into using electric delivery vehicles on several occasions and has carried out a great deal of pioneering work. But today’s technology is more promising than ever before. And the delivery staff themselves are delighted with their “StreetScooters”.