Daily press, 2020-01-30, 09:25 am
thyssenkrupp Steel with innovative method for drying out raw materials
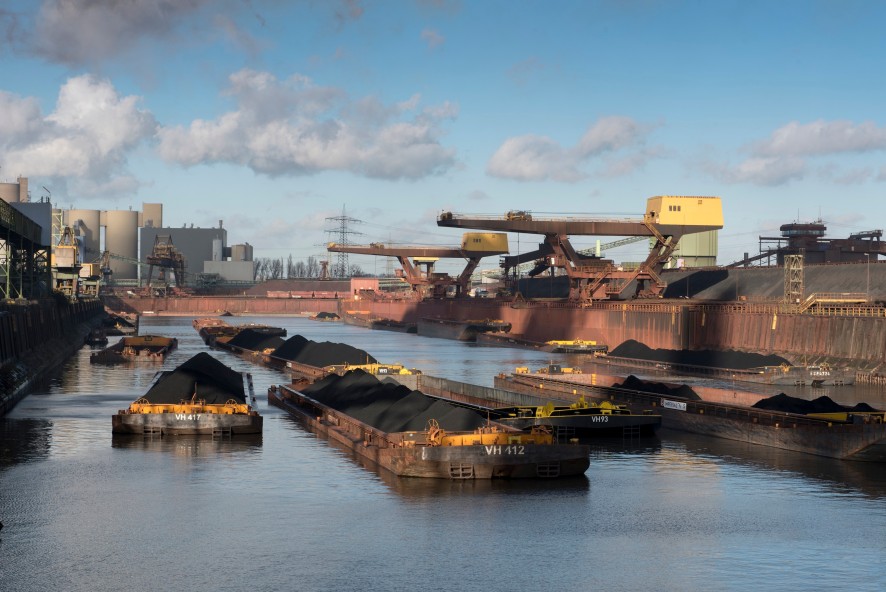
thyssenkrupp Steel’s Duisburg plant is the fifth biggest steel site in the world. Integrated iron and steel mills of this kind operate without interruption around the clock, 365 days a year. Huge amounts of raw materials are delivered to thyssenkrupp Steel’s port in Duisburg every day – mainly iron ore and coal for the blast furnaces. These raw materials need to be prepared so that they are always available in the best possible quality for use in production.
Ideas from home integrated into business operations
The various materials are removed from the ships by grabs for onward transportation at the mill. As all of this happens outdoors, rain can be a real problem for the grabs: Some of the materials are so fine that they turn to sludge if they get wet, making it impossible for the grabs to pick them up. As the materials take a long time to dry, and it often rains again before they are ready, engineers at thyssenkrupp started looking for possible solutions – and found inspiration from an unlikely source.
“We need a chemical solution to dry the ores more quickly” – that was the task chemical engineer Dr. Stefan Wienströer and his team set themselves. And straight away father-of-two Wienströer hit on an idea: diapers. Sodium polyacrylate is normally used in diapers to absorb fluid. This material is a superabsorbent polymer, capable of absorbing and retaining extremely large amounts of liquid relative to its own mass.
Less work, lower costs
This turned out to be the perfect solution for the port: In numerous tests the team in cooperation with their colleagues from raw material procurement demonstrated that the technology can be integrated seamlessly into the existing workflows with no loss of quality in the raw materials, while at the same time improving logistics and lowering port handling costs.
“Instead of waiting days or weeks for materials to dry out, we now use the superabsorbent polymers whenever needed. We mix them in using one of the grabs, and the raw materials are ready to go within two hours,” says a satisfied Stefan Wienströer. “Reliable production flow is a key factor in an integrated iron and steel mill. This method gives us greater process stability at an important step in the chain.”
And in addition to the satisfaction of seeing their idea work in practice, the project developed by Wienströer and the team also won the “steeltomorrow” award in December 2019, which thyssenkrupp Steel bestows every year on internal innovation projects.