Powering a Sustainable Future
Electric energy is the heartbeat of the energy transition, and GOES by thyssenkrupp Electrical Steel sets the rhythm and keeps it alive. By enhancing the efficiency of transformers, our products play a crucial role in reducing energy waste and supporting the integration of renewable energy sources. This not only helps in lowering greenhouse gas emissions but also ensures a reliable and more sustainable energy supply for future generations.
Applications:
- Large power transformers
- Distribution transformers
- Small transformers
- Current transformers
- Shunt reactors
- Wound cores
- Power generators
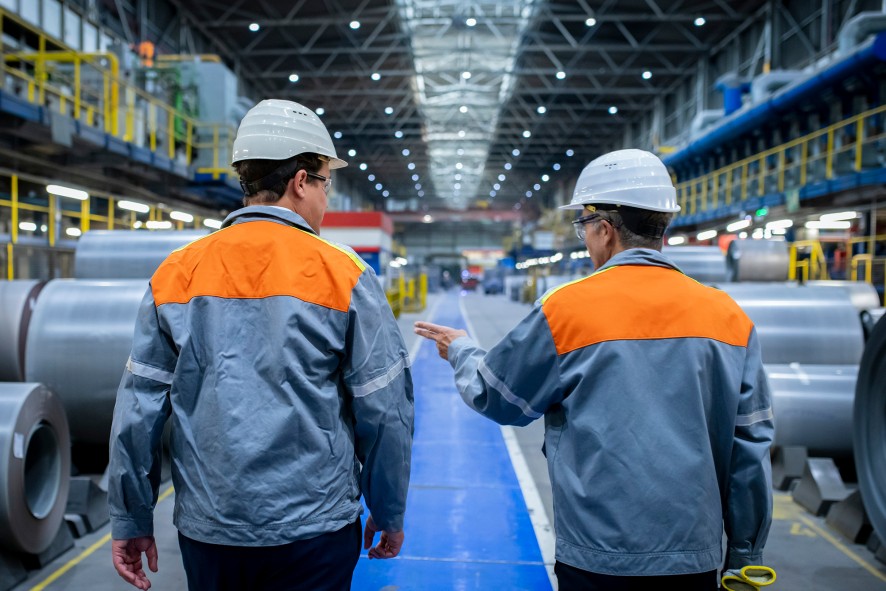

Product range
Grain oriented electrical steel bluemint® powercore® Traction GO