Elektroband ist entscheidend für die Energiewende
Energiewende: Kernkomponente Elektroband
In der Energiebranche liegt die besondere Aufmerksamkeit derzeit auf einem Material, das zwar bereits seit geraumer Zeit etabliert ist, dessen Potenzial aber erst vor dem Hintergrund der Energiewende wirklich zum Tragen kommt: hochlegiertes Elektroband. Der in einem komplexen Produktionsverfahren hergestellte Hightech-Werkstoff spielt seine Stärken unter anderem dort aus, wo Rotationsbewegungen effizient in elektrische Energie umgewandelt werden sollen oder Energie verlustarm von einer Spannung in eine andere transformiert werden muss.
„Ohne Elektroband ist ein Umbau der Energie-Infrastruktur nicht machbar. Es ist der Schlüsselwerkstoff für Kernkomponenten der Energiewende wie Windkraft-Generatoren und Transformatoren. Auch die Elektromobilität funktioniert nicht ohne Elektroband, denn es wird für jedes E-Fahrzeug und in jeder Ladesäule gebraucht“, darin sind sich Angelo di Martino, CEO von thyssenkrupp Electrical Steel, und Georgios Giovanakis, Head of Sales einig. Sie verantworten bei thyssenkrupp Steel die beiden Elektroband-Sparten kornorientiert und nicht kornorientiert.
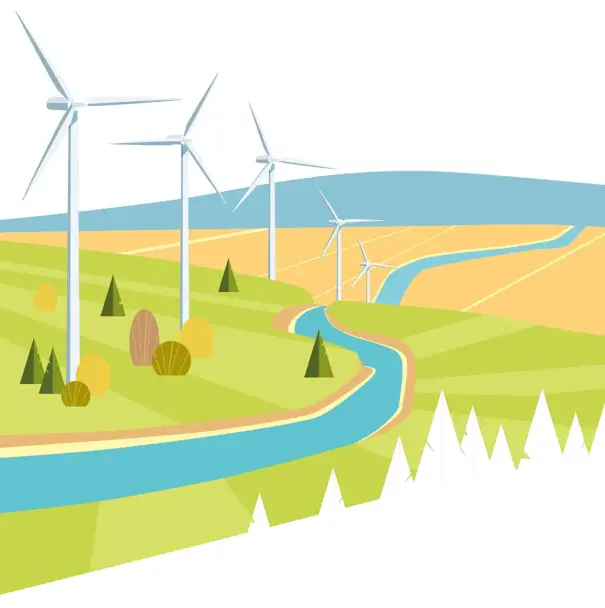
Während thyssenkrupp Electrical Steel als internationaler Premium-Hersteller von kornorientierten Elektroband-Produkten der Marke powercore® und einer der führenden Anbieter in Europa vor allem die Transformatorenbranche bedient, bringt der Bereich Sales Automotive mit seiner nicht kornorientierten Marke powercore® zum Beispiel Generatoren von Windkraftanlagen in Bewegung und mit den powercore® Traction Produkten die E-Mobilität ins Rollen. Di Martino weiter: „Mit unseren Hightech- Elektrobändern der Marke powercore® tragen wir dazu bei, den zunehmenden ökologischen Ansprüchen im Transformatorenbau gerecht zu werden. Das Material ermöglicht hohe Wirkungsgrade, die unseren Kunden helfen, die anspruchsvollen Effizienzvorgaben der EU-Ökodesign-Richtlinie einzuhalten, und trägt somit zur Senkung des weltweiten Energiebedarfs und der damit verbundenen CO2-Emissionen bei.“
Frischer Wind: Elektroband sorgt für grünen Strom
Bei der Entwicklung dieser für die Energie- und Mobilitätswende benötigten Schlüsselwerkstoffe vertraut thyssenkrupp Steel auf intensive Kundenkooperationen. Giovanakis: „Wir forschen kontinuierlich und entwickeln weitere Lösungen, um die steigenden Anforderungen der Energie- und Mobilitätsbranche zu begleiten. Kooperationen im Bereich Forschung und Entwicklung für innovative Produkte stellen für uns eine Selbstverständlichkeit dar. Dabei legen wir großen Wert auf langjährige Partnerschaften.“
Um zu sehen, wie aus solchen Entwicklungspartnerschaften erfolgreiche Praxisprojekte entstehen, lohnt sich ein Blick nach Aurich. So wie Berlin das politische Epizentrum Deutschlands ist und Frankfurt am Main den Ruf als Finanzmetropole genießt, ist die norddeutsche Kleinstadt, anderthalb Autostunden von Bremen entfernt, die inoffizielle Hauptstadt der Windenergie. Nicht nur wegen der steifen Brise, die hier rund 30 Kilometer entfernt vom Wattenmeer und den Ostfriesischen Inseln weht. Sondern vor allem, weil Enercon hier seinen Stammsitz hat. Der größte Windkraftanlagenhersteller Deutschlands verwendet seit vielen Jahren nicht kornorientiertes Elektroband von thyssenkrupp Steel.
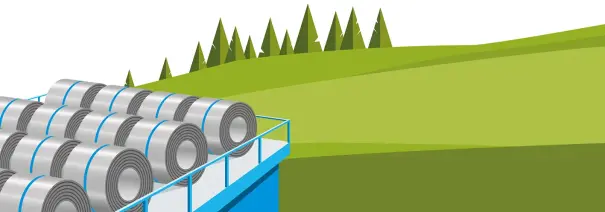
„Seit unseren Anfängen setzen wir bei unseren Generatoren auf Produkte der Marke powercore®“, sagt Ralf Mühlenbrock, Senior Component Head Generator bei Enercon Production. Wieso, ist leicht erklärt: Im Bereich der Windenergie benötigt man Werkstoffe, die über einen langen Zeitraum hinweg anspruchsvollen Umweltbedingungen – beispielsweise der salzigen Luft im Küstenbereich – standhalten. Für nicht kornorientiertes Elektroband, das schwerpunktmäßig für die Lamellen der Generatoren verwendet wird, kein Problem. Noch wichtiger aber ist: Der weichmagnetische Stahl bündelt und verstärkt den magnetischen Fluss im Inneren der Windkraft-Generatoren auf sehr effiziente Weise. So kann die mechanische Rotationsenergie fast ohne Verluste in elektrischen Strom umgewandelt werden.
Für die Enercon-Ingenieure ist das Elektroband aus Bochum in mehrfacher Hinsicht eine Kernkomponente: Sie nutzen den Werkstoff nicht nur zur Erzeugung von Strom, sondern durch das vielseitige Produktportfolio von Enercon über die gesamte Energiewertschöpfungskette hinweg. Bis hin zum Verbrauch der Energie in Elektromotoren und Geräten. In Abhängigkeit von der eingesetzten Elektroband-Sorte kann powercore® dort einen hohen Wirkungsgrad erzielen. „Die Leistungsfähigkeit der Generatoren und damit auch die Effizienz der gesamten Windenergieanlage (WEA) hängt maßgeblich von den Materialeigenschaften ab“, erklärt Thomas Sube, Key Account Manager für nicht kornorientiertes Elektroband bei thyssenkrupp Steel.
Elektroband: für Kundenwünsche maßgeschneidert
Weil Enercon als einer der weltweiten Marktführer mit über 31.600 installierten Windrädern individuelle Anforderungen an das Material stellt, hat thyssenkrupp Steel die Eigenschaften und die Zusammensetzung des Elektrobands speziell für den Windanlagenhersteller angepasst. Etwa durch eine spezielle Legierung, die für eine bessere Leitfähigkeit und gute Stanzbarkeit sorgt.
Diese Werkstoffeigenschaften sind erforderlich, weil Enercon wichtige Fertigungsschritte bündelt. Das Unternehmen kooperiert zum Beispiel mit einer Gießerei im Landkreis Aurich, in der Rotornaben, Maschinenträger und Blattadapter entstehen. Die Besonderheit: Knapp die Hälfte des verwendeten Materials ist Stahlschrott aus der eigenen Generatorproduktion. Die Stanzreste aus Elektroband werden gesammelt, eingeschmolzen und recycelt – dies ist nur durch den maßgeschneiderten Werkstoff von thyssenkrupp Steel möglich.
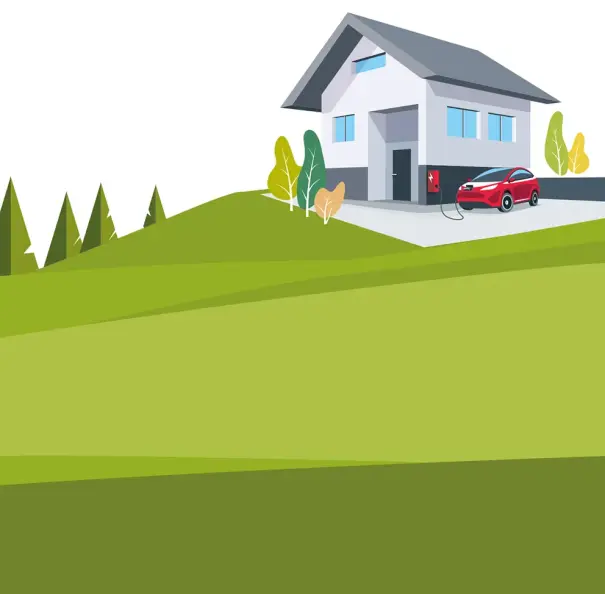
Die exzellente Zusammenarbeit der beiden Partner zahlt sich inzwischen mehr als aus:
Windkraftanlagen von Enercon mit Elektroband von thyssenkrupp Steel werden heute bereits an der französischen Atlantikküste, in den Weiten Anatoliens und sogar in Kanada eingesetzt. Und auch auf dem Heimatmarkt ist die Ausgangslage günstig. Denn der Bedarf an grünem Strom ist bereits groß – und wächst durch die aktuelle geopolitische Lage weiter. Mit Blick auf den Ausbau der erneuerbaren Energien hat sich die Bundesregierung verpflichtet, die bestehende Windkraft-Kapazität von aktuell 54 Gigawatt sukzessive auf 136 Gigawatt auszubauen. Grund genug für Enercon und thyssenkrupp Steel auf Innovationskurs zu bleiben. Thomas Sube: „In erster Linie sind wir an noch besseren magnetischen Eigenschaften unseres Elektrobands interessiert. Wir konnten bereits viel erreichen und arbeiten an mehr.“
Ultranet entlastet Versorgungssystem
Die Energiewende wird auch in Nordrhein-Westfalen vorangetrieben. Zum Beispiel vom Netzbetreiber Amprion, der sein Höchstspannungsnetz für die aktuelle Transformation des Energiesystems ausbaut. Unter anderem ist das Unternehmen dafür verantwortlich, den grünen Strom, der durch Wind- oder Solarkraft im Norden Deutschlands entsteht, zu den großen Verbraucherzentren in Süd- und Westdeutschland zu transportieren. Ein Ausbau der Strominfrastruktur ist dafür unerlässlich – schließlich soll der Anteil erneuerbarer Energien am Bruttostromverbrauch bis 2030 auf mindestens 80 Prozent steigen. So zumindest sieht es die EEG-Novelle 2021 vor. Deshalb planen und errichten Amprion und sein Projektpartner TransnetBW derzeit das sogenannte Ultranet, eine rund 340 Kilometer lange Stromautobahn. Sie reicht von Osterath in Nordrhein-Westfalen bis nach Philippsburg in Baden-Württemberg und wird nach aktuellem Stand 2026 in Betrieb gehen. Die Gesamtkosten des Mammutvorhabens betragen laut Amprion rund 1,7 Milliarden Euro.
Wie ein Bypass soll die neue Verbindung die aus dem Norden ankommende Windenergie am heute schon voll ausgelasteten Netz im Rheinland vorbei nach Süden leiten. Und das für Deutschland auf technisch neue Art und Weise. Dazu muss man wissen: Elektrischer Strom lässt sich mittels zwei verschiedener Methoden transportieren: als Wechselstrom oder Gleichstrom. Bisher gilt Wechselstrom, bei dem sich die Polarität ständig ändert, als europäischer Standard. Vor dem Hintergrund der Energiewende gewinnen jedoch die für den Langstrecken-Transport verlustärmeren Hochspannungs- Gleichstrom Übertragungsleitungen (HGÜ-Leitungen) an Bedeutung. Ultranet ermöglicht demnächst eine leistungsstärkere Nutzung der bestehenden Stromtrasse, weil ein Wechselstromkreis am Mast künftig in der Gleichstromtechnik betrieben werden kann.
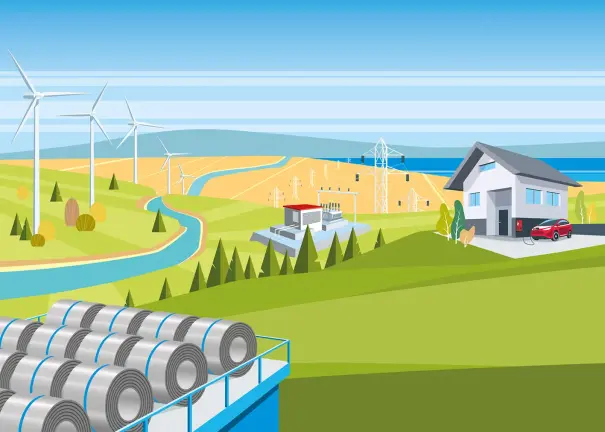
„Alle HGÜ-Leitungen, die in Deutschland geplant werden, ergänzen wiederum das bestehende Wechselstromnetz und entlasten so das Wechselstromsystem. Bei Ultranet können beide Stromarten gemeinsam auf einem Mast übertragen werden. Mit Gleichstrom gezielt sowohl von Nord nach Süd, bei Bedarf aber auch entgegengesetzt – beispielsweise zum Abtransport überschüssigen Photovoltaik-Stroms“, erklärt Joëlle Bouillon, Ultranet-Projektsprecherinvon Amprion.
Damit grüner Offshore-Strom von Verbraucherinnen und Verbrauchern in Baden-Württemberg genutzt werden kann, muss er vor seinem Weg über die HGÜ-Leitung erst in einer Konverterstation in Meerbusch nahe Düsseldorf reisefertig gemacht werden. Hier, am Anfangspunkt des Ultranet, kommt es neben der Arbeit von Schaltanlagen und Umrichtermodulen vor allem auf die Leistung der Transformatoren an. Bei der notwendigen Umwandlung von Wechsel- auf Gleichstrom und wieder zurück sorgen sie für die notwendige effiziente Umspannung auf das jeweils benötigte höhere oder niedrigere Spannungslevel – und machen es am Endpunkt wieder für das 380-Kilovolt- Wechselstromnetz der Endverbraucherinnen und -verbraucher nutzbar.
Transformatoren brauchen Top Grades
In den drei für das Ultranet und dessen Verlängerung namens A-Nord benötigten Konverterstationen in Meerbusch, Philippsburg und Emden verrichten jeweils zwölf Hightech-Transformatoren ihren Dienst. Jeder ist so groß wie eine klassische Doppelhaushälfte mit drei Etagen: zwölf Meter hoch, zehn Meter lang, 280 Tonnen schwer. Hergestellt werden die riesigen Apparate von Siemens Energy, einem weltweit führenden Unternehmen der Energietechnologie und einem von nur drei weltweiten Anbietern von Gleichstromtechnologie. Kornorientiertes Elektroband spielt laut Commodity Manager Mike König eine Schlüsselrolle im Konstruktionsprozess. Denn für das zentrale Bauteil der Maschine, den Transformatorenkern, braucht es ein Material, das die Energieverluste auf ein Minimum reduziert.
„Für die Transformatoren des Ultranet finden ausschließlich sogenannte Top Grades von thyssenkrupp Electrical Steel Verwendung“, so König. Dabei handelt es sich um haarfeine Elektrobänder mit Eisen-Silizium-Legierung, oft nicht dicker als 0,23 Millimeter. Hergestellt werden sie bereits zum Teil aus bluemint® powercore®, einem CO2-reduzierten und somit klimafreundlicheren Werkstoff, der dazu beiträgt, den ökologischen Fußabdruck der Trafo-Produktion bei Siemens Energy spürbar zu senken. Dank der innovativen Hightech-Bleche erreichen die Transformatoren, die für das Ultranet eingesetzt werden, unter Volllast einen Wirkungsgrad von rund 99 Prozent. König: „Damit genügen unsere Anlagen nicht nur höchsten Ansprüchen an die Energieeffizienz, sondern erfüllen auch die erst kürzlich weiter verschärften Vorgaben der EU-Ökodesign-Richtlinie“. Welches Einsparpotenzial sich durch die sukzessive Modernisierung von Transformatoren in Europa mit Hilfe von Elektroband realisieren lässt, weiß Marcel Hilgers, Verkaufsleiter bei thyssenkrup Electrical Steel: „Die EU erhofft sich durch die strengeren Anforderungen an Transformatoren bis 2030 eine jährliche Einsparung von rund 16 Terawattstunden. Dies entspricht ungefähr dem halben Stromverbrauch von Dänemark.
E-Mobilität gehört die Zukunft
Die voranschreitende Energiewende verändert nicht nur das Energiesystem selbst, sondern auch Nutzung und Anwendungsfelder von Energie im Allgemeinen. Ein gravierender Wandel ist bereits im Bereich Mobilität zu beobachten: So fordert unter anderem die EU-Kommission, dass ab 2035 nur noch Null-Emissions-Fahrzeuge verkauft werden dürfen. Da passt es ins Bild, dass Deutschland im Rahmen seiner angepassten Klimapolitik der Zero-Emission Vehicle Alliance (ZEV) beigetreten ist. Dieser internationale Zusammenschluss, zu dem unter anderem auch Großbritannien und die Niederlande gehören, hat das Ziel, den weltweiten Umstieg auf emissionsfreie Fahrzeuge zu beschleunigen. Bis 2050 soll es nur noch emissionsfreie PKW geben. Folgerichtig arbeitet auch die Automobilindustrie unter Hochdruck an neuen Fahrzeugen und Technologien, deren Betrieb nicht mehr von fossilen Energien abhängig sein soll. Stattdessen setzen die Hersteller auf die direkte Stromnutzung durch batterieelektrische Antriebe – und treffen damit mehr und mehr den Nerv der Kunden. Bereits heute stellt Deutschland den größten Markt für Elektroautos in Europa dar.
Stahl von thyssenkrupp Steel ist unverzichtbarer Bestandteil dieser Entwicklung. Zahlreiche renommierte Markenhersteller setzen für die Entwicklung und Konstruktion zeitgemäßer automobiler Lösungen auf den in jeglicher Hinsicht vielseitigen Werkstoff. So gibt es am Markt bereits CO2-neutral produzierte Fahrzeugmodelle, deren Stahlanteil samt Türen und Motorhaube bei weit über 90 Prozent liegt.Aber nicht nur in der Karosserie, sondern auch im Herzen des E-Fahrzeugs – dem Elektromotor – spielt Stahl eine ganz wichtige Rolle. Und wieder sind es Elektroband-Produkte, die den Weg Richtung Zukunft ebnen.
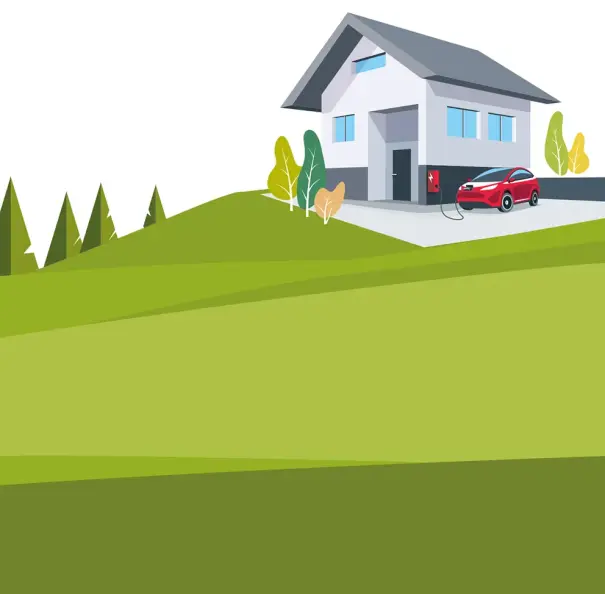
„Nicht kornorientiertes Elektroband ist unverzichtbar für die E-Mobilität“, so Frank Bosch, Key Account Manager im Bereich Sales Automotive bei thyssenkrupp Steel. Das liegt an den besonderen Anforderungen, die bei elektrischen Fahrzeugen an das Antriebsaggregat gestellt werden. Denn im Gegensatz zu herkömmlichen Elektromotoren, etwa für Aufzüge oder Haushaltsanwendungen, wo die Betriebsfrequenz bei rund 50 Hertz liegt, weisen Motoren für Elektroautos hohe Drehzahlen auf. Hieraus resultieren wesentlich höhere elektrische Frequenzen von deutlich über 400 Hertz. Damit es bei diesen Frequenzen nicht zu hohen Ummagnetisierungsverlusten kommt, die den Wirkungsgrad des Motors – und damit auch die Reichweite des Fahrzeugs – negativ beeinflussen, braucht es die weichmagnetischen Werkstoffe. Idealerweise dünn, mit homogenen mechanischen Eigenschaften und magnetischen Eigenschaften. Nicht kornorientiertes Elektroband fällt in diese Kategorie. „Die magnetische Flussdichte des Materials, die für das Drehmoment des Motors entscheidend ist, wird zusätzlich durch ein besonderes Processing positiv beeinflusst“, weiß Frank Bosch. Das Ergebnis: Mit nicht kornorientiertem Elektroband der Marke powercore® Traction liegen die Ummagnetisierungsverluste in Elektromotoren für E-Fahrzeuge fast 30 Prozent unter denen heutiger Standardsorten.
Ohne stetige Forschungs- und Entwicklungsarbeit wäre das nicht möglich. Frank Bosch: „Wir betreiben in unserer Anwendungstechnik einen eigenen Motorenprüfstand, wo wir unsere powercore® Traction Güten in den unterschiedlichen Motorentypen untersuchen. So können wir unsere Kunden bei der Auswahl der richtigen Güte in Abhängigkeit von den jeweiligen Anforderungen bestens beraten.“ Wie gut dies funktioniert, zeigt nicht zuletzt der Erfolg bei den Endkundinnen und -kunden. Im vergangenen Jahr ist die Zahl der Neuzulassungen von batteriebetriebenen E-Autos in der EU im Vergleich zum Vorjahr deutlich gestiegen: von 539.000 auf 878.000 Fahrzeuge. Ein Trend, der weiter anhält: Wie der Verband der europäischen Automobilhersteller (ACEA) berichtet, betrug der Anteil der zugelassenen rein elektrisch betriebenen Fahrzeuge im zweiten Quartal 2022 knapp 10 Prozent an den Gesamtzulassungen. Das ist ein deutlicher Sprung im Vergleich zum selben Vorjahreszeitraum. Und wer weiß: Vielleicht werden schon bald einige Modelle mit grünem Offshore-Strom aus dem Ultranet aufgeladen.