Electrical steel is crucial for the energy turnaround
Energy turnaround: electrical steel as a core component
In the energy sector, particular attention is currently being paid to a material that has been established for a long time, but whose potential is only really coming to fruition against the backdrop of the energy turnaround: high-alloyed electrical steel. The high-tech material, which is manufactured in a complex production process, shows its strengths, among other things, in areas where rotational movements are efficiently converted into electrical energy or energy has to be transformed from one voltage to another with low losses.
"Without electrical steel, a transformation of the energy infrastructure is not feasible. It is the key material for core components of the energy transition such as wind turbines generators and transformers. Electric mobility will not work without electrical steel either, because it is needed for every electric vehicle and in every charging station," agree Angelo di Martino, CEO of thyssenkrupp Electrical Steel, and Georgios Giovanakis, Head of Sales. At thyssenkrupp Steel, they are responsible for the two electrical steel divisions: grain-oriented and non-grain-oriented.
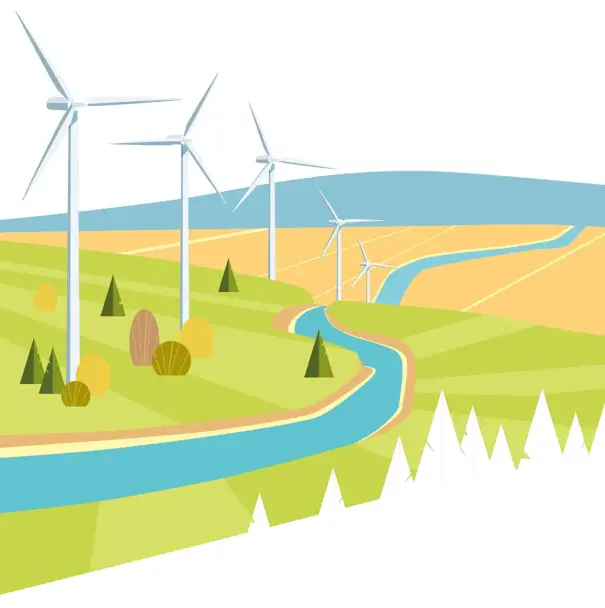
thyssenkrupp Electrical Steel, as an international premium manufacturer of grain-oriented powercore® electrical steel products and one of the leading suppliers in Europe, mainly serves the transformer sector. The Sales Automotive unit, on the other hand, with its non-grain-oriented powercore® brand gets wind turbine generators moving, for example, and brings electric mobility up to speed with its powercore® Traction products. Di Martino continues: "With our high-tech powercore® electrical steels, we are helping to meet the increasing ecological demands in transformer construction. The material enables high efficiencies that help our customers meet the demanding efficiency targets of the EU Ecodesign Directive, helping to reduce global energy demand and associated CO2 emissions."
Fresh wind: electrical steel provides green electricity
In developing these key materials needed for the energy and mobility revolution, thyssenkrupp Steel relies on intensive customer cooperation. Giovanakis: "We are continuously researching and developing further solutions to accompany the increasing demands of the energy and mobility industry. Cooperations in the field of research and development for innovative products are a matter of course for us. In doing so, we place great value on long-term partnerships."
To see how successful practical projects emerge from such development partnerships, it is worth taking a look at Aurich. Just as Berlin is the political epicenter of Germany and Frankfurt am Main enjoys a reputation as a financial metropolis, the small northern German town, an hour and a half's drive from Bremen, is the unofficial capital of wind energy. Not only because of the stiff breeze that blows here about 30 kilometers away from the Wadden Sea and the East Frisian Islands. But above all because Enercon has its headquarters here. Germany's biggest wind turbine manufacturer has been using non-grain-oriented electrical steel from thyssenkrupp Steel for many years.
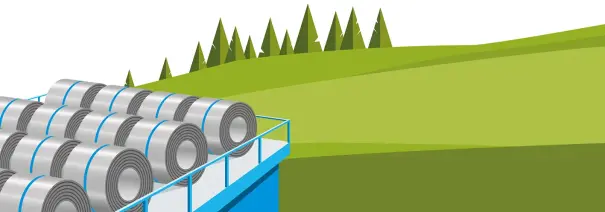
"Since our beginnings, we have relied on powercore® products for our generators," says Ralf Mühlenbrock, Senior Component Head Generator at Enercon Production. Why, is easily explained: In the wind energy sector, materials are needed that can withstand demanding environmental conditions over a long period of time – for example, the salty air in coastal areas. No problem for non-grain oriented electrical steel, which is mainly used for the plates of the generators. But even more important: the soft magnetic steel concentrates and amplifies the magnetic flux inside the wind turbine generators in a very efficient way. So, the mechanical rotational energy can be converted into electric current with almost no losses.
For the Enercon engineers, the electrical steel from Bochum is a core component in several respects: they use the material not only to generate electricity, but also across the entire energy value chain thanks to Enercon's versatile product portfolio. Right through to the consumption of energy in electric motors and devices. Depending on the electrical steel grade used, powercore® can achieve high efficiency there. "The performance of the generators and thus the efficiency of the entire wind turbine (WT) depends to a large extent on the material properties," explains Thomas Sube, Key Account Manager for non-grain-oriented electrical steel at thyssenkrupp Steel.
Electrical steel: tailor-made for customer requirements
Enercon, as one of the world's market leaders with over 31,600 wind turbines installed, has individual requirements for the material; for this reason, thyssenkrupp Steel adapted the properties and composition of the electrical steel especially for the wind turbine manufacturer. For example, through a special alloy that ensures better conductivity and good punchability.
These material properties are necessary because Enercon combines important manufacturing steps. For example, the company cooperates with a foundry in the district of Aurich, where rotor hubs, machinery frames and blade adapters are produced. The special feature: just under half of the material used is steel scrap from the company's own generator production. The chads from electrical steel are collected, melted down and recycled – this is only possible thanks to the tailored material from thyssenkrupp Steel.
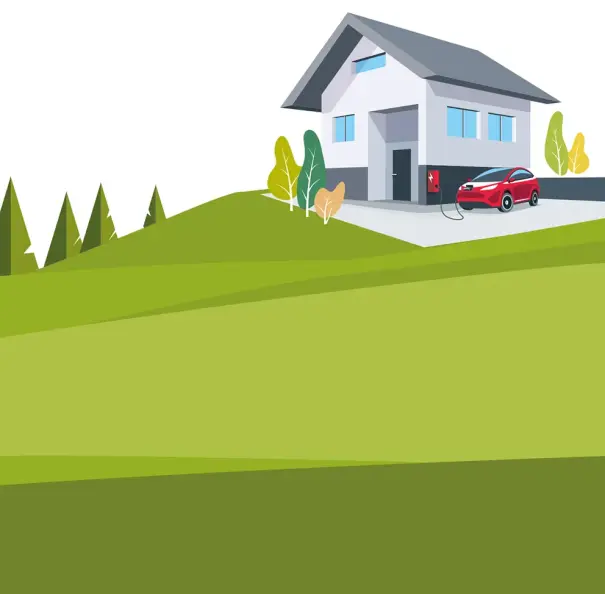
The excellent cooperation between the two partners is now more than paying off:
wind turbines from Enercon with electrical steel from thyssenkrupp Steel are already in use on the French Atlantic coast, in the vast expanses of Anatolia and even in Canada. And the starting position on the domestic market is also favorable, because the demand for green power is already high – and continues to grow due to the current geopolitical situation. With a view to expanding renewable energies, the German government has committed itself to successively increasing existing wind power capacity from the current 54 gigawatts to 136 gigawatts. Reason enough for Enercon and thyssenkrupp Steel to stay on course for innovation. Thomas Sube: "First and foremost, we're interested in even better magnetic properties for our electrical steel. We've already been able to accomplish a lot and are working on more."
Ultranet reduces the strain on the supply system
The energy turnaround is also being driven forward in North Rhine-Westphalia. For example, by the grid operator Amprion, which is expanding its extra-high voltage grid for the current transformation of the energy system. Among other things, the company is responsible for transporting the green electricity generated by wind or solar power in northern Germany to the major consumer centers in southern and western Germany. An expansion of the electricity infrastructure is essential for this – after all, the share of renewable energies in gross electricity consumption is to rise to at least 80 percent by 2030. At least, that's what the 2021 amendment to German Renewable Energy Act (EEG) envisages. That's why Amprion and its project partner TransnetBW are currently planning and constructing the so-called Ultranet, a 340 kilometer-long electricity highway. It stretches from Osterath in North Rhine-Westphalia to Philippsburg in Baden-Württemberg and, as things stand at present, will come on stream in 2026. According to Amprion, the total cost of the mammoth project is around 1.7 billion euros.
Like a bypass, the new connection is intended to route the wind energy arriving from the north to the south past the grid in the Rhineland, which is already fully exploited today. And in a technically new way for Germany. To understand this, you need to know: Electric current can be transported by two different methods: as alternating current or direct current. Until now, alternating current, in which the polarity changes constantly, has been considered the European standard. Against the backdrop of the energy turnaround, however, high-voltage direct-current (HVDC) transmission lines, which have lower losses for long-distance transport, are gaining in importance. Ultranet will soon enable more powerful use of the existing power line because an AC circuit on the mast can be operated in DC technology in the future.
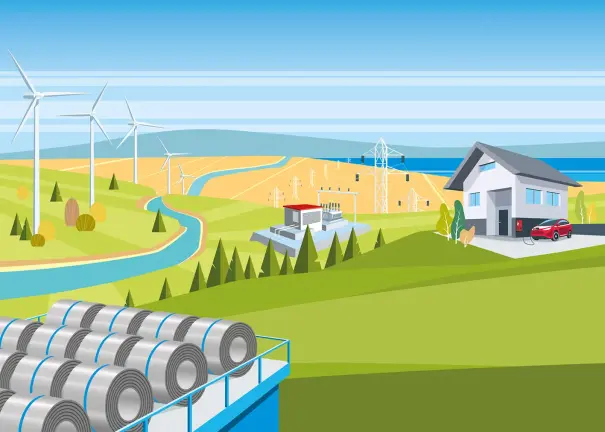
"All HVDC lines planned in Germany will in turn complement the existing AC grid, relieving the AC system. With Ultranet, both types of electricity can be transmitted together on one pylon. With direct current targeted both from north to south, but also in the opposite direction if required – for example, to transport surplus photovoltaic electricity," explains Joëlle Bouillon, Ultranet project spokesperson for Amprion.
In order for green offshore electricity to be used by consumers in Baden-Württemberg, it must first be made ready for transport in a converter station in Meerbusch near Düsseldorf before it travels via the HVDC line. Here, at the starting point of the Ultranet, in addition to the work of switchgear and converter modules, the most important thing is the performance of the transformers. During the necessary conversion from alternating to direct current and back again, they ensure the efficient transformation to the higher or lower voltage level that is required in each case – and make it usable again at the end point for the 380-kilovolt alternating current grid of the end consumers.
Transformers need top grades
Twelve high-tech transformers are doing their job in each of the three converter stations required for the Ultranet and its extension called A-North in Meerbusch, Philippsburg and Emden. Each is the size of a normal semi-detached house with three floors: twelve meters high, ten meters long, weighing 280 metric tons. The giant apparatuses are manufactured by Siemens Energy, a world leader in energy technology and one of only three global suppliers of direct current technology. Grain-oriented electrical steel plays a key role in the design process, according to commodity manager Mike König. For the central component of the machine, the transformer core, a material is needed that reduces energy losses to a minimum.
"Only top grades from thyssenkrupp Electrical Steel are used for the Ultranet transformers," says König. These are hair-thin iron-silicon alloy electrical steel strips, often no thicker than 0.23 millimeters. They are already partly made of bluemint® powercore®, a reduced-CO2 and thus more climate-friendly material that helps to noticeably reduce the ecological footprint of transformer production at Siemens Energy. Thanks to the innovative high-tech plates, the transformers used for the Ultranet achieve an efficiency of around 99 percent under full load. König: "This means that our systems not only meet the highest standards of energy efficiency, but also fulfill the recently further tightened requirements of the EU Ecodesign Directive." Marcel Hilgers, Sales Manager at thyssenkrupp Electrical Steel, knows the savings potential that can be realized through the successive modernization of transformers in Europe with the help of electrical steel: "The EU hopes the stricter requirements for transformers will save about 16 terawatt hours annually by 2030. This is roughly equivalent to half the electricity consumption of Denmark.
Electric mobility is the future
The advancing energy turnaround is not only changing the energy system itself, but also the use and application fields of energy in general. A serious change can already be observed in the area of mobility: Among other things, the EU Commission is demanding that only zero-emission vehicles be sold from 2035 onwards. It fits into the picture that Germany has joined the Zero-Emission Vehicle Alliance (ZEV) as part of its adapted climate policy. This international alliance, which includes the United Kingdom and the Netherlands, among others, aims to accelerate the global switch to zero-emission vehicles. By 2050, there should only be zero-emission passenger cars. Consequently, the automotive industry is also working at full speed on new vehicles and technologies, the operation of which should no longer be dependent on fossil fuels. Instead, manufacturers are focusing on the direct use of electricity through battery-electric drives – and are increasingly striking a chord with customers. Germany already represents the largest market for electric cars in Europe.
Steel from thyssenkrupp Steel is an indispensable part of this development. Numerous renowned brand manufacturers rely on this versatile material in every respect for the development and design of contemporary automotive solutions. For example, there are already CO2-neutral vehicle models on the market, the steel content of which, including doors and hood, is well over 90 percent.However, steel plays a very important role not only in the body, but also in the heart of the electric vehicle – the electric motor. And again, it is electrical steel products that pave the way to the future.
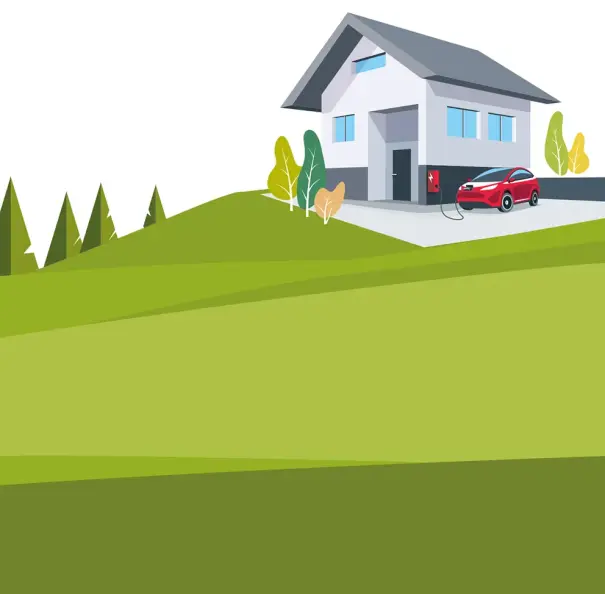
"Non-grain-oriented electrical steel is indispensable for electric mobility," says Frank Bosch, Key Account Manager in Sales Automotive at thyssenkrupp Steel. This is due to the special requirements placed on the drive unit in electric vehicles. Because in contrast to conventional electric motors, for example for elevators or household applications, where the operating frequency is around 50 Hz, motors for electric cars have high speeds. This results in significantly higher electrical frequencies of well over 400 Hz. Soft magnetic materials are needed to prevent high remagnetization losses at these frequencies, which would have a negative impact on the efficiency of the motor – and thus also on the range of the vehicle. Ideally thin, with homogeneous mechanical and magnetic properties. Non-grain oriented electrical steel falls into this category. "The magnetic flux density of the material, which is crucial for the torque of the motor, is additionally positively influenced by a special processing," observes Frank Bosch. The result: with non-grain-oriented powercore® Traction electrical steel, the core losses in electric motors for electric vehicles are almost 30 percent lower than those of today's standard grades.
This would not be possible without constant research and development work. Frank Bosch: "We operate our own motor test bench in our Application Technology department, where we test our powercore® Traction grades in the various motor types. This enables us to provide our customers with the best possible advice on selecting the right grade depending on the specific requirements." How well this functions is shown not least by the success with end customers. In the past year, the number of new registrations of battery-powered electric cars in the EU increased significantly compared with the previous year: from 539,000 to 878,000 vehicles. A trend that is continuing: As reported by the Association of European Automobile Manufacturers (ACEA), registered all-electric vehicles accounted for just under 10 percent of total registrations in the second quarter of 2022. This is a significant jump compared with the same period of the previous year. And who knows: perhaps some models will soon be charged with green offshore electricity from the Ultranet?