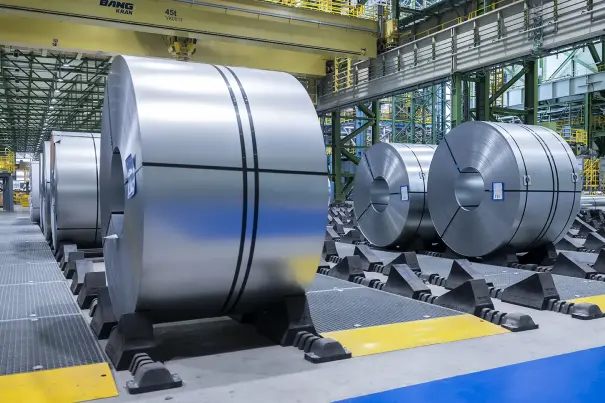
Rund 3.500 Schaltschränke sind in der FBA 10 zu finden. Sie dienen je nach Ausführung unter anderem dazu, die elektrische Leistung in der Anlage zu verteilen sowie die Antriebe und Aggregate der Produktionsstraße zu steuern und zu regeln. 13.000 Quadratmeter feuerverzinktes Feinblech mit einem Gesamtgewicht von etwa 150 Tonnen waren in der Herstellung notwendig – natürlich produziert von thyssenkrupp Steel. Damit aus dem korrosionsbeständigen und langlebigen Ausgangsmaterial funktionale und robuste Systemschränke für die empfindliche Automatisierungstechnik entstehen konnten, gingen sechs Coils auf Reisen, um bei spezialisierten Dienstleistern weitere Bearbeitungsschritte zu durchlaufen.
Entwicklung von Station zu Station
Erster Stopp: Dillenburg in Mittelhessen. Hier ist die Firma Stahlo, ein Unternehmen der Friedhelm Loh Group, zu Hause, eines der größten werksunabhängigen Stahl-Service-Center in Deutschland. Das Unternehmen produziert unter anderem Spaltband, Tafeln, Formzuschnitte und Konturen in allen gängigen Güten: von ultrahochfest bis zu sensibler Außenhautqualität. Als Schnittstelle ist Stahlo im Gesamtprozess von zentraler Bedeutung. „Wir sind das auf den Materialeinsatz spezialisierte Bindeglied zwischen Stahl produzierenden und weiterverarbeitenden Unternehmen und vernetzen auf effiziente Weise Ressourcen, Menschen und Technologien“, erklärt CEO Oliver Sonst. Bei Stahlo, das sich perspektivisch als „Green Steel Provider“ positionieren will und mit thyssenkrupp Steel bereits eine Vereinbarung zur Lieferung von CO2-reduziertem bluemint® Steel abgeschlossen hat, wurde das Ausgangsmaterial für die weitere Verarbeitung präzise in passende Zuschnitte getafelt. Sonst: „Die Produktionsverfahren sind besonders optimiert in Bezug auf Maßhaltigkeit und Verschnitt. Die Bereitstellung der lackierfähigen Stahloberflächen erfolgt durch uns stets just in time.“
Flexible Systemtechnik
Im nächsten Schritt erreichte das angearbeitete Blech die Kleinstadt Rittershausen, Geburtsstätte des Stahlo-Schwesterunternehmens Rittal. Bei Rittal handelt es sich um einen weltweit führenden Anbieter für Schaltschranksysteme, Automatisierungstechnik und die dazugehörige Infrastruktur. Rittal formt das von Stahlo geschnittene Blech durch Rollprofilierungsverfahren in Rahmen- und Schrankteile um und verarbeitet sie so, dass nachfolgende Prozessschritte für die Kunden wenig Aufwand erfordern. „Ein wesentliches Merkmal unserer Systemtechnik ist, dass der Aufbau der Schränke völlig flexibel gestaltet und ausgehend von einem digitalen Zwilling effizient und mit hohem Automatisierungsgrad realisiert werden kann – einschließlich mechanischer Bearbeitung der Montageplatten und der Flachteile“, so Dr. Dirk Pieler, Leiter der Business Unit Industry bei Rittal. Die virtuellen Abbildungen der einzelnen Schaltschränke – die sogenannten digitalen Zwillinge – entstehen bereits in der frühen Planungsphase und begleiten den Gesamtprozess. Sie entwickeln sich mithilfe einer Software, die das Rittal-Schwesterunternehmen Eplan entwickelt hat, und dienen dem in Graz (Österreich) ansässigen Technologieunternehmen Andritz als Basis für die Konfiguration und Bestückung der vielen unterschiedlichen Gehäuse.
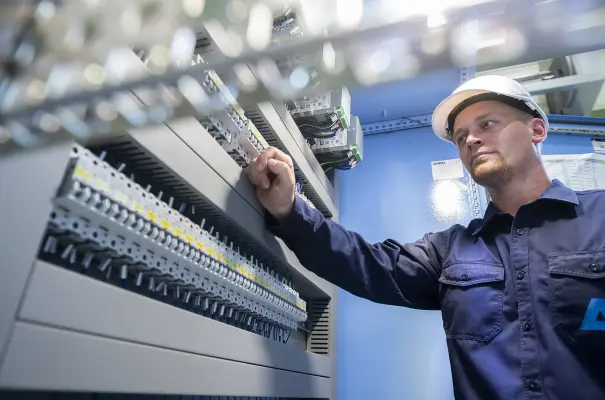
Andritz bietet Anlagen, Systeme und Serviceleistungen für unterschiedliche Industrien – und war bei der FBA 10 dafür zuständig, die notwendige Intelligenz in das Gesamtsystem einzupflanzen. „Die Planungsabwicklung des sehr komplexen und umfangreichen Projektes mit mehr als 100.000 Stromlaufplanseiten und Millionen von Datenpunkten wurde mit einem hochautomatisierten, datenbankbasierten Engineering-Prozess durchgeführt, der von der Planung bis zur Fertigung einen durchgängigen, digitalen und effizienten Workflow ermöglicht“, erläutert Michael Luu, Head of Engineering Processes E&A bei Andritz Metals. „Daraus entstanden in der Fertigung Tausende Schränke und Kästen zur effizienten Energieverteilung und smarten Anlagenautomatisierung, die wir an der FBA 10 in Betrieb genommen haben“, ergänzt Michael Czakert, Vice President Global Metals Automation bei Andritz Metals.
Erfolgsgeschichte setzt sich fort
Seit Mitte 2022 sind die fertig ausgestatteten Systemschränke nun bereits in der FBA 10 in Betrieb und stellen auf verschiedene Art und Weise sicher, dass die Anlage reibungslos funktioniert. Sie sind damit ein weiteres von vielen Dutzend Erfolgsbeispielen für die gute und bewährte Zusammenarbeit von thyssenkrupp Steel, Stahlo, Rittal und Andritz. Axel Pohl: „Alle vier Unternehmen stehen dafür, dass die Prozessschritte unserer gemeinsamen Projekte immer so mit Know-how und Wissen angereichert werden, dass am Ende intelligente, innovative – und künftig auch immer nachhaltigere – Produkte und Lösungen entstehen.“