Fachpresse, Tagespresse, 25.03.2015, 13:12
Maßanfertigung aus Grobblech: Erstmals wurde Kokskübel für die Kokerei Schwelgern in Duisburg ausgetauscht – Nachfolger entstand in Handarbeit
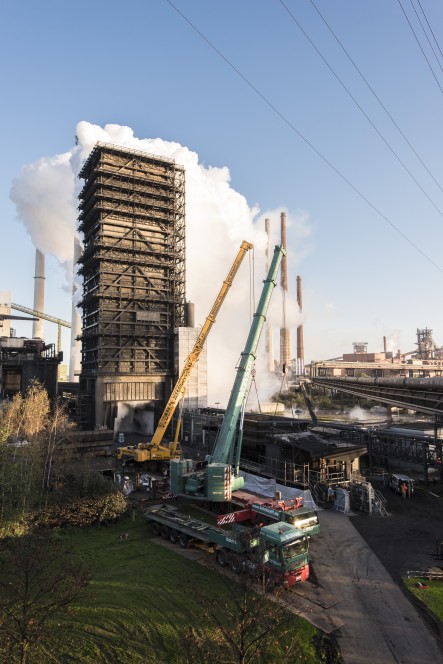
Wenn ein Topf spröde wird und kaputt zu gehen droht, muss er ausgewechselt werden. Das ist in der heimischen Küche so, aber auch in der Kokerei Schwelgern in Duisburg – einem Unternehmen, das den für die Stahlherstellung wichtigen Brennstoff Koks herstellt. „Unsere Kokerei ist zwar erst elf Jahre jung, ein Kokskübel der ersten Stunde war aber schlichtweg verschlissen“, erklärt Michael Cremer, Leiter Erhaltungsbetriebe Maschinenanlagen. „Die Kübel stehen täglich unter einer extremen Belastung, da ist ihre Lebenszeit automatisch begrenzt.“ Deshalb musste ein neuer Behälter her, der so groß ist wie ein Einfamilienhaus, so viel wiegt wie 15 Elefanten (mit Anbauten 75 Tonnen) und nur aus Stahl besteht. Nach dem Umbau gilt „aus alt mach neu“: Derzeit wird der ausrangierte Koloss verschrottet und wiederverwertet.
Die riesigen Kübel sind täglich hohen Temperaturschwankungen ausgesetzt. Sie werden an den Koksbatterien mehrmals täglich mit 55 Tonnen glühendem Koks gefüllt, zum Löschturm gefahren und dort mit rund 100 Kubikmeter Wasser abgeschreckt. Durch diese Behandlung wird verhindert, dass der glühende Koks verbrennt und sichergestellt, dass er als Reduktionsmittel und Energieträger bei der Erschmelzung von Roheisen im Hochofen eingesetzt werden kann. Eine solche Behandlung ist gut für den Koks, aber auf Dauer schlecht für selbst das widerstandsfähigste Material: Der alte Kübel war irgendwann nicht mehr brauchbar.
Die Arbeiten zur Herstellung des neuen Gefäßes haben rund zwölf Wochen gedauert. Der 65 Tonnen-Koloss wurde nach vorhandenen Bauzeichnungen von Hand und vor Ort zusammengeschweißt: „Solche Kübel gibt es natürlich nicht von der Stange zu kaufen“, verdeutlicht Cremer die aufwändige Fertigung. „Die Einzelteile wurden in einer Werkstatt vorgefertigt und bei der Kokerei in Handarbeit zusammengefügt. Und zwar Tag und Nacht, nach Plänen, die wir gemeinsam mit einem Ingenieurbüro und unserem konzerninternen Dienstleister ThyssenKrupp Mill Services & Systems ausgearbeitet hatten.“ Dabei hat das übergreifende Team die Ursprungskonstruktion in verschiedenen Bereichen aufgrund der in den vergangenen elf Jahren gesammelten Erfahrungswerte geändert. Erstmals wurden auch Grobbleche der Sorte XAR500 – das ist ein zwei Zentimeter dicker, besonders hochwertiger und widerstandsfähiger Baustahl aus dem Hause ThyssenKrupp Steel Europe - im Inneren des Kübels als Verschleißschutz eingesetzt „Jetzt ist das Gefäß noch funktionaler und hält womöglich länger“, blickt Cremer in die Zukunft.
Bevor der fertig gestellte Kübel seine erste Schienenfahrt zwischen Koksbatterien und Löschturm aufnehmen konnte, war noch eine Menge Arbeit nötig. Der fertige Würfel musste im Rahmen eines zweieinhalbwöchigen Stillstands ausgetauscht werden. Also: Den alten Kübel vom Fahrwerk demontieren, mit Hilfe zweier, insgesamt 700 Tonnen schwerer Spezialkräne ausschwenken und neben dem Fahrzeug absetzen, den neuen Kübel wieder auf das Fahrwerk setzen und dann noch die Wasserleitung, Elektrik und Hydraulik anschließen. Der Tausch hat gut geklappt: „Wir waren voll im Zeitplan und alles ist gut und vor allem unfallfrei vonstattengegangen“, resümiert Cremer erleichtert. „Jetzt haben wir erst mal wieder lange Zeit Ruhe.“
Extreme Temperaturschwankungen belasten Kokskübel
55 Tonnen glühenden Koks kann der Löschkübel aufnehmen. Mehrmals täglich wird er mit einer heißen Ladung befüllt. 1.000 Grad ist die Temperatur des Kokses, wenn er in die Kübel fällt. Er wird innerhalb von 50 Sekunden auf 50 Grad abgekühlt. 100 Kubikmeter Wasser werden benötigt, um eine Ladung Koks im Kübel zu löschen. Das entspricht etwa 400 Badewannenfüllungen. Die Kokerei Schwelgern stellt jährlich 2,6 Millionen Tonnen Brennstoff für die Duisburger Hochöfen her. Sie ist die modernste Anlage ihrer Art in Europa und besitzt die weltweit größten Öfen. Derzeit sind rund 300 Mitarbeiter bei der Kokereibetriebsgesellschaft Schwelgern (KBS) beschäftigt.