Trade press, Daily press, 2015-03-25, 01:12 pm
Made-to-measure heavy plate construction: Coke bucket for Schwelgern coke plant in Duisburg replaced for the first time – replacement built by hand
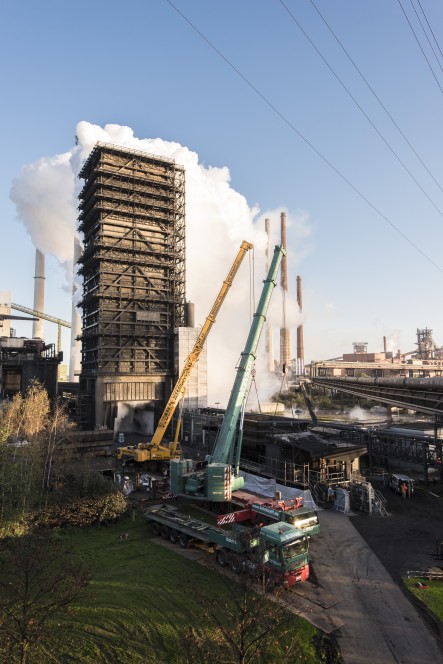
When pots and pans wear out, you replace them. It’s no different at the Schwelgern coke plant in Duisburg, which produces coke as a fuel for steel production. “Our coke plant may be only eleven years old but one of the original coke buckets was completely worn out,” explains Michael Cremer, head of mechanical maintenance. “The buckets come under extreme strain every day so their life is naturally limited.” A new bucket was therefore needed, as big as a house, as heavy as 15 elephants (75 tons with attachments) and consisting entirely of steel. The decommissioned bucket is now being scrapped and recycled.
The giant buckets are exposed to extreme temperature fluctuations. Several times a day they are filled with 55 tons of red-hot coke, transported to the quenching tower and quenched with around 100 cubic meters of water. This treatment stops the hot coke from burning and ensures it can be used as a reducing agent and energy source in the production of pig iron in the blast furnace. The treatment is good for the coke but in the long term bad for even the toughest material: Eventually the old bucket was no longer fit for purpose.
Manufacturing the new bucket took around twelve weeks. The 65 ton vessel was welded together by hand on site according to existing construction drawings: “Obviously you can’t buy buckets like these off the peg,” says Cremer. “The individual parts were prefabricated in a workshop and joined together by hand at the coke plant. We worked day and night to plans we developed jointly with a consulting engineering firm and our sister company ThyssenKrupp Mill Services & Systems.” The team modified several areas of the original construction based on the experience gained over the past eleven years. For the first time, heavy plates of grade XAR500 – two centimeters of particularly tough high-quality structural steel made by ThyssenKrupp Steel Europe – were used as a wear lining inside the bucket. “Now the bucket is even more functional and may last longer,” says Cremer.
Before the finished bucket was able to make its first journey on rails between the coke batteries and the quenching tower there was still a lot of work to be done. The bucket had to be replaced during a two and a half week shutdown. It involved removing the old bucket from its car using two special cranes weighing a total 700 tons, placing the new bucket on the car and reconnecting water, electrical and hydraulic systems. The operation was a success: “We were bang on schedule. Everything went smoothly and above all there were no accidents,” says Cremer. “The new bucket should keep us going for a long while.”
Extreme temperature fluctuations put strain on coke buckets
The quenching bucket can hold 55 tons of red-hot coke. Several times a day it is filled with a hot load. The temperature of the coke when it falls into the bucket is 1,000 degrees. It is cooled to 50 degrees in the space of 50 seconds. 100 cubic meters of water is needed to quench one load of coke in the bucket. That’s the equivalent roughly of 400 bath tubs. The Schwelgern coke plant produces 2.6 million tons of fuel a year for the blast furnaces in Duisburg. It is the most modern of its kind in Europe and boasts the world’s biggest ovens. Kokereibetriebsgesellschaft Schwelgern (KBS) currently employs around 300 people.