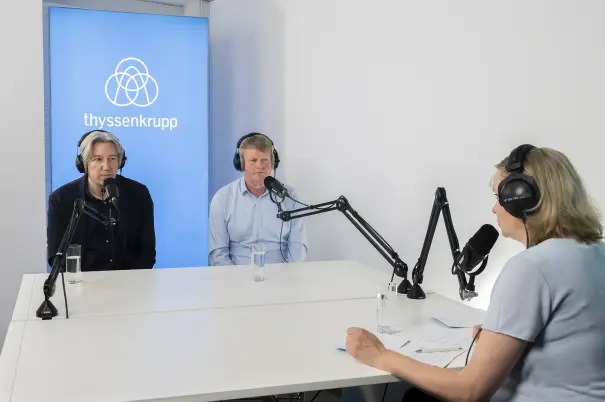
Folge 13: Pionierprojekt in Hohenlimburg – Stahlproduktion mit Windkraft
In der neuesten Folge von "gekocht gewalzt veredelt" taucht Christine Launert tief in das spannende Thema Windkraft ein. Gemeinsam mit Milan Nitzschke, Geschäftsführer der SL Naturenergie, und Thomas Westermann, Projektleiter bei thyssenkrupp Hohenlimburg, stellt sie ein bahnbrechendes Projekt vor, das in Deutschland bis dato einmalig ist: die direkte Anbindung eines Windparks an ein Industriewerk in Hagen bei thyssenkrupp Hohenlimburg. Erfahren Sie, welche Herausforderungen und Erfolgsgeschichten hinter diesem Pionierprojekt stecken und wie es die Zukunft der industriellen Produktion beeinflussen kann. Eine spannende Diskussion über Innovationen, Nachhaltigkeit und die Transformation der Stahlindustrie.
Folge 13 in Schriftform
Christine Launert: Liebe Zuhörerinnen, liebe Zuhörer, willkommen zu einer neuen Folge von gekocht, gewalzt, veredelt, dem Podcast rund um das Thema Stahl. Nachdem wir in der letzten Folge über die Energiewende gesprochen haben und darüber, was das ganze mit Stahl zu tun hat, habe ich heute Gäste zu einem ganz konkreten Beispiel, wie Windstrom direkt in eines unserer Werke kommt. Meine Gäste heute werden uns ein Projekt vorstellen, das in Deutschland bislang einzigartig ist: Milan Nitzschke, Geschäftsführer der SL Naturenergie, ein Spezialist für Windparkanlagen, schön, dass sie da sind.
Milan Nitzschke: Hallo.
Christine Launert: Und mein Kollege von thyssenkrupp Hohenlimburg, der das Projekt nicht nur geleitet, sondern auch mit initiiert hat, Thomas Westermann, danke auch ihnen, dass sie heute mein Gast sind.
Thomas Westermann: Hallo.
Christine Launert: Mein Name ist Christine Launert, ich bin Pressesprecherin bei thyssenkrupp Steel. Schön, dass ihr dabei seid.
Christine Launert: Herr Westermann, sie sind seit vielen, vielen Jahren bei thyssenkrupp in Hagen Hohenlimburg, haben dort viele Projekte geleitet. Bei dem Projekt, über das wir heute sprechen, geht es darum, dass das Werk in Hohenlimburg mit Windenergie versorgt wird. Worum geht es, kurz gesagt?
Thomas Westermann: Ja, es geht darum, dass wir uns entschlossen haben, auch einen Bestandteil der Transformation selber mit in die Hand zu nehmen, das heißt, für unser Produkt grünen Stahl, auch etwas grüne Energie, und die dann natürlich direkt in diesem Fall einsetzen zu wollen, und hatten an der Stelle, ja, ich sag mal, mehrere Optionen, die wir auch alle in der Vergangenheit sehr intensiv geprüft haben und sehr intensiv hinterfragt haben, und eine dieser Optionen war dann zum Beispiel auch Windenergie, und da sind dann im Jahr 2022 die ersten Kontakte mit SL Naturenergie zustande gekommen, und seitdem beschäftigen wir uns intensiv mit dem Thema, und wir haben das Projekt nach einem langen Weg und nach vielen, vielen Hürden mittlerweile zu einem Punkt gebracht, wo wir Energie einspeisen und Energie auch grün nutzen können.
Christine Launert: Und was ist das besondere jetzt daran? Ich meine Windenergie einzusetzen, an und für sich, ist ja nichts besonderes mehr.
Thomas Westermann: Das besondere daran ist natürlich, dass wir hier zum ersten Mal in Deutschland eine Direkteinspeisung haben, dass wir uns damit beschäftigt haben: wie kann man also direkt ein Kabel bei uns in das Werk bekommen? Das war ein langer Weg, das war auch viel Arbeit und, wie gesagt, viele Hürden, die wir haben überschiffen müssen oder überspringen müssen. Hier insbesondere, sage ich mal, die Regularien, die an den Stellen sicherlich immer noch in Deutschland relativ schwierig sind, aber wo wir uns intensiv mit den Kollegen von SL beschäftigt haben und es zu einem, ja, ich sage jetzt mal, aktuell guten Abschluss gebracht haben.
Christine Launert: Dankeschön. Herr Nitzschke, sie sind seit vielen Jahren in der Branche der erneuerbaren Energien beheimatet und sind jetzt Geschäftsführer eines Spezialisten für den Bau von Windkrafträdern. Kann man sagen, dass natürliche Energie ihre Passion ist?
Milan Nitzschke: Ja, das kann man auf jeden Fall sagen. Also ich habe irgendwann mit 16, 17 oder so mich das erste Mal mit erneuerbaren Energien beschäftigt, hatte dann das Glück, über die Arbeit für damals ein Mitglied des europäischen Parlamentes, in den politischen Bereich reinzurutschen. Da ging es dann auch schon darum, erneuerbare Energien in Europa auszubauen. Später ganz viele andere Tätigkeiten, heute ganz praktisch der Bau von Windkraftanlagen, insbesondere in diesem sehr schönen Energieland Nordrhein-Westfalen.
Christine Launert: Was war das besondere für sie an diesem Projekt?
Milan Nitzschke: Ja, erstmal hatten wir einen Windpark und haben uns überlegt, was machen wir jetzt damit? Irgendwo muss der Strom hin, und sie müssen dann halt immer eine Trasse planen für ein Kabel, und dann gehen sie normalerweise ins öffentliche Netz. Und dann kam uns die Idee, wir können hier oben, quasi vom Standort aus, können wir runter schauen auf das Werk von thyssenkrupp in Hohenlimburg. Eigentlich ist es doch total naheliegend, dass wir das Kabel dann genau dort hinlegen, weil ja offensichtlich ist, dass ein solcher Betrieb sehr viel Strom braucht, und dann haben wir gedacht, machen wir das einfach, und haben dann auf dem Weg allerdings auch lernen müssen, wie schwierig das sein konnte.
Christine Launert: Bevor wir da ganz genau drauf eingehen, wie kamen sie beide denn dann auch zusammen? Also wie muss man sich das vorstellen, nachdem sie geschaut haben und das Werk gesehen haben?
Thomas Westermann: Also, wenn ich das richtig erinnere, hat unser Energiemanager irgendwann mal zu mir gesagt, da hat ein Herr Nitzschke angerufen, und mit dem habe ich am Telefon ein bisschen gequatscht. Der sitzt da oben mit seinen Windrädern auf dem Berg und weiß nicht wohin mit dem Kabel, und das wäre eine Option, sollen wir uns nicht mal damit beschäftigen? Das war, sage ich mal, so der Anfang. Ich hatte ja vorhin schon mal gesagt, 2022, im Sommer muss das so rum gewesen sein. Genaues Datum, Zeitpunkt haben wir zu dem Zeitpunkt nicht festgehalten und auch nicht auf Papier geschrieben. Aber zu dem Zeitpunkt gab es so die ersten Kontakte, und wir haben uns dann sehr intensiv mit den Technikern von SL auch damit auseinandergesetzt. Was geht da, was ist das, was kommt da überhaupt über Windprognosen von Windrädern, die, sag ich mal, ähnliche Standorte haben, haben wir dann mal geguckt, wie sehen unsere Lastgänge im Werk aus, passt das irgendwie übereinander, und sind also dann im Laufe des Jahres 22 bis zum Ende hin sehr überzeugt gewesen davon, dass das ein guter Weg sein kann, dass es für uns eine gewisse Grundlast bringen wird, um uns zu versorgen. Und ja, so ist es dann, wie gesagt, peu à peu weitergegangen.
Christine Launert: Ganz im Sinne quasi der heutigen Politik, bestimmt dann auch einfach umzusetzen, oder?
Thomas Westermann: Ich glaube, da haben wir beide genug Manpower reingesteckt, also beide Parteien genug Manpower reingesteckt, sowohl auf der technischen Seite als natürlich auch auf der juristischen, kaufmännischen Seite. Das war, wie gesagt, ein zähes Ringen in Teilbereichen und in Details, die immer mal wieder dazu führten, dass die eine Partei gesagt hat, da geht es nicht weiter, und die andere dann gesagt, das muss weitergehen. Das war aber geben und nehmen, das war auf beiden Seiten, sag ich mal, ähnlich und gleich, und ich bin eigentlich froh an der Stelle, dass keiner, sage ich mal, frühzeitig dann mal das Handtuch aus der Ecke geworfen hat und gesagt hat, K.O. ich kann nicht mehr. Wir waren eigentlich immer an dem Punkt, dass wir gesagt haben, ja, aufstehen, weitermachen, geht!
Milan Nitzschke: Also wir haben hier tatsächlich ein bisschen Pionierarbeit geleistet, und ich glaube, unsere beiderseitige Erwartung war eigentlich, das gibts schon irgendwo, das können wir einfach abkopieren. Und das war merkwürdigerweise nicht der Fall. Und im Nachhinein haben wir dann obwohl, wie gesagt, ich bin lange dabei bei den erneuerbaren Energien und bei der Windenergie, und ich habe aber auch fest damit gerechnet, irgendwo gibt's das, und musste dann selber lernen: nee, wir sind die ersten, die das umsetzen. Und der Grund war, dass es durchaus schon ein Paar versucht hatten, aber immer auf der Strecke aufgegeben haben, weil die Regularien, Energiewirtschaftsrecht, Erneuerbare-Energien-Gesetz so viele Rechtsunsicherheiten für die Projekte mitgebracht haben, dass sich keiner getraut hat, da ranzugehen. Am Ende gibt es möglicherweise irgendwie ein wirtschaftliches Risiko darin, dass man nicht tragen mag, und deswegen haben wir uns dann aber zusammengesetzt, nicht gesagt, okay, wir gehen jetzt hier wieder auseinander, sondern wir ziehen das einfach bis zum letzten durch. Und da möchte ich mal ein ganz dickes Kompliment aussprechen. Das hätte man nämlich nicht mit jedem machen können, und da war ein Team in Hohenlimburg, dann später auch die Konzernleitung quasi in Duisburg mit im Boot, das zu keinem Zeitpunkt irgendwann gesagt hat, da ist ein Problem, vor dem knicken wir ein, sondern wir haben immer eins nach dem anderen gelöst. Aber dieser ganze Prozess, nicht etwa das Kabel legen, das anschließen, das ist eine Sache von Tagen oder Wochen, aber der rechtliche Prozess, bis wir einen rechtssicheren Vertrag hatten mit allen Beteiligten, auch dem Netzbetreiber und anderen, das hat ungefähr ein Jahr gedauert. Und jetzt ist es natürlich wichtig, dass wir einmal diese Pionierarbeit geleistet haben, aber das bitte niemals nochmal jemand so lange dafür brauchen muss, sondern jetzt haben wir einfach mal ein Modell, das können sich andere auch anschauen, und ich hoffe, dass es davon noch ganz viele geben wird.
Christine Launert: Also keinesfalls ein Selbstläufer, und ohne eine gute Portion Hartnäckigkeit wäre es nicht gegangen. Gibt es denn Dinge in dem Projekt, an die sie sich ganz besonders gern erinnern oder die sie vielleicht auch immer mal wieder erzählen?
Thomas Westermann: Es gibt viele Dinge, die wir gerne erzählen an der Stelle und auch gerne, sag ich mal, der Öffentlichkeit erzählen wollen. Wir haben also auch von unserer Seite, auf der technischen Seite viele Dinge gemacht, die wir in normalen Projekten in der Form nicht machen, auch auf der technischen Seite. Wir sind alle vorangegangen, haben Dinge ausgerüstet, vorgerüstet, um dann für den Tag X eigentlich gewappnet zu sein. Und das sind Dinge, die macht man im normalen Projekt so nicht, sondern da geht man eigentlich einen Projektsteckbrief durch, plant den, lässt den vernünftig einkaufen, fängt irgendwann an, wenn alle Regularien und alle kaufmännischen Dinge geregelt sind. Hier sind wir zwischendurch, sag ich mal, immer mal wieder ins kalte Wasser zusammen gesprungen, haben das gelöst, haben da weitergemacht. Bestes Beispiel war eigentlich die Kabelverlegung, die auch zwischenzeitlich immer mal wieder von der Trassierung einen anderen Weg genommen hat, weil dann der eine oder der andere, ob es nun die Stadt war oder ob es nun ein liebenswerter Nachbar war, im Wege gestanden hat. Da gab's Lösungen, und wir haben die gemeinsam gemeistert und haben auch, sag ich mal, an der Stelle durchaus unseren Mitarbeitenden über viele Monate viel zugemutet. Wir haben Parkplatzflächen gesperrt, und wir haben in Hohenlimburg nicht viel Parkplatz. Das weiß jeder, der schon mal da war oder das gesehen hat. Aber wir konnten das gut vermitteln, weil wir einfach an der Stelle auch vermitteln konnten, das ist ein innovatives Projekt. Das ist ein Projekt, wo wir eine Vorreiterschaft haben und wo wir im Grunde genommen auch vieles, sag ich mal, tun, was vielleicht andere an der Stelle nicht tun, wo viele drüber reden, aber es dann nicht ausführen. Und das ist für uns auch wichtig, denn das ist für mich, sag ich mal, so ein Projekt, wo wir wirklich kein Greenwashing machen, sondern wir haben etwas in der Hand, nämlich grünen Strom, der direkt bei uns in die Anlagen eingespeist wird und unsere Anlagen betreibt.
Christine Launert: Darauf würde ich gerne gleich nochmal ein bisschen näher eingehen. Herr Nitzschke, gibt es auch bei ihnen etwas bei dem Projekt, wo sie sagen, das erzähle ich auch bei jeder Betriebsversammlung oder wie auch immer?
Milan Nitzschke: Das ganz besondere war, hier sind sich Menschen aus zwei Welten begegnet. Wir müssen einfach mal 10, 15 Jahre zurückdenken. Da war die Stahlindustrie und auch die Menschen, die in der Stahlindustrie gearbeitet haben, auch die Gewerkschaft, sehr, sehr kritisch gegenüber dem Ausbau erneuerbarer Energien, sehr kritisch gegenüber der Windenergie. Die These war, das macht doch alles nur teurer, und andere in Europa ziehen da gar nicht mit. So, jetzt haben wir einmal erlebt, was teuer ist in den Jahren 2022/2023 nach dem Angriff Russlands auf die Ukraine, und alle haben gemerkt, wie fragil unser Energiesystem ist. Mit fossilen Energien, mit importierten Energien werden wir nicht dauerhaft bezahlbare Preise haben können, und da ist etwas komplett umgeschlagen. Und eigentlich hat auch der oder die Letzte im Land verstanden, wir brauchen die Erneuerbaren, und wir brauchen sie nicht irgendwann, sondern jetzt so viel wie möglich. Denn auch wenn ich erst mal Geld in die Hand nehmen muss, um eine Windkraftanlage zu bauen, wenn die erst mal steht, verursacht die ja kaum noch Kosten, dann kommt der Wind und dann haben wir den Strom. Das heißt, wir haben kalkulierbare Preise, während das bei fossilen Energien, die ich immer wieder neu zukaufen muss, was weiß ich, eine Schiffsladung Kohle oder Gas aus der Pipeline, jedes mal den tagesaktuellen Preis zahlen muss. Und auf einmal sind sich Leute begegnet, wie gesagt, die vorher skeptisch sich gegenüberstanden, die auch aus ganz anderen Kulturen kamen, sich vielleicht auch ihren Job mal unter ganz anderen Gesichtspunkten ausgewählt haben. Und die sind sich begegnet und haben sich erstaunlicherweise sofort verstanden, weil da eine Macher-Mentalität auf beiden Seiten war. Wir ziehen das jetzt durch, und alle reden darüber, wir machen das jetzt, wir machen hier ein Produkt grün oder zumindest grüner. Das ist das wesentliche. Die ganzen Kleinigkeiten, wie oft wir da im Berg gestanden haben, weil wir sehr schwierig in Hohenlimburg von einer ordentlichen Anhöhe runter ins Tal mussten, was wir da bei der Kabelverlegung für Probleme hatten, das gerät alles im Hintergrund, wenn man auf der anderen Seite weiß, man hat da einen Partner, der genauso das Projekt umsetzen will wie man selbst, und das war das wichtigste.
Christine Launert: Hm, da waren wir gerade bei der Nachhaltigkeit unserer Produktion. In den letzten Folgen von "gekocht, gewalzt, veredelt" haben wir immer wieder von unserer Dekarbonisierung gesprochen. Wir ändern die Art, wie wir Roheisen herstellen, nämlich mit Hilfe von Wasserstoff anstelle der Kokskohle. Das spart immens viele CO2-Emissionen. Kann denn da die Windenergie mithalten? Also dass wir das Werk in Hohenlimburg mit 4 Windrädern betreiben?
Thomas Westermann: Das ist durchaus ein nicht zu vernachlässigender Faktor. Wir haben aktuell, sag ich mal, von der Prognose her, ungefähr 40 Gigawatt-Stunden, die wir im Jahr jetzt über die Windenergie beziehen werden. Das sind zirka 40 % unseres Gesamtbedarfs an elektrischer Energie, und wenn wir das Umrechnen auf unseren Fußabdruck, dann sehen wir, dass es nahezu 11 % unseres Fußabdrucks grüner macht, also 11 % an den CO2 Emissionen sparen wir über diese grüne Windenergie. Und das ist aus meiner Sicht schon ein ganz erheblicher Anteil, und der führt natürlich auch dazu, dass wir die Anfänge jetzt des grünen Stahls auch im Verkauf, das Näherbringen an den Kunden, natürlich sauber vermarkten können. Wir können sauber den grünen Stahl, so wie wir ihn verkaufen wollen, jetzt mit diesem grünen Strom herstellen und haben natürlich auch noch Reserven. Also ich kann nur an alle appellieren, in dieser Welt, kauft grünen Stahl. Das ist im Moment möglich, und das ist eine schöne Sache, und, wie gesagt, ist es auch ein schöner Effekt, in Richtung unserer Belegschaft, in Richtung der Gesamtkundschaft, einfach zu zeigen, guckt mal hier, das kommt direkt vom Berg, und das passt direkt zu unserem Produkt.
Christine Launert: Nehmen wir unsere Zuhörerinnen und Zuhörer einmal mit zu uns ins Werk, weil wir haben jetzt schon ganz viel vom Berg, der Strom bis ins Werk, da sind wir außen. Was machen wir denn überhaupt in Hohenlimburg? Was stellen wir da her, und wo wird dann der grüne Strom eingesetzt? Wo kommt der zu tragen?
Thomas Westermann: Ja, wir sind ein Warmwalzwerk für Mittelband, das heißt, wir stellen Flachstahl her, Flachband her, in kleineren Dimensionen als unsere Kollegen in Duisburg, maximal so bis 720 Millimeter breite, und haben in der Regel, sage ich mal, in den vergangenen Jahren über den Daumen ungefähr 1 Millionen Tonnen Warmband erzeugt, haben dahinter noch Anlagen geschaltet wie Beizen, Beizen zirka 80 %, 32 % wird gespalten, ein Teil wird noch geglüht. Das heißt also eine Wertschöpfungskette, die je nach Kunde unterschiedlich aussehen kann. Es kann Spaltband sein, also längsgeteiltes Material, es kann geglühtes Material sein, es kann nur gebeiztes Material sein. Das wird also in Hohenlimburg produziert.
Christine Launert: Habe ich als Normalsterblicher Mittelband bei mir im Alltag?
Thomas Westermann: Ja, überall, also, sie fahren wahrscheinlich jeden Morgen mit dem Auto zur Arbeit und unser Produkt ist ein hoch präzises Produkt und hat spezielle Anwendungen, gerade im Automobilbau und in Sicherheitsbauteilen, ob das nun irgendwelche Airbags sind, ob das nun Bremsen sind, Bremsanlagen sind, ob das nun Sitze sind, da wird es in großer Vielzahl eben eingesetzt und verbaut, teilweise auch noch über den Zwischenschritt, über die im hiesigen Raum oder in unserem Raum ansässige Kaltwalzindustrie. Aber es findet, sage ich mal, eine große Anwendung im Automobilbereich. Aber nichtsdestotrotz haben wir natürlich auch noch andere Bereiche. Wir sind eben ein spezieller Hersteller von Spezialprodukten und können auch andere Industrien, sag ich mal, bedienen, die da sind Messertechnik, Agrarwirtschaft oder auch Luftfahrt, da sind wir, sage ich mal, natürlich mit wesentlich weniger Mengen unterwegs, aber jeder hat eigentlich, sage ich mal, dieses Produkt irgendwo direkt in seinem Alltag in der Nähe.
Christine Launert: Warmwalzwerke arbeiten ja mit wahnsinnigen Kräften, mit viel Hitze. Wo hat da die Windenergie eine Chance bzw. wo wird sie da eingesetzt?
Thomas Westermann: Ja, ich hatte ja vorhin gesagt, wir haben ungefähr 40 % unseres Energiebedarfs elektrisch jetzt über die Windräder abgedeckt. Wir haben, wie gesagt, insbesondere die Lastkurven und die Prognose sehr stark versucht zu matchen und übereinandergelegt und stellen da einfach fest, dass wir den größten Anteil dieser Windenergie direkt in unserem Warmwalzwerk einsetzen können. Da sind die größten Antriebe, da sind die größten Verbraucher. Das heißt jetzt nicht, dass, sage ich mal, an die anderen Anlagen nicht auch ein Elektron dieser grünen Energie fließen würde. Das ist natürlich so, weil das Netz ist, sag ich mal, ein Verbundnetz, aber der Hauptabnehmer ist das Walzwerk.
Christine Launert: Wenn mehr Strom produziert wird, als wir jetzt verbrauchen in Hohenlimburg, was passiert dann mit dem Strom? Es ist ja eine Direktanbindung. Sie sagten ja gerade, es wird nicht ins Netz eingespeist.
Thomas Westermann: Doch, es wird dann auch ins Netz eingespeist, und zwar indirekt. Es geht also praktisch durch unsere Leitungen. Wir haben ja nicht nur die Windenergie, das wäre jetzt schön, aber wir haben natürlich weiterhin den öffentlichen Netzzugang, denn der Rest der Energie muss eben aus dem Netz kommen. Und natürlich gibt es über diesen Weg auch die Rückkopplung, wieder Energie ins Netz einzuspeisen. Und das wird dann, sage ich mal, ins öffentliche Netz eingespeist und wird dann vertraglicherseits so gehandled, dass wir es an unsere weiteren Companies im Konzern, hier Electrical Steel, vermarkten können, verkaufen können.
Christine Launert: Marcel Hilgers von thyssenkrupp Electrical Steel war ja in der letzten Folge Mein Gast. Gelsenkirchen und Hagen-Hohenlimburg liegen jetzt nicht wirklich in direkter Nachbarschaft. Wie kommt also der überschüssige Strom dorthin?
Thomas Westermann: Der kommt einfach über das öffentliche Netz dahin, und hier gibt es natürlich dann auch wieder Dinge, über die wir uns lange Zeit und viel und intensiv haben unterhalten müssen. Sie müssen natürlich das irgendwie abgrenzen können, und das darf natürlich nicht irgendein ein Gemauschel unter der Hand sein, sondern das muss über Bilanzkreise, die auch dafür zugelassen sind, die das können, im Prinzip gehandled werden. Das heißt, sie haben da noch andere Player im Spiel, und die sind, wie gesagt, teilweise die Netzbetreiber, teilweise dann auch Companies, die sich mit der Mengenbilanzierung und der Mengenvermarktung ganz normal am Markt tummeln. Und die können das dann weiterschieben, können das bilanzieren, und da erfolgen dann auch die Abrechnungen.
Christine Launert: Der Vollständigkeit halber und wenn wir eben mehr Strom benötigen als gerade zur Verfügung steht an Strom...
Thomas Westermann: Dann ziehen wir den einfach aus dem öffentlichen Netz beziehungsweise mischen das zusammen. Das ist also dann die große Mischtrommel.
Milan Nitzschke: Aber das ist ja gerade das Thema, auch in der öffentlichen Debatte: Offensichtlich, wenn wir aus Wind Strom produzieren, und wir haben viel Wind, haben wir viel Strom. Wenn wir keinen Wind haben, haben wir keinen Strom, und dann heißt es immer, na ja, guck mal, da kannst dich gar nicht drauf verlassen. Wer weiß, hast du Strom, hast du keinen Strom, ein Industriewerk kann damit gar nicht arbeiten. Also, wenn wir jetzt nur und alleine die Windkraftanlagen als Energiequelle oder Elektrizitätsquelle für das Werk verwenden würden, dann würde das natürlich nicht klappen. Aber da hilft das öffentliche Netz tatsächlich, um einen Ausgleich zu schaffen. Aber am Anfang, Herr Westermann hat ja gesagt, 40% des gesamten Strombedarfs am Standort wird aus diesen nur 4 Windkraftanlagen gedeckt. So, wir könnten, wenn wir die ganze Strommenge einfach immer in das Werk geben würden, könnten wir auch über 50 % decken. Aber wir haben halt Tage, an denen wir Wind haben, aber nicht produziert wird, oder Tageszeiten, an denen nicht produziert wird, und wir haben eben auf der anderen Seite auch Tage, an denen produziert wird und wir zu wenig Wind haben. Deswegen gibt es halt diese im Vergleich doch relativ geringe Menge, die dann noch hin und her geschoben werden muss. Aber zunächst mal können wir so viel des Stroms, der oben auf dem Berg produziert wird, direkt im Werk unterbringen, und nur die Überschussmenge geht dann eben unter Nutzung des öffentlichen Netzes an den anderen Standort von thyssenkrupp Steel. Was wir jedenfalls von vornherein gesagt haben und auch umgesetzt haben: wir schaffen es, dass keine Kilowattstunde tatsächlich über das öffentliche Netz noch an zusätzliche Verbraucher geleitet werden muss. Also, es gibt nur die direkte Lieferbeziehung zwischen den Windenergieanlagen des Windparks Hohenlimburg und thyssenkrupp. Nur da geht der Strom hin. Jetzt würde ich das natürlich gerne noch auf ganz andere Energieformen übertragen. Sie haben eben gesagt, okay, das, was am Ende wirklich den grünen Stahl ausmacht, ist, wenn dann auch das Direktreduktionsverfahren angewandt werden kann, wenn umgestellt wird von Kokskohle auf Wasserstoff. Da wollen wir auch alle hinkommen, und für mich war das auch total faszinierend, als ich das erste mal ins Werk gekommen bin, hab ich gedacht, meine Güte, das ist ganz schön warm hier, und dann wird der der Ofen geöffnet, und dann sehe ich, das ist wirklich ganz schön heiß, und es glüht auch sehr stark. Machen wir das alles mit unserem Strom? Nee das natürlich nicht, den Teil nicht, die mechanischen Teile, alles, was tatsächlich das Walzen betrifft, nach meinem Verständnis jedenfalls ist das im Wesentlichen alles Strombetrieben. Da kommt der Windstrom rein, aber das Erhitzen der Bramme, die Ankommt, passiert weiterhin durch Gas. Und dieses Gas soll ja dann eben mittelfristig auch ersetzt werden durch Wasserstoff. Aber Wasserstoff ist nur dann grüner Wasserstoff, wenn er auch wieder mit Hilfe CO2-freier Technologien, in dem Fall erneuerbare Energien, beispielsweise Windstrom, erzeugt werden kann. Und das funktioniert natürlich auch, weil wir reden jetzt über 4 Windenergieanlagen, 4 für so ein riesiges Werk. Wir können da natürlich auch 8 hinstellen oder 10 oder 12 oder 40 oder 50 Windkraftanlagen. Die Strommenge muss tatsächlich irgendwann zusammenkommen, um auch den Wasserstoff dann sauber mit grünem Strom herstellen zu können. Aber machbar ist das tatsächlich alles.
Christine Launert: Ja, jetzt gibt es ja viele Quellen für erneuerbare Energie. Es gibt Wind, Wasser, Solar, Geothermie, viele mehr. Warum ist Windenergie so wichtig für die Energiewende und für eine nachhaltige Energiebranche?
Thomas Westermann: Wir haben uns ja damit auch beschäftigt, mit Solarenergie und mit Solar auf Dächern und mit Solarflächenbelegung, und man muss sich einfach nur mal auf der Zunge zergehen lassen, was dahinter steckt. Diese 4 Windräder mit 16 MW Leistung würden theoretisch bedeuten, dass wir, wenn wir auf Solarenergie bauen würden, müssten wir bei, über den Daumen 1 Megawatt pro Hektar ,die gesamte Werksfläche komplett belegen mit Photovoltaik. Und das ist natürlich, wenn man sich das überlegt, eigentlich gar nicht möglich, geht auch nicht, funktioniert auch nicht wirklich. Den Platz brauchen wir für was anderes, und es wird auch nicht funktionieren, es wird auch viel zu teuer.
Milan Nitzschke: Also, die Windenergie ist der Hauptleistungsträger bei der erneuerbaren Energien-Stromerzeugung. Wir haben von nichts so viel wie Wind, und wir haben auch keine andere Technologie, die so platzsparend ist, weil eine Windkraftanlage geht erst mal nach oben, und da dreht sich dann was. Aber unten ist ein sehr geringer Platz, den man für das Fundament benötigt. Da ist noch eine freie Fläche, wo man theoretisch, wenn man das braucht, noch einen Kran hinstellen kann, und alles andere kann im Prinzip so bleiben, wie es ist. Die Windenergieanlagen hier in Hohenlimburg sind ja oben im Wald, und der Wald wird so gut wie gar nicht angetastet dafür. Noch dazu sind wir da auf Kalamitätsflächen, das heißt Flächen, die sowieso schon durch Borkenkäfer oder vorher durch Orkan zerstört sind. Aber wir brauchen kaum Fläche dafür und können dabei ungemein viel Strom produzieren, und wir haben halt nicht das Tag-Nacht Problem, also nachts scheint wirklich wenig Sonne, also kann ich da keinen Solarstrom erzeugen. Trotzdem brauche ich am Ende beide. Wir haben zum Beispiel im Sommer immer etwas weniger Windaufkommen als im Herbst und Winter, im Sommer haben wir aber längere Tage und mehr Sonneneinstrahlung. Da ergänzen sich insgesamt in Deutschland Solar und Wind ganz hervorragend, und da brauchen wir auch beide. Aber wenn ich jetzt, wenn wir gerade über Industrie sprechen, dann ist Wind natürlich die erste Wahl, weil viel stetiger, viel mehr, viel leichter zu erzeugen, viel weniger Platz verbrauchend.
Christine Launert: Also wie im wahren Leben, die Mischung macht's eigentlich. Zu jeder Herausforderung gibt es ja immer mehrere Studien. Die einen, die kommen zu dem Schluss, dass eine Energieversorgung Deutschlands für Strom und Wärme mit 100 % erneuerbaren Energien möglich ist, und andere schränken wieder ein, dass das für uns als Industrieland eben niemals zu 100 % möglich sein wird. Auf dem Weg zu den hypothetischen 100 %: Welche Trends beobachten sie denn, und welche Entwicklung würden sie sich denn wünschen?
Milan Nitzschke: Also zuerst mal muss ich sagen, natürlich geht das, aber, wenn ich rumfrage, wahrscheinlich auch in diesem Raum, oder wir gehen einfach auf die Straße. Wer glaubt denn daran, dass das funktioniert? Ja, schwierig, wäre ja schön, aber wahrscheinlich doch nicht.
Christine Launert: Aber so sind wir Deutschen, ne?
Milan Nitzschke: So sind wir Deutschen, und so agiert aber auch teilweise die Politik. Auch unter Journalistinnen, Journalisten ist es sehr weit verbreitet zu sagen, ja wäre ja schön, es gibt ja Ziele, aber ob wir die jemals erreichen? Man muss es sich nur einmal vergegenwärtigen. Wir haben bereits einen Beschluss der Bundesregierung. Der wird auch umgesetzt, dass 2 % der Landesfläche, nicht mehr, nur 2 % der Landesfläche, für Windenergie zur Verfügung gestellt werden. Auf diesen 2 % der Landesfläche kann ich so viele Windenergieanlagen bauen, von modernster Bauart, mit der entsprechenden Höhe, mit ganz viel Windausbeute, dass ich deutlich mehr Strom erzeugen kann, als heute in Deutschland verbraucht wird. Ich habe einen Verbrauch von gut 500 Milliarden Kilowattstunden, und ich kann damit 700 plus x Milliarden Kilowattstunden nur Windstrom an Land erzeugen, nur mit dem, was heute schon Beschlusslage ist, dass diese Fläche dafür genutzt wird. Gerne können wir darüber hinausgehen, aber ich würde sagen, fürs erste reicht das mal. Und dann habe ich die Möglichkeit, Offshore vor der Küste Windstrom zu erzeugen. Ich habe Solar, wir haben noch die anderen Energieträger: Bioenergie, Wasserkraft und sofort. Das heißt, ich kann alleine in Deutschland ungefähr 1.500 -1.600, vielleicht auch mehr Milliarden Kilowattstunden Strom erzeugen. Das ist viel mehr Strom, als wir heute brauchen, und gleichzeitig wissen wir, wir gehen ja dahin. Warum machen wir das? Weil es ebenfalls eine Systementscheidung gibt, das zukünftig nahezu alles über Strom abgewickelt wird. Heute verbrennen wir Gas, Kohle, Öl, und zukünftig wollen wir mit Strom heizen, wir wollen mit Strom Autofahren, tun das auch schon, also jedenfalls bin ich mit dem Elektroauto hergekommen, hat prima geklappt, und sie wollen für ihre Produktion Kokskohle durch Wasserstoff ersetzen, der wiederum mit Strom produziert wird. Das heißt, wir werden auch wirklich so einen Stromverbrauch haben, und dann passt es alles wieder zusammen. Also das das Szenario, von dem ich jetzt spreche, das wird irgendwann in 2040 Plus X erreicht sein, und auf dem Weg dahin kommen wir schnell auf die 80 %, und dann geht das so weiter. Und jetzt haben manche vielleicht noch die Sorge, Ohgott Ohgott, wie sieht denn das aus, wenn wir das alles mit Windstrom machen? Wir brauchen dafür über den Daumen 40.000 Windenergieanlagen in Deutschland, um diese fast Hälfte des kompletten Stromverbrauchs, zukünftigen riesigen Stromverbrauchs, nur mit Windenergie zu decken? 40.000 klingt auch wieder viel. Dann kommt die Frage, wie viel haben wir denn heute? 30.000. Es ist nicht viel mehr, die sind größer, die müssen ein bisschen weiter voneinander weg stehen. Deswegen brauchen wir die Fläche, aber die laufen auch viel stetiger, ein viel ruhigeres Gesamtbild. Also, es ist einfach keine Belastung für die Allgemeinheit, für wen auch immer, die man tatsächlich ernsthaft diskutieren kann, wenn man auf der anderen Seite sieht, was wir uns durch Klimawandel, durch Ressourcenverbrauch und so weiter alles schon eingehandelt haben. Es ist ein ganz kleiner Schritt, mit dem wir die 100 % erneuerbare Energien-Stromversorgung in Deutschland hinbekommen können. Wir können auch was importieren. Alles Okay, aber den Großteil werden wir selber machen.
Christine Launert: Herr Nitzschke, Sie sind jetzt in Leitungsorganen sowohl des Bundesverbandes für erneuerbare Energien sowie der Windenergie. Ich habe über sie gelesen, dass sie sich auch deshalb engagieren, um das ganze politische Gewicht der Branche in Berlin, Brüssel und den Ländern einzusetzen. Warum ist es so wichtig, dass sich die Branche organisiert? Erneuerbare Energien erleben doch gerade ihren Aufschwung.
Milan Nitzschke: Ja, immer wenn es einen Aufschwung gibt, dann geht es am Ende auch um Marktanteile. Die Erneuerbaren gewinnen Marktanteile, andere verlieren Marktanteile. Das sind zum Beispiel diejenigen, die aktuell Erdgas verkaufen, auch Flüssiggas verkaufen aus unterschiedlichen internationalen Quellen, und die finden das jetzt gar nicht so toll, dass das alles so schnell geht, und deswegen gibt's auch immer wieder Steine, die einem in den Weg gelegt werden. Also, ohne klare politische Rahmenbedingungen kann in dieses Riesenprojekt Energiewende nicht ausreichend investiert werden. Und was wir halt auch haben, sie sehen ja hier am Tisch einerseits europäische Großindustrie und auf der anderen Seite kleinen regionalen Mittelstand. Sie brauchen aber für den Ausbau der erneuerbaren Energien, der ja maximal dezentral, regional stattfindet, brauchen sie ganz viele kleine mittelständische Player, die das machen. Die sind, zeigt sich ja auch jetzt, viel schneller, viel flexibler, viel durchsetzungsstärker auch als die großen Schiffe, die wir aus der Vergangenheit in der Energieversorgung kennen. Und die allerdings können nicht investieren, wenn sie nicht einen festen Rahmen haben, unter dem sie kalkulieren können, wo ihnen dann auch eine entsprechende Bank das Fremdkapital zur Verfügung stellt. All diese Investitionen, nehmen sie an, ein Windrad kostet 10 Millionen Euro, davon zahlt etwa 9 Millionen Euro die Bank. Das tut sie nicht, wenn sie nicht eine Sicherheit hat. Eine Sicherheit in einem solchen System, in einem so volatilen System, wie dem Deutschen / Europäischen Energiemarkt, kriegen sie nur hin mit geeigneten politischen Rahmenbedingungen. Und immer wenn sie hören, dass so eine Rahmenbedingung abgeschafft werden soll, müssen sie ein bisschen bösgläubig vermuten, das ist wo jemand, der das mit den erneuerbaren Energien nicht so toll findet. Weil, wenn der Rahmen fällt, ist die Sicherheit weg, können sie nicht investieren. Wenn der Rahmen steht, können sie investieren, und das machen wir jetzt seit Jahren, und allein unser nicht sehr großes Unternehmen baut in den nächsten 3 Jahren 100 Windenergieanlagen. Wenn sie es über den Daumen nehmen, dann ist das eine Investition von ungefähr 1 Milliarde Euro. Die können wir nur wuppen, wenn der Rahmen da ist, wenn die Sicherheit gegeben ist, und dann machen wir das aber auch.
Christine Launert: Nicht ganz unwichtig in diesem Zusammenhang ist ja auch, dass die Energie mit erneuerbaren Quellen auch bezahlbar sein muss und international wettbewerbsfähig sein muss. Haben wir das schon, sind wir auf einem guten Weg?
Milan Nitzschke: Also offensichtlich sind die Stromerzeugungskosten so, dass wir beide jedenfalls zusammenkommen konnten. Und jetzt ist es vielleicht nicht der Traumpreis, den sich thyssenkrupp immer gewünscht hat. Da sind ja auch Zahlen im Zuge der Industriestrompreisdebatte genannt worden. Aber es hat hier den Vorteil, dadurch, dass wir eine Direktleitung haben, der weit überwiegende Teil der Strommenge nicht durchs öffentliche Netz muss, fallen an der Stelle auch keine Netzentgelte an, und dann rechnet es sich. Das muss man auch machen, um der Industrie eine Möglichkeit zu geben, bezahlbaren Strom zu haben. Also, wir sind offensichtlich aber schon sehr nah dran, dass das alles wettbewerbsfähig ist. Wenn ich jetzt subventionierten Atomstrom in Frankreich nehme, muss man sich vergegenwärtigen, dass keines der Unternehmen dort, die den Atomstrom herstellt oder die Kraftwerke baut, noch privat ist. Die sind alle verstaatlicht worden, weil ansonsten es wirtschaftlich nicht mehr leistbar gewesen wäre. Also da stecken irre viele Subventionen drin. Da gibt es einen Preisdeckel, über den man den Preis nicht gehen lassen darf und so weiter. Wenn wir uns damit vergleichen, können wir sagen, das ist noch ein bisschen billiger, aber selbst da sind wir fast dran. Windstrom, auch die anderen Erneuerbaren sind am Ende die billigsten Energiequellen, die wir haben. Was heute die Sache noch ein bisschen teuer macht, ich habe eben von Unsicherheiten und Sicherheiten gesprochen, wir brauchen, um so ein Projekt zu entwickeln, teilweise über 10 Jahre. Dieses Projekt in Hohenlimburg hat, bis wir überhaupt angeklopft haben und gesagt haben, wollen wir nicht was zusammen machen hier, wollt ihr den Strom nicht haben? Haben wir schon 10 Jahre Vorlaufzeiten gehabt, Rangeleien mit der Gemeinde, mit der Landespolitik, mit der Bundespolitik, bis wir es endlich so weit hatten, dass wir eine BImSchG-Genehmigung hatten, für die Errichtung der Anlagen, und bauen konnten. Das kostet natürlich auch Geld. Erst mal gibt es immer das Ausfallrisiko, das wird nix, das Projekt wird eingestampft, dann haben sie alles umsonst investiert, müssen sie einkalkulieren, und auf der anderen Seite die ganzen Kosten bis dahin ebenfalls. Wenn wir uns das mal sparen könnten, wenn das alles schneller, dynamischer, effektiver gehen würde, wir schneller die Genehmigungen erlangen würden, auch ein klares PRE da wäre, du willst eine Windkraftanlage bauen? Ja, die brauchen wir! Wir machen das möglich, dass die gebaut werden kann und wir nicht lange dafür kämpfen müssen, dann können wir den Strom auch noch 30, 40 % billiger anbieten.
Christine Launert: Ja, und, Herr Westermann, Geschwindigkeit und bezahlbarer Strom sind ja für uns jetzt auch keine unwichtigen Themen.
Thomas Westermann: Das ist auf jeden Fall ein Faktor, den wir immer wieder ins Kalkül ziehen müssen, auch vor dem Hintergrund, wenn wir aus dem Strom, aus dem grünen Strom zukünftig auch mal das machen wollen, was wir noch brauchen. Das ist ja in Hohenlimburg auch der Fall. 20 % brauchen wir Strom, 80 % brauchen wir Gas, und wir sind ja auch an der einen oder anderen Stelle da technologisch, sag ich mal, durchaus auf Hybridlösungen aus, wo wir vielleicht auch mal den Stahl erwärmen können, mit anderen oder mit elektrischen Mitteln. Aber wir werden die letzte Meile auch bei der Erwärmung immer noch mit Gas machen wollen, weil es einfach technologisch zu unserem Produkt besser passt und es auch am Ende des Tages vernünftig ist und technologisch nur so geht. Und da sind sicherlich Dinge, die wir noch weit, weit in der Zukunft weiter treiben müssen oder auch in der nahen Zukunft schon weitertreiben müssen. Was passiert mit überschüssigem Grünstrom? Macht es nicht Sinn, sich auch mal Gedanken darüber zu machen, vor Ort, sage ich mal, auch regional Elektrolyseanlagen zu bauen, um das gleich wieder ins Werksnetz einzuspeisen, um dann, sag ich mal, auch den Erdgasanteil zu drücken und mit Wasserstoff aufzupimpen? Dann hätten wir natürlich Effekte auch bei dem grünen Stahl, der weit über diese 11%, die ich vorhin genannt habe, hinausgehen und das Produkt noch wesentlich grüner machen könnten. All das sind natürlich Dinge, da brauchen wir Rahmenbedingungen, da brauchen wir allerdings auch niedrigere Kosten. Da brauchen wir auch den Erfinder und den Kreis, sag ich mal, der Leute, die sagen, wir machen das jetzt einfach mal, wir gucken uns das mal an. Und da muss ich ganz ehrlich immer zu sagen, wir sind natürlich von der Größe her so ein Werk, wo man sowas gut machen kann, wo man sowas gut ausprobieren kann, weil wir eben nicht so ein Riesen Industriebetrieb sind. Aber schon ein Industriebetrieb, der nicht vergleichbar ist mit so einem Mittelständler, der natürlich so eine Direkteinspeisung irgendwo nicht nutzen kann, der muss aus dem öffentlichen Netz den grünen Strom ziehen. Aber wir können sicherlich da Vorreiter sein für diverse Ausbaustufen, die die grüne Transformation noch weiter nach vorne bringen und noch weiter pushen.
Christine Launert: Ja, also, das Ende ist lange nicht erreicht. Das Projekt ist jetzt erst mal erfolgreich abgeschlossen, aber es gibt noch viele Möglichkeiten, daran anzuschließen. Sie hatten es vorhin angesprochen. Sie hatten eigentlich gehofft, dass es für so etwas schon eine Blaupause gibt. Kann denn dieses Projekt eine Blaupause sein, wie Industrie und Energieerzeuger viel direkter Zusammenkommen, ohne das jetzige System natürlich auszuhebeln?
Milan Nitzschke: Ja, das ist schon eine Blaupause, also ich bekomme regelmäßig Anrufe und E-Mails: Wie habt ihr das gemacht? Wie können wir das auch machen? Ich hoffe auch, dass wir in der Verbindung thyssenkrupp Steel und SL vielleicht auch nochmal was zusätzlich mit auf den Weg bringen können. Ehrlich gesagt, wenn ich hier aus dem Fenster gucke und Duisburg sehe, und da ist so viel Platz, da könnte man doch eine Windkraftanlage hinstellen. Also, da gibt es noch viele Möglichkeiten, glaube ich. Aber wir haben jetzt die ganze Energie da reingesteckt und die Zeit da reingesteckt, um unser Projekt hinzukriegen, aber natürlich auch, um für andere ein bisschen den Weg zu ebnen, dass es einfacher wird. Gleichzeitig ist aber auch eine klare Schlussfolgerung, alles kann man nicht so einfacher machen. Da muss die Politik auch was tun. Was wir gefordert haben, ist ein Windenergie-Industriestrom-Pakt, das heißt, da ist jetzt ist auch mal die Landesregierung am Zug. Ich habe das auch so verstanden, dass die Wirtschaftsministerin, die bei der Einweihung der Direktleitung auch anwesend war, das mit eröffnet hat, dass sie sich dafür auch einsetzen will. Auf Bundesebene führt man dazu auch Gespräche. Wir müssen es hinkriegen, dass die Regularien, die heute noch stören, die aus einer ganz anderen Zeit kommen, wo keiner an sowas gedacht hätte, dass die dann auch fallen und sagen, okay, wir machen das jetzt einfacher. Ein Beispiel ist, sowie im Erneuerbaren Energien-Gesetz als auch im Energiewirtschaftsgesetz ist die Rede davon, dass man solche Direktleitungen nur bei unmittelbarer räumlicher Nähe als solche behandeln kann. Ja, wie soll ich denn einen Windpark in unmittelbare räumliche Nähe, quasi 1,50m vom Werk weg bauen? Das geht ja gar nicht. Wenn ich das aber ermöglichen will, dann muss ich halt viel mehr Luft lassen an der Stelle. Und dann hat das Energiewirtschaftsgesetz jetzt eine neue Regelung eingeführt, die ist nicht ganz zutreffend auf unseren Fall, aber da wird das erste Mal gesagt, ja, das ist eine Direktleitung, kann als solche behandelt werden, wenn es maximal fünf Kilometer Kabellänge sind. Aber wo kommt denn die Zahl jetzt wieder her? Macht auch keinen Sinn. Also, wenn wir investieren in ein Kabel, das vom Windpark zum Werk geht, da werden wir schon keine 20 Kilometer bauen, das ist nämlich viel zu teuer. Das heißt, man bleibt eh in der Größenordnung, irgendwie drei, vier, fünf, sechs, sieben, acht Kilometer oder sowas. Aber solange es sich wirtschaftlich darstellen lässt, muss man es doch machen. Wir entlasten ja dadurch auch graduell das Netz, also zumindest führen wir, auch wenn wir weiterhin Netzausbau brauchen, weiterhin Netzanschluss brauchen, müssen wir auf Nummer sicher gehen. Auch thyssenkrupp muss sicher sein, dass, wenn kein Wind weht, sie weiter Strom kriegen können. Aber wir belasten ja trotzdem zu der Zeit, wo der Strom von uns direkt im Werk abgenommen wird, graduell weniger das Netz, und es ist eine direkte Unterstützung auch für einen Industriestandort, den wir ja erhalten wollen, und daher muss es einen politischen Willen geben, dann auch mal ein paar bürokratische Hemmnisse einfach abzubauen, damit es für andere leichter wird.
Thomas Westermann: Also, ich kann das an der Stelle eigentlich nur wiederholen, aber auch nochmal erhärten. Ich kriege pausenlos jetzt Anrufe von Firmen, die sagen, wie habt ihr das gemacht, dürfen wir mal darüber sprechen? Klar dürfen wir darüber sprechen, wir sprechen gerne darüber, und da stellt man jedes Mal fest, die kämpfen ja genauso wieder an denselben Stellen, wo wir auch gekämpft haben, also wieder das gleiche, es geht wieder los, und ich glaube, da muss einfach an der Stelle das einfach viel einfacher gehen, viel gradliniger gehen, und da sind wir gerne bereit, wie gesagt, auch dem einen oder anderen, ich sag mal, jetzt nicht die Geheimnisse des Vertrages, aber das zu erklären, was wir gemacht haben, wie wir es gemacht haben, und ich glaube, da sind wir beide dann auch in demselben Ruderboot unterwegs und ziehen an derselben Pinne.
Christine Launert: Die Energiewende ist keine leere Worthülse. Sie ist bereits in vollem Gange. Mit Menschen, die sich unermüdlich dafür einsetzen, Menschen der Next Generation Steel. Vielen Dank an meine Gäste für den interessanten Austausch, danke euch fürs Zuhören. Ich hoffe, es hat euch gefallen. Falls ja, abonniert "gekocht, gewalzt, veredelt" gerne auf den bekannten Podcast Plattformen und lasst uns gerne auch Feedback da, zum Beispiel via Mail an [email protected]. Ich freue mich auf weitere spannende Stahlthemen mit euch.
Bisherige Podcast-Folgen
Folge 12: Elektroband treibt Transformation voran – Energiewende gemeinsam gestalten
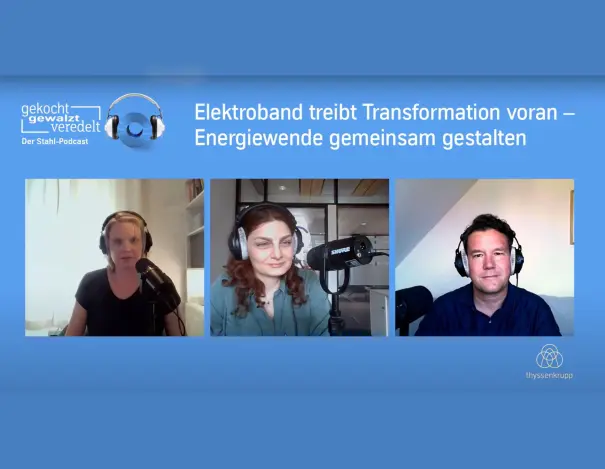
In dieser Episode von "gekocht, gewalzt, veredelt" spricht Christine Launert mit Christina Iosifidou von Siemens Energy und Marcel Hilgers von thyssenkrupp Electrical Steel. Die Experten diskutieren, wie nachhaltige Stahlproduktion und effiziente Netztechnik Hand in Hand gehen und entscheidend zur Dekarbonisierung von Lieferketten beitragen. Wir schauen auf die enge Zusammenarbeit zwischen Stahlproduzent, Elektro- und Energietechnikhersteller sowie Übertragungsnetzbetreiber und ihren gemeinsamen Weg in eine nachhaltige Zukunft.
Christine Launert: Liebe Zuhörerinnen, liebe Zuhörer, willkommen zu einer neuen Folge von gekocht, gewalzt, veredelt, dem Podcast rund um das Thema Stahl. In dieser Folge spreche ich mit unseren Gästen über die Energiewende. Warum diese Aufregung um das Thema? Was bedeutet diese Wende überhaupt für uns? Und was hat das Ganze mit Stahl zu tun? Ich möchte mit meinen Gästen heute vor allem darüber sprechen, was sich außer der Energieträger selbst noch wandeln muss, damit die Energiewende gelingt. Und noch etwas macht diese Folge besonders spannend: Ihr könnt uns zum ersten Mal auch sehen. Ich stelle euch heute zwei Gäste vor, die sich nicht nur damit beschäftigen, wie sich Transformation und Business miteinander vereinbaren lassen, sondern auch damit, was die Zusammenarbeit in der Lieferkette zur Transformation beitragen kann. Christina Iosifidou von Siemenens Energy, schön, dass du da bist. Und Marcel Hilgers von thyssenkrupp Electrical Steel. Danke auch dir, dass du mein Gast heute bist. Mein Name ist Christine Launert, ich bin Pressesprecherin bei thyssenkrupp Steel. Schön, dass ihr dabei seid.
Christine Launert: Marcel, du leitest bei thyssenkrupp Elektrikal Steel den Vertrieb und den technischen Kundendienst für Elektroband. Wofür braucht man Elektroband überhaupt, und wem verkaufst du es?
Marcel Hilgers: Vielen Dank erst mal für die Teilnahmemöglichkeit hier am Podcast. Ganz spannendes Thema für mich, und ich freue mich auch, gemeinsam mit Christina hier zu diesen ganz spannenden Thema Elektroband und Relevanz für die Energiewende ja hier zu sprechen. Also zu deiner Frage: Elektroband, was ist das eigentlich? Kornorientiertes Elektroband ist ein absolutes Nischenprodukt. 0,2 % der gesamten Weltstahlerzeugung, nur darum geht es heute hier. Aber dafür ist es ein ganz, ganz relevantes Thema, denn ich fasse es mal so zusammen: In jedem Transformator, der Strom von einem Spannungslevel auf ein anderes überträgt, steckt kornorientiertes Elektroband drin. Das heißt, alle Geräte, die jetzt gerade verbunden sind, um diesen Podcast hier abzuhören, die haben irgendwo am Stromkabel auch ein Transformator, und darum geht es hier. Gerade bei dem Thema Elektrifizierung und Energiewende spielen wir also eine ganz wichtige und zentrale Rolle.
Christine Launert:Christina, Du leitest das Nachhaltigkeitsmanagement Netztechnik bei Siemens Energy. Erklärst du uns kurz, was das genau heißt?
Christina Iosifidou: Ja, sehr gerne und Hallo auch von meiner Seite an die Zuhörer, und zwar bei Siemens Energy, nehmen wir unsere Verantwortung für das Thema Nachhaltigkeit sehr ernst, und wir haben eine Organisation, in der Nachhaltigkeit sowohl auf höchster Ebene Chefsache zum einen ist, im Corporate Team und auf der anderen Seite auch in den verschiedenen Geschäftsbereichen, wie zum Beispiel der Netztechnik eine entscheidende Rolle spielt und auch vertreten ist. Hier befindet sich mein Team. Gemeinsam mit meinem Team gehen wir eben alle Themen an, die den ökologischen Fußabdruck unserer Produkte verbessern, und dabei schauen wir uns eben die gesamte Netztechnik an. Es geht um die Transformatoren, wie Marcel schon vorher erwähnt hat, Schaltanlagen und die gesamten Lösungen, die wir eben ins Feld stellen für die Energiewende.
Christine Launert: Zwei Menschen also, die sich ihrer beruflichen Aufgabe mit ganzem Herzen widmen, und da können wir sehen, Energiewende und Stahl passen hervorragend zusammen. Aber warum ist Stahl überhaupt wichtig für die Energiewende? Marcel, du hast es gerade schon angesprochen. Kannst du das nochmal ganz genau auf den Punkt bringen? Warum ist Stahl wichtig für die Energiewende?
Marcel Hilgers: Ja, wenn wir uns anschauen, worum es bei der Energiewende geht, wir reden ja dann über Elektrifizierung, das heißt, wir wollen weg von fossilen Brennstoffen, wir wollen erneuerbare Energien ins Netz bringen, und da fällt auch schon das Stichwort. Wir brauchen also viel Netz, viele Stromnetze, und Stromnetze, das hat jeder vor Augen, das sind die Strommasten, das sind Leitungen, aber das sind halt auch zum Beispiel die ganzen Transformatoren, die dort benötigt werden, um die erneuerbaren Energien zum Beispiel von der Nordsee nach Süddeutschland zu bringen und so weiter. Überall ist Stahl drin, dran, drum. Es wird viel Stahl gebraucht, und vor allen Dingen, es wird sehr, sehr guter Stahl gebraucht. Zum Beispiel die besten Kernbleche, um Transformatoren so effizient wie möglich zu machen und damit auch Energieverluste zu vermeiden. Darum geht es dann auch ganz besonders.
Christine Launert: Und warum, mal abseits von von euren Produkten selbst? Warum liegt euch die Energiewende überhaupt am Herzen?
Christina Iosifidou: Oh da muss ich gleich einsteigen, darf ich? Also, Marcel hat das ja eigentlich schon gesagt, Stahl und die Bedeutung. Ich möchte aber wirklich ergänzen und sagen, warum machen wir eigentlich das ganze, und was bedeutet Energiewende? Energiewende ist nichts anderes als die Dekarbonisierung der Energieerzeugung und -nutzung. Und warum machen wir das? Weil, und das sehen wir auch jetzt schon, der Klimawandel vor der Tür steht, die. Die tragischen Folgen des Klimawandels begegnen uns schon heute, und wir müssen es, wir alle müssen es zu unserer Verantwortung machen, die Treibhausgasemissionen zu reduzieren. Das ist der Haupthebel, um dem ganzen zu begegnen. Die Energienutzung weltweit ist für über 70 % der Emissionen verantwortlich. Das heißt, wir sind jetzt hier im Kern des Geschehens. Wir müssen handeln. Und, was besonders wichtig ist bei dem ganzen: Wir als Netztechnik auch oder auch Siemens Energy, in Gänze, natürlich haben wir die Netztechnik und stellen sie zur Verfügung, um die Übertragung sicherzustellen und auch die erneuerbaren Energien zu integrieren. Aber das reicht natürlich nicht. Wir müssen auch sicherstellen, dass alle diese Produkte, die wir für 35, 40 Jahre ins Feld stellen, nachhaltig sind, grüner sind. Und genau dafür brauche ich auch die Stahlindustrie, die Kupferindustrie und viele weitere, die den Weg mit uns beschreitet. Und letztendlich, wenn wir noch einen Schritt weiterdenken, dann kann Dekabonisierung sowohl in der Energieindustrie als auch in der Industrie selbst, wie zum Beispiel der Stahlindustrie oder auch der Mobilität nur stattfinden, wenn wir alle das Netz so weit ausbauen, dass es eben diesen Mehrbedarf an Strom, und dann auch grünen Strom, decken kann.
Marcel Hilgers: Ja Christine, du hast gefragt, was mir persönlich auch am Thema Energiewende am Herzen liegt, und ja, mein Beispiel dazu, oder was ich dazu denke. Ich hab vor vor einem Jahr, glaube ich, bei einer Konferenz zum Thema Nachhaltigkeit in unserer Branche damit gestartet, die Frage gestellt, warum wir das überhaupt machen. Warum treffen wir uns hier dazu? Und ich habe ein Bild von meinem Sohn gezeigt. Der ist jetzt gerade vier Jahre alt, und ich mache das schon aus dem Grund, dass ich denke, ich habe die Möglichkeit, hier Sachen auch in die richtige Richtung zu bringen, gemeinsam mit Christina von Siemens Energy, gemeinsam mit dem Team von thyssenkrupp Electrical Steel, thyssenkrupp Steel und so weiter. Und da haben wir eine Verantwortung. Und was ich auch immer schön finde, ist dieser Begriff der Enkelfähigkeit, dass sich jeder für seine Handlung, egal ob geschäftlich oder privat, schon überlegen muss, ob das, was er jetzt gerade dort entscheidet oder macht, auch quasi von seinen Enkeln so unterstützt oder erlaubt werden würde. Christina hat das gesagt, die Transformatoren, das Netzequipment, die gehen jetzt für die nächsten 35, 40 Jahre ins Netz. Das heißt, wir müssen jetzt schon wirklich entscheiden, ob das, was wir da ins Netz bringen, auch wirklich nachhaltig ist.
Christine Launert: Das erklärt es einfach, warum nicht nur zwei Unternehmen wie Siemens Energy und thyssenkrupp zusammenarbeiten, sondern warum ihr auch als Teams zusammenarbeitet, es ist einfach eine Herzensangelegenheit. Und gemeinsam verbessert ihr mit euren Produkten die Effizienz von Transformatoren. Ihr habt es gerade schon angedeutet. Was müssen sich die Zuhörerinnen und Zuhörer darunter vorstellen - Die Effizienz von Transformatoren?
Christina Iosifidou: Wozu sind denn Transformatoren überhaupt da? Transformatoren sind dazu da, um die Spannung zu wandeln, zu transformieren, um dadurch den Strom über längere Distanzen effizient, also mit geringen Verlusten, zu transportieren.
Christine Launert: Du sprichst von Trassen, das heißt von der Stromgewinnung bis zum Verbraucher.
Christina Iosifidou: Genau, weil am Ende die Netztechnik, wozu ist sie da? Um den erzeugten Strom, egal ob im Süden Deutschlands oder Norden, zum Endverbraucher zu transportieren.
Christine Launert: Es geht um die Dekarbonisierung. Wir müssten dahin unsere Hörer vielleicht nochmal ganz kurz abholen. Marcel, was übernimmt denn thyssenkrupp Steel zum Beispiel, um den CO2-Fußabdruck der Stahlproduktion zu reduzieren? Kannst du das in wenigen Sätzen einmal erläutern?
Marcel Hilgers: Ja klar, gerne. Also erst mal muss allen bewusst sein, dass die Stahlerzeugung ein massiver CO2-Emittent ist. Wir sind ja alleine als Unternehmen thyssenkrupp Steel dafür verantwortlich, 2,5 % der deutschen CO2-Emissionen zu verursachen. Das ist natürlich viel, und daran müssen wir arbeiten, und das tun wir. 85 % dieser ca. 20 Millionen Tonnen CO2 werden im Hochofenprozess erzeugt, und das heißt, da müssen wir als erstes Mal ansetzen. Im Hochofenprozess geht es darum, aus Eisenerz das Eisen herauszubekommen. Das machen wir klassisch im Hochofen, indem wir Koks-Kohle dazugeben, und wenn dann aus dem Eisenerz der Sauerstoff zusammenkommt mit der Koks-Kohle, dann entsteht nun mal in einem chemischen Prozess in dem Reduktionsprozess CO2, und zwar sehr, sehr viel CO2. Deswegen ist unser Ansatz, dass wir die Koks-Kohle in Zukunft durch Wasserstoff ersetzen, denn wenn Wasserstoff auf den Sauerstoff trifft, der im Eisenerz enthalten ist, dann haben wir ein H2O letztendlich, also Wasserdampf, der dort rauskommt, und dadurch können wir massiv viel CO2 einsparen, damit die gleichen Produkte, das gleiche Eisen, die gleichen Stahlprodukte, die am Ende dort herauskommen, produzieren, aber extrem viel CO2 vermieden haben.
Christine Launert: Wie beeinflusst denn die Produktion aller die Nachhaltigkeit der gesamten Lieferkette? Machen die Anstrengungen eines einzelnen Unternehmens überhaupt Sinn?
Christina Iosifidou: Jemand muss ja anfangen, das mal vorne weg, und ich glaube, was wir jetzt auch erleben, gemeinsam auch mit Marcel, ist, dass immer mehr aufsteigen auf diesen Zug und verstehen, was wir vielleicht vor, auch vor eineinhalb, zwei Jahren erklärt haben, und das ist schön zu sehen. Und es ist wichtig, und das erkläre ich auch immer intern meinen Leuten zu verstehen, wo wir Impact erzeugen können, und uns dafür auch einzusetzen, auch nach außen hin. Zum Beispiel für uns als Technologys Netztechnik in der Siemens Energy. Wir haben hocheffiziente Produkte heute schon, und das ist Teil unseres DNAs. Wir arbeiten immer daran, besser zu werden, und das wird sich nicht ändern. Also, Produkteffizienz ist uns super wichtig, genauso natürlich wie Produktqualität und Produktsicherheit und Verlässlichkeit. Aber worauf wir halt mehr und mehr schauen müssen im Sinne der Nachhaltigkeit, ist eben, was können wir in der Lieferkette tun? Als Siemens Energy können wir eben wirklich Einfluss nehmen auf unsere Lieferkette, und wir haben nun mal eine riesen Menge an Lieferanten, und das ist eben, was ich so wichtig finde und wofür ich mich einsetze, gemeinsam auch mit Marcel, um da eben die Transparenz zu schaffen und auch die Bedeutung des Themas immer präsenter zu machen.
Marcel Hilgers: Und das schafft ihr ja auch bei uns. Das heißt, ihr seid ja ein ganz, ganz wichtiger Kunde von uns, aber auch ein ganz massiv wichtiger Antreiber zum Thema Dekarbonisierung. Antreiber in dem Sinne, dass ihr uns ja auch challenged, wie wir Dekarbonisierungsbemühungen definieren, was wir anbieten, gemeinsam Erklärungen, Erläuterungen an eure Kunden auch, all das ergibt sich ja aus dieser, ja aus dieser, auch Pionierarbeit, die wir irgendwo leisten. Das ist auch manchmal Trial and Error, und wir sind ja auch nicht immer erfolgreich bei dem, was wir dort machen, aber wir merken, dass wir immer weiterkommen halt.
Christina Iosifidou: Ja, du hast es auch so schön gesagt, Trial and Error, ich meine wir, wir versuchen ja wirklich auf verschiedenste Weise, unsere Lieferanten, natürlich auch, aber unsere Kunden vornehmlich zu erreichen, und wir haben ja schon vieles getan in der Vergangenheit. Ich meine, eins der Themen, die besonders gut auch ankamen und auch wirklich für Verständnis gesorgt hat, war eben die Veranstaltung bei euch im Stahlwerk in Duisburg, wo wirklich unsere Kunden mit großem Interesse teilgenommen haben, um zu verstehen, wie grau oder grün ein Stahlwerk tatsächlich ist und welche Dimension dahinter steckt, um zu verstehen auch, warum so viel Geld, so hohe Investitionen benötigt werden, um ein Stahlwerk zu transformieren, und ich denke, das war wirklich hilfreich. Weil unsere Kunden können sich natürlich vorstellen, wie ein Transformator aussieht und wie eine Produktion eines Transformators gestaltet ist und wie diese vielleicht grüner werden kann. Aber sie können sich nicht vorstellen, wie es bei einem Stahlwerk aussieht. Und das war, glaube ich, nochmal so ein Augenöffner und ein Event, dass wir, ich glaube erstmalig, gemacht haben, tatsächlich, um rein über das Thema Nachhaltigkeit zu sprechen und Transformation.
Marcel Hilgers: Ja, in der Tat, es war ein ganz, ganz tolles Event, auch für uns das erste Mal, dass wir sowas gemacht haben. Unser direkter Kunde, Siemens Energy, ihr bringt eure Kunden mit, die wichtigsten Übertragungsnetzbetreiber und Verteilnetzbetreiber, um ja auch zu informieren. Es hat ja keinen Werbecharakter oder sonstiges, sondern es geht wirklich um Information, um dieses Thema Nachhaltigkeit im Übertragungsnetz, im Stromnetz irgendwo voranzutreiben. Und, da waren viele erste Ereignisse bei, wie zum Beispiel mit eurem Vertriebsleiter hatten wir einen sogenannten Expertentisch, in dem wir dann eure Kunden gemeinsam auch transparent über die Mehrkosten informiert haben. An dem Punkt sind wir ja auch schon angekommen. Wir wollen alle dekarbonisieren, das ist mit Kosten verbunden. Machen wir da jetzt quasi noch ein extra Benefit, oder machen wir das ganze wirklich transparent, um dieses Thema Dekarbonisierung, Nachhaltigkeit nach vorne zu treiben? Und ich glaube, diese Transparenz, die wir da gemeinsam erzeugen, schafft dann auch vertrauen, dass es sich hier nicht um einen Marketing Gag handelt, sondern wirklich um die Bestrebung, das richtige zu tun.
Christina Iosifidou: Ja, definitiv, und ich glaube, was mir auch bei dem ganzen sehr wichtig war, ist eben, dass wir nicht nur die Übermittler spielen, sondern dass unsere Kunden alles live selber miterleben und sich auch erkundigen können in genaueren Fragen, was steckt dahinter? Und das ist der einzige Weg, eben Transparenz zu schaffen, den wir heute haben, weil alles ist relativ ungewiss und unklar und dynamisch, wie ich schon vorher gesagt habe, und ich fand es auch sehr gut, dass auch die Politik dabei war, das BMWK, und auch nochmal an uns appelliert hat, dass wir ja, die hier alle zusammensitzen, genau die richtigen sind, um das Thema Verwendung von grünerem Elektroblech in Transformatoren wirtschaftlich zu gestalten. Nur wir, die Wirtschaft selbst, kann das gestalten oder kann verstehen, wie es am effektivsten, am besten eben laufen könnte, und ich denke, dass wir uns hier auch zusammenschließen und daran arbeiten müssen. Und wir haben das auch schon mit Marcel, also thyssenkrupp und Siemens Energy arbeiten schon daran, wie wir das Thema in unserer Industrie adressieren können und auch andere Partner dafür begeistern können, mitzumachen.
Christine Launert: Das heißt einmal noch, um unsere Zuhörerinnen und Zuhörer abzuholen, es gab einen Workshop, der wirklich die gesamte Lieferkette einmal eingeladen hat und einmal zusammengebracht hat und nicht immer nur den Fokus zwischen zwei Parteien in den Mittelpunkt gerückt hat, und euer Resumèe konnten wir jetzt alle hören. Das war sehr gut, und ihr spracht es an: Ihr habt den Kreis sogar noch erweitert und die Politik mit dazu geholt. Was bedeutet denn die Zusammenarbeit mit der Politik gerade, ihr habt es angesprochen, Richtung grüne Leitmärkte, denn das ganze ist ja keine rein ökonomische Angelegenheit, die Wirtschaftsunternehmen allein hinkriegen müssen. Da gehört ja noch ein bisschen mehr dazu.
Marcel Hilgers: Ja, absolut wichtiger Punkt! Wir haben ja einen Anstoß gegeben von unserem Unternehmen in die Dekarbonisierung, auch durch Unterstützung. Siemens Energy und andere sind natürlich auch Pioniere darin, erste Pilotprojekte mit nachhaltigen Materialien an den Markt zu bringen, und das ist auch alles gut so, um erste Informationen in die Märkte zu geben. Was ist da überhaupt im Angebot? Wie wird das zertifiziert, wie glaubwürdig ist das alles, und darüber in die Diskussion zu kommen. Aber wir sind eigentlich an einem Punkt angekommen, wo sich jetzt auch ein Markt entwickeln muss für nachhaltige Produkte. Nehmen wir mal hier ganz konkret nachhaltige Transformatoren. Und wer kauft Transformatoren? Das sind die Übertragungsnetzbetreiber, die Verteilnetzbetreiber, das sind meist regulierte Unternehmen. Da gibt's auch ganz tolle Pilotprojekte, Ultranet, Amprion sei da genannt und andere, wo nachhaltige Materialien verwendet werden. Aber, um wirklich einen großen Wurf zu machen, dort muss auch sowas entstehen wie ein grüner Leitmarkt für nachhaltige Materialien im Stromübertragungsnetz, ganz konkret in den Transformatoren. Und Christina hat es angedeutet, genau daran arbeiten wir. Da haben wir uns jetzt zusammengefunden in einer Arbeitsgruppe mit allen Beteiligten, um letztendlich dem BMWK ein Konzept vorzubereiten, wie nachhaltige Materialien, nachhaltiger Stahl Einzug finden kann, und stellen da Kostentransparenz her, um einfach einen sogenannten Pull von einem Markt, der auch refinanziert wird, zu erzeugen. Da müssen wir hinkommen. Es wäre absurd, wenn die Übertragungsnetzbetreiber grünen Strom in unser Stahlwerk übertragen, dafür ein neues Netzequipment anschaffen und kaufen und dann am Ende aber sagen ja, aber dafür können wir keinen grünen Stahl verwenden. Wir sind ja ein reguliertes Unternehmen, und das muss kostenneutral ablaufen. Wir wissen alle, das wird so nicht sein. Aber da beißt sich die Katze irgendwie den Schwanz.
Christina Iosifidou: Ja, und das ist nicht einfach zu erklären, und ich glaube, auch für unsere Kunden ist das sicherlich keine einfache Diskussion gegenüber ihren Endkunden, und das verstehen wir natürlich, weil am Ende müssen wir uns genau überlegen, wie dieses Kostenverteilungsmodell aussieht.
Christine Launert: Das Ende ist ja wirklich noch lange nicht erreicht bei diesem ganzen. Wir sind ja mittendrin. Wie sieht eure langfristige Version für eine nachhaltige Energiezukunft aus?
Marcel Hilger: Eine große Frage. Ich beziehe es mal auf die Stahlindustrie. Ich meine, unser Plan ist ja klar. Letztendlich wollen wir irgendwann hier keinen Hochofen mehr stehen haben, sondern wir wollen Stahl, wir wollen Eisen und dann Stahl erzeugen, indem wir grünen Wasserstoff verwenden, indem wir unsere Downstream-Aggregate, also zum Beispiel die Kaltwalzwerke, die Glühöfen, alles, was danach kommt, um daraus die finalen Produkte zu machen, auch nachhaltig zu betreiben, mit grünem Strom, mit Wasserstoff, mit sonstigen Sachen. Wenn wir das geschafft haben, dann sind wir schon ganz, ganz massiv viel weiter, und für mich bedeutet das letztendlich grüne Energie, also grüner Strom. Das Thema ist eigentlich adressiert. Da sind wir auf nem ganz guten Wege was das angeht. Da gibt's noch viel zu tun, sind wir aber auf dem guten Weg. Aber dann auch wirklich darauf zu achten, dass alle Betriebsmittel, zum Beispiel Transformatoren oder auch Autos und sonstiges, dann auch wirklich mit nachhaltigem Material gefertigt werden, da müssen wir noch hinkommen.
Christina Iosifidou: Und vielleicht von meiner Seite ergänzend, wie ich das für die Netztechnik eben sehe, der erste und wichtigste Beitrag ist natürlich der Ausbau der erneuerbaren Energien und die Integration dieser im Netz, und daran arbeiten wir heute schon sehr aktiv, mit sehr vielen Projekten für Offshore Windanlagen, wie zum Beispiel die 2 Gigawatt-Projekte von Amprion und TenneT. Aber auch in Zukunft ist der nächste Schritt, wie ich schon vorab erwähnt habe, neben den Produkten, die eben die Energiewende ermöglichen, und ohne Netztechnik wäre eine Energiewende nicht möglich, auch die Produktion von uns, und da haben wir das Ziel, 2030 klimaneutral zu sein in unseren Werken, in unseren Fertigungsstandorten und Büros, aber auch eben die Lieferkette. Da haben wir einen ganz konkreten Plan, bis 2030 zumindest 30 % zu reduzieren, und wir schauen uns natürlich auch die Produkteffizienz in der Betriebsphase an, und auch hier haben wir Ziele bis 2030.
Christine Launert: Bei mir heute zwei Menschen, die in die Hände spucken und eben anpacken wollen. Was wünscht ihr euch, was zum Beispiel schneller gehen?
Marcel Hilgers: Also ich glaube, abhalten tut uns gar nichts. Ich glaube, wir packen schon wirklich viel an, und ich würde das auch so interpretieren, Christina korrigiere mich da, aber, dass wir schon Antreiber für die gesamte Industrie Trafo-Industrie auch sind irgendwo, dass wir vorangehen und zum Beispiel gemeinsame Initiativen irgendwo starten. Zur Definition, was ist eigentlich ein nachhaltiger Transformator? Wie wird der bewertet? Wie können wir gemeinsam zu Bewertungsmaßstäben kommen, die in Deutschland, in Europa, aber auch global irgendwo akzeptabel sind? Christine, du hast gefragt, was müsste schneller gehen? Definitiv müssten wir jetzt viel, viel schneller Konsens in der Industrie finden, dass wir uns auf gemeinsame Normen, Zertifizierung, Klassifizierungen einigen und da noch stärker zusammenarbeiten, also noch transparenter miteinander umgehen. Das ist, glaube ich, das A und O, und wenn wir das geschafft haben, dann kommen die nächsten Schritte von alleine.
Christina Iosifidou: Ja, definitiv, also, dem stimme ich komplett zu, Marcel. Wir arbeiten ja auch aktiv, und das war immer der erste Baustein für uns an Transparenz und Messbarkeit. Und Messbarkeit in der Industrie über Standardisierung, Harmonisierung, das ist superwichtig. Ich denke, das werden wir auch erreichen. Das müssen wir jetzt zum Abschluss bringen. Dann muss es auch natürlich noch von einem Industrieansatz in eine Standardisierung, eine Norm münden, die auch in einem regulierten Markt wie unserem eben greift. Und was ich auch ganz klar sehe, die Arbeit, die wir auch aktuell leisten, ist in Richtung Politik, da auch beratend unterwegs zu sein, unsere Ansätze reinzubringen aus der Industrie. Was läuft gut, was müssen wir vielleicht nochmal verbessern. Wie gesagt, da passiert aktuell auch sehr viel im Rahmen des Zero Green Geals, sehr viele neue Policies, die beschlossen werden, und ich denke, wir können hier einfach uns sehr gut einbringen in Zukunft. Der dritte Punkt, vielleicht auch noch von meiner Seite. Wir werden weitermachen, das steht fest. Ich hoffe einfach auch durch diesen Podcast und über die anderen Aktivitäten und Kommunikationswege, die wir ersuchen, dass den Zuhörern, aber auch der Gesellschaft draußen immer klarer wird, wie eng eben alles zusammenhängt, und wenn wir nicht alle in dieselbe Richtung schreiten, dann wird das leider nicht funktionieren, und das ist meine größte Sorge, dass, wenn wir die Zusammenhänge nicht verstehen, die Dekarbonisierung und schlussendlich auch die Energiewende nur erschwert stattfinden kann.
Christine Launert: Ja, die Energiewende ist keine Floskel, sie ist Realität und findet gerade statt mit Menschen, die vollen Herzens dabei sind, Menschen der Next Generation Steel. Vielen Dank an meine Gäste für den interessanten Austausch, danke euch fürs Zuhören. Ich hoffe, es hat euch gefallen. Falls ja, abonniert gekocht, gewalzt, veredelt gerne auf den bekannten Podcast Plattformen und lasst uns gerne auch Feedback da, zum Beispiel via Mail an [email protected]. Ich freue mich auf weitere spannende Stahlthemen mit euch.
Folge 11: KI in der Industrie – Wettbewerbsvorteile durch digitale Transformation
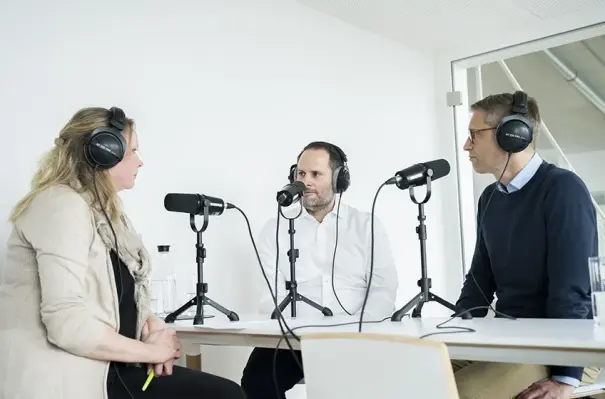
KI nimmt eine Schlüsselrolle in der digitalen Transformation von Industrieunternehmen ein. In der aktuellen Folge von "gekocht, gewalzt, veredelt" sprechen wir über Trends, Chancen und Herausforderungen im Zusammenhang mit KI. Wie kann die Produktion, Geschäftsabläufe und Lieferketten verbessern, bei der grünen Transformation helfen und dabei die Effizienz steigern, Kosten senken, die Produktqualität erhöhen und die Wettbewerbsfähigkeit in der zunehmenden digitalisierten Wirtschaft verbessern?
Im Dialog mit Christine Launert sind Professor Boris Otto vom Frauenhofer-Institut für Software- und Systemtechnik und Volker Lang, CIO von thyssenkrupp Steel.
Christine Launert: Liebe Zuhörerinnen, liebe Zuhörer. Willkommen zu einer neuen Folge von "gekocht, gewalzt, veredelt", dem Podcast rund um das Thema Stahl. In dieser Folge spreche ich mit unseren Gästen über künstliche Intelligenz. Was steckt dahinter? Wie viel Intelligenz steckt drin, und welche Möglichkeiten bietet sie Mensch und Wirtschaft? Ich möchte mit meinen Gästen auch über Grenzen, Gefahren und eine mögliche Bedrohung der natürlichen Intelligenz sprechen. Ich begrüße heute zwei Gäste, die sich täglich ganz intensiv mit der Digitalisierung der Welt beschäftigen, aber auch gleichzeitig so nah an der Realität sind, dass sie nicht nur in 0 und 1 denken. Professor Boris Otto vom Dortmunder Fraunhofer-Institut für Software- und Systemtechnik und Volker Lang, CIO und damit Leiter der Digitalisierung von thyssenkrupp Steel. Mein Name ist Christine Launert und ich bin Pressesprecherin bei thyssenkrupp Steel. Schön, dass ihr dabei seid!
Intro: gekocht, gewalzt, veredelt
Christine Launert: Volker Lang, vor fast 20 Jahren hast du bei thyssenkrupp Steel als Trainee und Softwareentwickler angefangen. Du hast die Digitalisierung der Stahlproduktion begleitet, gestaltet und mit allem drum und dran hautnah miterlebt, die Weiterentwicklung von Maschinen, Datenverarbeitung und Menschen. Heute bist du Leiter der IT bei thyssenkrupp Steel und unser erster Ansprechpartner, wenn es um Digitalisierung geht. Volker, wie viel Intelligenz steckt denn in KI?
Volker Lang: Ja, danke erst mal für die Vorstellung und die Einleitung. Wie viel Intelligenz steckt in KI? Ich glaube, das ist gar nicht so leicht zu beantworten. Am Ende hat jeder von uns, glaube ich, ein gewisses Verständnis davon, was er für intelligent hält. Und alleine der Begriff künstliche Intelligenz ist, ich sage mal, vor dem Hintergrund finde ich schwierig, weil da steckt so was Bedrohliches drin, als könnte mich jetzt KI substituieren, macht mich das als Mensch überflüssig. Ich glaube, dass in künstlicher Intelligenz, viel mehr Mathematik, viel mehr Technologie, viel mehr Daten drin steckt als das, was uns als Menschen auszeichnet, was wir als intelligent empfinden. Ich sag mal, Empathie, Kreativität, alles das, was wir da draußen erleben, was dem irgendwie nahe kommt, wenn KI Kunstwerke schafft, Musik macht, ist am Ende doch nichts anderes als ein gut trainiertes Modell und eine Riesenmenge Daten. Also nach meinem Dafürhalten viel weniger Intelligenz, als man vielleicht meint, und vor allem glaube ich etwas, was vom Begriff her, wie gesagt, unglücklich ist, weil es uns doch irgendwie so ein bisschen bedroht.
Christine Launert: Professor Boris Otto, als studierter Wirtschaftsingenieur hast du auch die wirtschaftliche Seite kennengelernt und später Unternehmen sogar beraten. Frage an dich, ist die Wirtschaft gut beraten, den Trend der künstlichen Intelligenz mitzumachen?
Boris Otto: Ja, klar. Also, ich glaube, wir haben in Deutschland in der industriellen Basis unheimlich viele Stärken, die sehr stark einfach begründet sind darin, dass wir in der Lage sind, gute Produkte zu entwickeln, die die Kunden überzeugen, und Produktionsprozesse so zu organisieren, dass sie am Ende eben halt auch Produkte produzieren, die zu einem vernünftigen Preis halt am Markt auch absetzbar sind. Also, da sind wir, glaube ich, sehr gut. Aber die Welt steht nicht still, und ich bin persönlich davon überzeugt, dass die Digitalisierung als solche, die gesamte digitale Transformation, aber auch die bessere Nutzung von Daten und eben halt auch die künstliche Intelligenz riesige Chancen für uns sind, weil es eben Möglichkeiten bietet, das, was wir schon immer gut konnten, also Produkte zu entwickeln und zu verkaufen, die man anfassen kann, das zu ergänzen durch digitale Dienste, die letzten Endes halt den Kundenmehrwert nochmal erhöhen. Also, ich persönlich sehe das als große, große Chance und glaube auch, dass wir gerade in dieser Kombination, also aus Produkt und Leistungsbündeln, also insbesondere von Dienstleistungen, die digital gestützt sind, eine Kombination erreichen können, die unschlagbar ist. Weil wir tatsächlich eben halt das, was wir schon immer gut konnten, verbinden können mit den Möglichkeiten, die sich durch KI, aber generell aus der digitalen Transformation auch ergeben.
Christine Launert: Vor diesem Hintergrund, welchen Einfluss hat also die Digitalisierung auf den Wirtschaftsstandort Deutschland oder das Ruhrgebiet im speziellen?
Boris Otto: Also, ich bin ja auch nur zugezogen ins Ruhrgebiet. Also ich komme ursprünglich aus Hamburg, und ich war von vornherein einfach Feuer und Flamme vom Ruhrgebiet, und ich glaube auch, dass das etwas ist, was sich eben halt auch in Bezug auf die Frage, wie wir digital Transformation nutzbar machen können, hier am Standort durch Unternehmen wie thyssenkrupp niederschlägt. Weil ich glaube, wir sollten uns nicht vergleichen mit Standorten wie Hamburg oder München oder Berlin, wo wir letzten Endes ja so in Berlin Mitte irgendwie die coolen Apps entwickeln, stark für den Consumerbereich, sondern wir sollten uns auf das konzentrieren, was wir gut können. Hier war immer das industrielle Herz Deutschlands, und das ist auch nach wie vor noch so, und ich glaube, diese Stärken muss man transportieren in die Zukunft, und letzten Endes haben wir, das muss man eben auch sagen, hier im Ruhrgebiet auch mittlerweile ein digitales Powerhouse. Also, wir haben zig Universitäten, eigentlich auf einer Distanz von ein bisschen mehr als 50 Kilometern, ich glaube, mehrere 100.000 Studenten und Studentinnen, die sich mit diesen Themen beschäftigen. Wir haben an der TU Dortmund einfach Kerne in der Logistik, in der Informatik, und wir können letzten Endes halt wirklich, naja, digitale Dienste, digitale Transformation für die Industrie machen. Und das ist gar nicht in so vielen anderen Orten von Deutschland der Fall und auch möglich. Also, wenn wir das verbinden und tatsächlich auch ein bisschen das, was man hier immer propagiert, ehrliche Arbeit, down to earth und wirklich halt auch die letzte Meile gehen, das ist super, das ist eine Stärke, die man einfach in die Waagschale legen muss aus dem Ruhrgebiet für Deutschland, aber ehrlich gesagt auch weltweit, letztenendes halt, das dann zu vermarkten. Damit werden wir erfolgreich sein.
Volker Lang: Dem kann ich mich nur anschließen. Ich meine, es gab ja Jahre, da sind wir immer in die ganze Welt gepilgert, in Silicon Valley, nach Berlin-Kreuzberg immer gerne, nach Tel Aviv, um uns anzugucken, wie Digitalisierung funktioniert. Ehrlicherweise ist das nicht nötig. Wir haben, du hast das gesagt, hier eine unglaublich starke Hochschulszene, und vor allem haben wir hier die Anwendungsfälle. Also wir müssen ja am Ende des Tages die Technologie dahin bringen, wo der Anwendungsfall ist, und nicht uns angucken, wie andere Technologien entwickeln. Das ist auch das, wo es bei thyssenkrupp Steel ganz stark darum geht. Wir entwickeln keine KI, wir sind nicht sozusagen an der Spitze der Forschung. Das, was wir tun müssen, ist, dafür sorgen, dass die Technologie, die da draußen verfügbar ist, bei uns schnellstmöglich in der Fläche ankommt und auch wirklich ihen Nutzen entfaltet. Und das machen wir am besten hier vor Ort.
Boris Otto: Und ich glaube halt auch das ist, das hast du gesagt, Volker, weil das war so, in der Tat, also bei uns kamen ja auch immer viele an, die gesagt haben, was da so im Silicon Valley passiert und genau, in Israel, das ist ja alles cool. Und man hat dann so den Eindruck gehabt, da kommen jetzt Firmen, die haben irgendwie 150 Jahre lang wirklich erfolgreiches Business gemacht, Marktführer, unter den Top 3 der Welt, und die beklagen jetzt sozusagen, dass sie sozusagen noch ihren Produktballast mit sich rumschleppen und nicht Digital Native sein können, was für ein Unfug. Also letzten Endes, wenn man etwas versucht zu kopieren, dann wird man nie besser, aus meiner Sicht, als das Original. Es gibt auch andere Bereiche auf dem Erdball, wo das vielleicht anders gesehen wird, aber ich glaube bei uns, wir müssen ja irgendwie innovativ sein und nach vorne gehen, und ich glaube, wenn wir tatsächlich unsere Stärken weiter in die Waagschale werfen, wir müssen auch tatsächlich, das ist vielleicht schon auch ein Punkt, wir müssen verstehen, wie Digitalwirtschaft funktioniert, also wir brauchen irgendwie Skalierung und so weiter, wir brauchen kritische Masse. Gerade bei Plattformen müssen wir sehen, Netzwerkeffekte, das funktioniert anders als klassisches Produktgeschäft. Also da muss man sich dann schon mit auseinandersetzen. Aber wenn man das tut, hat man einfach unheimliches Potenzial, mit einem eigenen Leistungsangebot, was sich eben klar differenziert von allen anderen Wettbewerbern, dann auch am Markt erfolgreich zu sein.
Christine Launert: War das die große Herausforderung für industrielle Unternehmen, die digitalisieren wollten oder das auch getan haben?
Boris Otto: Ja, Herausforderungen gibt es ja immer viele, da sind wir auch natürlich in Deutschland immer gut, die alle zu benennen, aber in der Tat ist es natürlich so: Es gibt ja in der Forschung diesen Begriff des Innovators-Dilemma, und natürlich ist es immer schwierig, Dinge, die jahrzehntelang super funktioniert haben, zu hinterfragen, am Ende sind es alles nur Menschen. Der Mensch ist gerne in seiner Komfortzone und sich zu zwingen, jeden Tag neu zu überlegen, was könnte man noch besser machen, damit man, na ja, den Zug auch nicht verpasst, der da so kommt, das ist, glaube ich, wirklich eine große Herausforderung. aber man sieht eben halt gesagt immer auch Unternehmen, bei denen das einfach gut gelingt, wie man das dann eben halt in das eigene Leistungsangebot einbauen kann. Und das muss letzten Endes aus meiner Sicht auch der Weg sein, dass wir unsere Stärken nutzen, dass wir aber eben immer die Karrotte weiter nach vorne hängen. Wir müssen innovativ sein, weil sonst, wenn wir das nicht machen, haben wir halt das große Risiko, dass wir faktisch nur noch über Preis konkurrenzieren, und das dürfen wir niemals zulassen, weil da werden wir immer verlieren. Wir müssen innovativ sein, und die digitale Transformation bietet wahrscheinlich mehr Möglichkeiten dafür als in den letzten 100 Jahren, klassische Produktentwicklung.
Christine Launert: Das heißt also war die Entwicklung der künstlichen Intelligenz nur der nächste logische Schritt in der Digitalisierung?
Volker Lang: Hm, ja, der nächste logische Schritt, ich sag mal, künstliche Intelligenz, ist ja jetzt gar nicht mal so neu, wie man meint, wenn man quasi erst dann anfängt, sich dafür zu interessieren. Ich sage mal gerade Chat GPT, ich weiß gar nicht, wann war es, 18 Monate her oder was, wo das durch die Presse und durch die Decke gegangen ist. Das ist ja sozusagen die neueste Ausbaustufe, und ich glaube, das Spannende an der technologischen Entwicklung ist eigentlich die Geschwindigkeit. Wenn du heute über Chat GPT redest, finden es alle schon fast langweilig, weil jeder hat es schon dreimal benutzt und weiß, wie es funktioniert, und hat eine Vorstellung, was er damit machen kann. Vor einem Jahr war das noch in jedem Impulsvortrag zur Digitalisierung, war die Live-Demo Chat GPT das Highlight. Bis dahin ist das gar nicht so spannend. Was ich spannend finde, ist, vor drei Jahren hätte ich keine Ahnung gehabt, dass es in zwei Jahren kommt. Das hat man nicht kommen sehen, und das ist auch das, was, glaube ich, für uns herausfordernd ist. Sagen wir mal, Wege zu finden, um als Industriekonzern mit diesem Ausmaß an Dynamik klarzukommen, weil es geht ja nicht darum, mehr Energie da reinzustecken, was kommen wird. Ich sag mal, da findest du immer Antworten. Und umso mehr Energie du reinsteckt, um so plausibler sind die. Eigentlich müssen wir lernen, schnellstmöglich Technologie-Neuerungen zu adaptieren. Das ist eigentlich die Kernkompetenz der Zukunft, und jetzt kann man als Außenstehender meinen, Stahl und Industriekonzern und Digitalisierung, das ist ja irgendwie wahnsinnig weit auseinander. Wenn man sich ein bisschen mit dem beschäftigt, dann weiß man halt, naja, ganz so weit liegt das nicht auseinander. Ich meine, wir sind ein Technologiekonzern. Stahl ist sehr, sehr physisch, ist kein digitales Produkt, und ehrlicherweise ist uns auch bisher nichts eingefallen, wie man da KI einbauen kann. Es bleibt also ein sehr physisches Produkt, aber es ist trotzdem ein High-Tech-Produkt. Ich meine, das hat höchsten Kundenanforderungen zu genügen in Bezug auf Oberflächenqualität, auf mechanisch-technologischen Eigenschaften, und wenn ich mir, sagen wir mal, ein Bild von den Anlagen mache, mit dem wir das produzieren, dann ist völlig klar, dass das völlig automatisierter, durchdigitalisierter High-Tech -Prozess ist. Anders geht das bei den Mengen gar nicht. Und deshalb ist auch, sagen wir mal, wenn du quasi 30 Jahre Automatisierungstechnik in der Geschichte hast, dann ist Digitalisierung eigentlich nur der nächste Schritt, und auch Industrie 4.0 war für die Kollegen in der Produktion ja nichts wirklich Verrücktes. Richtig ist, wir haben die Fähigkeiten, mehr Daten auszuwerten. Wir nutzen das heute anlagenübergreifend, wir nutzen das unternehmensübergreifend. Die Potenziale sind andere. Aber im Kern ist die Idee, zu optimieren, zu automatisieren, Prozesse enger und besser zu überwachen, die ist irgendwie schon Teil von dem, was Stahlproduktion und Stahlfertigung ausmacht, schon immer.
Christine Launert: Ja, also bis vor kurzem haben wir uns vor allem über Big Data unterhalten und das Management von großen Datenmengen, und dass ich sehr viel sammeln kann, aber viel weniger davon auswerten und nutzen kann. Vielleicht kannst du das einmal kurz abgrenzen. Was hat denn das eine überhaupt mit dem anderen zu tun, und welchen Impact hat dieser Grad der Digitalisierung denn auf die reale Produktion, wie zum Beispiel unsere Stahlproduktion?
Volker Lang: Ja, kann ich gerne versuchen einzuordnen. Also, wir unterhalten uns immer noch über Big Data, und wir sammeln auch immer noch Daten, und sei es, weil wir es können. Also nur die Frage ist, was bringt das? Wenn ich jetzt sage, in unserem Data Lake landen jeden Tag 600 Millionen Datensätze aus der Produktion. Klasse. Mit der Aussage kann ich aber nichts anfangen, weil die eigentliche Frage ist ja nicht, welchen Aufwand betreiben wir um Daten zu sammeln, sondern was tun wir eigentlich damit? Und warum sammeln wir überhaupt Daten, bevor wir sie brauchen? Na ja, ich meine, wir reden heute über KI, wir reden über KI -Modelle. Es liegt einfach, ich sag mal, im Wesen der Technologie, dass ich eine Unmenge an Daten brauche, um überhaupt Modelle trainieren zu können. Am Ende geht es ja immer darum, Muster zu suchen in irgendwelchen Daten. Zusammenhänge erklären zu können, die wir in der Vergangenheit nicht erklären konnten, und meistens ist es so, dass der konkrete Anlass, um sich dann zum Beispiel mit KI an eine Herausforderung zu setzen, ist, ja, dass irgendwas passiert ist, was ich erklären will. Wenn ich erst in dem Augenblick anfange, Daten zu sammeln, dann habe ich ja keine Historie, auf die ich gucken kann. Das heißt, wir haben das große Glück, dass wir stellenweise auf 15 Jahre Historie in den Daten zurück gucken. Wir haben einfach unglaubliche Datenmengen, sodass wir es wirklich schaffen, das Problem einzugrenzen, Modelle zu trainieren, und das hilft uns halt, Abweichungen in der Qualität oder Abweichung in der, ich sag mal, Zuverlässigkeit unserer Anlagen doch relativ gut zu analysieren oder auch zum Beispiel vorherzusagen, wie sich bestimmte Anlagenbauteile in der Zukunft verhalten werden, das ist der eigentliche Wert da drin, und auch dann der Impact in der Produktion.
Boris Otto: Also, das finde ich ganz interessant, was du gesagt hast, Volker, weil, das ist, glaube ich, auch vielen Unternehmen gar nicht so bewusst. Es wird häufiger davon geredet, dass man auf einem Datenschatz halt sitzt, und das stimmt eben auch. Weil, wenn wir uns die Entwicklung von künstlicher Intelligenz und auch generativer KI gerade anschauen, ist es ja so, dass die ganzen bekannten Modelle eigentlich basieren auf Daten, die mehr oder weniger frei verfügbar sind und die eben auch in textueller Form verfügbar sind. Und die Ergebnisse, die man damit produzieren kann, sind gigantisch. Aber das Potenzial, wenn wir tatsächlich halt auch die Daten beispielsweise aus Produktionsprozessen der letzten 20 Jahre nutzen können, um viel besser noch vorher zu sagen, wie bestimmte Verhaltensweisen in Produktionsprozessen sich auswirken auf die Qualität von beurteilen und so weiter, dann wird letzten Endes dann auch tatsächlich etwas daraus, was wirklich Mehrwert stiftet, auch für industrielle Prozesse. Und das wiederum ist aber auch ein Grund, weswegen wir nicht einfach blauäugig sein können und diese großen Datenbestände einfach so irgendwo hin kippen, wo man dann auch nicht so weiß, wer da noch so mit agiert, sondern wir müssen tatsächlich dann auch schauen, dass diese Daten eben eine gewisse Werthaltigkeit haben, und man muss sie dann eben auch so bewirtschaften. Lass mich vielleicht auch das noch mal aufgreifen, was wir eben kurz diskutiert hatten, mit der auch Industrie 4.0 und die Abgrenzung zwischen Big Data und KI und so weiter. Da möchte ich nochmal auch das herausstellen, was Volker gesagt hat, weil ich meine, überspitzt formuliert, Industrie 4.0. kam auf, alle so: ja, das ist die industrielle Revolution. Aber ich habe jetzt kein Unternehmen gesehen, was jetzt irgendwie seine alten Werke abgebrannt hat im Sinne einer Revolution und auf der grünen Wiese daneben alles neu gebaut hat. Was ich damit sagen will, das ist ja eigentlich immer eine technische Evolution, das ist auch gut. Und gerade bei KI, also ich habe in den 90er-Jahren studiert, bei Dieter Bressmer hatte ich ein Fach, das hieß damals noch "betriebliche Datenverarbeitung". Da ging auch schon um neuronale Netze und künstliche Intelligenz, und letzten Endes waren viele von den theoretischen Grundlagen damals schon gelegt. Aber es mangelte eben halt an dem Zugang zu Daten, die man braucht, um diese Muster auch vernünftig und effektiv zu erkennen. Man hatte nicht die Rechenleistung verfügbar. Das muss man eben sagen, um letzten Endes die Berechnung auch durchzuführen, um diese Muster zu erkennen. Und man hatte letzten Endes dann am Ende auch nicht die die Masse an Mitarbeitern und Mitarbeiterinnen, die sich hinreichend damit auskannten. Also es muss viel zusammenkommen, damit dann letzten Endes halt auch gewisse Technologien eigentlich erst ihre Wirkung entfalten können. Und bei Industrie 4.0, wie gesagt, ich meine, wir haben auch in den 80er und 90er Jahren gab es schon Computer Integrated Manufacturing, es gab die digitale Fabrik. Das sind alles letzten Endes halt Evolutionsstufen, die dann heute ein Stück weit konvergieren in dem, was wir dann Industrie 4.0 nennen.
Volker Lang: Das, was das bei uns ausgelöst hat oder eher ausgemacht hat, war sozusagen keine Revolution der Technologie, genau wie du sagst, es war alles durchautomatisiert. Aber wir haben halt in der Vergangenheit die, ich sag mal, Anlage für Anlage optimiert, und, ähm, wir hatten auch mit der Technologie, die in dem Zuge entwickelt worden ist, also Data Lakes, IOT-Plattformen, das erste Mal die Möglichkeit, wirklich einfach die Daten aller unserer Anlagen in Kontext zu setzen und übergreifend auszuwerten. Da gehört natürlich auch immer, ich sag mal, dann so ein bisschen Mindset-Transformation mit dazu, weil natürlich es auch stark so ist, dass man oft eine Situation vorfindet, wo jemand sagt, das sind aber meine Daten. Also da steckt ja zumindest schon mal die Idee drin, dass das einen Wert hat sind. Da freuen wir uns schon mal. Also offensichtlich haben die Kollegen den Wert ihrer Daten erkannt, aber sie wollten sie halt anfangs gerne behalten. Dann eben auch zu erklären, dass wir natürlich eine Chance haben, an der Stelle viel mehr zu erreichen, wenn wir gemeinsam drauf gucken, das ist ein Prozess, der ist jetzt bei uns auch schon irgendwie 10 Jahre her, aber das war sehr, sehr wichtig. Und was ich halt spannend finde, ist das gleiche, was wir quasi innerhalb unserer Wertschöpfungskette gemacht haben, nämlich übergreifend zu vernetzen oder zu optimieren. Das ist eigentlich das, was ich jetzt nach vorne heraus auch sehe, dass man das halt unternehmensübergreifend tun kann, weil da mit Sicherheit auch Potenziale liegen, wenn ich, sagen wir mal, irgendwie, es schaffe, eine Transparenz zu schaffen, um eine Kollaboration eigentlich vom Rohmaterial bis zum fertigen Konsumerprodukt. Das ist auch spannend.
Boris Otto: Also genau, das ist tatsächlich das, was jetzt möglich wird, dass wir quasi die gesamte Prozesskette und auch den Produktlebenszyklus komplett eigentlich erfassen können und damit auch besser steuern können. Das hilft uns einerseits auch, sagen wir mal, Kundenbedürfnisse noch besser zu bedienen, aber auf der anderen Seite gibt es eben auch Anforderungen, wo wir es einfach tun müssen. Also wir haben, das ist immer natürlich kein besonders glücklicher Treiber, Regulierung. Aber das Lieferkettensorgfaltspflichtengesetz, mit dem schönen deutschen Namen, verpflichtet uns ja dazu, dass wir eigentlich in die Prozesskette hineingucken müssen und eigentlich alle Daten zusammensammeln müssen über den gesamten Lebenszyklus von Produkten, die sich damit beschäftigen, wo kommen diese Daten her, wo wurden sie produziert? Ist das alles erfolgt im Einklang mit gesetzlichen Vorgaben hinsichtlich von Umweltstandards, von Sozialstandards und so weiter? Aber und ich glaube, das ist etwas, was noch wichtiger ist, Stichwort Kreislaufwirtschaft, also letzten Endes halt Komponenten wiederzuverwerten, was wir ja gerade in der Elektromobilität einfach sehr, sehr stark haben, weil, ich meine, bin da zwar kein Experte, aber was ich so wahrnehme, ist, können, wir haben ja gar nicht so viel Lithium, dass wir einfach faktisch die ganzen E-Autos bauen könnten, die man bräuchte, um dann den Mobilitätssektor tatsächlich klimaneutral machen. Das heißt, wir müssen das, was wir jetzt nutzen, wieder in einem Sekundärkreislauf in die Produktion überführen, und dazu müssen wir eigentlich, und das fand ich gut, was du gesagt hast, Volker, über den gesamten Lebenszyklus, über den gesamten Prozess eigentlich ein digitales Abbild, einen sogenannten digitalen Zwilling haben, nicht nur über das Produkt selber während der Nutzung, sondern letzten Endes auch die Komponenten, die in das Produkt einfließen, die Werkstoffe und eben halt dann während der Nutzung, um in der Lage zu sein, zu erkennen, welche Batteriekomponenten denn tatsächlich jetzt zur Sekundärnutzung noch verfügbar gemacht werden können und welche eben nicht.
Christine Launert: Ja, aber da will ich kurz einhaken, denn wenn es schon so schwierig ist, Daten auszutauschen oder loszulassen zwischen meinem Arbeitsbereich und dem eines anderen, wie schaffe ich es denn dann, dass ich einsehe in meiner Position, dass ich Daten in der Lieferkette, also wirklich von Anfang bis Ende auch teile und das unter Umständen mit der halben Welt teile?
Boris Otto: Also, ich glaube, das ist einfach, man muss es immer sagen, häufig ist der, muss der Druck groß genug werden, damit dann auch Aktion passiert. Tatsächlich, ich glaube, alle haben jetzt, und vielleicht, um ein Beispiel zu nennen, Catena-X, ist ja das Datenökosystem oder der Data Space der Automobilindustrie, und alle treibenden Unternehmen haben es alleine versucht, sozusagen, haben gesagt, nee, wollen wir alleine machen, wir wollen eine Plattform bauen und so für unser Liefernetzwerk, und dann können wir auch ganz genau bestimmen auf welche Formatenstandards das alles funktioniert, und es hat eben nicht funktioniert aus zwei Gründen. Das eine war, dass es einfach schlicht und ergreifend zu teuer war für eine einzelne Unternehmung, und das andere war, dass man eingesehen hat, dass man die Durchdringung gar nicht erreicht, weil man ja, man hat ja nicht eine Lieferkette, sondern ein weitverzweigtes Liefernetzwerk, wo gerade die Zulieferer eigentlich die sind, die sozusagen die Spinne im Netz sind, weil sie in ganz verschiedene Kundensituationen liefern. Und man hat dann eben halt auch durch so Sachen wie die Halbleiterkrise auch festgestellt, dass man zwar groß ist, aber dass es im Teich noch größere Fische gibt, so wie Samsung oder Apple, die dann einfach alles wegkaufen. Also man muss einfach mal schauen, dass man sich zusammentut, und diese Erkenntnis, es gemeinsam zu machen, die dann auch dazu führt, und das war ja auch etwas, was wir für uns in einem gemeinsamen Projekt schon vor, ich glaube, 5 oder 6 Jahren auch mal pilotiert haben, wie man so einen Datenaustausch, der fair ist und gleichberechtigt ist, umsetzen kann. Ich glaube, diese Erkenntnis ist jetzt wirklich da, und deshalb bin ich auch davon überzeugt, dass so Ansätze wie Catena-X auch erfolgreich sein werden, weil es anders nicht geht.
Christine Launert: Entscheidend ist wahrscheinlich, dass jeder seinen Nutzen rausziehen kann.
Volker Lang: Genau, und der ist zum Beispiel für uns heute völlig klar. Also, als wir vor 5 Jahren zusammengearbeitet haben, lief es bei uns auch noch, ich sag mal in der Abteilung Forschung und Entwicklung, und lass uns doch mal gucken, wie sich das denn anfühlen würde, und es hat auch funktioniert. Heute haben wir aus einer thyssenkrupp Steel-Perspektive den denkbar größten Anwendungsfall direkt an der Hand. Das ist unsere eigene grüne Transformation. Ich meine, klar denken wir immer, wenn wir über Dekarbonisierung reden, zuerst, ich sag mal, an den Bau einer Direktreduktionsanlage auf unserem Gelände. Das ist auch völlig richtig, da zuerst dran zu denken, weil das ist ja der Schritt, der eigentlich wirklich das CO2 aus dem Prozess entfernt, und das ist mit Sicherheit ein gewaltiger Schritt. Als zweites stellen wir uns dann vielleicht die Frage, na ja, wo kommt denn der grüne Strom her oder der grüne Wasserstoff? Das ist auch alles richtig. Aber das ist eben auch mit Abstand die größte Geschäftsmodelltransformation, der wir uns zu stellen haben. Am Ende geht es darum, einem Endverbraucher zu ermöglichen, eine bewusste Kaufentscheidung zu treffen, wenn er sich eine Waschmaschine kauft, wenn er sich ein Auto kauft, ich weiß nicht, was. Dafür braucht er eine Information nicht nur zu den Produkteigenschaften, die man so kennt, und zu einem Preis, sondern eben auch zu einem CO2 Fußabdruck. Der kann ja nur entstehen, ich sage mal, wenn wir, ich meine, wir sind ganz am Anfang der Wertschöpfungskette in Europa. Wir müssen in der Lage sein, das transparent zu machen und entlang der Lieferkette bereitzustellen. Und selbstverständlich funktioniert das nicht, indem wir irgendwie E-Mails an alle unsere Kunden und Freunde schicken mit einem Anhang mit einem CO2- Fußabdruck, sondern wir brauchen genau solche Plattformen. Das ist völlig klar, und da profitieren wir davon, dass wir eben vor ein paar Jahren sozusagen die Zusammenarbeit schon mal geübt haben, und die werden wir jetzt im Rahmen von Catena-X ganz sicherlich brauchen, weil das ist klar, ich meine, das ist die Plattform unserer größten Kundengruppe, keine Frage.
Boris Otto: Ja, und ich glaube, man muss auch lernen, dass man das, was man jahrzehntelang im Materialfluss, also in der Wertschöpfungskette der Produkte gelernt hat, dass man das in gleicher Art und Weise auch überträgt auf den Datenfluss, der letzten Endes über die gesamte Kette halt läuft. Wir müssen Daten genauso begreifen wie jede andere Ressource, es ist halt eine betriebswirtschaftliche Ressource, die ist nicht for free da. Also, Daten in vernünftiger Qualität bereitzustellen, ist nicht umsonst, sondern wie alles, was Qualität hat, comes at a cost. Das letzten Endes ist etwas, und gerade quasi auch ein Produktpass oder ein product carbon footprint-Ausweis ist im Prinzip ein Informationsprodukt, was ich bereitstelle für den Kunden, und da fließen eben halt Datenkomponenten ein, und da muss ich eben sehen, wo ich die herbekomme, wo ich sie beschaffe, und das Letztenendes genauso bewirtschaften und managen wie halt die ja, die physische Wertschöpfungskette. Und der Vorteil ist, und das, was du gesagt hast, Volker, ist, das fand ich auch nochmal gut, dass man ja, na ja, jeder hat die Daten. Also ist ja nicht so, dass wir das Problem haben, dass sie nicht da sind, die Daten. Wir müssen sie eben halt nur in fairer Art und Weise, dass das du gesagt, so dass jetzt mal platt gesagt, keiner über den Tisch gezogen wird, dass man sie eben halt im Sinne des ganzen, im Sinne des Kunden halt auch verfügbar macht. Und das haben wir gemeinsam schon vor fünf Jahren gezeigt, dass das geht, und jetzt ist es etwas, was wir in großer Anwendung einfach sehen.
Volker Lang: Es ist halt keinesfalls trivial. Du hast ja gesagt, es gibt einen Fluss der Produkte. Den ergänzen wir um den Fluss der Daten, und dem entgegen gerichtet, ist ja normalerweise ein Zahlungsfluss. Wir reden immer über Daten haben einen Wert, aber welchen denn eigentlich? Also können wir bald Daten handeln?
Christine Launert: Wer gibt den Wert?
Volker Lang: Ja genau, wer bestimmt den Wert, und wie organisieren wir das? Das ist, wie gehen wir mit Datensouveränität um? Also übertragen wir jetzt eigentlich Eigentumsrechte an Daten oder Nutzungsrechte zeitlich begrenzt oder nicht zeitlich begrenzt? Egal, was wir da tun, das muss wahlweise technisch oder vertraglich geregelt werden. Und ganz ehrlich, das ist für unser Geschäftsmodell essenziell, aber wir wollen das alles gar nicht tun. Insofern bin ich sehr dankbar, dass es Leute gibt, die da Forschen und Lösungen bauen. Das können wir dann gerne einfach benutzen, wenn es fertig ist.
Christine Launert: Deswegen machen wir das alles nicht alleine, ne?
Volker Lang: Deshalb machen wir das nicht alleine. Es geht immer um Ökosysteme, es geht um Partnerschaften, es geht darum, dass da ganz, ganz viele Leute ihre Kompetenz mit an Tisch bringen.
Christine Launert: Wir hatten es gerade schon. Am Ende entscheidet der Kunde, will ich das Produkt kaufen, gefällt mir der Footprint? Jetzt haben wir die Menschen und ihre natürliche Intelligenz noch an ganz anderen Stellen in dieser ganzen Kette, nämlich die Frage von allen, müssen wir uns darauf gefasst machen, dass durch künstliche Intelligenz unsere Arbeitsplätze künftig verdrängt werden, ähnlich der Automatisierungswelle in den 70er und 80er-Jahren? Oder entstehen vielleicht neue Berufsfelder und ich muss es positiv sehen und die Möglichkeiten erkennen?
Boris Otto: Also vielleicht, wenn ich da kurz einhaken darf, was du gerade beschreibst, das war schon immer so. Jede technische Innovation hat dazu geführt, dass der Mensch bestimmte Dinge nicht mehr machen brauchte. So muss man es auch sehen, das ist ja etwas, was letzten Endes Ausweis unseres Fortschritts auch ein Stück weit ist. Und ja, es gibt ganz viele Dinge, die wir einfach gar nicht mehr können, weil uns das die technische Innovation einfach abnimmt. Und letzten Endes ist das eben halt auch, klingt zwar vielleicht ein bisschen pathetisch, aber eben halt auch, na ja, eine Voraussetzung dafür, dass wir auch am Ende Wohlstandsgewinne irgendwo erreichen, und natürlich ist es immer so, dass das mit Veränderungen zu tun hat, und ich glaube, das ist der springende Punkt. Veränderung ist für den Menschen immer etwas, und da nehme ich mich auch gar nicht aus, was erst mal, na ja, irgendwo mit einem gewissen Hemmnis daherkommt. Man muss irgendwie was anders machen. Man ist immer geneigt, in seine Komfortzone zurück zu fallen und ist immer sehr zufrieden damit, dass alles so läuft, wie es immer gelaufen ist. Aber wenn das auch in der Vergangenheit schon so gewesen wäre, hätten wir nie technischen Fortschritt halt erreicht. Und ich bin fest davon überzeugt, dass uns die technische Entwicklung, insbesondere auch bei der künstlichen Intelligenz, das Leben leichter machen wird, sowohl im privaten wie auch im industriellen. Und man muss ja auch so sehen, also, ich meine, es ist ja nicht so, dass irgendwie Deutschland in der Bevölkerung unendlich wächst. Also, wir haben ja die Herausforderung, dass wir die Arbeit, die zu erledigen ist, naja, ohne letzten Endes technologischen Fortschritt wahrscheinlich mehr gar nicht mehr erledigen könnten. Das muss man ja auch mal so sehen, und ich sehe das grundauf positiv. Und ich finde auch immer, vielleicht das als letzten Punkt, wir sollten nicht in so eine Situation wie das Kaninchen vor der Schlange verfallen und sagen, oh, ich bin irgendwie bloß der Spielball, und wir können nur noch reagieren. Nee, wir haben die Chance, die Zukunft zu gestalten und eben auch in dem Sinne zu gestalten, wie wir das für richtig halten, und das finde ich einfach vernünftig.
Volker Lang: Das ist glaube ich eine gute Perspektive. KI macht mit uns mal so gar nichts. Die Frage ist, was wir mit KI machen und gerne dabei auch den Begriff irgendwie erklären. Ich sag mal, wenn man, wenn man die Schlange sich mal genauer anguckt, ist die auch schon gar nicht mehr so gefährlich, und das ist halt auch unser Ansatz, das ist nur eine Bindschleiche und Kaninchen können ganz schön groß werden, also so schlimm ist das alles gar nicht, und am Ende ist es ja wirklich so, das ist auch das, was wir tun, wenn wir versuchen, KI begreifbar zu machen, das fängt damit an, dass man es demystifiziert. Also wenn man jemanden mal gezeigt hat, wie blöd ein KI-Modell ist, bevor man das trainiert hat, das ist ja wirklich wie, wenn ich einem kleinen Kind beibringe, und das ist auch das Beispiel, mit dem wir zum Beispiel in die Produktion gehen. Also wir zeichnen Kreise, Dreiecke und trainieren mit diesen Bildern und einer Kamera ein KI-Modell. Dann erkennt das, ich sag mal, Kreise und Dreiecke, und dann zeichne ich ein Rechteck, und dann sagt das, das ist aber ein hässlicher Kreis, und dann muss ich halt das trainieren, und ich sag mal, das ist das, was wir wirklich Menschen ermöglichen müssen, nämlich zu begreifen, wie das funktioniert und wo die Grenzen sind. Und dann hast du auch automatisch die Rolle des Menschen zum Beispiel in dem Beispiel, in dem Prozess, gefunden. Wir müssen die Modelle trainieren. Und ich habe noch kein Digitalisierungsprojekt gemacht, ob mit oder ohne KI, wo nicht hinterher die Leute, die wir davon entlastet haben, bestimmte automatisierbare oder repetitive Tätigkeiten durchzuführen, nicht dankbar wären. Ich meine, es hat doch keiner Lust, den ganzen Tag irgendwas von der SAP-Maske in eine andere Maske abzutippen oder andersrum. Das macht keinen Spaß. Also, am Ende ist es in der Tat so, dass Automatisierung und Digitalisierung hilft und uns auch die Chance gibt, ich sage mal, uns auf das zu fokussieren, was wir als Menschen dann doch sehr viel besser können als ein wie auch immer ausgefuchster Algorithmus.
Christine Launert: Und der beste Effekt ist, dass ich es halt wirklich merke.
Volker Lang: Ja, absolut. Es entlastet, sofort!
Christine Launert: Bei allem Spaß an neuer Technik müssen wir einmal über Sicherheit sprechen. Wir haben vor allem den Punkt der Datensicherheit, das heißt, ich häufe Daten an, ich verwalte sie, ich teile sie im besten Fall. Wie können aber jetzt Unternehmen oder Organisationen ihre Daten auch wirksam schützen, und wo sind da die einfachsten Hebel oder die wirkungsvollsten Hebel?
Boris Otto: Ja, das ist ein ziemlich breites Thema. Also, ich glaube, man muss grundsätzlich immer sehen, dass nichts Risikolos ist. Das muss man so sagen. Also, wenn man versucht, jedes Risiko auf Null zu reduzieren, ist man handlungsunfähig, und das ist bei den Daten eigentlich auch so. Ich könnte das natürlich so machen, dass ich sie in ein Fort Knox, sozusagen packe, nicht mal mehr die eigenen Leute ran lasse und das alles da irgendwie einschließe. Aber dann kann ich die Daten eben auch nicht nutzen, weder selber, noch kann ich sie irgendwie nutzbar machen in einem Ökosystem, wo sie dann noch sogar ihren höheren Mehrwert entfalten. Also, ich muss letzten Endes halt mit dem Data Sharing ein gewisses Risiko eingehen. Auf der anderen Seite ist es eben so, dass halt Informationssicherheitstechnologien sich immer weiterentwickeln und gerade beim Datenaustausch, bei dem Beispiel von Catena zum Beispiel auch State of the Art Sicherheitstechnologien verwendet werden. Aber, und das halte ich sogar für wichtiger, dass neben der Security eben halt auch die Datensouveränität, Volker hat das schon angesprochen, gewahrt ist, dass ich also selber bestimmen kann, wer was mit den Daten machen kann, und sie werden eben auch nur dann getauscht, wenn ich tatsächlich von jemandem vertrauenswürdigen angefragt werde. Also, ich bin eben nicht gezwungen, sie in Hände Dritter per se zu geben, sondern teile sie eben halt nur im Kreise von vertrauten Partnern. Das ist etwas, was auch eine Anforderung an diese Data Spaces immer war, dass ich eben nicht gezwungen bin, meine Daten in einen großen Data Lake zu kippen, der von jemandem Dritten betrieben wird, der dann eben halt auch noch die Data Governance Regeln, festlegt. Man muss auf der anderen Seite, und deshalb hatte ich eingangs gesagt, es ist auch ein nicht einfaches Thema. Es wird dann immer schnell geschimpft auf die großen Cloud Plattformanbieter, und die sind ja dann monopolistisch und so weiter. Natürlich haben sie auch eine große Marktmacht. Das ist völlig klar und auch unstrittig. Aber jeder möchte überlegen, ob er in der Lage und Willens ist, die gleichen Aufwendungen für Informationssicherheit zu leisten, die diese Cloud-Plattformbetreiber leisten. Ich würde mal behaupten, dass die meisten Unternehmen dazu gar nicht in der Lage sind, diesen Level an Security zu erreichen, den eben die großen sogenannten Hyperscaler erreichen. Also insofern ist das immer ein zweischneidiges Schwert, und weil es so zweischneidig ist, muss man eben immer anschauen, welchen Anwendungsfall habe ich eigentlich gerade, welche Daten sind dafür erforderlich, und welche Kritikalität haben diese Daten für mich? Und da, wo ich sage, naja, das ist irgendwie etwas, was gut wäre, auch schon blöd, wenn es irgendwo in falsche Hände kommt, aber es ist nicht dramatisch, da kann ich auch Public-Cloud-Plattformen verwenden und so weiter. Aber da, wo es eben halt sehr kritisch ist, da muss ich eben halt ein höheres Schutzniveau und einen höheren Vertrauensschutz halt gewährleisten, und insofern ist die Antwort eben meistens nicht so eindimensional. Aber wie gesagt, ich glaube, wenn man da strukturiert rangeht und das eben auch analytisch macht, dann kann man für sich da auch den richtigen Weg als Unternehmen finden.
Volker Lang: Ich sag mal, die kurze Reaktion wäre, und deshalb machen wir das genau so, dass ist in der Tat so, es geht um Vertrauen und vielleicht um das zu ergänzen, das komplette Geschäftsmodell von Microsoft oder auch AWS hängt davon ab, dieses Vertrauen nicht zu brechen. Deshalb stecken die einen Großteil ihrer Energie und ihrer finanziellen Mittel genau darein, das abzusichern. Zu glauben, dass, völlig egal, was wir tun, wir auch nur im Ansatz da mithalten könnten, ist völlig naiv. Also, Angst vor Cloud-Plattformen aus der Perspektive von Vertraulichkeit halte ich für für nicht besonders rational. Wir haben andere Themen. Ich sag mal, wenn ich einen Hochofen habe, und ich habe eine IT-Unterstützung für diesen Hochofen, dann habe ich vielleicht Probleme mit der Verfügbarkeit, weil die Cloud ist ganz woanders. Die ist in Frankfurt oder in Amsterdam oder sonst wo, aber jedenfalls nicht in Duisburg. Das heißt, es gibt viele Gründe, Dinge nicht in der Cloud zu tun. Ich sag mal, die Sorge davor, dass vertrauliche Daten öffentlich werden, wäre nicht die rationalste. Klar ist, dass wir hohe Standards haben. Es gibt Gesetzgebungen, wir sind ganz besonders vorsichtig, wenn es um personenbezogene Daten geht, aber die braucht man auch meistens nicht. Für die wenigsten Dinge, die wir gerade besprochen haben, brauche ich personenbezogene Daten.
Boris Otto: Ich glaube auch, was du eben gesagt hast, das ist auch ein Stück weit eine Chance für die Deutsche Industrie oder vielleicht für Deutschland, Europa generell. Weil also, die großen Cloud basierten Datenplattformen werden wahrscheinlich auch in Zukunft von den großen Plattformanbietern gestellt werden, weil die das einfach, das muss man eben auch sagen, auch gut können. Man muss ja auch eben die Fähigkeit, dass man haben, sowas zu entwickeln, das auch nicht ganz trivial. Aber wie das Internet selbst werden Dateninfrastrukturen sich auch verteilen, weil die Welt verteilt ist, du hast es angesprochen. Es gibt eben Hochöfen in Duisburg, und die stehen eben nicht irgendwo in Frankfurt, Amsterdam oder da, wo es kalt ist, am Polarkreis, weil die Kühlung da leichter gemacht werden kann. Das heißt, wir müssen eigentlich dahin kommen, dass wir, sagen wir mal, so ein Kontinuum haben zwischen zentralen, großen Cloud- Plattformen, die dann irgendwie in Amsterdam oder Frankfurt stehen, und sogenannten Edge-Lösungen, die eben dort stehen, wo der Prozess passiert oder das Produkt ist, und gerade an der Edge, das ist aus meiner Sicht ein Bereich, wo die Deutsche Industrie und aber auch die Deutsche Software Branche und die europäische Software Branche unheimlich viel gewinnen können, weil wir da einfach den Vorteil haben, da, wo man nah am Prozess und am Produkt ist, da muss man nämlich auch noch wissen, was da eigentlich passiert. Also, man braucht Expertise, und das ist das, was die, sagen wir mal, domain-agnostischen Plattformanbieter meistens gar nicht haben und gar nicht haben wollen, weil das nämlich nicht so skaliert nach ihrem Geschäftsmodell. Und das ist etwas, wo wir gewinnen können, weil es Zehnerpotenzen mehr von diesen Edge-Lösungen geben wird und Instanzen, als es zentrale Cloudplattformen geben wird.
Volker Lang: Das ist auch genau das, was uns beschäftigt. Du kriegst sicherlich, sagen wir mal, ein KI-Modell, was ist so ein schönes Beispiel, ein Foto von einem Schokocroissant von einem Faultier unterscheiden kann. Das kannst du sozusagen von der Stange kaufen. Das sind dann immer die die klassischen Cloud Beispiele. Das ist aber nicht das, was wir brauchen. Wir brauchen letzten Endes Modelle, die sich mit Antriebsströmen, mit Drücken, mit Temperaturen beschäftigen, und das passiert wirklich alles vor Ort an der Anlage. Das ist auch vor Ort an der Anlage zu trainieren, weil du kriegst diese Modelle nicht transportiert. Da gibt es ganz, ganz viel, was wir tun müssen, aber die Technologie dafür zu entwickeln, das können gerne andere tun.
Boris Otto: Und da ist Deutschland auch wirklich weit vorne, also gerade in der Sensorik zum Beispiel oder Kamera, Bilderkennung ist wahnsinnig, was letzten Endes in Realtime passiert, gerade in der Intralogistik, wo man eigentlich nicht mehr scannt, sondern wirklich Kameras hat, die letzten Endes halt die Artikel, die da in wirklich hoher Geschwindigkeit auf dem Band vorbei gefördert werden, identifizieren. Das ist etwas, wo wir wirklich gut sind.
Christine Launert: Aber Arbeitsteilung, wie es eigentlich schon immer in der Wirtschaft war, jeder macht das, was er kann und vernetzt sich damit.
Boris Otto: Ja, ich glaube, das stimmt. Ich glaube, man muss eben die Möglichkeiten erkennen, man muss in der Lage sein, auch dynamisch auf, sagen wir mal, sich die verändernden Markt- und auch Technologie-Umgebungen einstellen zu können, und dann muss man für sich bewerten, so wie du gesagt hast, ist das etwas, was man selber macht, weil es eben halt zur Kernkompetenz gehört oder wirklich zu dem, was man, ja, wo man sich also zum Alleinstellungsmerkmal, was man nicht externalisieren kann? Oder ist das, was, was man zukauft von einem vertrauenswürdigen Partner? Und letzten Endes ist diese Überlegung auch nichts neues. Das macht man schon seit, keine Ahnung, wahrscheinlich seit 70 Jahren, dass man sich überlegt, was tue ich eigentlich selbst, und wo habe ich Partner, von denen ich diese Leistung beziehen?
Christine Launert: Was gehört zu meinem Geschäftsmodell und was nicht?
Volker Lang: Da hast du auch die Anknüpfung zu deiner Eingangsfrage, was denn hier eigentlich mit dem Wirtschaftsstandort und der Region Rhein-Ruhr ist, weil die gute Nachricht ist, dass du ganz viel von dem, was du brauchst, an Kompetenzen und Lösungen, an Partnern, an Hochschulen findest du hier im Umkreis von 50 Kilometern. Ehrlicherweise den Cloud Provider nicht, da müssen wir ein bisschen weiter gucken, aber den Rest können wir selbst.
Christine Launert: Da habe wir eine schöne Vernetzung hier.
Boris Otto: Also, das ist tatsächlich so. Wir haben, weil du das gerade ansprichst, also bei den großen Cloud-Plattformen sind die Amerikaner und die Chinesen halt weit vorne, und das ist wahrscheinlich auch nicht mehr einholbar, das muss man so sagen. Aber es gibt eben gerade an der Edge sehr viele interessante Firmen in Deutschland, die da sehr gute Angebote machen. Wobei, jetzt muss ich das, was ich eben gerade vor zehn Sekunden gesagt habe, vielleicht bisschen revidieren, weil wir ja schon auch von der Schwarz Gruppe, um den Namen auch zu nennen, zumindest halt mit STACKIT, einen ganz interessanten Anbieter aus Deutschland haben, der auch das Ziel verfolgt, tatsächlich den großen da Dampf zu machen und Konkurrenz zu machen, und da würde ich sagen, das ist nicht aussichtslos.
Christine Launert: Man sollte es auf jeden Fall versuchen.
Volker Lang: Ja, wir drücken die Daumen.
Christine Launert: Dann würde ich jetzt noch ein bisschen in die Zukunft schauen und eine Frage an euch beide noch stellen, weil ihr euch ja nicht nur mit allen Facetten der Digitalisierung beschäftigt, sondern jetzt auch schon ganz viel unseren Hörerinnen und Hörern erzählt habt. Werden wir irgendwann oder sogar schon bald die denkende Maschine haben, die mit uns lebt, die mit uns kommuniziert, die Alltagsprobleme für uns löst, ähnlich Science Fiction Figuren?
Volker Lang: Ja, so Science Fiction ist das gar nicht so, denk dir Siri mit Körper, dann bist du ja nah dran, also, wenn man ehrlich ist. Ich glaube, dass es heute schon so ist, dass KI in ganz, ganz vielen Produkten drin steckt. Du hattest eben ein Beispiel. Ich habe auch, ich habe 19, weiß ich nicht 99, meine erste Waschmaschine, da stand Fuzzy Logic drauf, wen auch immer das damals beeindruckt hat und was auch immer das Ding mit Fuzzy Logic gemacht hat. Aber das fand ich total lustig, weil das würde man heute auch alles unter KI laufen lassen. Und das heißt, ich glaube, dass wir viel länger schon mit KI leben, ohne dass wir uns dessen bewusst werden. Also, du hast auch gar keine Chance, ehrlicherweise, auch den Teil des Hypes mal zu bewerten. Du kriegst doch als Konsument von KI-Automatisierung gar nicht mit, was das für nen Algorithmus ist. Also weißt du, wie die Google Suche funktioniert? Also heute und vor 20 Jahren? Merkst du gar nicht. Und wir haben das ganze Thema Sprache, wir haben das Thema Siri, wir haben das Thema Alexa, wir haben das Thema autonomes Fahren. Wenn du sozusagen das einzige, was eigentlich fehlt, ist, quasi diese ganze Intelligenz und diese ganze Digitalisierung, jetzt noch in irgendwas körperähnliches sozusagen reinzudenken, was dann, weiß ich nicht, morgens neben dir aufwacht und dir dann Frühstück macht. Der Teil fehlt ehrlicherweise bei uns zum Beispiel. Wenn du jetzt nach Japan guckst, was ich selten tue, aber ich habe das Gefühl, die sind schon näher dran, aber ich weiß nicht, ob das kommt, aber das wird so schrittweise sein, dass es sich dann nicht komisch anfühlt, wenn es da ist.
Boris Otto: Ja, also ist immer spannend, ein bisschen zu überlegen, was die Zukunft so bringt. Ich meine, Vorhersagen sind immer mit Vorsicht zu genießen, insbesondere wenn sie die Zukunft betreffen. Aber ich glaube schon, also wir haben so überlegt, was sind so, also du hast ja gefragt, selbst denkend, da wäre ich also, es kommt uns dann wahrscheinlich so vor, als wäre selbst denkend. Aber es ist eben halt nur eine unglaublich hochperformante, so wie du gesagt hast, Musteranalyse und Mustererkennung und dann eben halt auch verbunden mit, was man vor 10 Jahren mal so Recommendersysteme genannt hatten Also, Leute, die so sind wie sie, haben nicht nur dieses Buch gekauft, sondern auch jenes, und das eben halt in einer, sagen wir mal, ambienten Art und Weise, die uns einfach umgibt. Ich glaube zum Beispiel auch, dass halt ein ganz großer Treiber sein wird die Gaming Industrie, also alles, was wir so mit industriellen Metaverse oder Metaversum bezeichnen, hat aus meiner Sicht den größten Innovationsfortschritt aus diesem Bereich. Und wenn ich also an unsere Kinder denke, die, muss ich sagen, das ist die reale Welt. Das sehe ich immer dann, wenn ich meine Kreditkartenabrechnung anschaue, weil da wird tatsächlich auch, da werden Werte gehandelt, und ich glaube, das wird schon kommen, dass uns sozusagen digitale Technologie einfach umgibt und wir das einfach, naja, ohne große Gedanken uns zu machen, auch anders nutzen als heutzutage. Weil, was einfach schräg ist, muss man sagen, ist, dass wir immer noch mit einer QWERTZ-Tastatur einfach ne Schnittstelle zur Technik haben. Sicherlich war die Software-Tastatur schon ein großer Fortschritt, aber das kann es einfach irgendwie nicht sein. Also da wird, glaube ich, ne ganze Menge kommen, und gerade in dieser Verschmelzung zwischen Virtual Reality, Augmented Reality und der Realität selber, das wird, glaube ich, tatsächlich einen großen, großen Schritt machen. Und es wird eben auch so sein, dass die Generation, die damit aufwächst, das selbstverständlich einfach nutzen wird.
Volker Lang: Ich glaube, die entwickeln eine ganz andere Haltung zum Thema KI. Wenn wir über KI nachdenken, auch im Dialog mit Kollegen, dann ist KI immer, ich sag mal, ein Assistenzsystem, das hilft mir dabei, Entscheidungen zu treffen. Das kann man so machen, und das fühlt sich als Mensch erst mal gut an. Aber ehrlicherweise ist das völlig irrational, dass derjenige das letzte Wort hat, der die geringere Informationsverarbeitungskapazität hat. Also, ich sag mal, wenn ich sozusagen als KI-Modell terabyteweise Daten in Millisekunden analysiere, und ich sage linksrum, und dann guckt sich das einer an und sagt, für mich fühlt sich aber rechts besser an. Das macht ja keinen Sinn, und ich glaube, die Power von KI hängt davon ab, wie viel Autonomie wir ihr zutrauen, und das ist am Ende auch ein Generationen-Ding. Das glaube ich auch. Weil, wir können versuchen, uns dahin zu verändern. Das sollten wir auch tun. Aber alles, was nach uns kommt, macht es sozusagen, denkt das sozusagen von Anfang an von der anderen Seite des Spektrums her kommend.
Boris Otto: Ich glaube, interessant wird sein, und das ist ja auch die Diskussion gewesen in der Verabschiedung des AI-Acts oder KI-Gesetzes, welche Entscheidung eigentlich tatsächlich automatisch getroffen wird. Also ich fand ehrlich gesagt, auch wenn ich jetzt nicht 100 prozentig ganz nahe dran war, also ich war ziemlich nah dran am Data Act und solchen Geschichten, aber beim KI-Act hab ich das ein bisschen beobachtet. Ich fand aber tatsächlich dann, worauf man sich geeinigt hat, schon relativ nachvollziehbar und auch eigentlich ganz gut ausbalanciert, dass man für bestimmte Bereiche gesagt hat, also, diese Entscheidung sollten wir uns vielleicht noch als Menschen selber vorbehalten, aber alles, was letztenendes unkritisch ist, wenn sie mir, wie gesagt, so vorschlägt, ich guck mal, das wäre auch ein tolles Buch, was du bestellen kannst, muss ich sagen, habe ich noch nie einen schlechten Vorschlag gesehen. Da ist es dann okay. Aber dass man wirklich sich überlegt, in welchen Lebenslagen oder für welche Art von Entscheidung wir eigentlich die, ich sag mal, Hoheit behalten wollen, das fand ich nicht so ganz doof, muss ich sagen. Und auch die Tatsache, dass man die Foundation Models auch, sagen wir mal, auch offen gestaltet, um letzten Endes damit auch überhaupt Humus zu haben für letzten Endes bessere KI-Algorithmen. Also ich fand das eine ganz gut balancierte Entscheidung, muss ich sagen.
Christine Launert: Also bleiben wir gespannt, wer das Rennen der intelligenzen macht.
Boris Otto: Ja, da gibt es ja diese schöne Grafik, wo man so auf dem Zeitstrahl einträgt, dann, das da erst die menschliche Intelligenz die Konstante ist.
Volker Lang: Gegen exponentielles Wachstum ist immer schwierig. Wir haben, glaube ich, so im Jahre der Evolution haben wir ein paar 100 Milliliter Gehirnvolumen dazugewonnen, aber das wird nicht reichen.
Christine Launert: Vielen Dank.
Boris Otto: Ja gerne
Volker Lang: Dir vielen Dank, hat Spaß gemacht.
Christine Launert: Digitalisierung ist also keine Bedrohung und künstliche Intelligenz auch keine vorübergehende Erscheinung. Beides gehört ohnehin schon zum Alltag der Next Generation Steel. Vielen Dank an meine Gäste für den interessanten Austausch, danke euch fürs Zuhören. Ich hoffe, es hat euch gefallen. Falls ja, abonniert gekocht, gewalzt, veredelt gerne auf Apple, Spotify oder einer anderen Podcast Plattform, und lass uns auch gerne Feedback da, zum Beispiel via Mail an [email protected]. Ich freue mich auf weitere spannende Stahlthemen mit euch.
Folge 10: Innovationen – Zukunft für den Industriestandort Deutschland
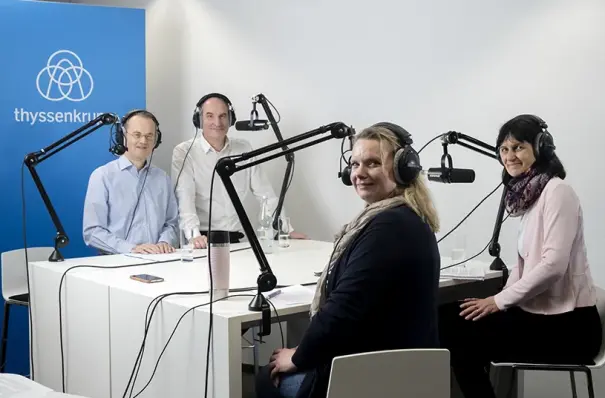
Innovationen sind wesentlicher Teil des Fundaments für den Industriestandort Deutschland und die globale Wettbewerbsfähigkeit. Sie sind Treiber der grünen Transformation und damit auch der Zukunft der Stahlbranche.
In unserer neuen Podcast-Folge von „gekocht, gewalzt, veredelt“ sprechen wir über die Bedeutung von interdisziplinärer Vernetzung zwischen Forschung, Lehre und Wirtschaft, betrachten die richtige Zusammenstellung von Innovations-Teams und bieten spannende Einblicke in die Innovationsprozesse bei thyssenkrupp Steel.
Im Gespräch mit Christine Launert sind diesmal Prof. Dr. Jutta Lommatzsch, Dekanin des Fachbereichs Wirtschaft der Hochschule Ruhr West, Niels Lohmeyer (Leiter Innovation) und Dr. Matthias Weinberg (Leiter des Competence Center Metallurgie (CCM).
Christine Launert: Liebe Zuhörerinnen, liebe Zuhörer! Willkommen zu einer neuen Folge von gekocht, gewalzt, veredelt, dem Podcast rund um das Thema Stahl. In dieser Folge spreche ich mit unseren Gästen über Innovationen. Wo kommen sie her? Welchen Wert haben sie für Unternehmen und den Wirtschaftsstandort Deutschland, und wie viel Innovation braucht ein Unternehmen? Wir hinterfragen, wie Bildung und Wirtschaft eine Innovationslandschaft fördern und nutzen können und welche Rolle die Politik dabei spielt. Ich spreche heute mit drei Menschen, die sich täglich mit der Weiterentwicklung des "Heute" beschäftigen und sich mit einem "das haben wir immer so gemacht" nicht zufrieden geben. Ich freue mich sehr, Professor Dr. Jutta Lommatzsch begrüßen zu dürfen. Sie lehrt an der Hochschule Ruhr West in Mülheim an der Ruhr allgemeines und spezielles Wirtschaftsrecht und verantwortet als Dekanin Forschung und Lehre des Fachbereichs Wirtschaft. Auch begrüßen darf ich meine beiden Kollegen Niels Lohmeyer und Dr. Matthias Weinberg. Nils Lohmeyer leitet den Bereich Innovation bei tyssenkrupp Steel, durch seine Position schon prädestiniert für unsere aktuelle Folge. Dr Matthias Weinberg verantwortet den Bereich Competence Center Metallurgie und damit Innovation mit weitreichenden Folgen für die Stahlherstellung und ihre Transformation. Mein Name ist Christine Launert. Ich bin Pressesprecherin bei thyssenkrupp Steel. Schön, dass ihr dabei seid.
Christine Launert: Frau Professor Lommatzsch, bevor wir einsteigen, sie verantworten Forschung und Lehre an ihrer Hochschule. Was bedeutet das?
Jutta Lommatzsch: Ja, Forschung und Lehre sind die Kernbereiche einer Hochschule und machen ganz viel Freude und sind vor allen Dingen verzahnt. Wir setzen in der Lehre auch unsere Forschungsergebnisse ein, und wir forschen Sachen, die wir dann in der Lehre auch weiter aktiv betreiben. Forschung und Lehre sind sehr, sehr wichtig, denn Bildung ist die Grundlage für alle weiteren beruflichen Tätigkeiten, und wir glauben, dass wir an unserer Hochschule einen großen Beitrag leisten können.
Christine Launert: Da komme ich doch gleich zu ihnen, Herr Lohmeyer. Sie leiten den Bereich Innovation. Was passiert denn bei ihnen, und was machen ihre Mitarbeitenden?
Niels Lohmeyer: Bei uns passiert sehr vieles: Die Produktentwicklung für den Stahlbereich, die Anwendungstechnik, also wie wird der Stahl verarbeitet bei unseren Kunden, wie wird geschweißt, gefügt, geklebt? Als Beispiel, aber auch zwei große Dienstleistungsbereiche, nämlich die Chemie und die Werkstoffprüfung sind im Bereich Innovation. Wir halten die Produktion am Laufen, vom Erz bis zum Fertigen Coil in chemischen Prozessen, aber auch in der Werkstoffprüfung, und last but not least ist das gesamte Thema Patentschutz und Patentanwälte auch im Funktionsbereich Innovation.
Christine Launert: Herr Dr. Weinberg, was hat ein Kompetenzzentrum Metallurgie mit Innovation zu tun, und wie innovativ kann Metallurgie sein?
Matthias Weinberg: Das ist eine sehr gute Frage, was das mit Innovation zu tun hat. Eigentlich kommt die Innovationsbestrebung tatsächlich von auswärts. Seit über 500 Jahren sind wir systematisch dabei, die Kohlenstoff-Metallurgie weiterzuentwickeln. Da haben wir eine hervorragende Präzision in Steuerung und Kontrolle der Prozesse mittlerweile erlangt. Aber wir haben leider alle unsere Prozesse auf Kohlenstoff basiert entwickelt, und weil wir jetzt kein Kohlendioxyd mehr mit unseren Prozessen emmitieren wollen, sind wir gezwungen, alles auf Wasserstoff umzustellen, und das ist natürlich ein signifikanter Paradigmenwechsel, der sich daraus ergibt. Das heißt, im Grunde ist das, was wir machen, mal eben 500 Jahre metallurgische Entwicklung neu aufrollen.
Christine Launert: Vielen Dank. Damit sind wir schon mitten drin in unserem Thema "Innovationen". Damit komme ich schon zu unserer ersten Frage. Wie sieht denn die derzeitige Innovationslandschaft der deutschen Marktwirtschaft überhaupt aus?
Jutta Lommatzsch: Also, ich denke, insgesamt muss man das auf jeden Fall positiv sehen. Die Innovation ist in Deutschland ein ganz treibender Faktor für unsere Wirtschaft. Das war so, und das ist auch immer so noch, wobei sich die Randbedingungen natürlich ein wenig geändert haben. Wo man meines Erachtens noch dran arbeiten muss, ist, dass Innovationen noch sehr, sehr viel von großen Unternehmen ausgehen, Deutschland aber ja auch geprägt ist durch den Mittelstand, und im Mittelstand einfach noch zu wenig Innovation ist. Die Bundesregierung bemüht sich ja auch, den Mittelstand mit reinzuholen durch Förderprogramme und auch durch eine Zukunftsstrategie, was auf jeden Fall förderlich ist. Das zweite, was ich wichtig finde, ist, oder nicht nur ich wichtig finde, die Innovationslandschaft ist auch branchenspezifisch geprägt, das heißt, die Branchen sind unterschiedlich innovativ, und da ist es aber einfach wichtig, noch viel mehr Branchen mit ins Boot zu holen. Beispielsweise die Pharmaindustrie oder auch die Stahlindustrie sind natürlich führend in der Innovation. Aber es gibt einfach, wenn man an der Hochschule arbeitet, nicht nur die beiden Zweige, sondern noch viel mehr, und da kann sich noch deutlich mehr positiv entwickeln, wenn eben auch entsprechend gefördert wird, beispielsweise durch Steuervergünstigungen, durch günstige Kreditbedingungen oder sonstige Förderungen auch des Mittelstands.
Christine Launert: Dann kommen wir mal von der Makro- in die Mikroökonomie. Wie wichtig ist denn Innovation überhaupt für Wirtschaftswachstum und auch eben für die Wirtschaft, um selber wachsen zu können?
Niels Lohmeyer: Da würde ich vielleicht mal einsteigen, wenn ich das jetzt hier erst mal für uns auf den Stahl beziehe, dann haben wir Gott sei dank hier mitten im Ruhrgebiet eine sehr lebendige Forschungslandschaft. Ich bin selber in diversen Beiräten von Forschungsinstituten, und was ich sehr schätze, ist die industrielle Gemeinschaftsforschung, die auch vom Bundeswirtschaftsministerium intensiv gefördert wird, und da gelingt es sehr gut, eine Kombination aus Großunternehmen und KMUs und Hochschulen zu vernetzen. Dieses Thema vernetzen, und ich würde sagen, auch People-Business, Ideen, neue Innovationen entstehen ja nicht am Grünen Schreibtisch, sondern durch Vernetzung und durch kreative, kluge Ideen, neugierige Köpfe, und da haben wir, glaube ich, eine sehr lebendige Forschungslandschaft in Deutschland, aber auch im Ruhrgebiet.
Christine Launert: Damit wären wir so ein bisschen bei dem Thema "Wie funktioniert Innovation überhaupt?" Man stellt sich immer den Entwickler, die Entwicklerin vor, im Elfenbeinturm, fernab von der Realität. Ist das wirklich so, oder bedarf es nicht viel mehr, auch wie sie es gerade angesprochen haben, Herr Lohmeyer, der Zusammenarbeit verschiedener Disziplinen, verschiedener Bereiche, um überhaupt zu einer Innovation zu kommen?
Niels Lohmeyer: Aus meiner Sicht unbedingt, aber ich denke, Matthias Weinberg kann gleich für die Prozesse noch mehr etwas sagen. Da ist die Vernetzung insbesondere mit Produktionsbetrieben sehr entscheidend. Bei mir die Produktentwicklung ist vernetzt mit den Kunden, mit Forschungsinstituten, mit Hochschulen, intern mit der Produktion, mit der Planung. Also eigentlich ist es weniger eine Entwicklung alleine an einem grünen Schreibtisch, sondern eher managen eines Entwicklungsteams. Das ist dann auch eine andere Herausforderung als das, was man häufig in der Hochschule lernt und gelernt bekommen hat. Wie können Hochschulen auf dieses dann auch besser vorbereiten?
Jutta Lommatzsch: Ich bin überzeugt, dass sich Hochschulen da schon sehr, sehr geändert haben, denn das ist genau unser Ansatz. Also, ich selbst bin ja Juristin, habe klassisch die ganzen Fächer gelernt, und von Vernetzung war wenig zu spüren, und Interdisziplinarität gab es höchstens, dass man eben bürgerliches Recht und Strafrecht hatte, das ist aber nicht sonderlich interdisziplinär. Und genau das hat sich ganz entscheidend geändert. Also beispielsweise ist ein Kennzeichen unserer Hochschule Ruhr West, dass alle Studiengänge interdisziplinär sind, das heißt, alle technischen Studiengänge haben auch wirtschaftliche Elemente, denn es lohnt sich nicht, wenn man ein Produkt herstellen kann, die Prozesse kennt, aber das nicht wirtschaftlich an den Markt bringen kann. Und genauso umgekehrt haben unsere Wirtschaftsstudiengänge alle technische Elemente. Das heißt, wir haben das aufgenommen ins Studium, und das ist uns total wichtig, und so arbeiten auch unsere vier Fachbereiche ganz eng zusammen. Wir haben eine Matrix-Struktur, das heißt, wir importieren und exportieren Module, um genau das zu gewährleisten, was sie gerade gesagt haben, die Vernetzung, und um auch zu gewährleisten, dass dann von Fachleuten auch die Lehre gemacht wird. Also, wir stellen uns nicht hin und meinen, wir könnten jetzt Ingenieurwissen vermitteln, können wir nicht, sondern im Gegenteil, der Ingenieur kommt dann in ein Import Modul und unterrichtet. Also da sind wir viel, viel weiter als zur Zeit unseres Studiums.
Matthias Weinberg: Ja, vielleicht kann ich ein bisschen erzählen, wie das in den vergangenen fünf, fünfeinhalb Jahren gelaufen ist. thyssen ist da mit unter den ersten. Bei der Dekarbonisierung der Stahlherstellung spielen wir ganz vorne mit. Wie konnte das passieren? Ein eigentlich konservativ aufgestelltes Unternehmen hat auf einmal eine Herausforderung, dass an die Unternehmung herangetragen wird, die nie dagewesen ist. Das nächste, was passieren muss, es müssen Leute da sein, die Anfangen, dort Diskussionen zu führen "Wie könnte es gehen? Was geht nicht? Was geht? Wo sind Randbedingungen? wo sind zwingende, ich nenn sie mal einfach, Restriktionen einzuhalten? Wie sieht das aus mit der Wirtschaftlichkeit? In welchem Rahmen kann man eigentlich denken?" Und da ist Interdisziplinarität ein Riesen, Riesending. Weil die Personalabteilung so erstaunt war, nach welchen Qualifikationen ich dieses erste Team, diesen Nukleus zusammengestellt habe, haben sie den treffenden Namen Oceans Eleven genommen für dieses Team. Nicht, dass da jetzt Fluchtwagenfahrer und Panzerknacker bei gewesen wären, aber es war sehr, sehr interdisziplinär. Und das ist eigentlich der Schlüssel zum Erfolg. Neben der Interdisziplinarität muss man darauf achten, meiner Überzeugung nach, dass man Kommunikation hochhält. Daher sind in diesen Entwicklungsabteilungen, die ich da führe, Anwesenheitspflichten, die, ich nenne es mal einfach, aus der Norm ragen. Viele, viele seit der Corona Krise, viele, viele Kollegen pflegen in großem Umfang Homeoffice zu machen. Das funktioniert für die Innovation nur sehr, sehr beschränkt. Weil die Innovation so funktioniert, dass ein Problembewusstsein in ein Kollektiv getragen wird. Es gibt ein Problem, das müssen wir lösen, und dann fängt das Team an zu denken. Das Team weiß sehr gut, wer was kann und wer was nicht kann, und dann gehen die auf denjenigen, der die beste Lösung offerieren kann, zu. Und dann gibt es eine Kaffeeküchen-Dynamik, so nenne ich das. Da steht dann einer in der Kaffeeküche an der Kaffeemaschine und sagt zum anderen, der daneben steht, hör mal, da ist mir was verrücktes eingefallen gestern Nacht, das wäre ein Thema, da würde niemand ein Videocall führen. Das passiert wirklich per Zufall. Das heißt, diese gesteuerten Zufälle sind ganz, ganz wichtig. Am nächsten Tag steht dann nämlich der Kollege in der Kaffeeküche und sagt, so verrückt ist das gar nicht. Ich habe auch drüber nachgedacht, und dann ist die erste Idee, ein kleiner Nukleus, geboren, und dann wird es ins Team getragen. Dann wird die ausstrukturiert, dann werden die KOs abgeklopft, dann werden Lösungen gesucht für Detailprobleme, und so funktioniert eine Innovation. Und wenn dieses Team, und das macht das Ruhrgebiet so interessant für Innovationen, wenn das Team alleine nicht weiterkommt, was immer Ruckzuck der Fall ist, es sind ja nur wenige Leute, die nicht über alle Fachgebiete komplett bescheid wissen. Die brauchen auch Hilfe, und die Leute, die holen sich dann von auswärts Hilfe, und dafür ist das Ruhrgebiet natürlich ein idealer Fischteich. Man hat in Schlagdistanz, ganz, ganz kurze Entfernungen, hat man wirklich Spezialisten für unglaubliche Details, die man sonst alleine nie ausgearbeitet bekommen würde, und das ist eigentlich ein Erfolgsschlüssel für Innovation im Ruhrgebiet.
Niels Lohmeyer: Ich würde schon noch mal ergänzen wollen. Ich glaube, extrem wichtig für eine erfolgreiche Innovation und Entwicklung, die dann auch hinterher ein Business wird, ist, ein Team zusammenzustellen, was sich in seinen Fähigkeiten ergänzt. Weil Kreativität kann man nicht anerziehen, es gibt aber, ich nenne sie immer die Trüffelschweine, die sind so kreativ, die Sprühen vor Ideen, sind aber häufig nicht die richtigen, die Idee dann hinterher bis zum Ende umzusetzen. Also, da braucht man eigentlich den Umsetzer im Team. Und ich glaube, diese Mischung aus unterschiedlichen Fähigkeiten, die bestimmt den Erfolg einer Innovation, die macht es aber auch so spannend, weil man mit so vielen verschiedenen Leuten im Team zusammenarbeiten kann.
Jutta Lommatzsch: Ich glaube, genau das muss man eben auch erkennen und auch schon früh den Menschen vermitteln. Es ist ja so, dass die einzelnen Disziplinen ja auch sogar einzelne Sprachen haben und man sich ja am Anfang ein bisschen schwer tut in interdisziplinären Teams, weil man den anderen gar nicht richtig versteht. Der spricht ganz anders, der nimmt plötzlich nur Exceltabellen und schreibt nichts auf, und man muss sich erst mal daran gewöhnen. Das ist aber auch eben eine Aufgabe der vorgelagerten Bildung schon, dass man einfach zeigt, dass die Ergänzung so wichtig ist, dass Innovation nicht nur die Innovation des Produktes ist, sondern auch die Innovation der Arbeitsweise. Denn dieses ganz enge zusammenarbeiten und was interdisziplinär ist, und noch jemanden dazuholen, die eigenen Grenzen erkennen, das ist ja auch ein Fortschritt. Auch das ist eine Innovation, die Zusammensetzung der Teams, das Zusammenarbeiten, und das versuchen wir auch schon im Vorfeld an der Hochschule zu vermitteln.
Christine Launert: Also zwei ganz wichtige Grundlagen. Einmal, dass sich auch die Forschung, die Innovationstätigkeit selber weiterentwickelt und weiterentwickelt hat, und das zweite ist, über den Tellerrand hinauszuschauen, nicht alles selber können zu müssen und wirklich in einem großen Team zusammenzuarbeiten. Sie hatten es gerade schon angesprochen, Herr Weinberg. Das Ruhrgebiet ist eigentlich ein idealer Standort dafür. Wie einfach ist es denn überhaupt, über den eigenen Tellerrand hinauszugehen und zu sagen, hier haben wir eine Kompetenz, die fehlt diesem Team, die müssen wir uns dazu holen, und ist das Ruhrgebiet wirklich so prädestiniert dafür?
Matthias Weinberg: Ja, für mich ist es eigentlich das Ruhrgebiet ein idealer Nukleus, weil es auf einer sehr, sehr kleinen Fläche eine Unzahl an wirklich technisch hochversierten Instituten, Hochschulen, Spezialisten, kleine Mittelständler. Sie finden hier innerhalb von 100, 200 Kilometern im Umkreis einen Spezialist für wirklich alles. Die exotischsten Fragestellungen kriegen sie hier beantwortet. Und da sind wir ganz klar Nutznießer auch der mittlerweile für mich auch erkennbaren Skills, die die Hochschule den Absolventen, den Jungen vermittelt. das heißt, da eine, ich nenne es mal einfach, Kommunikationskultur zu pflegen, die nicht, wie es früher gerne der Fall war, wirklich fachbezogen im eigenen Carrè ein Spezialist sein, das zählt heute bei den jungen Leuten weniger als früher. Das ist tatsächlich so, dass ich dort aufgrund meines Alters eine Entwicklung beobachtet, die sehr, sehr positiv ist und eine Innovation wirklich befördern kann. Da ist eine Kommunikationsbereitschaft auch über die Grenzen hinweg schon aus dem universitären Umfeld, ich will nicht sagen, anerzogen, aber kultiviert.
Christine Launert: Frau Professor Lommatzsch, beobachten sie das an der Hochschule auch? Ihr Einzugsgebiet umfasst viele Studierende aus dem Ruhrgebiet oder auch von weiter weg?
Jutta Lommatzsch: Nein, unser Einzugsgebiet ist in der Tat lokal. Wir sind eine Hochschule für das Ruhrgebiet, also der Großteil der Studierenden kommt aus dem Ruhrgebiet, und die Studierendenschaft ist sehr, sehr divers. Das stellt uns vor Herausforderungen. Wir haben sehr viele Studierende der First Generation, für die eine Hochschule wirklich erstmal auch gelernt werden muss. Wir haben sehr, sehr viele Nationalitäten, die auch unterschiedliche Hintergründe haben, aber wir sehen das als Chance. Es ist teilweise nicht einfach. Man muss sagen, was die erste Schwierigkeit schon ist, ist, wir unterrichten in Deutsch, und das beherrscht halt nicht jeder, so, dass man auch hinterher einen akademischen Abschluss in deutscher Sprache erteilen kann, machen dann aber Zusatzprogramme und sagen einfach, jeder soll die Chance bekommen, und wir nutzen das eben auch da diese diversen Interessen einzuholen, und wenn man das nutzt und es schafft, die Studierenden zu begeistern, dann kann man auch innovativ was auf die Beine stellen.
Christine Launert: Zu meiner Zeit haben wenigstens die Partys einen wieder an die Uni gebracht, vielleicht fehlt das heute. Zu den Innovationen. Innovationen sind ja jetzt auch kein Selbstzweck. Also, wir sind zwar alles kreative Menschen, aber wir bringen ja keine Innovation an den Markt, weil es uns so viel Spaß macht. Innovationen sind ja auch nicht ganz risikoarm und auch nicht ganz günstig. Welchen Vorteil hat ein Unternehmen? Stärkt es die Widerstandsfähigkeit? Stärkt es die Marktfähigkeit? Wie sehen sie das?
Niels Lohmeyer: Vielleicht erst mal als Erklärung, wenn man sich die F&E-Projekte in der Produktentwicklung bei uns anschaut, dann machen wir den etwas kleineren Teil in der Grundlage, dann aber häufig mit Hochschulen zusammen als verlängerte Werkbank. Wir machen Vorentwicklung, und wir machen dann einen Start einer echten Produktentwicklung. Und eine Produktentwicklung starten wir nur, wenn ein Businessplan dahinter steht. Der Businessplan kommt über den Kunden und den Vertrieb und unser eigenes Produktmanagement dann an uns in der Innovation, und da wir eben auch begrenzte Entwicklungskapazitäten haben, priorisieren wir anhand des Nutzens, den wir uns vorstellen. Das kommt dann nicht immer 1 zu 1. Das ist die Natur einer Innovation und einer Entwicklung. Aber die Vorauswahl, mit welcher Produktentwicklung wir uns beschäftigen, die kommt immer aus dem Business Case heraus, und wir prüfen auch hinterher ab, inwieweit wir diese Prämissen des Plans da auch in den Folgejahren erreicht haben.
Matthias Weinberg: Ja, vielleicht kann ich ein bisschen was zur Prozessentwicklung sagen, wie sich das dort verhält. Es sind in der Prozessentwicklung schon seit Jahren, seit Dekaden sind es drei ganz klassische Treiber, die immer wieder Entwicklungen in Gang setzen. Das sind entweder Probleme mit der Umwelt, im Moment ein Riesenthema wegen CO2-armem Stahl. Dann sind es häufig Probleme tatsächlich mit den Kosten. Dass Prozesse nicht mehr kompetitiv sind, dass die Kosten einem weglaufen, dass man die nicht mehr wirtschaftlich führen kann, ist auch ein ganz, ganz beliebter Treiber. Oder aber Probleme mit der Qualität, dass Prozesse so schwierig zu kontrollieren sind, dass die Schwankungsbreite der normalen Prozessergebnisse tatsächlich eine Auswirkung auf die Produktqualität hat, das sind die ganz, ganz klassischen Treiber zur Prozessentwicklung. Für Prozesse haben wir aktuell natürlich dort, wenn man mal aufzeichnen will, wie es jetzt aktuell sortiert wird. Es gibt ja unheimlich viele Prozessoptimierungen, die in der Vergangenheit eben einfach daran gescheitert sind, dass sie kostentechnisch keine Verbesserung brachten. Und jetzt haben wir natürlich eine Situation, wo eine Tonne CO2 zu emittieren den Erwerb eines Emissionsrechts benötigt, und das wiederum verdreht natürlich die gesamte ursprüngliche Bewertung der Prozessverbesserung. Auf einmal habe ich eine Zusatzwährung CO2, die muss ich mit einpreisen und muss dann nochmal sämtliche Prozessverbesserungen, die in den vergangenen Dekaden, als Emissionsrechte noch preisgünstig waren, die Verbesserungen, die damals verworfen worden sind, müssen heute neu bewertet werden, und zwar vor einem noch anderen Hintergrund. Nicht nur einfach die direkten Emissionen zählen, sondern es zählt auch noch eine sogenannte Lifecycle Analysis. Das heißt also, es werden sämtliche mit dieser Prozessveränderung einhergehenden CO2 Emissionen in der gesamten Fertigungskette betrachtet. Brauche ich weniger Erz? dann muss ich natürlich auch weniger Erz verschiffen, weniger Erz transportieren, weniger im Bergbau gewinnen, weniger aufbereiten. Solche Ketten, die betrachten wir mittlerweile und benutzen das dann als Richtschnur für die Güte einer Prozessveränderung.
Jutta Lommatzsch: Ja, ich möchte auch gerne noch was ergänzen. Also, Innovation war ja jahrelang getrieben, insbesondere durch die finanzielle Betrachtung. Innovation wird gemacht, damit am Ende letztendlich mehr Gewinn stand, um es etwas vereinfacht auszudrücken. Und unsere Welt hat sich aber ja nur extrem verändert. Also insbesondere durch den Krieg, durch den Ukrainekrieg sind einfach Innovationen erforderlich im Bereich der erneuerbaren Energien, weil wir halt gesehen haben, dass Energie kein endloses Gut ist, was wir aus Russland beziehen können, und fertig ist es, sondern wir müssen uns umstellen. Und das zweite ist, dass der Klimawandel ja nun schon lange läuft, aber viel, viel mehr ins Bewusstsein der Leute gekommen ist. Also gerade heute konnte man hören, aktuell, die Erderwärmung hat im ganzen letzten Jahr 1,5 Grad überschritten. Das heißt noch nicht, dass das Ziel aus Paris verfehlt werden kann, weil man es dann doch etwas langfristig betrachtet. Aber es heißt einfach, es ist fünf vor zwölf, und damit ist die ganze Innovation ja eben nicht mehr nur getrieben durchs Geld, sondern wirklich, wie sie das gesagt haben, durch die CO2-Reduktionen, die absolut erforderlich sind und auch erforderlich sind, wenn sie eben nicht ganz so wirtschaftlich sind, wie man sich das vorher vorgestellt hat. Und man muss einfach Förderprogramme aufsetzen, was aber natürlich auch nicht ganz einfach ist, weil wir vorher die Corona Krise hatten, wo man ja auch unendlich viele Förderprogramme gemacht hat und am Ende dann eben merken musste, das ganze Geld, was man quasi in Umlauf gebracht hat und immer weitergebracht hat, ist eben auch nicht endlos, sondern die Schuldenbremse steht im Grundgesetz und muss einfach auch beachtet werden.
Christine Launert: Sie haben den Fokus jetzt sehr international gesetzt, und da sehen wir uns ja auch als Unternehmen, das im Ruhrgebiet zwar tätig ist und viele Standorte im Ruhrgebiet hat, aber im internationalen Wettbewerb steht, mit internationalen Kunden. International gesehen haben Unternehmen ganz unterschiedliche Herausforderungen, und das schließt Energieversorgung und andere Bepreisungen, sie sprachen es an Herrn Weinberg, die CO2-Zertifikate, ein. Wie wichtig ist denn auch die Förderung überhaupt von Forschung und Entwicklungen in der Deutschen Wirtschaft?
Matthias Weinberg: Die Frage ist im Grunde ganz, ganz einfach zu beantworten. Wenn ich die Folgen, die wir hier in unserer Zivilisation über technik und technische Hilfsmittel, wenn wir über die Folgen nachdenken, in Richtung CO2. CO2 ist Wohlstand. CO2 ist natürlich einen Lebensstandard, der sehr, sehr viel Energie verbraucht, den wir hier pflegen, und wenn wir die Folgen kontrollieren wollen, wenn wir die eindämmen wollen, wenn wir die beherrschen wollen, dann geht es ohne Technik nicht. Und die Technik von gestern wird uns dabei nicht helfen, sondern wir brauchen Technik für morgen, und dass die nicht vom Himmel fällt und dass man das auch keinen einzelnen Unternehmen aufbürden sollte, die Last einer technologisch gestalteten Zukunft, einer umgestalteten Zukunft alleine zu schultern, das ist für mich eigentlich selbstverständlich, das Klimawandel genauso wie Innovation eine gesellschaftliche Aufgabe ist, und daher sollten wir uns nicht scheuen, da Subventionsmittel für freizuschaufeln und auch mal die Frage zu stellen, in welcher Relation das zu unserem gesamten Wohlstand und der Zukunft unserer Kinder steht.
Jutta Lommatzsch: Der internationale Wettbewerb, der ist wichtig. Man muss einfach auch sehen, dass bei uns die Arbeitskräfte teuer sind, wir am Ende auch qualitativ hochwertige Produkte haben. Die Energiekosten sind relativ hoch, und auch die Steuern sind in Deutschland relativ hoch. Und damit wir verhindern, dass wir eben die ganze Produktion ins Ausland verlagern, wo möglicherweise dann sogar menschenunwürdige Bedingungen sind, ist es wichtig, dass einfach gefördert wird, denn ein Unternehmen kann nicht alleine Forschung und Entwicklung stemmen, bei den Rahmenbedingungen, die Unternehmen ansonsten in Deutschland haben. Es geht einfach nicht.
Niels Lohmeyer: Vielleicht auch nochmal eine Ergänzung, weil ich das in vielen Förderprogrammen sehe. Die Vernetzung wird dadurch auch gefördert, es ist nicht nur immer die reinen Finanzen, sondern die Mischung aus kleinen mittelständischen Unternehmen, Hochschulen, Forschungsinstituten, großen Unternehmen, die dann in einem öffentlichen geförderten Entwicklungs- und Forschungsprojekt zusammenarbeiten. Und das ist dann auch manchmal ein Raum, der einfach geboten wird über die diversen Forschungskooperationen, in denen dann Player zusammenkommen, die normalerweise vielleicht nicht zusammenkommen würden. Deutschland hat nicht viele Rohstoffe, Deutschland hängt von der Bildung, hängt von der Entwicklung neuer Prozesse und neue Produkte elementar ab, und da eine Anschubfinanzierung in Geld, aber auch Vernetzung zu schaffen, ist überlebensnotwendig.
Christine Launert: Jetzt wollen wir auch mal auf die innovativen Prozesse eingehen. Wir haben jetzt schon ganz oft drüber gesprochen, aber haben sie noch nicht ganz durchleuchtet. Deswegen, Stahlindustrie verursacht heute unheimlich viel CO2, Herr Dr. Weinberg, sie sprachen es an. Das wollen wir reduzieren. Da gibt es innovative Ansätze, die Prozesse komplett umzustricken. Wie genau sieht das aus, und wie genau ist man denn da hingekommen?
Matthias Weinberg: Oh, schwierige Frage! Jetzt muss ich ja schon sofort fragen, wie viel Zeit haben wir? Ich will es trotzdem versuchen, kurz zu machen. Eigentlich ist die Lösung, die Lösung des Kernproblems der Stahlherstellung, vergleichsweise einfach, aber nichts in der Technik, in der großindustriellen technischen Anwendung ist so einfach, wie es scheint. Am Hochofen entwickeln wir bereits seit mehreren 100 Jahren, und was wir da jetzt haben, ist natürlich ein, wenn man so will, ein wirklich ausgefeiltes Formel 1-Aggregat, was Hochleistung liefert, und jetzt müssen wir unsere Hochleistungsindustrie mit einem Aggregat beglücken, das das gleiche mit Wasserstoff macht. Aber bis vor zehn Jahren wurde Wasserstoff faktisch nur im Labor angewandt, und da gehen dann die Probleme im Detail los. Wasserstoff reagiert anders, ist ein winzig kleines Molekül, findet überall Lücken und Wege und Fugen, um sich zu bewegen, und dann treten Reaktionen auf in Substanzen, die wir heute üblicherweise mit Kohlenstoff behandeln, die wir noch nicht kennen. All das muss erforscht werden, muss ausgearbeitet werden, muss optimiert werden und muss dann zu einer industriellen Anwendungsreife, die unseren Ansprüchen und unserem Hunger nach Rohstoffen tatsächlich gerecht wird, muss das weiterentwickelt werden.
Christine Launert: Die gesamte Stahlproduktion, die, wie sie sagen, schon so lange Tradition hat, umzukrempeln, erfordert ja nicht nur Innovationsgeist, sondern erfordert vor allem auch Mut. Man muss ja erst mal auch anbringen, wir können auch alles ganz anders machen. Wie ist ihr Team damit umgegangen?
Matthias Weinberg: Das ist eine sehr schöne Frage. Da brauchen sie erst mal die passenden Charaktere für. Wenn sie da jemand haben, der am liebsten immer alles macht wie immer, dann ist er da falsch. Das heißt also, sie brauchen wirklich Leute mit einem sehr, sehr offenen Mindset, die wirklich Lust haben, etwas zu verändern, die die richtigen Fragen stellen, die neugierig sind. Wenn sie ein solches Team zusammenkriegen, dann entwickelt sich da eine sehr, sehr hohe Eigendynamik. Oft ist es so gewesen in den vergangenen fünf Jahren, dass ich tatsächlich spät abends, wenn ich nach Hause gefahren bin, den einen oder anderen jungen Familienvater an seine Familie erinnern musste "fahr mal nach Hause, guck mal nach Frau und Kindern", und das sind natürlich Dynamiken, die man sich da in so einem Entwicklungsdruck wünscht, dass wirklich die Leute Ideen wälzen und mit Herzblut dabei sind und tatsächlich am Wochenende weiterdenken. Oft ist es mir passiert, dass ich am Freitag mit einem Ingenieurteam ein Problem diskutiert habe, und am Montag kamen die an und haben da, wir haben da nochmal nachgedacht, uns ist das und das Eingefallen, ich sag "wie uns?" "Ja, wir waren ein paar Bier trinken, und dann haben wir..." und so eine Dynamik ist natürlich toll für so ein Entwicklungsteam. Wenn sie da einmal Blut geleckt haben, mit so einem Entwicklerteam an einer Sache zu arbeiten, die sich wirklich mit Hochdruck in der Umsetzung befindet, dann ist das eine Eigendynamik, die wirklich beeindruckend sein kannl.
Niels Lohmeyer: Vielleicht noch ergänzend von mir, ich sage intern immer: Hunger nach Erfolg haben und sich nicht von Rückschlägen entmutigen lassen. Also in einer Innovation klappt das nie nach Plan, sondern man kommt um eine Ecke herum, und plötzlich funktioniert ein Produkt oder ein Prozess oder ein Teilprozess, den man sich überlegt hat, da funktioniert das nicht so, wie es vielleicht vorher auf dem Papier, im Labormaßstab erprobt wurde, funktioniert dann plötzlich nicht in der Skalierung auf eine Industrieanlage, beim Prozess oder eben beim Produkt. Und dann darf man nicht locker lassen, sondern man möchte das Thema, was sein eigenes ist, oder ihr eigenes, am Ende zum Erfolg bringen.
Jutta Lommatzsch: Ja, ich glaube auch, dass das Bewusstsein ganz wichtig ist, dass man hier in einem Team mitarbeitet, wo man wirklich was bewegen kann. Also, wenn man die Nachrichten anmacht, ist ja doch vieles ganz schön erschreckend. Was man da alles sieht, habe ich ja eben schon mal aufgezählt, will ich jetzt auch nicht wiederholen. Wenn man aber an einem Projekt mitarbeiten kann, grünen Stahl zu entwickeln, der wirklich extrem dazu beiträgt, dass das CO2 weltweit, wenn es gut vermarktet wird, reduziert wird, das ist ja ein tolles Projekt, und wenn dann die verschiedenen Charaktere zusammenkommen, eben Menschen, die einfach beißen, von Natur aus, bis sie das Ziel haben, oder Menschen, die wirklich was bewegen möchten, Frauen, Männer, verschiedene Nationalitäten, dann ist diese Dynamik da, die dann auch wirklich zum Erfolg führen kann. Denn das ist ja kein örtliches Problem, der grüne Stahl oder der dreckige Stahl, sondern das ist ein Problem, was unsere ganze Welt betrifft, und wenn man da mitwirken kann, ist das doch eine tolle Aufgabe, und es ist einfach super, weil man wirklich was bewirkt.
Christine Launert: Zu welchem Zeitpunkt muss man auch beschließen, aber jetzt brauchen wir auch einen Partner. Ab jetzt ist das Projekt so weit fortgeschritten. Wir können Kooperation machen, oder vielleicht können wir auch als Wissensgeber agieren. Aber wann macht es Sinn, wirklich Partner auch an Bord zu holen?
Niels Lohmeyer: Schöne Frage. Ich glaube, das ist immer, bei jedem Projekt, ob nun in einem Unternehmen oder anderswo, die schwierigste Aufgabe, dass das Team sich selbstständig meldet, wenn es nicht mehr alleine zurechtkommt, wenn es eine Abweichung gibt, weil wir natürlich alle doch ein Stück weit geprägt sind, Erfolge auch für die eigene Sache zu vermarkten und eine quasi Abweichung im Terminplan oder in den Zielen, die man erreicht, nicht so gerne von einem Team in die Außenwelt abgegeben wird. Und ich glaube, das ist auch eine Veränderung dann gegenüber früher, wo sehr hierarchisch auch in Unternehmen geführt worden ist. Das funktioniert in der Entwicklung eigentlich überhaupt nicht, weil das ist der Tod nicht nur der Kreativität, sondern das ist auch der Tod, rechtzeitig genau das, was sie gerade gesagt haben, ein Team zu verstärken, vielleicht auch anders aufzustellen, Unterstützung zu holen, intern oder extern, zum richtigen Zeitpunkt, ist entscheidend, Offenheit.
Christine Launert: Abschließend möchte ich doch noch mal den Blick in die Zukunft werfen, denn wir arbeiten gerade an sehr großen Innovationen. Herr Lohmeyer, bei ihnen wird täglich an Produktinnovationen gearbeitet. Und dennoch, was braucht denn die Deutsche Stahlindustrie, um auch langfristig wettbewerbsfähig zu bleiben? Welche Technologien sind unbedingt notwendig? Welche Technologien sind denkbar? Ein Blick in die Glaskugel.
Niels Lohmeyer: Da könnte man auch jetzt wieder lange Antworten auf diese Frage. Ich versuche mal, so ein paar Punkte herauszuarbeiten, die wichtig sind. Ich glaube immer, verlässliche Rahmenbedingungen. Eine Produktentwicklung dauert Jahre, von der ersten Idee zum Start der Produktentwicklung, bis dann vom Labomaßstab dann die ersten Versuche auf den Anlagen gemacht werden, es dann beim Kunden durchgesetzt wird und freigeprüft wird. Da sind locker in der Automobilindustrie mehrere Jahre vorbei. Und wenn dann im Laufe dieser Zeit Rahmenbedingungen geändert werden, ob nun über den Gesetzgeber oder über andere Einflussfaktoren, dann wird der ursprüngliche Businessplan vielleicht in Frage gestellt. Dann hat man ein tolles Produkt, aber es ist nicht mehr erfolgreich auf dem Markt. Das ist für mich so ein erster Punkt, also: Verlässlichkeit in den Prämissen, mit denen die Stahlindustrie Entwicklung treibt. Das gilt für die Prozessseite, denke ich ganz genauso. Könnte man jetzt sagen: Strompreise und so ist bekannt, also verlässliche Rahmenbedingungen. Zweiter Punkt ist, wir hatten über das Thema Förderung und Forschungslandschaft am Anfang gesprochen. Unglücklich ist dann, wenn eine Förderung plötzlich verändert wird. Ich mache mal ein Beispiel, ist gar nicht Stahlindustrie, wenn man Freitags verkündet, dass Montags die Förderung für E-Fahrzeuge ausläuft.
Jutta Lommatzsch: Ach, das wollte ich doch sagen, das Beispiel noch, weil das wirklich so schön plastisch ist!.
Niels Lohmeyer: Ja, also, man kann immer geteilter Meinung zur Subventionen sein, aber wenn man es von heute auf morgen plötzlich alles verändert, dann ist es natürlich extrem negativ für eine Entwicklungsperspektive und hat uns natürlich am Ende auch getroffen, weil wir Stähle für die Energiewende und auch für die Elektromobilität entwickeln, und wenn dann eben durch so eine überraschende politische Entscheidung quasi der ursprüngliche Businessplan wieder in Frage gestellt wird, dann hat das auch Auswirkungen auf die Priorisierung von Produktentwicklung.
Jutta Lommatzsch: Ich kann mich nur anschließen, dass in der Tat der Gesetzgeber gefordert ist. Ich glaube, wir haben hier sehr deutlich rausgestellt, wie wichtig Interdisziplinarität ist, damit überhaupt die ganzen Innovationen auch erfolgreich sein können. Aber das Beispiel Elektromobilität oder auch das Gebäudeenergiegesetz oder kurz Heizungsgesetz zeigt einfach, dass da keine Verlässlichkeit gegeben ist und da Produkte entwickelt werden, die dann plötzlich nicht mehr vermarktet werden können, wo in der ganzen Lieferkette sehr, sehr viele Benachteiligte sind. Und das ist extrem wichtig, dass auch die Gesetzgebung nicht plötzlich, wie sie so schön sagten, übers Wochenende eben in ihrem Beispiel, da rausgeschossen wird, sondern da tatsächlich auch wieder alle Disziplinen einbezogen werden und nicht andauernd es zu Änderungen kommt, sondern zu durchdachten Änderungen. Und da wird einfach, jetzt nochmal eine juristische Anmerkung, viel zu wenig genutzt, dass man eben Gesetze auch langsam und gut ändern kann, und wenn man was sonst machen möchte, kann man es durch eine Verordnung machen. Aber im Moment werden Gesetze rausgeschossen, die einfach nicht gut sind.
Christine Launert: Wir haben jetzt viel davon gesprochen, dass Innovationen die Wettbewerbsfähigkeit eines Unternehmens stärken, auch bezogen auf die Stahlindustrie. Warum ist es jetzt aber so wichtig, dass die Stahlindustrie am Standort Deutschland bleibt?
Niels Lohmeyer: Ein paar Beispiele für Produkte, die ohne Stahl nicht funktionieren: Alles für die Energiewende. Transformatoren, E-Motoren in Autos sind Elektrobleche, also Stahl. Und wollen wir tatsächlich uns wie in anderen Produkten vollkommen abhängig machen von vielleicht auch autokratischen Regimen im Ausland? Oder wollen wir das in Europa und in Deutschland halten? Es gibt sehr, sehr viele Anwendungen von Stahl. Ein Beispiel war eben die Energiewende. Ich könnte Haushaltsgeräte, natürlich das Thema Auto nehmen, was ohne Stahl nicht funktioniert, und deswegen halten wir es für extrem wichtig, dass eben auch die Förderzusagen kommen für die Deutsche und Europäische Stahlindustrie, die grüne Transformation zu bewerkstelligen, weil ansonsten das Vormaterial für alle diese Produkte nicht aus Europa kommen wird.
Matthias Weinberg: Ich glaube, das ist eine sehr gute Zusammenfassung. Dass wir hier natürlich als High-Tech-Land und exportorientiertes Land natürlich auf einen Basiswerkstoff wie Stahl angewiesen sind, ist völlig selbstverständlich. Ich glaube aber, dass uns allen miteinander tatsächlich der Blick für den Wert des Stahls verlorengegangen ist, und deshalb sage ich gerne, insbesondere, wenn wir Besuchergruppen mit wenig Stahlaffinen Besuchern haben, bitte machen sie das Experiment, schauen sie, wo immer sie sind, einfach mal um sich herum, denken sie sich alles aus Stahl weg. Im gleichen Moment wird man feststellen, dass man dann bar jeder Zivilisation in der Wildnis, im besten Fall in einer Dschungelcamp-Atmosphäre, wieder wach wird. Zivilisation ist stahlbasiert. Das ist einer der ältesten Werkstoffe, die die Zivilisation nutzt, und die haben wir bis zum Hi-Tech perfektioniert, und das sollten wir nicht aufgeben. Wer die Wurzel der industriellen Wertschöpfung abschneidet, und das ist nun mal der Stahl, der riskiert natürlich auch, die ganzen Ketten, die dahinter liegen, zu verlieren, und dessen muss man sich bewusst sein.
Christine Launert: Wirtschaft und Lehre brauchen also Neugier und Forschergeist, motivierende Aussichten für die Next Generation Steel. Vielen Dank an unsere Gäste für den interessanten Austausch. Danke fürs Zuhören, ich hoffe, es hat euch gefallen. Falls ja, abonniert "gekocht, gewalzt, veredelt" gern auf Apple, Spotify oder einer anderen Podcast Plattform, und lasts uns auch gerne Feedback da, zum Beispiel via Mail an [email protected]. Ich freue mich auf weitere spannende Stahlthemen mit euch.
Folge 9: New Work statt Old School –Wie sich traditionelle Industrieunternehmen im War for Talents behaupten
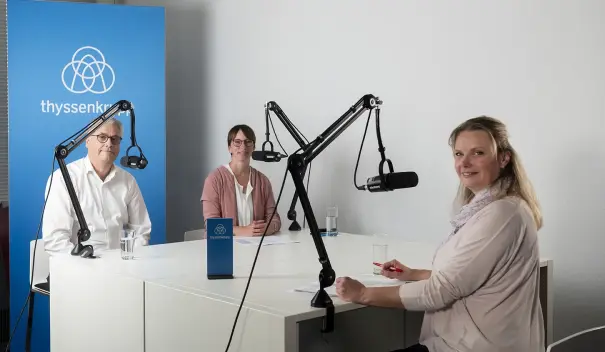
Fachkräftemangel, Ausbildungsflaute, Gen Z, weniger Work, mehr Life: Die Arbeitswelt verändert sich rasant. Was das für Industrieunternehmen bedeutet und welche neuen Anforderungen sich an das Recruiting und Development ergeben, darum geht es in der aktuellen Folge unseres Podcasts „gekocht, gewalzt, veredelt“. Professor Dr. Friedrich Hubert Esser, Leiter des Bundesinstituts für Berufsbildung, und Kerstin Dähne, Head of Recruiting & Development bei thyssenkrupp Steel, geben spannende Einblicke in aktuelle Herausforderungen und innovative HR-Konzepte.
Christine Launert: Liebe Zuhörerinnen, liebe Zuhörer! Willkommen zu einer neuen Folge von "gekocht, gewalzt, veredelt", dem Podcast rund um das Thema Stahl. In dieser Folge geht es um den Arbeitsmarkt der Zukunft und damit um drängende Themen wie Fachkräftemangel und sich verändernde Präferenzen bei der Berufswahl nachfolgender Generationen. Zum Beispiel die Verschiebung der Work Life Balance hin Richtung Life. Wir hinterfragen, was das mit den Industriebranchen in Deutschland macht und welche neuen Anforderungen damit an das Recruiting und Development von Unternehmen geknüpft sind. Ich begrüße heute zwei ganz besondere Gäste, denn ich spreche mit zwei Menschen, die sich täglich mit dem Wandel und der Zukunft der Arbeitswelt auseinandersetzen und dafür moderne Ansätze der beruflichen Aus- und Weiterbildung entwickeln. Ich freue mich sehr, sie, Professor Dr. Friedrich Hubert Esser, Leiter des Bundesinstituts für Berufsbildung, und dich, Kerstin Dähne, meine Kollegin bei thyssenkrupp Steel, begrüßen zu dürfen. Sie leitet den Bereich Recruiting und Development. Mein Name ist Christine Launert, und ich bin Pressesprecherin bei thyssenkrupp Steel. Schön, dass ihr dabei seid.
Christine Launert: Herr Professor Esser, sie beschäftigen sich seit über 30 Jahren mit dem Thema Berufsbildung. Sie sind der Berufsbildungs-Experte schlechthin. Was bedeutet das denn überhaupt?
Friedrich Hubert Esser: Ja, zunächst einmal hallo und guten Tag. Vielen Dank für die Einladung. Ja, was bedeutet das? Ich mache einen total spannenden Job. Ich kümmere mich um Berufe wie ein Fußballer, der früher selber im Hobby Fußball gespielt hat und heute Profifußballer ist. So habe ich auch mal einen Beruf gelernt. Ich bin gelernter Bäcker und bin über einige Umwege ins Bundesinstitut für Berufsbildung gekommen und habe jetzt die Möglichkeit, über alle Berufe hier in Deutschland zu schauen, und das ist nicht nur eine große Verantwortung, sondern macht auch sehr, sehr viel Spaß.
Christine Launert: Kerstin, du bist Head of Recruiting und Development bei thyssenkrupp Steel. Das klingt großartig, was verbirgt sich aber dahinter?
Kerstin Dähne: Ja genau, hallo, auch von meiner Seite! Ich freue mich, dass ich heute mit dabei sein kann. Ja, du hast es angesprochen, für mich ist es ein großartiger Job. Wir beschäftigen uns im Team mit Konzepten und Strategien zu den Themen Recruiting und Personalentwicklung für das gesamte Segment Steel. Das heißt, wir machen uns Gedanken, wie sprechen wir Mitarbeitergruppen an, die wir rekrutieren wollen, intern wie extern, wenn wir Employer Branding Kampagnen machen, um Mitarbeiter zu rekrutieren? Das liegt in der Verantwortung meines Teams, aber auch zu überlegen, mit welchen neuen Strategien, mit welchen neuen Recruitingtools können wir zum Beispiel auf dem externen Arbeitsmarkt Mitarbeitende für uns gewinnen, und im zweiten Schritt dann eben zu gucken, wie entwickeln wir dann diese Mitarbeitenden, und welche Angebote können wir machen? Welche Strategien haben wir da als Unternehmen? Das ist so ganz grob das Spektrum in meinem Team.
Christine Launert: Wie entwickelt sich denn überhaupt die Arbeitswelt, welche Trends zeichnen sich denn ab?
Friedrich Hubert Esser: Na ja, für uns sind zwei Stichworte ganz wichtig. Das eine ist die demografische Entwicklung. Sie macht uns mehr und mehr zu schaffen. Wir werden in diesem Jahrzehnt die Babyboomer in die Rente gehen sehen, und das setzt viele Betriebe und Unternehmen unter Druck. In den 2030er Jahren wird es noch extremer werden. Das ist das eine. Das zweite ist, dass wir einen lahmenden Ausbildungsmarkt haben. Das heißt also, die Dynamik am Ausbildungsmarkt lässt nach. Insbesondere macht uns Kummer, dass junge Leute immer weniger auch berufliche Bildung nachfragen, und das setzt viele Branchen und Betriebe zunehmend unter Druck. Das Handwerk ist betroffen, aber auch die verarbeitende Industrie bekommt keine jungen Leute mehr, oder weniger junge Leute, die den Mut haben und die Lust haben, in Werkstätten zu arbeiten. Das hat auch etwas mit dem Akademiker Trend zu tun, den wir seit vielen Jahren beobachten. Hinzu kommt aber auch, und das ist sicherlich auch ein Punkt, den wir uns genauer anschauen müssen, wir haben 2,6 Millionen Menschen zwischen 20 und 35, die überhaupt keine Berufsbildung in Deutschland haben, und bei dem sich anbahnenden Fachkräftemangel ist das ein besonderes Problem. Auch die Frage, wie können wir Potenziale heben, die wir ja brauchen, um die Nachfrage der Unternehmen nach Fachkräften auch zu sichern?
Christine Launert: Wieso haben wir so viele Menschen in Deutschland, die sich nicht für einen dieser beiden Wege entscheiden können?
Friedrich Hubert Esser: Wenn wir uns die Zielgruppen derer anschauen, die keine Berufsbildung haben, so ist auffällig, dass sehr viele Menschen darunter sind, die einen Migrationshintergrund haben, auch gerade jetzt seit 2015 die erste Flüchtlingswelle, dann seit dem Russlandkrieg dann auch die zweite Flüchtlingswelle, insbesondere aus der Ukraine. Das heißt also, wir tun uns auch schwer, in unserem Land, die Menschen zu integrieren, und Integrieren heißt natürlich im optimalen Fall, sie zur Arbeit zu bringen, und zur Arbeit bringt man in Deutschland vor allen Dingen die Menschen, in dem sie qualifiziert sind. Das heißt, hier müssen wir auch in den nächsten Jahren viel, viel besser werden, weil es gibt ja auch Einschätzungen, dass wir im Jahr in Zukunft rund 400.000 qualifizierte Zuwanderung brauchen, und wenn wir jetzt sehen, dass wir uns schwer tun, so haben wir da viel aufzuholen, um besser zu integrieren und die Menschen über Qualifizierung in Arbeit zu bringen.
Christine Launert: Kerstin, das trifft genau ins Mark deines Arbeitsbereiches. Du bist Head of Recruiting and Development bei Steel. Wie trifft uns das, dass es so viele Menschen gibt, die Potenzial haben, aber eben nicht in die Ausbildung kommen?
Kerstin Dähne: Das trifft uns insofern, dass es zum einen natürlich auch eine Chance für uns ist, also das, was Herr Professor Esser auch gesagt hat. Wir merken natürlich auch den Fachkräftemangel, gerade in ganz bestimmten Berufsgruppen. Und ich glaube, diese große Gruppe derjenigen, die eben nicht diese Ausbildung schon hat, bietet für uns eine Chance, durch Umschulung, durch Unterstützung, durch Weiterbildung, Qualifizierung da auf jeden Fall auch Potenziale zu heben, die wir eben so am Arbeitsmarkt nicht mehr so ohne weiteres bekommen. Das ist, glaube ich, für uns auf jeden Fall eine Chance, aber das bringt sicherlich auch Aufwände mit sich. Dann müssen wir als Unternehmen, auch natürlich gucken, wie sprechen wir diese Zielgruppen an, welche Angebote können wir tatsächlich machen, mit welchen Kooperationspartnern können wir da auch zusammenarbeiten, weil das sicherlich auch eine große Aufgabe ist.
Christine Launert: Lassen wir einmal die jetzt nochmal beiseite, die schon im Berufsleben stehen oder die Ausbildung hinter sich haben. Wir sprechen jetzt über die Generation Z, die sich selber nicht so gerne nennt und wie alle anderen Generationen sich auch gar nicht gerne über einen Kamm scheren lässt. Aber wir sprechen über diejenigen, die in den späten 1990ern und den 2000er Jahren geboren sind und die eben vor diesen Herausforderungen des sich wandelnden Arbeitsmarktes stehen. Es gibt alte Berufsbilder, die eine handfeste Ausbildung versprechen. Es gibt sehr neue Berufsbilder, die im einzelnen Erfolg versprechen, die vielleicht auch keine handfeste Ausbildung im ersten Blick brauchen. Und andererseits muss sich aber auch der Arbeitsmarkt den Bedürfnissen dieser jungen Menschen anpassen. Die Unternehmen, die Branchen müssen sich anpassen. Wie passt das zusammen? Wie kommen diese beiden Seiten zusammen, Herr Professor Esser, welche Erfahrung haben sie da gemacht?
Friedrich Hubert Esser: Ja, zunächst einmal sagen uns ja die Jugendstudien, dass die Generation Z sich erst mal dadurch auszeichnet, dass sie zwei große Krisen, eine haben wir hinter uns, das ist die Corona-Problematik. Jetzt sind wir in einer Situation, wo wir Kriege wieder unmittelbar vor unserer Haustüre erleben müssen, und die Jugendstudien sagen, dass diese Generationen doch sehr selbstbewusst mit diesen Rahmenbedingungen unserer Gesellschaft umgehen. Das finde ich sehr, sehr positiv. Das zweite ist, dass sich die jungen Leute dadurch auszeichnen, dass sie nicht, ich sage mal, paradiesische Zustände wünschen, sondern dass sie schon konkrete und auch sehr sachliche Wünsche haben, wie sie in Zukunft leben wollen, wie sie Beruf und Familie vereinbaren wollen, wie sie auch eine Beschäftigung suchen, die eine hohe Verbindlichkeit hat. Das heißt also, nicht nur die Einstellung in ein Unternehmen ist wichtig, sondern auch die Perspektive, die man in einem Unternehmen bekommt, ist wichtig, und dass es eine gute Qualifizierung gibt. Also man weiß schon, dass man hier in Deutschland am sichersten fährt auf dem Arbeitsmarkt, wenn man gut aus- und weitergebildet ist und eben im Unternehmen selber eine stabile Position hat, aber auch immer in der Lage ist, die Position auch zu wechseln. Das ist auch ganz, ganz wichtig. Also unterm Strich sehe ich die Generation sehr pragmatisch unterwegs. Herr Hurrelmann hat mal gesagt, das sind Ego-Taktiker. Das ist auch nochmal so ein schöner Begriff, der eben sagt, dass die jungen Leute heute auch abwägen und auch Entscheidungen, die ganz wichtig sind, also die lebenswichtig sind, zum Beispiel, wo möchte ich später mal arbeiten? Wo möchte ich ausgebildet werden? In einem Betrieb, oder möchte ich lieber an eine Universität gehen? Dass man auch solche Entscheidungen gerne herauszögert. Man wartet ab, man schaut, man will auch ein Stück weit optimieren, dass man also möglichst sichere Informationen hat, die dann auch eine Entscheidung fundiert. Etwas zögerlich kommt dann auch der eine oder andere rüber. Aber insgesamt, so meine Feststellung, haben wir mit einer Jugend zu tun, die in unsere momentane Situation passt und auf die wir uns auch einstellen müssen.
Christine Launert: Das trifft ja eigentlich unseren Nerv ganz genau. Kerstin, wie müsst ihr auf die jungen Leute zugehen? Was warten die auch in den Gesprächen? Da würde ich sagen, da passen unsere Erfahrungen ganz gut zu dem, was Herr Professor Esser gerade gesagt hat, so das Thema der Möglichkeiten. Was bietet mir ein Unternehmen, nicht nur im Moment des Einstiegs, sondern auch, wenn ich im Unternehmen bin und wenn ich mich weiterbilden möchte, wenn ich eine Ausbildung beginne, habe ich zum Beispiel später die Möglichkeit, auch noch zu studieren, wenn ich mich im ersten Schritt erst mal für eine Ausbildung entschieden habe, was gibt es ansonsten für Entwicklungsmöglichkeiten? Gibt es Möglichkeiten, eine Stelle zu wechseln? Welche anderen Dinge gibt, die ich für mein Leben nutzen kann? Auch das Thema, wie flexibel bin ich als Arbeitgeber, was zum Beispiel Arbeitszeiten und Arbeitsmodelle betrifft? Also, es kann ja gut sein, ich starte in dem Unternehmen, ich bin irgendwie dann vielleicht in der Phase, wo ich sage, das passt gut, dass ich gerade viel arbeite, dass ich mein Arbeitsvolumen gut ausschöpfe, wenn sich aber das Leben drumherum verändert. Das muss ja nicht unbedingt eine Familienplanung sein. Es können ja auch andere Dinge dazu kommen, wo ich mich dann entscheiden möchte. Ich möchte jetzt weniger arbeiten, ich möchte ein anderes Arbeitsmodell haben, ich möchte in Teilzeit arbeiten. Das sind schon Dinge, die nachgefragt werden und wo wir, glaube ich, aber auch als Arbeitgeber schon sehr viele gute Möglichkeiten anbieten können, wie flexibel wir tatsächlich sind und was wir alles so bieten können. Darauf würde ich gerne später nochmal zurückkommen. Das frage ich dich auch noch mal. Ich würde jetzt gerne erst mal reinhören. Was sagen denn die jungen Leute? Was sagen Werkstudentinnen, die sich bei uns bewerben, um einen Fuß in die Tür zu bekommen oder einfach schon mal erste Berufserfahrung zu sammeln? Was sagen denn die aus, die jetzt gerade angefangen haben oder auch schon ein wenig länger bei uns sind? Welche Erfahrungen haben sie bis jetzt gemacht? Warum haben sie sich aber auch für uns als Arbeitgeber entschieden? Und wir fragen auch ein Train, das heißt jemand, der gerade bei uns angefangen hat mit einem akademischen Hintergrund.
Werkstudent: Ich bin 25 Jahre alt, Werkstudent in der Marketing Abteilung, und ich habe mich hierfür entschieden, weil, als ich mich über einen Werkstudenten Job informiert habe, bin ich auf thyssenkrupp gestoßen und auch auf dieses große Thema der grünen Transformation. Und das fand ich für mich einfach eine riesen Herausforderung, auch, das natürlich im Marketing an die Menschen weiterzugeben, was hier bei thyssenkrupp passiert. Und das fand ich eben sehr spannend. Deswegen bin ich bei thyssenkrupp. Wenn ich mal fertig bin, erwarte ich von meinem Arbeitgeber, dass man mobiles arbeiten hat mit flexiblen Arbeitszeiten und eben auch ein sicheres Arbeiten, wo man quasi keine Angst haben muss, irgendwann auf der Straße zu landen, gepaart eben auch mit einem kollegialen Arbeiten, wo man nicht von oben herab behandelt wird, sondern wo alles einfach quasi nach dem Ziel ausgerichtet ist. Das erwarte ich.
Azubi: Mein Name ist Aileen Yalzin. Ich bin 27 Jahre alt, und ich mache meine Ausbildung beim Werkschutz bei thyssenkrupp Steel. Ich habe mich für thyssenkrupp Steel entschieden, weil ich thyssenkrupp Steel für einen sicheren Arbeitgeber halte und ich mich hier sehr gut aufgenommen gefühlt habe. Ich erwarte von thyssenkrupp Steel einen sicheren Arbeitsplatz und eine faire Bezahlung, die auch an den wirtschaftlichen Situationen angepasst wird, und dazu erwarte ich noch, dass man mit den Mitarbeitern transparent umgeht, dass man weiß, woran man ist, und dass man offen kommuniziert.
Trainee: Mein Name ist Sebastian Tenkamp. Ich bin 25 Jahre jung und habe hier in Duisburg Maschinenbau studiert. Aktuell bin ich als Trainee tätig in dem Bereich Instandhaltung, beispielsweise im Warmbandwerk 2. Für thyssenkrupp habe ich mich entschieden, da ich damals bereits zur Bachelor-Zeit hier sein durfte und ein sehr kollegiales Verhältnis zu meinen Kollegen hatte, und das Geschehen auf Augenhöhe war einer der Punkte, die mich sehr fasziniert hat. Außerdem ist es thyssenkrupp für mich persönlich hier im Pott einer der facettenreichsten Arbeitgeber, und ich bin nun auch schon in der dritten Generation hier. Ich erwarte von meinem Arbeitgeber, vor allem, um es auf den Punkt zu bringen, Flexibilität. Jetzt gerade ist für mich besonders interessant, Gas zu geben. Ich verbeisse ich gerne auch in Themen und bin auch wirklich bereit, viel dafür zu tun. Wie sich das ganze aber langfristig ändern wird, vor allem beispielsweise auch mit der Familienplanung, weiß man nicht, und ich glaube, hier ist Flexibilität ein wichtiger Punkt.
Christine Launert: Ja, das sind relativ ähnliche, aber doch recht unterschiedliche Ansätze, die wir jetzt gehört haben, und genauso flexibel müssen wir als Arbeitgeber auch darauf reagieren auf diese unterschiedlichen Bedürfnisse. Jetzt haben wir nur drei Stimmen gehört. Es gibt ja viele, viele, viele Tausende da draußen. Kerstin, welche Möglichkeiten bieten wir denn als Arbeitgeber, seine Arbeitszeit oder überhaupt seine Work Life Balance oder Life Work Balance flexibel zu gestalten?
Kerstin Dähne: Das sind ganz verschiedene Instrumente, die wir haben. Also, wir haben angefangen von dem Thema Wahlarbeitszeit, als ich mir überlegen kann, wieviel meiner wöchentlichen Arbeitszeit möchte ich denn eigentlich im Unternehmen verbringen, also zwischen 33, 34, 35 Stunden beispielsweise. Das haben wir tarifvertraglich geregelt. Wir haben das ganze Thema mobiles Arbeiten mit einer Betriebsvereinbarung als Unternehmen festgeschrieben. Da, wo es möglich ist, sicherlich nicht an jedem Arbeitsplatz, aber da, wo es eben möglich ist, bieten wir diese Möglichkeit, ich glaube auch im Vergleich mit einer sehr großzügigen Regelung mit bis zu 60 Prozent der Arbeitszeit, die man eben nicht im Büro verbringen muss, sondern mobil an einem Arbeitsplatz, wo man eben gerne arbeiten möchte. Wir haben unterschiedlichste Möglichkeiten, in Teilzeit zu gehen, seine Stundenanzahl zu reduzieren, wir haben Gleitzeitmodelle, und ich glaube, auch ein Vorteil bei uns ist das Thema Vereinbarkeit von privatem und Beruf betrifft ja jetzt nicht immer nur die Arbeitszeit, sondern es gibt ja auch viele Dinge, wo ich als Unternehmen auch die Mitarbeiter unterstützen kann, also wo ich sagen kann, was hilft ihnen denn in der Bewältigung von ihrem Alltag, und da ist sicherlich immer so ein ganz klassisches Beispiel: unsere Betriebskita, die wir ja in Duisburg auch beispielsweise haben, aber auch ganz viele andere Angebote, von unserem Sozialservice, die ich in Anspruch nehmen kann, bis hin zur Flexibilisierung. Wir haben jetzt eine Packstation hier in Werksnähe auf jeden Fall aufgestellt. Das sind, glaube ich, alles kleine Bausteine, die dazu beitragen können, dass das Thema Flexibilität, was sich die Mitarbeitenden wünschen, dem wir da gut entgegenkommen können.
Friedrich Hubert Esser: Ja, kann ich nur unterstreichen und ergänzen. Man sieht eben, wir befinden uns mittlerweile auf einem Bewerbermarkt. Das heißt also, Unternehmen haben verstanden, dass man Personalmarketing machen muss, und was uns auffällt, gerade auch mit Blick auf junge Leute, die aus der Schule kommen und in die Ausbildung gehen, dass Unternehmen bemüht sind, möglichst niedrigschwellig mit den jungen Leuten in Kontakt zu kommen. Das heißt also, Kommunikation zu ermöglichen, die spontan auch sein kann, die direkt sein kann. Also, wenn ich da an meine Zeit als jugendlicher erinnere, da mussten erst mal dicke Bewerbungsmappen geschrieben werden, bevor man überhaupt einen Kontakt bekommen hat in einer Personalabteilung.
Christine Launert: Und die mussten auch einen sehr, sehr formellen Charakter haben, sehr ordentlich sein.
Friedrich Hubert Esser: Genau, und das hat sich massiv verändert. Viele Unternehmen gehen heute hin, Ich will noch nicht sagen, dass das sehr positiv ist, aber die gehen hin, dass man überhaupt keine Bewerbung mehr so formal machen muss, die man online machen kann, die man im Grunde genommen vom Mobile Phone aus entsprechend auch tätigen kann. Zeugnisse, Schulzeugnisse werden auch ein Stück weit relativiert. Man sagt, komm, trau dich ruhig. Komm und wir machen einen Test mit dir, und dann gucken wir, ob du passt. Und was auch interessant ist, und das ist ja eben auch schon von Frau Dähne angesprochen worden, dass man auch signalisiert: wir investieren in dich, und dass man eben auch, wenn man Probleme hat, an der einen oder anderen stelle, dass man nochmal ein bisschen Nachhilfe braucht in Mathe oder ein Stück weit Unterstützung, wenn es um Deutsch geht, um das Sprechen mit Kunden, Verständigung im Team, dass man auch sagt, wir coachen dich, wir bieten dir Trainings an, und dann klappt das schon irgendwann. Also, dass man auch in die Menschen investiert. Das ist sehr, sehr auffällig und drückt nochmal aus, das Unternehmen jetzt strategisch auch unterwegs sind, diesem Fachkräfteproblem zu begegnen, was ja auch im Grunde in den nächsten Jahren eine massive Schwierigkeit bedeutet, auch im ökonomischen Sinne, dass das so auch zu einer Wachstumsbremse wird, das sagen uns die Volkswirte ja heute schon.
Kerstin Dähne: Das ist definitiv ein Punkt, den wir auch feststellen, also gerade das Thema auch Flexibilisierung im Recruiting, das, was sie angesprochen haben, so diese One click Bewerbung, möglichst ohne viele Dokumente, ohne viele Ausführungen. Da machen wir auch schon so erste Versuche mit einigen Tools, und das ist auch für uns eine Umstellung in der Suche der Kandidatenprofile. Gerade da, wo wir sagen, wir finden nicht mehr den 100, 110, 120sten Kandidaten oder Kandidatin, wo wir dann eben sagen, was sie angesprochen haben, da müssen wir dann gegebenenfalls einfach nochmal investieren und sagen, so, das Profil passt, aber vielleicht zu 80 Prozent, und die letzten 20 Prozent müssen wir als Unternehmen investieren, weil wir einfach diese Profile so nicht mehr finden. Und das bedeutet aber auch für uns als Unternehmen und auch für unsere Führungskräfte natürlich eine Umstellung. Der Weg hin zum Arbeitnehmermarkt, das ist sicherlich eine große Herausforderung, auch immer noch für das gesamte Unternehmen.
Christine Launert: Lohnt es sich denn auch, also, nehmen es die jungen Leute auch an? Ist das etwas, was deren Nerv genau trifft, und ist das auch die Erwartung, dass ich gar nicht mehr alles mitbringen muss, was in der Stellenbeschreibung unter den einzelnen Bullet Points aufgezählt ist, sondern bewerbe ich mich einfach, und dann schaue ich, ob wir irgendwie zusammenkommen?
Kerstin Dähne: Das würde ich schon so sagen. Wir haben ja gerade gesagt, auch für die Generationen-Beschreibung ist sicherlich nicht immer eine pauschale für alle richtig. Aber ich würde sagen, im Trend ist das so, dass wir durchaus merken, dass da die Bewerbungen auch vielfältiger werden. Auch das kann ja ein Vorteil sein, und das ist auf jeden Fall eine Bewegung, die wir merken, und ich glaube aber auch, dass die Bewerberinnen und Bewerber das zu schätzen wissen. Also, das sind die Erfahrungen, die wir machen, dass wir auch immer noch als Arbeitgeber, glaube ich, eine gute Reputation haben. Das sind natürlich auch die Möglichkeiten, die wir im Konzern haben, dass die da sicherlich gut angenommen werden. Aber wir müssen uns da sicherlich weiter strecken und anstrengen, weil wir ja nicht alleine auf dem Arbeitsmarkt sind.
Friedrich Hubert Esser: Was dazu noch zu ergänzen ist, ist, dass, eben das Stichwort Bewerbermarkt bemüht, dass das natürlich auch heißt, dass junge Leute natürlich auch mehr Möglichkeiten haben, auch des Wechsels. Und deshalb sehen wir auch, dass Betriebe, Unternehmen darauf achten, auch Bindungen herzustellen, dass man eben bleibt, auch nach der Ausbildung bleibt, und das ist wichtig. Wir sehen an den Zahlen, dass wir gerade auch in der Ausbildung noch relativ hohe Zahlen haben bei der vorzeitigen Vertragsauflösung, also dass hier auch mehr Bemühungen da sein müssen, weil es ist nicht im Sinne des Unternehmens, aber auch nicht im Sinne der jungen Leute, wenn man eben Ausbildungen abbricht, wie es so schön heißt, dass man mehr darauf achten muss, auch bei der Rekrutierung zu schauen, ob der Ausbildungsberuf auch wirklich passt, das ist das eine. Das zweite ist natürlich, ob derjenige, der ausgebildet werden will, auch ins Unternehmen passt. Hier ist immer noch die Empfehlung, dass man möglichst auch ein Praktikum, also Praktikumsmöglichkeiten eröffnet, für uns immer noch die beste Vorbereitung, Auszubildende zu akquirieren, auf der einen Seite auch für den jungen Menschen die Berufserfahrung, so ein Stück weit mal einen Einblick in einen Beruf zu bekommen, das Unternehmen kennenzulernen und aus der Phase des Praktikums heraus auch den Ausbildungsvertrag zu machen, um eben die Abbruchzahl zu senken, die bei uns in Deutschland immer noch relativ hoch ist.
Kerstin Dähne: Das stellen wir definitiv auch fest. Also auch wenn wir gucken, wer fängt bei uns eine Ausbildung an, ist das eine, aber auch wir haben mal analysiert von unseren Trainees, wer hat da eigentlich schon eine Vorgeschichte im Unternehmen? Also, wer hat ein Praktikum gemacht? Wer war mal Werkstudent? Das waren, ich glaube, über 80 Prozent der Trainees, die wir eingestellt haben, hatten diese Art der Vorbeschäftigung. Das heißt, wir hatten als Unternehmen die Chance, die jungen Menschen kennenzulernen, und die hatten aber auch die Chance, uns kennenzulernen als Unternehmen. Denn ich glaube, dass, was immer wichtiger wird neben den ganzen Themen, die wir schon angesprochen haben, bestimmte Leistungen, die das Unternehmen bietet, Flexibilisierung, das ist das Thema Unternehmenskultur. Und da merken wir immer stärker, dass da gerade diejenigen, die von extern ins Unternehmen kommen, dass für die das Thema Unternehmenskultur, wie werden hier Werte tatsächlich gelebt, dass das immer wichtiger wird und das immer wichtiger wird, wie authentisch ist eigentlich das Unternehmen, so, wie es sich auf einer Messe oder über eine Kampagne präsentiert, ist es auch das, was ich vorfinde? Und es ist das, mit dem ich mich auch wirklich identifizieren kann? Und das ist, glaube ich, ein ganz wesentlicher Faktor, um auch die Leute tatsächlich dann zu binden in diesem Arbeitnehmermarkt, den wir jetzt mehrfach angesprochen haben, und deswegen ist das auch ein ganz wichtiger Punkt, wo wir auch dran arbeiten. Wir haben als Teil unserer Strategie das Thema Führungs- und Leistungskultur ja auch etabliert, weil wir eben merken, dass das auf jeden Fall ein sehr wichtiges Thema ist, nicht nur für die Leute, die neu ins Unternehmen kommen, sondern natürlich auch für die gesamte Belegschaft.
Christine Launert: Ja, Unternehmenskultur kann man schwer als Exposée mit auf eine Messe nehmen, man kann es nicht in eine Broschüre abdrucken. Es ist sehr schwer, das nach außen zu tragen. Deswegen die Frage, mit wem konkurrieren wir denn auf dem Arbeitgebermarkt? Also, welche Branchen sind denn vom Fachkräftemangel betroffen, und wer muss denn sich jetzt wirklich recken, um die besten Fachkräfte, Stichwort War of Talents, wirklich zu rekrutieren und wirklich als Arbeitgeber hinterher das Rennen zu machen?
Friedrich Hubert Esser: Ja, also zunächst einmal, ich hab das Eingangs ja gesagt, der Fachkräftemangel geht mittlerweile in die gesamte Breite der Wirtschaft. Wenn wir vor 2, 3 Jahren noch gerade das Handwerk immer herausgestellt haben als ein Bereich, der massiv unter Fachkräftemangel leidet, im besonderen auch mit Blick auf die Transformationsrelevanz dieses Sektors. Wir brauchen elektrotechnische Handwerke, wir brauchen installationstechnische Handwerk, wir brauchen die Dachdecker, die Solardächer auf die Häuser bringen, massiver Druck. Aber das ist jetzt nicht nur das Handwerk, wo wir sehen, wo die Fachkräfte zurückgehen, in der verarbeitenden Industrie: massive Probleme. Dann auch in so Bereichen wie Gesundheit und Pflege brauchen wir mehr und mehr auch Kräfte, die die Generationsstarken Menschen auch betreuen. Wir haben Probleme im IT Sektor, wo wir Informatiker brauchen, sowohl die eine Hochschule durchlaufen haben, aber auch Fachinformatiker, die aus dem dualen System kommen. Wir haben im Bereich Erziehung, heute in der Presse ganz groß, uns fehlen viele Kitaplätze, aber uns fehlen nicht nur die Plätze, uns fehlen auch die Erzieherinnen und Erzieher. Wir haben einen massiven Lehrerinnen- und Lehrermangel an den Schulen, der sich verstärken wird. Also, sie sehen, in der kompletten Breite unserer Wirtschaft und Gesellschaft merken wir jetzt auch vor allem durch den demografischen Druck, dass die Fachkräfteproblematik zunimmt.
Christine Launert: Kerstin, Jetzt haben wir ganz viel darüber gehört, was denn die nächste Generation überhaupt von den Arbeitgebern erwartet. Was bringen die aber denn mit? Denn die haben ja auch ganz, ganz viel im Gepäck, schon.
Kerstin Dähne: Ja, definitiv, und ich glaube, das ist auch eine große Chance, die in der neuen Generation definitiv liegt, wenn wir sie als Mitarbeitende gewinnen können. Das ist beispielsweise das Thema Technologieaffinität und Digitalisierung. Die sind einfach ganz anders mit digitalen Medien zum Teil aufgewachsen, gehen ganz anders mit denen um, und ich glaube, das ist für uns als Unternehmen eine große Chance, diese Fähigkeiten, die sie mitbringen, die sie schon haben, einfach auch zu nutzen und für uns einzusetzen.
Friedrich Hubert Esser: Komma aber, was, glaube ich, noch ganz, ganz wichtig ist in diesem Zusammenhang. Die Affinität ist da, das ist richtig, und es macht uns auch die Sache einfacher, junge Leute mit digitalen Konzepten auch entsprechend abzuholen. Auf der anderen Seite, aber, das muss man auch sagen, es ist nochmal ein Unterschied, ob ich in der Freizeit mit meinem Handy spiele und wild kommuniziere oder ob ich es wirklich im beruflichen Sinne fachlich anwenden kann, und ich sage das deshalb, weil wir brauchen dringend eine strukturiertere Bildung, auch in unseren Schulen, was das Thema Medienkompetenz und IT Kompetenz angeht. Also das müsste im Grunde in allen Schulen ein klar definierter Bildungsstandard sein, um sie dann auch mit unseren Ausbildungsansprüchen, die ja auch teilweise sehr digital ansetzen, auch wirklich abholen zu können. Also da müssen wir auch aufholen.
Kerstin Dähne: Das würde ich direkt unterstreichen, und ich glaube, das ist dann genau das. Die Grundlage ist sicherlich da gut gegeben, und dann müssen wir gucken, wie können wir auch als Unternehmen da unterstützen, diese Kompetenzen eben so auszubauen, dass sie genau zu dem passen, was wir eigentlich brauchen. Und was wir auch feststellen, ist, die treten selbstbewusst auf, aber wir können als Unternehmen durchaus dem auch selbstbewusst entgegentreten. Wir haben gerade bei thyssenkrupp Steel mit dem ganzen Thema der grünen Transformation merken wir, dass das ein Thema ist, was auf eine sehr starke Resonanz stößt. Also das ist ja auch ein Punkt zu sagen, mit welchem Wert gehe ich eigentlich in so ein Unternehmen, was ist mir wichtig, was dieses Unternehmen verkörpert? Das ganze Thema Nachhaltigkeit ist sicherlich auch ein sehr wichtiges für diese Generation, und das ist natürlich was, was, glaube ich, sehr gut aktuell zusammenpasst, unsere Unternehmensentwicklung und diese Erwartung der Generation, auch in einem Beruf was Sinnvolles zu finden und auch für ein Unternehmen zu arbeiten, mit dem man sich eben gut identifizieren kann.
Christine Launert: Die Transformation, die treibt uns gerade um. Das bedeutet, dass wir die Stahlherstellung auf CO2-neutrale Stahlproduktion umstellen werden, aber die braucht auch eine Menge Fachkräfte.
Kerstin Dähne: Das ist so, das ist so, definitiv. Und das ist natürlich für uns insofern eine große Herausforderung. Wir haben das mal grob überschlagen, so, in den nächsten 10 Jahren werden uns wahrscheinlich zirka 30% unserer Mitarbeiter und Mitarbeiter aus demografischen Gründen verlassen. Das ist eine riesige Anzahl, wo wir uns eben bemühen müssen, Nachfolger zu finden. Und diese Nachfolger suchen wir, ich würde mal so schätzen, in ca. 70% der Fälle im technischen Bereich. Das heißt, wir suchen ausgebildete Elektroniker, Mechaniker in den technischen Berufen, wir suchen Ingenieure im Bereich Elektrotechnik, Maschinenbau, und auch da ist ja der Trend auch zum Beispiel bei den Studienzahlen zum Teil eher rückläufig. Das heißt, wir haben nicht nur die Konkurrenz zu anderen Arbeitgebern, wir haben sowieso auch da einen sehr knappen Markt an ausgebildeten Fachkräften, die wir aber unbedingt brauchen, um sowohl die Transformation zu schaffen als auch einfach unsere Produktion weiter so fort führen zu können, und das ist für uns eine Riesenherausforderung.
Christine Launert: Wie stellen wir denn sicher, dass das Know how nicht einfach weg ist?
Kerstin Dähne: Wir haben da Konzepte zum Wissenstransfer, also wie wir gut sicherstellen können, dass gerade so dieses Implizite wissen, was man ja oft sagt, was im Kopf der Mitarbeitenden ist, dass sich einfach zum Teil über Jahrzehnte auch angesammelt hat, wie wir das gut übertragen können. Aber das ist sicherlich nach wie vor ein großes Thema, wo wir auch noch gefordert sind, uns da stärker mit auseinanderzusetzen, wie wir das bewerkstelligen, dass, wenn diese Mitarbeitenden uns verlassen, wie wir dann das neue Wissen oder das Wissen wieder neu aufbauen für die, die dann neu dazukommen.
Christine Launert: Das heißt, wir schaffen gerade eine große Spielwiese für eine Menge Berufsbilder. Aber uns fehlen die Menschen, die diese Berufsbilder ausfüllen. Das sind ja auch nicht nur die, die man bei uns vermutet, wie ElektrikerInnen und IngenieurInnen, sondern es sind ja noch weit mehr, die man bei uns gar nicht vermutet.
Kerstin Dähne: Das stimmt, das stimmt. Also, wir haben in ganz vielen Berufszweigen, auch gerade vielleicht in eher kleineren Bereichen, zum Teil Schwierigkeiten, Stellen nachzubesetzen. Also ein Beispiel ist sind unsere Betriebsärzte. Also wenn wir da sagen, die sind natürlich auch notwendig, die müssen Untersuchungen durchführen, damit Mitarbeiter weiter an ihrem Arbeitsplatz eingesetzt werden können, und das ist wirklich auch eine Zielgruppe, die ist recht schwierig, zum Beispiel, zu rekrutieren. Ich weiß, es geht nicht nur uns so als Unternehmen, aber aber das ist eben so ein Beispiel jenseits der Elektroniker, Elektrotechniker, wo wir einfach merken, dass wir da wirklich uns neue Dinge auch zum Teil einfallen lassen müssen, wie wir diese Zielgruppen ansprechen, um die eben dann für unser Unternehmen auch zu begeistern.
Christine Launert: Auch wir brauchen ja Lokführer, Feuerwehrleute, alles Berufe, die man bei uns gar nicht so vermutet, Chemikerinnen. Was können denn Unternehmen tun, Herr Professor Esser, um wieder darauf aufmerksam zu machen, dass diese Berufe benötigt werden und dass es eben auch wirklich sichere Berufe sind?
Friedrich Hubert Esser: Ich würde erst mal sagen, wir haben sowohl ein Mengenproblem wie auch ein Qualitätsproblem. Fangen wir mal mit den Mengenproblem an, Frau Dähne hat es ja gerade ausgeführt. Wir brauchen, glaube ich, zunächst einmal Strategien, wie wir Potenziale heben, die da sind und die auch, ich sag mal, beruflich, die wir beruflich auch von den weißen Kragen weg auch in andere Dimensionen unserer Branche führen müssen und auch wieder Interesse wecken müssen. Für mich ist, glaube ich, eine große Chance, wir wissen, dass wir einen großen Anteil haben an jungen Leuten, die sehr Umweltorientiert sind, die Fridays For Future Generation, um ihnen deutlich zu machen, wie viel Umweltschutz, wie viel Transformation in unseren Berufsbildern steckt, wenn man eben jetzt hier diese Umstellungen vornimmt auf eine Wasserstofftechnologie, dass man sich im Grunde sehr aktiv beruflich an Umweltschutz beteiligen kann und Transformation mitbewirken kann, das, glaube ich, ist ein ganz wichtiges Signal an junge Leute, um sie nicht nur demonstrieren zu lassen, sondern auch sagen, du kannst richtig was bewegen. Wir haben diese Berufe und du kannst sogar Geld verdienen, wenn du Transformation betreibst. Also dass man dieses Thema aktiv mit jungen Leuten unterstützt. Etwas anderes ist natürlich die Zuwanderung, die wir wuppen müssen, keine Frage, sie muss natürlich sozialverträglich sein. Wir müssen besser integrieren, wie ich das am Anfang gesagt habe. Wir müssen viel besser werden, auch in der Bildung, in den Schulen und Qualifizierungen in den Unternehmen, denn wir sehen an unseren Auswertungen, die wir jedes Jahr betreiben, dass Menschen mit Migrationshintergrund prinzipiell schlechter unterwegs sind als unsere Deutschen jungen Leute, und das zeigt eben, dass es hier nach wie vor Probleme gibt einer vernünftigen Integration, die schon in der Vorschule beginnen muss, in den Schulen weitergeführt und dann natürlich dann in den Unternehmen aufgegriffen werden müssen. Aber auch Potenziale, ein Beispiel sind Frauen. Wir haben sehr viele Frauen, die Teilzeit beschäftigt sind, die also nicht in der vollen Stundenzahl unterwegs sind. Das hat auch damit zu tun, dass wir zu wenig Möglichkeiten haben, was die Kitas angeht, dass wir zu wenig Möglichkeiten haben einer Ganzschulstruktur, also Ganztagsschulen. Man kann darüber streiten, wie vernünftig das ist, Stichwort Erziehung und so weiter. Aber erst mal sind das Potenziale, die gehoben werden könnten. Dann hat das natürlich auch zur Folge, dass wir besser auch überlegen müssen, warum sind die Frauen heute, auch gerade junge Frauen in den MINT-Berufen, noch schwächer unterwegs als die Männer? Auch da sehe ich noch Möglichkeiten, verstärkt Potenziale zu heben, und dann Stichwort Arbeitszeit. Also das ist ja eine hochinteressante Debatte, die wir jetzt haben, vier Tage Woche bei vollem Lohnausgleich, ob das die Strategie ist, um diese Probleme zu bewältigen, die wir haben, da stelle ich auch mal ein großes Fragezeichen dahinter. Was gut ist, was Frau Dähne ausführte, ist, dass wir viel flexibler denken, wenn es um die Organisation von Arbeit angeht. Aber ich bin skeptisch, ob wir mit weniger Arbeit die Herausforderungen schaffen, die Anstehen, unabhängig davon, wie die Transformation in sich gestaltet, dass menschliche Arbeit in maschinelle Arbeit transformiert werden, dass wir eine andere Unterstützung auch haben, Stichwort Cyberphysische Produktionstechnologien, wo Roboter auch mehr und mehr eine Rolle spielen. All das mal, ich sage mal, an die Seite, ist schon meines Erachtens das falsche Signal, auch gerade an unsere jungen Leute, den Eindruck zu vermitteln, mit weniger machen wir mehr. Das glaube ich nicht, sondern wir brauchen ein Signal an junge Leute, die die Herausforderung beschreibt und auffordert, an dieser Herausforderung zu arbeiten, sich zu bewähren, etwas zu entwickeln. Also auch, dass Deutschland, Herr Scholz sprach von einer Zeitenwende, dass diese Zeitenwende auch von jungen Leuten mit gehoben wird und dazu Mut zu machen und auch sagen, es gab ja vor vielen, vielen Jahren mal so ein schönes Lied, jetzt wird wieder in die Hände gespuckt, wir steigern das Bruttosozialprodukt, ja, da lacht man heute drüber. Aber so eine Einstellung wieder in die Gesellschaft zu bringen, eine optimistische, eine sportliche Einstellung, auch wir wollen gewinnen, das, glaube ich, ist viel, viel wichtiger als zu überlegen, wie kann ich weniger arbeiten, damit ich mehr Freizeit habe.
Christine Launert: Wenn sie das so erläutern, Herr Professor Esser, klingt es ein wenig nach zwei Fronten: die Unternehmen auf der einen Seite, die Nachwuchs brauchen und eben aber auch viel zu bieten haben, und auf der anderen Seite Menschen mit viel Potenzial, dass sie vielleicht selber gar nicht kennen und auch nicht wissen, wie sie das heben können. Wie kommen denn diese beiden Parteien jetzt zusammen? Wo gibt es denn da Möglichkeiten?
Friedrich Hubert Esser: Ich denke, Frau Dähne hat es eben schon auch angesprochen, genau das ist der Punkt. Meine These ist, dass junge Leute, wenn man sie richtig anspricht und anpackt, dass man sie auch gewinnen kann, an so einem Projekt auch bei thyssen hier mitzuwirken und mitzuarbeiten. Und dann kommt es natürlich auch darauf an, dass die Rahmenbedingungen stimmen, und Frau Dähne hat sie ja eben auch beschrieben, was uns da auch noch auffällt, ist eben, dass neben dieser Bindung, die da sein muss, neben den Perspektiven, die da sein müssen, dass auch, glaube ich, ganz, ganz wichtig ist, das hat viel mit Flexibilität zu tun, dass die Hierarchien flacher sind. Dass mehr Verantwortung in Teams entsprechend grundgelegt sind, dass Teams sich auch ein Stück weit selbst organisieren. Ich mache mal ein Beispiel, wenn man Urlaub machen möchte oder man hat irgendwelche krankheitsbedingten Ausfälle, dass das nicht immer über die Personalabteilung kommuniziert und dann verwaltet und geregelt wird, sondern dass man Kommunikationsmöglichkeiten in Teams hat, wo man sich selbst organisiert, wo man sagt, klar, wenn du Urlaub machst, dann wird der Kollege das machen, und dass man das eben in so einem Team hat, also kleine Betriebe in große Betriebe bringt. Ich glaube, das ist auch etwas, was dem Naturell unserer jungen Leute viel eher entspricht als alte hierarchische Strukturen von oben nach unten.
Kerstin Dähne: Das würde ich auch unterstützen, und ich glaube halt der Punkt, den du ja gerade auch nochmal nachgefragt hattest, was wir als Unternehmen auch tun können. Ich glaube, unsere Aufgabe dabei ist auch, einfach nochmal viel transparent zu werben, was wir wirklich für Möglichkeiten haben, was eben genau für so eine Generation, welchen Beitrag sie leisten können, wenn sie sich für uns als Arbeitgeber entscheiden. Wir sind auch dabei, zum Beispiel wieder unsere Aktivitäten auszubauen, was so die Zusammenarbeit, die Kooperation mit Schulen betrifft. Einfach um da nochmal stärker klarzumachen, welche Ausbildungsmöglichkeiten haben wir, welche Einsatzmöglichkeiten haben wir auch, wenn man ein Studium beispielsweise abgeschlossen hat, weil ich glaube, diese Verknüpfung einfach herzustellen und nochmal deutlich zu machen, was auch hinterher eine praktische Anwendungsmöglichkeit ist. Ich glaube, das ist ganz wichtig. Wir sind auch gerade dabei, ich hatte ja gesagt, so das Thema zurückgehende Studierendenzahlen gerade in den Fächern, die wir suchen. Wir sind dabei, mit mit einigen Unis auch schon ins Gespräch zu gehen, weil die natürlich auch merken, unsere studierenden Zahlen gehen zurück. Wir müssen noch mal klarer machen, wenn du Elektrotechnik studierst, wenn du Maschinenbau studierst, wie sehen hinterher genau die Berufe aus, in die du gehen kannst? Was ist die praktische Anwendungsmöglichkeit? Und ich glaube, da gibt's noch ganz viele Möglichkeiten der Zusammenarbeit und der Kooperation, um auch einfach wieder so ein Stück weit Begeisterung für Technik und für bestimmte Berufe zu wecken. Und ich glaube, da haben wir neben den Bildungseinrichtungen als Unternehmen auch eine ganz wichtige Aufgabe, das mit voranzutreiben und zu unterstützen, weil wir am Ende merken werden, je weniger junge Menschen eine Ausbildung in technischen Bereichen beginnen oder ein Studium beginnen, das hat ganz direkte Auswirkungen auf uns.
Christine Launert: Das bedeutet also, dieser Blick hinter die Kulissen, Berufe einmal von nahem zu erleben, anzufassen, wie fühlt sich das überhaupt an, in diesem Unternehmen zu arbeiten? Was sind das konkret für Berufe, und habe ich überhaupt das Talent, diese Berufe auszuüben? Das ist eigentlich das A und o sowohl für die Bewerberinnen als auch für Unternehmen, da zusammenzukommen. Da geht ihr auch auf Messen, Praktika, hast du gerade angesprochen, Corona hat da viel Kontaktmöglichkeiten zumindest unterbrochen und für eine Generation auch echt schwierig gemacht. Und wie läuft es jetzt wieder an?
Kerstin Dähne: Positiv ist für uns natürlich im Moment, dass wir generell auch einfach gerade viel einstellen, durch unsere Transformation. Das heißt, da sind wir auch grundsätzlich wieder am externen Arbeitsmarkt unterwegs. Das waren wir auch früher nicht unbedingt in dem Ausmaß, und das merkt man sicherlich auch bei den Bewerberinnen und Bewerbern, die das wahrnehmen, dass wir aktiv auf der Suche sind. Und das ist natürlich auch dann für diejenigen, die noch studieren, beispielsweise sicherlich attraktiv, in so ein Unternehmen einzusteigen, wo man merkt, da ist ein Weg nach vorne, da ist eine Vision da.
Friedrich Hubert Esser: Aber ergänzend auch noch mal dazu: Corona hatte eben nicht nur ganz schlechtes, sondern auch ein bisschen was gutes, und das Gute war darin, dass wir massiv aufgeholt haben in Sachen Digitalisierung und auch verstärkt berufsorientierte Angebote wie auch Berufsinformative Angebote über das Internet bereitzustellen. Und hier ist sehr, sehr viel passiert. Das heißt Stichwort: Einblick in Berufe, Einblick in Betriebe über virtuelle Angebote, auch über eine vernetzte Struktur, die heute über die ganze Bundesrepublik gespannt ist. Das heißt, dass ich mir heute auch ohne Probleme die Ausbildungsmöglichkeiten in Rosenheim angucken kann, eben über Internetangebote, was ich vor Corona so nicht konnte. Also da ist auch vieles passiert, was gerade auch die Berufsorientierung für junge Leute einfacher macht. Wichtig ist auch, denke ich, dass man schauen muss in den Regionen, dass die Unternehmen und die Betriebe eben auch mit Schulen vernetzt sind. Das, glaube ich, ist nochmal ganz wichtig, also ein Stichwort: regionale Bildungsnetzwerke. Es gibt sehr, sehr schöne Beispiele darüber, dass beispielsweise Schulen Projektmonate haben in bestimmten Fächern, die sie gemeinsam mit Unternehmen machen. Das heißt also, dass letztendlich die Inhalte von Berufen mit dem, was die jungen Leute in den Schulfächern machen, über ein Projekt verbunden wird und dadurch auch Berufe kennenlernen und natürlich über den Kontakt zwischen den Schulen und den Unternehmen nachher auch das Vermitteln von Praktika und ähnliches viel, viel besser funktioniert. Also das, denke ich, ist auch nochmal eine ganz, ganz wichtige Strategie für eine Win Win Situation für die Betriebe, die eine bessere Akquisemöglichkeit haben, und für die jungen Leute, die eine bessere Berufsinformation und Vorbereitung haben.
Christine Launert: Sicherlich nicht für alle Unternehmen gleich einfach umzusetzen, aber wenn ich sie richtig verstanden habe, dann auf jeden Fall eine lohnende Investition für potenzielle Bewerberinnen. Auf jeden Fall virtuell sichtbar zu sein, zur Verfügung zu stehen und eben auch dann Mitarbeitenden zu ermöglichen, die virtuelle Arbeitswelt eben auch zu nutzen. Vielen Dank, ich lasse ihnen beiden jetzt das Schlusswort.
Kerstin Dähne: Ja, ich glaube, wir haben ja jetzt nicht nur in dem Podcast festgestellt, es gibt einfach viele, viele Herausforderungen, mit denen wir auch bei thyssenkrupp Steel nicht alleine sind, sondern das sind einfach Herausforderungen, die generell die Generation mit sich bringt, die der Arbeitsmarkt mit sich bringt. Aber ich glaube, was man auch spürt, ist, dass es sich lohnt, in diese Investitionen zu gehen, und ich finde, es macht auch Spaß. Macht auch Spaß mitzuwirken, das Unternehmen für Mitarbeitende attraktiver zu machen, für neue Generationen attraktiver zu machen, und ich glaube, da liegt ganz viel Potenzial, was wir nutzen können, und das stimmt mich sehr hoffnungsfroh.
Friedrich Hubert Esser: Ja auch nochmal für mich, zusammenfassend für die Betriebe ganz, ganz wichtig, dass sie einfach flexibler sind, auch mit Blick auf die unterschiedlichsten Zielgruppen, die man heute gewinnen muss. Wir reden über Menschen mit Migrationshintergrund, mit Fluchthintergrund, wir reden über Studienabbrechende, wir reden über Berufswechselnde. Wir müssen flexibler werden, auch mit unseren Ansprüchen, und auch immer eine Plattform bieten, wo man eben dann auch zielgruppengerecht einsteigen kann. Ein zweiter Punkt, glaube ich, der ganz wichtig ist, jedes Unternehmen, jeder Betrieb muss eine Geschichte haben. Das ist heute für junge Leute ganz, ganz wichtig. Wo steige ich ein, und wie werde ich Teil dieser Geschichte? Und thyssenkrupp hat ja auch eine Vita, die sehr interessant ist und auch spannend ist, und die muss man erzählen können. Ich glaube, das ist auch ein ganz wichtiges Akquise-Instrument, also eine Geschichte über das Unternehmen, was natürlich auch viel mit Unternehmenskultur zu tun hat. Ein dritter Punkt ist eben, dass ich Perspektiven eröffnen muss, das hatten wir herausgestellt, dass ist auch noch mal für junge Leute ganz, ganz wichtig, um auch eine Bindung zu erzeugen. Und das hat dann auch etwas zu tun, und das ist für uns als Bundesinstitut für Berufsbildung wichtig, Beruf als die Integration von Aus- und Weiterbildung zu sehen oder Fortbildung. Das heißt also, dass man nicht nur auf die Ausbildung schaut und sie fokussiert, sondern sagt, eben an die Ausbildung anknüpfend in die höhere Berufsbildung einsteigend, wir haben ja heute drei große Abschlüsse, die auch akademisch vergleichbar sind: Spezialist in Bachelor und den Master professional, sprich auf die Meisterprüfung, sich zuarbeiten, auch die Meister Plus Ebene in den Blick zu nehmen, also dass man auch über die gewerblich technischen Berufe eine wunderbare Karrieremöglichkeit entsprechend anbietet und unterstützt, die mit der akademischen Laufbahn vergleichbar ist.
Christine Launert: Ganz herzlichen Dank! Das sind gute Aussichten für die Zukunft der Arbeit, für die Unternehmen und für die Menschen, kurz, für die Next Generation Steel. Vielen dank ihnen beiden, Herr Professor Esser, Kerstin, dass sie heute für den Podcast meine Gäste gewesen sind. Danke euch fürs Zuhören. Ich hoffe, es hat euch gefallen. Falls ja, abonniert "gekocht, gewalzt, veredelt" gern auf Apple, Spotify oder einer anderen Podcastplattform, und lasst uns auch gerne Feedback da, zum Beispiel via Mail. Ihr erreicht uns unter [email protected] Ich freue mich auf die nächste spannende Stahlfolge des Podcasts mit euch.
Folge 8: #nextgenerationsteel – Wir starten in die Wasserstoff-Ära
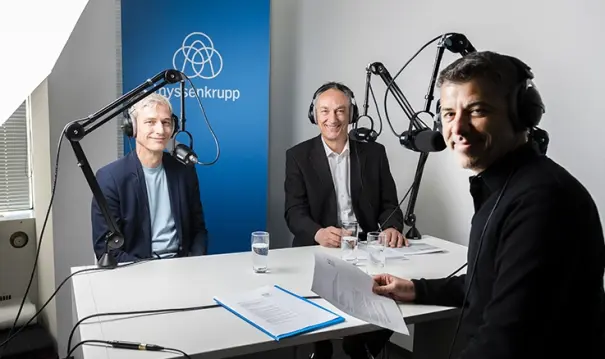
Mit der Auftragsvergabe für den Bau der ersten wasserstoffbetriebenen Direktreduktionsanlage an die SMS Group ist der Startschuss gefallen für ein weltweit einzigartiges Modellprojekt zur Produktion von grünem Stahl. In unserer neuen Podcast-Folge „gekocht, gewalzt, veredelt“ erklären unser CTO Dr. Arnd Köfler und Burkhard Dahmen, CEO der SMS Group, wie es dazu kam und was dieses Mega-Projekt für die Menschen und die Industrie bedeutet.
O-Ton: Lassen sie mich in aller Bescheidenheit sagen, dass sie heute einem historischen Moment für thyssenkrupp Steel beiwohnen.
O-Ton: Für Deutschland und insbesondere für Nordrhein-Westfalen markiert der heutige Tag den konsequenten Einstieg in die klimaneutrale Stahlerzeugung.
O-Ton: Eines der wichtigsten Projekte der Transformation der Industrie in unserem Land geht jetzt in die Umsetzung. Grüner Stahl.
O-Ton: Tausende von Arbeitsplätzen, die in der Industrie hiermit gesichert werden. Das ist auch ein starkes, großes Signal für die Region.
Mark Stagge: Liebe Zuhörerinnen, liebe Zuhörer, willkommen zu einer neuen Folge von "gekocht, gewalzt, veredelt" dem Podcast rund um das Thema Stahl. Die eingespielten Statements und O-Töne zu Beginn stammen von einer Pressekonferenz, die hier in Duisburg vor wenigen Wochen stattfand. Es ging um die Auftragsvergabe zum Bau der ersten Direktreduktionsanlage am Standort Duisburg. Den Auftrag hat die SMS Group aus Düsseldorf erhalten. Ein historischer Tag für beide Unternehmen und für den Stahl in Deutschland, denn es geht um große Fragen: Schaffen wir die Wende zur klimaneutralen Wirtschaft? Was kann die Stahlindustrie dazu beitragen? Was genau wollen thyssenkrupp Steel und SMS hier am Standort Duisburg bauen? Und wieso hilft das dem Klima? Wieso ist das gut für Deutschland und für Europa? Wir sprechen heute mit den beiden Menschen, die mit ihren Unterschriften den Startschuss für dieses Megaprojekt mit einem Gesamtinvestitions volumen von über 2 Milliarden Euro, den Bau der ersten Fabrik für klimafreundlichen Stahl am Standort Duisburg gaben. Ich freue mich sehr, den CEO der SMS Group, Burkhard Dahmen, und den CTO von thyssenkrup Steel, Dr. Arnd Köfler, begrüßen zu können. Mein Name ist Mark Stagge, ich leite die Presseabteilung bei thyssenkrupp Steel. Schön, dass Ihr dabei sein!
Mark Stagge: Die Unterzeichnung fand einige Tage vor der Pressekonferenz statt. Sie beide, Herr Dahmen, Arnd, haben die Unterschrift unter den Vertrag gesetzt. Im Fußball würde man jetzt fragen, wie haben sie sich dabei gefühlt, Herr Dahmen? Wollen sie mal das noch mal beschreiben?
Burkhard Dahmen: Es war für uns das erfolgreiche Ende einer langen Verhandlung. Wir haben über mehr als ein Jahr intensiv projektiert, wir haben intensiv alle möglichen Einflüsse extern, auch intern, gemeinsam erörtert und sind zu einer technischen Lösung gekommen, die für thyssenkrupp, für den Standort, die beste Möglichkeit ist, um hier CO2 freien Stahl herstellen zu können. Für uns ist es eine Riesen Erleichterung, den Auftrag bekommen zu haben, aber gleichzeitig eine Herausforderung. Ist so eine positive Grundanspannung, die wir jetzt haben, weil die Herausforderung, die vor uns liegt, in 46 Monaten dieses Projekt zu realisieren, schon eine große Herausforderung ist, sowohl zeitlich, budgetmäßig als auch von den vielen Kolleginnen und Kollegen, die an dem Projekt dann eingesetzt werden. Das sind doch einige 100, die daran arbeiten werden. Aber wir fühlen uns auch bestätigt in unserer Vision: turning metals green.
Mark Stagge: Okay, Arnd, wie war das für dich? Ein bisschen der Stift gezittert beim Unterschreiben oder alles in Ordnung gewesen?
Arnd Köfler: Na ja, in der Tat hat der Stift schon ein bisschen gezittert in der Frage, wie hoch die Investition jetzt wird. Da denkt man schon zwei, drei mal drüber nach. Aber die Freude hat überwogen, und wir sind richtig stolz gewesen. Nach sechs Jahren Vorbereitungszeit auf den ersten Schritt hin zur Dekarbonisierung haben wir jetzt wirklich einen Pflock eingeschlagen, und deswegen ist die Freude wirklich, sehr, sehr groß!
Mark Stagge: Es ist ja so, dass das der größte Einzelauftrag den SMS bekommen wird und der größte Auftrag, den wir bei thyssenkrupp Steel vergeben haben, in Summe. Arnd, vielleicht beschreibst du einmal, warum wir denn dieses Projekt auch in der Größenordnung überhaupt hier am Standort durchziehen müssen.
Arnd Köfler: Wir sind ja aufgebrochen, vor einigen Jahren, ein Konzept zu entwickeln, den Standort hier mit 20 Millionen Tonnen zu dekarbonisieren bis spätestens 2045, und da muss man irgendwann mal auch den ersten Schritt gehen. Und der erste Schritt ist eben jetzt damit getan, dass wir zusammen mit der SMS diese erste Anlage, die einen ersten Hochofen ersetzen wird, dann auch bauen werden, und wir werden mit diesem ersten Schritt und dem, was dann bis 2030 folgen wird, schon mehr als 30 Prozent der CO2 Emissionen hier mindern. Und das ist nicht mehr und nicht weniger genau das Ziel, und, wie man so schön sagt: license to operate. Wir müssen dekarbonisieren. Wir haben hier die Verpflichtung, eben mit den 20 Millionen Tonnen auch den entsprechenden Beitrag zum Klimaschutz hier umzusetzen. Wir haben die riesen Chance, hier mitten im Ruhrgebiet, in einem Industriegebiet, das durch Energie durch Chemie, durch Stahl eben geprägt ist, mit der perfekten Infrastruktur hier auch den Nachweis zu bringen, dass es gelingen wird, und alle Menschen hier mitzunehmen, unsere Mitarbeiter, unsere Kolleginnen und Kollegen, aber natürlich auch die Wohnnachbarschaften und alles, was hier durch thyssenkrupp eben im Ruhrgebiet auch geprägt ist.
Mark Stagge: Zurzeit emmitieren wir ja zweieinhalb Prozent der deutschen CO2 Emissionen. Stahl insgesamt steht für ca. sieben Prozent der Emissionen in Deutschland. Arnd, kannst du einmal beschreiben, was für Einspareffekte wir denn erzielen, wenn wir allein diese erste Anlage hier schon bauen?
Arnd Köfler: Ja, die Prozente, die du genannt hast, sind rund 20 Millionen Tonnen, die wir hier an dem Standort hier im Duisburger Norden, emmitieren, und Ziel ist es jetzt, mit dem ersten Schritt circa 30, etwas über 30 Prozent, dann in Summe bis 20-30 zu vermindern, und das werden wir auch erreichen.
Mark Stagge: Das heißt, aus Sicht der Klimaziele ist klar, dass wir was ändern müssen. Wie kommt man dann auf einen Anbieter wie SMS? Das heißt, wir haben uns für eine Konzeption entschieden, und gehen dann auf den Markt und gucken, wer kann uns diese Anlage bauen? Wie sind wir dann vorgegangen? Es gibt ja mehrere Anbieter, oder?
Arnd Köfler: Ja, genau, es gibt andere Anbieter, aber auch nicht viele, die diese Technologie anbieten. Drei Stück gibt es weltweit, einer fällt immer aus, sofort, aus lizenztechnischen Gründen, sodass wir mit zwei Partnern intensiv in den letzten zwölf Monaten, Herr Dahmen hat es schon gesagt, in den letzten zwölf Monaten zusammengearbeitet haben und die etwas unterschiedlichen Konzepte weiter vorangetragen haben, eine Wettbewerbssituation aufrecht gehalten haben. Aber letztendlich glaube ich und bin fest davon überzeugt, dass wir mit der SMS jetzt einen Partner an der Seite haben, der uns insbesondere da, wo wir nicht die Stärken haben, mit seinen Stärken, die Montage aus einer Hand auch durchzuführen, zum Beispiel, und natürlich die Technologie, insbesondere auch bei den Einschmelzern, an der Seite haben werden, und wir freuen uns jetzt wirklich, dann von diesen Vorbereitungen in die Realisierung gehen zu können.
Mark Stagge: Herr Dahmen, wann haben sie das erste mal einen Anruf bekommen aus Duisburg von thyssenkrupp Steel mit der Frage, könnt ihr uns mal so eine kleine Anlage bauen für eine noch damals unbestimmte Summe? Jetzt wissen wir, dass es 1,8 Milliarden Euro ungefähr sind.
Burkhard Dahmen: Ja, klein ist ja wahrlich nicht. Also das ist der größte Auftrag in unserer Unternehmensgeschichte, wie sie eben schon ausgeführt haben. Also, es ist so, dass wir jahrzehntelange Partnerschaft schon haben zwischen thyssenkrupp Steel und der SMS Group und auch den beteiligten Unternehmen, die in der Zwischenzeit alle zur SMS Group dazugehören. Ob das Paul Wurth, ist oder die mea in Mönchengladbach. Insofern ist das schon eine jahrzehntelange Partnerschaft. Da ist man im intensiven Dialog, und wir haben ja auch vor über 25 Jahren zusammen auch die erste Gießwalzanlage hier in Duisburg gebaut. Das war auch ein Meilenstein, eine ganz neue Technologie, die wir zusammen eingeführt haben in den Markt und ausgebaut haben, weiterentwickelt haben, und so sind wir auch in der Dekarbonisierung, stehen wir ja vor einer riesigen Herausforderung. Die Stahlindustrie insgesamt, aber auch wir als Anlagenbauer und auch die Stahlhersteller sowie thyssen, und das kann man nur gemeinsam meistern, und so waren wir immer schon im Dialog. Und ja, vor ungefähr 2 Jahren, als das Thema auch politisch und gesellschaftspolitisch immer stärker in den Fokus rückte, ist man natürlich dann auch in die Diskussion stärker eingestiegen. Aber ich muss sagen, den Wettbewerb haben wir schon gespürt, der war also richtig intensiv, und wir haben aber auch nichts gegen Wettbewerb, weil das fördert dann auch, letztendlich erzeugt einen Zugzwang in der Weiterentwicklung des Prozesses, des technischen Prozesses und auch der Produkte, und hier sind wir zu einem ganz neuen Ergebnis gekommen, eben mit einer Direktreduktionsanlage, mit zwei Einschmelzen. Das ist so noch nie gebaut worden und hat große Vorteile gegenüber der Kombination Direktreduktion mit einem Elektrostahlwerk.
Mark Stagge: Ja, das werden wir gleich noch mal kurz beschreiben müssen, damit das auch verständlich wird, warum wir das genauso bauen. Wie lange haben denn die Verhandlungen insgesamt gedauert?
Burkhard Dahmen: Wir hatten einen sehr intensiven Austausch die letzten zwölf Monate. Wir haben einen Vorab-Engineering, Genehmigungs-Engineering Auftrag bekommen, der Wettbewerber übrigens auch. Damit hat sich thyssen dann auch abgesichert, dass sie wirklich zwei vergleichbare, vollständig ausgearbeitete Angebote mit allen Spezifikationen erhalten hat, um entsprechend Äpfel mit Äpfeln zu vergleichen und dann die richtige Entscheidung zu treffen, was sie dann auch getan haben, indem sie uns ausgewählt haben. Aber es war ein sehr intensiver Prozess mit über 100.000 Engineering Stunden, die wir dort reingesteckt haben. Das ging nicht nur um das Thema DRI-Anlage und dem Einschmelzer, sondern es ging auch um das Thema Fabrikplanung, Layout, Emissionsberechnung, all die Dinge, die fürs Genehmigungsverfahren auch notwendig sind, auch die gesamten Angaben für Massen und Mengen, für Stahlbau und Fundamente und Gebäude, und hier bauen wir ja auch deutlich in die Höhe. Wir haben ja eine Fläche von 500 mal 550 Metern, um mal eine Dimension zu nennen: 80.000 Tonnen Equipment, die geliefert werden, da von 40.000 Tonnen Stahl ist ein Wort, das sind über 3.200 LKW-Ladungen, wenn man es mal so ausdrückt, und das ganze Thema geht natürlich auch in die Höhe. Das heißt, wir werden die DRI-Anlage auch bis zu einer Höhe von 135 Meter entsprechend bauen müssen, um den Prozess zu gewährleisten. Also, das wird schon ein neues Wahrzeichen für thyssen und für die Stahlstadt Duisburg, und ich glaube, dieses Wahrzeichen steht dann auch für den Aufbruch in den CO2 freien Stahl, in eine neue moderne Stahlerzeugung, und das ist mit "first of its kind" ein Meilenstein, der entsprechend dann als Wahrzeichen da auch für steht, und insofern bin ich froh und stolz, dass wir hier daran mitwirken dürfen.
Mark Stagge: Wir müssen noch einmal erklären, warum wir denn genau so eine Anlage bauen. Die klassische Prozess zur Roheisen-Herstellung funktioniert mit Kohle im traditionellen Hochofen. Was genau machen wir jetzt anders, oder warum haben wir uns für diese Konzeption mit dem Einschmelzer entschieden?
Arnd Köfler: Ja, das ist einer der Kerninnovationen, die unser Konzept eigentlich darstellt. Wir hatten uns von vornherein die Aufgabe gestellt, möglichst nicht die entsprechende Herstellung von Stahl im Sinne unserer Kunden zu verändern, und dann gab es eigentlich nur eine Lösung. Wir müssen wieder Roheisen erzeugen, und dafür haben wir nach einer Lösung gesucht, und die Direktreduktionsanlage übernimmt praktisch den Teil des Hochofens, der den Sauerstoff aus dem Erz entfernt, und wir brauchten dann ein Einschmelzaggregat, ein elektrisches Einschmelzaggregat, das aus diesem festen Material, ja aus dem dann praktisch keine Sauerstoffmenge mehr entfernt werden muss, nur noch ein Einschmelzen, in Anführungszeichen, erzeugen wird. Und das haben wir mit der Technologie der Einschmelzer, der "Submerged Arc Furnace" heißt es technisch richti, jetzt vor der Brust. Das können wir so lösen, und dann kommt eben unten wirklich wieder das gleiche raus, was aus einem Hochofen rauskommt, nämlich Roheisen und zusätzlich dann auch dekarbonisierte Schlacke, und im Stahlwerk wird nichts verändert. Wir können unsere Güten weiter unseren Kunden so anbieten, was eben bei dem anderen Konzept mit nem klassischen Elektrolichtbogenofen nicht der Fall ist.
Mark Stagge: Das heißt, wir können dieses Versprechen an die Kunden sozusagen geben, dass wir, was die Produkte anbetrifft, da keine Veränderung haben an der Stelle.
Arnd Köfler: Genauso ist es.
Mark Stagge: Dieses Konzept mit dem Einschmelzer, das ist ja in der Form auch noch nicht gemacht worden oder erst recht nicht in der Größe. Das ist wahrscheinlich dann, Wir nennen das "first of its kind-Anlage". Oder haben wir bei SMS Projekte, die sie in der gleichen Art und Weise auf der Welt bauen, oder ist das hier die erste Anlage, die in dieser Konzeptionierung gebaut wird?
Burkhard Dahmen: Also, "first of its kind" Stimmt in Bezug auf die Kombination Direktreduktion mit dem Einschmelzer. Wir haben sowohl Direktreduktionsanlagen in der Größenordnung 2,5 Millionen Tonnen pro Jahr. Das ist die größte, die überhaupt je gebaut wurde. Davon haben wir schon einige gebaut, von den Einschmelzern haben wir auch schon viele gebaut, aber nicht für die Anwendung im Stahlbereich, sondern das ist im ferrometallurgischen Bereich. Insofern ist hier mit "first of its kind" gemeint, dass die beiden bewährten Produkte, Aggregate in einer neuen Kombination zusammengeführt werden. Also insofern ist das kein produktbezogenes Neuland, aber es ist ein Neuland bezogen auf den Prozess, und den haben wir aber auch in vielen Versuchen entsprechend hergeleitet und validiert, und da gibt es kein Risiko, dass dieser Prozess und dann noch in Verbindung mit nicht fossiler Energie, sondern mit 100 Prozent Wasserstoff entsprechend betrieben werden kann und auch betrieben werden wird, und das führt dann zu dem CO2 freien Stahl.
Mark Stagge: Wenn die Anlage dann fertig gebaut ist im Jahr 2026, werden wir mit großer Sicherheit noch nicht genügend Wasserstoff zur Verfügung haben. Was tun wir dann? Werden wir die Anlage auch 1 zu 1 mit Erdgas betreiben und dann auf Wasserstoff wechseln?
Arnd Köfler: Ja, das ist richtig. Also die Anlagen, die Direktreduktionsanlagen sind konzipiert worden, ursprünglich und seit 50 Jahren erfolgreich im Betrieb weltweit, um Erdgas eben zu nutzen. Wasserstoff haben auch schon mehrere Anlagen testweise eingeführt, aber aufgrund der Kosten ist es nie irgendwo dann industriell für eine lange Zeit genutzt worden. Deswegen werden wir die Anlage auch mit Erdgas starten. Aber wir haben hier eben diese einzigartige Situation, dass um uns herum zum Beispiel auch schon ein Wasserstoffnetzwerk ja besteht, und wir gehen fest davon aus, dass wir dann auch vielleicht schon vor der geplanten Wasserstoff Phase, das ist 28, dann auch schon Wasserstoff zur Verfügung haben werden und relativ zügig dann auch Wasserstoff hochfahren werden.
Mark Stagge: Okay, und wenn wir Erdgas nutzen, haben wir auch schon einen CO2-Einspareffekt.
Arnd Köfler: Ja, und zwar 50 Prozent schon, weil im Erdgas natürlich auch viel Wasserstoff enthalten ist. Das ist schon eine Einsparung. Deswegen ist es von vornherein eben auch eine CO2-Reduktion. Aber das Ziel ist ganz klar, den Wasserstoff hier so schnell wie möglich einsetzen zu können, und das wird uns auch gelingen.
Burkhard Dahmen: Wir haben auch noch einen anderen Vorteil bei diesem Prozess mit dem Einschmelzer gegenüber dem Elektrostahlwerk. Es fällt ja immer Schlacke an, bei dem Schmelzprozess, und die Schlacke, die wir hier in dem Reduktionsofen haben, die kann anschließend auch so wie auch früher beim Hochofen mit der Hochofenschlacke zu Hüttensand verarbeitet werden, was man der Zementindustrie wieder dann entsprechend verkaufen kann. Also insofern hat man kein Abfallprodukt, sondern einen Mehrwert, den man dann auch veräußern kann, und das ist im Elektro Stahlschmelzprozess nicht möglich.
Mark Stagge: Jetzt haben wir festgestellt, dass wir sowohl als auftragvergebendes Unternehmen den größten Auftrag sozusagen vergeben haben an SMS, den größten Auftrag, den sie erhalten haben. Wie geht man jetzt so ein Projekt in dieser riesigen Größenordnung an, organisatorisch? können sie das mal kurz beschreiben, Herr Dahmen, wie jetzt die nächsten Schritte sind, was genau wir jetzt tun werden?
Burkhard Dahmen: Also, der erste Schritt ist, dass wir ein internes Kickoff Meeting gemacht haben mit allen Beteiligten, die in der Vertriebsphase dabei waren. Aber jetzt in der Umsetzung kommen natürlich noch viele andere Kollegen bei uns aus dem Unternehmen dazu. Das hat stattgefunden. Da wird dann ein entsprechender Zeitplan detailliert ausgearbeitet, wer mit welchem Bereich, mit welchen Kollegen welche Arbeit zu erfüllen hat, bis wann. Aber das können wir nicht alleine machen, sondern das geht so wie im Vertriebsprozess auch schon im sehr engem Schulterschluss gemeinsam mit den Spezialisten und den Projektbeauftragten bei thyssen und bei der SMS Gruppe zusammen, und wir haben einen straffen Zeitplan. 46 Monate hört sich sehr lang an, aber wenn man sieht, wir haben 80.000 Tonnen an Equipment zu liefern, davon sind auch natürlich 40.000 Tonnen Stahlbau, aber 80.000 Tonnen, das ist ein Wort, und das muss man erst mal beibringen, und wir können das nicht sofort bestellen. Wir müssen sie erst mal konstruieren, müssen sie erst mal zeichnen, wir müssen erst mal die Maße alle fest legen und die Details. Also, da ist sehr viel zu tun in den 46 Monaten, und dazu gehört natürlich dann auch der Aufbau, die Montage und die Inbetriebnahme, bevor überhaupt die ersten Eisenpellets aus der DRI-Anlage unten rauskommen und dann in den Einschmelzer zugeführt werden können. Und ja, da haben wir viel vor der Brust. Aber wir sind hoch motiviert, weil das ist "first of its kind", heisst, für jeden Ingenieur eine Riesenherausforderung. Man hat Spaß daran, was Neues zu machen, und wir haben ein großes Versprechen abgegeben, bezogen auf die Leistung und bezogen auf den Zeitplan, und wir setzen alles daran, dass wir das einhalten, weil das ist unsere Reputation und durch die Nachbarschaft, die wir haben, wir haben ja eine räumliche Nähe, nicht nur, dass wir uns auch sprachlich ganz einfach verständigen können, wir haben auch eine jahrzehntelange Kooperation und eine Basis, wo man sich kennt, wie die beiden Häuser intern funktionieren, und gleichzeitig haben wir eben auch die räumliche Nähe, um, wenn man was hakt, entsprechend Verstärkung beibringen oder ranholen zu können, und ich bin überzeugt, dass das in der Form zum vollen Erfolg wird.
Mark Stagge: Arnd, bei dir ähnliche Einschätzung, was den Projektfortschritt angeht?
Arnd Köfler: Da bin ich fest von überzeugt, dass es ein Erfolg wird. Aber vielleicht erzähle ich noch mal ein bisschen, wie wir uns auch organisatorisch diesem Thema entgegenstellen, das begleiten werden. Wir haben ja schon viel Erfahrung damit, dass wir für die unterschiedlichen Schritte zur Dekarbonisierung von einer Konzept/Strategieentwicklung, Konkretisierung, was wollen wir bauen, und dann die Vorbereitung, bis man zu so einer Vergabe kommt, haben wir ja schon mehrere organisatorische Veränderungen durchgeführt. Wir haben auf der anderen Seite auch gelernt, dass wir in den letzten 15 Jahren rund 350 Millionen Euro jedes Jahr investieren mussten, also Großprojekte umsetzen mussten. Jetzt haben wir mit der Strategie 20-30 ein Riesenblock von circa einer 1 Milliarde Euro on Top gekriegt seit 3 Jahren, und jetzt kommt eben dieses große Projekt noch dazu, und das erfordert natürlich immer wieder organisatorische Anpassungen, und wir sind jetzt in der dritten Phase: erst Strategie und Konzeptentwicklung, dann Heranführung an eine Vergabefähigkeit, die haben wir jetzt hinter uns, und jetzt sortieren wir uns gerade so, dass wir eben in Zusammenarbeit mit SMS die beiden Teams, die das umsetzen sollen, die den eigentlichen Neubau jetzt realisieren sollen, auch optimal aufgestellt haben.
Mark Stagge: Vielleicht wollen wir noch einmal die Perspektive erweitern, um einmal zu schauen, dieses Projekt, das wir hier in Duisburg bauen, was heißt das für den Stahlstandort Deutschland, was heißt das für den Stahl in Europa? Könnte man dieses Konzept auch an jeder anderen Stelle der Welt bauen? Also warum genau machen wir das hier am Standort Duisburg, hier in Deutschland im Ruhrgebiet?
Arnd Köfler: Ja, ich knüpfe an das an, was ich eingangs schon gesagt habe. Wir befinden uns hier eigentlich im Zentrum der europäischen Industrie, Schwerindustrie mit vielen Energieunternehmen, mit Chemie-, Petrochemieunternehmen. Wenn man hier einen Kreis zieht von 150 Kilometern, 200 Kilometern, dann hat man Antwerpen, dann hat man Rotterdam, dann hat man Amsterdam, man hat die chemischen Standorte auf der Benelux-Seite, man hat im Süden des Ruhrgebiets in Anführungszeichen bis Köln. Man möge es mir verzeihen, Köln zum Ruhrgebiet mitzuzählen, haben wir viele chemische Werke im Norden mit Evonik und so weiter, und das ist ein Ökosystem, das eben von Energiebereitstellung, Grundstoffherstellung und eben finale Produkte, wie viele Artikel der Stahlindustrie und dann die weiterführenden Anwender. Dann, im Osten des Ruhrgebietes hat man ein riesiges Ökosystem, und dann auch, die sozialen Herausforderungen. Wir werden ja hier ganz viele neue Qualifikationen brauchen. Wir brauchen viele Menschen, die jetzt die Transformationen mit zusätzlich umbauen und nachher dann wieder ein fertiges Werk haben, wie es vorher in seiner kapazitiven Ausstattung war, und das in einem sozialen Umfeld, das durch die Montanmitbestimmung auch wirklich geübt und gut geübt ist. Und ich sage, wenn es hier nicht funktioniert, wo soll es denn dann funktionieren? Das ist unsere Pflicht, dass es hier funktionieren wird und es zeigt, dass wir die Dekarbonisierung auch woanders werden stemmen können.
Burkhard Dahmen: Ich glaube, es ist bekannt, Stahl ist einer der größten Emmitenten der CO2 Belastung für die Umwelt, und der Klimawandel ist uns allen mehr als gewahr, und ich sage mal, auf der anderen Seite steht thyssen und auch ein bisschen die SMS für ein erfolgreiches Unternehmen mit weltweiter Reputation und thyssen: überall, wo man in der Welt hinkommt, und man sagt, man hat Referenzanlagen für thyssen gebaut, dann hat man sofort die Türen offen, weil alle wissen, da kommt der beste Stahl her, und dass der natürlich bis heute CO2 emmitierend ist, ist verfahrenstechnisch bedingt, und wir sind stolz darauf und froh, dass wir hier die erste Anlage der Welt etablieren können, wo in einem bestehenden Hüttenwerk in den Rahmenbedingungen, die vorherrschen, mit Anlagen, die bereits im Betrieb sind, wir eine Dekarbonisierung, also einen CO2 freien Stahl ermöglichen können, und das ist "first of its kind". Das heißt auch, das ist eine Referenz für alle anderen Hüttenwerke, weltweit entsprechend den Weg zu gehen, und da führt auch kein Weg dran vorbei. Also insofern ist das auch für thyssen ein Meilenstein in eine erfolgreiche Fortführung der Reputation als führendes Stahlunternehmen.
Mark Stagge: Das heißt, sie sehen auch Stahl als Werkstoff in Deutschland, Europa als unverzichtbar an?
Burkhard Dahmen: Wir haben, glaube ich, alle in den letzten Jahren einmal durch die Unterbrechung und Schwierigkeiten in der Logistik, in den Lieferketten, aber zum anderen auch durch den russischen Angriffskrieg in der Ukraine gemerkt, wie plötzlich vermeintlich belastbare Lieferketten zusammenbrechen oder unsicher werden. Und Stahl ist ein Werkstoff mit Zukunft, ist der Werkstoff der Zukunft, weil er ist nicht ersetzbar durch andere Werkstoffe, zumindest in vielen Anwendungsbereichen, und wir brauchen in Deutschland, das ist meine persönliche Überzeugung, eine kritische Grundversorgung der Stahlerzeugung. Wir können uns nicht auf Importe aus irgendwelchen heutigen stabilen Regionen verlassen, die morgen vielleicht unsicher werden, ob das 50 Prozent sind, 40, 60 der heutigen 40 Millionen Gesamtkapazität in Deutschland, das muss der Markt beurteilen, aber wir brauchen eine kritische Versorgung, und dafür ist die Dekarbonisierung der richtige Schritt, und das ist der erste, den wir hier tun, und ich bin zuversichtlich, dass da noch weitere folgen werden, nicht nur in Deutschland, in Europa, aber auch weltweit.
Mark Stagge: Also ein klares Bekenntnis, sozusagen erst mal hier am Standort dieses Pilotprojekt zu starten und die Wertschöpfung hier zu sichern, auch für die Folgeindustrien, die wir haben, für die ganzen Kundenindustrien für die Anwender, für die Stahlanwender, die eben auch darauf angewiesen sind, eine sichere Versorgung mit Stahlprodukten auch in einer gewissen Qualität zu bekommen.
Burkhard Dahmen: Das ist ein Referenzprojekt, dem so viel öffentliche Aufmerksamkeit auch von Wettbewerbern von thyssen, auch von Wettbewerbern von SMS gezollt wird. Also, das wird schon seine Nachahmer finden, und ich bin froh, dass es uns gelingt, hier in Deutschland genau diesen ersten "first of its kind"-Ansatz zu gewähren. Denn ja, man sagt immer Old Economy, und was heißt das eigentlich? Also, Stahl ist nicht old, sondern Stahl ist modern, und es ist ein Werkstoff, den man braucht. Und Made In Germany war über viele Jahrzehnte ja auch etwas, was uns als Exportweltmeister groß gemacht hat, und mit der neuen Technologie haben wir auch wieder etwas, können wir etwas zeigen, dass wir auch in Zukunft aus Deutschland heraus Technologie weiter exportieren werden und können und nicht von irgendwelchen anderen, die es nur günstiger und billiger machen, entsprechend abgehängt werden, sondern wir sind moderner, fortschrittlicher, und Technologie lässt sich eben gut verkaufen.
Mark Stagge: Was heißt das für die Arbeitsplätze, die am Standort, wenn wir dieses Projekt umsetzen? Wir brauchen ja auch neue Qualifikationen. Wie gehen wir mit dem Thema um?
Arnd Köfler: Ja, das ist eine gute Frage. Wir haben ja festgestellt seit einem Jahr, dass der Arbeitsmarkt sich gedreht hat. Es ist wirklich schwierig, Menschen für die Stahlindustrie noch zu begeistern. Auch in anderen Industrien ist es schwer geworden. Aber ich denke, dass wir hier durch das Zeichen, dass wir in die Zukunft investieren und in eine grüne Zukunft mit neuen Innovationen, eben auch Menschen jetzt für unsere Bedürfnisse auch begeistern werden. Und das bedeutet ganz konkret, dass wir für die Errichtung dieses ersten Schrittes alleine schon 350 Menschen zusätzlich benötigen, von normalen Neubauingenieuren, aus dem Elektrofachgebiet, aus dem mechanischen Fachgebiet, aber auch für das Betreiben nachher viele Fachleute, zusätzlich 350, und dass eben mit diesem ersten Schritt, die hier am Standort schon beschäftigten Mitarbeiterinnen und Mitarbeiter natürlich auch eine zusätzliche Sicherheit haben, in Zukunft hier einen Arbeitsplatz zu haben, ohne den ersten Schritt in eine Dekarbonisierung, sicherlich nicht so sicher wäre.
Mark Stagge: Das heißt, wir haben neue Arbeitsplätze, neue Qualifikationen. Also für jemanden, der einen Job ausüben will, in dem er Zukunft gestalten will, der wäre hier am richtigen Platz bei uns in Duisburg.
Arnd Köfler: Ja, absolut, genau da ist hier ein Zeichen gesetzt, dass wir genau innovativ in die Zukunft, die Dekarbonisierung, investieren werden, und ich bin fest davon überzeugt, dass es viele junge Menschen, aber auch Menschen, die schon Berufserfahrung haben, auch anlocken wird und uns helfen werden, hier diese Ziele dann auch umzusetzen.
Mark Stagge: Arnd, wann werden wir das erste sehen, hier, auch bei uns, auf dem Baufeld? Wie sind da die nächsten Schritte?
Arnd Köfler: Ja, das erste, was wir wirklich sehen werden, ist das Freiräumen der neuen Anlagen beziehungsweise des Feldes, wo wir dann bauen werden. Das wird ja das Lager in Walsum sein und die Brammen, die versuchen wir gerade auszulagern, beziehungsweise zu verwerten, und dann werden wir ab Juni die ersten Sondierungsbohrungen dort vornehmen und die entsprechenden Vorbereitungen für das Baufeld dann tatsächlich sehen. Und dann wird sukzessive in den nächsten Jahren, dann bis zum Ende des Jahres 2026, dann die nächsten Schritte Hoch- und Tiefbau, Stahlbau und dann die Montage letztendlich vollzogen werden, so dass wir dann Ende '26 den ersten Abstich werden erleben können.
Mark Stagge: Okay, und beim Genehmigungsverfahren hoffen wir auf die neue Deutschlandgeschwindigkeit, die Bundeskanzler Scholz verkündet hat, oder?
Arnd Köfler: Ja, da hoffen wir drauf. Wir haben aber auch Grund, dass wir glauben können, dass das funktioniert. Also die entsprechenden Behörden, insbesondere hier in Düsseldorf, aber auch die Stadt, haben sich auch vorbereitet. Wir haben auch seit zwei Jahren schon regelmäßig Gespräche mit den entsprechenden Genehmigungsbehörden geführt. Die haben sich auch organisatorisch verändert, auch ressourcentechnisch etwas verstärkt, sodass wir guten Mutes sind, dass sie uns auf jeden Fall willentlich wirklich gut begleiten werden. Und ich denke, dass hier auch jetzt mit dem Rückenwind, den wir seit letztem Jahr im gesamten Bundesgebiet ja spüren, bei Genehmigungen dann auch hier die Geschwindigkeit dann vollzogen wird, die wir benötigen, um den Zeitplan einhalten zu können.
Mark Stagge: Zum Abschluss noch einmal die Frage nach der Unterzeichnung, nach der Auftragsvergabe, die wir gemeinsam vollzogen haben. Was heißt denn dieses Projekt, wenn sie persönlich mal das bewerten wollen? Was heißt denn das Projekt für sie beide, für dich, Arnd und für sie, Herr Dahmen?
Burkhard Dahmen: Auf der einen Seite eine riesige Herausforderung, die vor uns liegt, mit großem Respekt vor der Aufgabe, aber auch dem Wissen um die tolle Mannschaft, die bei uns im Hause verfügbar ist, um diese Herausforderung anzugehen. Wir sind alle voll begeistert, stehen hinter dieser Herausforderung, und in meiner über 30 jährigen Karriere hier beim Anlagenbau muss ich sagen, das ist die größte Herausforderung, die wir haben. Aber ich bin auch stolz, diese Herausforderung angehen zu dürfen und zu können, und ich freue mich schon auf Ende 2026, wenn wir hier den Knopf drücken, um die erste Schmelze entsprechend zu sehen.
Arnd Köfler: Ja, sieht bei mir ähnlich aus. Die Freude hat auf jeden Fall überwogen, aber sie ist begleitet von einer großen, großen Portion Demut, weil die eine Aufgabe zwar in den letzten sechs Jahren, jetzt in der gesamten Konzeption und Vorbereitung abgeschlossen ist, aber eben auch ein langer Weg bis zum Errichten und in Betriebnehmen der ersten Anlage, die ja auch parallel dann noch weiterverfolgt werden muss, hin zur Konzeption einer zweiten Anlage und den nächsten Schritten, und das wird sehr viel Kraft kosten uns alle. Aber so, wie auch SMS ein gutes Team hat, sind wir auch sehr, sehr gut aufgestellt. Wir haben viele wirklich sehr engagierte Mitarbeiterinnen und Mitarbeiter, und wir haben ja auch festgestellt in den letzten zwei Jahren, dass fast jeder Mitarbeiter, den man fragen kann von thyssenkrupp, weiß, was wir an Innovation dort errichten werden, und das auch wirklich gut findet und begleiten wird. Und mit dieser Kraft im Rücken oder neben mir freue ich mich, diese Aufgabe weiter angehen zu können.
Mark Stagge: Okay, dann sind wir gespannt auf die nächsten Schritte bei diesem Megaprojekt also das ja für unsere beiden Unternehmen in der Form noch nicht umgesetzt worden ist. Vielen Dank für das Gespräch. Weitere Informationen zur Sendung finden wir in den Shownotes der Podcastfolge. Vielen Dank.
Burkhard Dahmen: Dankeschön.
Arnd Köfler: Gerne. Danke.
Mark Stagge: Das sind gute Aussichten für das Klima, den Standort, die Produkte und die Menschen, kurz für die Next Generation Steel. Vielen Dank an unsere Gäste für den informativen Austausch. Danke fürs Zuhören. Ich hoffe, es hat euch gefallen. Falls ja, abonniert "gekocht, gewalzt, veredelt" gern auf Apple, Spotify oder einer anderen Podcast-Plattform, und lasst uns auch gerne Feedback da, zum Beispiel via Mail an [email protected] Ich freue mich auf weitere spannende Stahlthemen mit euch.
Folge 7: FBA 10 – Mehr als nur Oberfläche
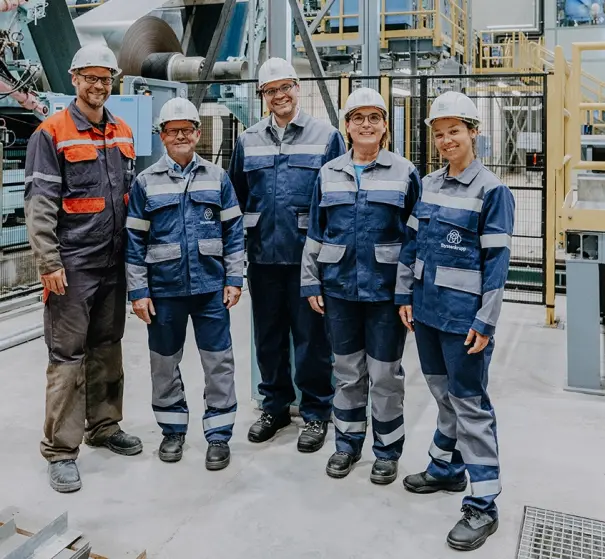
Weltweit machen die Automobilhersteller Tempo beim Umstieg auf E-Mobilität und die Nachfrage nach hochwertigen, feuerverzinkten Stählen steigt und steigt. Mit dem Bau einer zweiten, hochmodernen Feuerbeschichtungsanlage, der FBA 10, auf der Westfalenhütte können wir unsere Kapazitäten steigern und setzen Maßstäbe in puncto Nachhaltigkeit. Was die neue Anlage alles zu bieten hat und warum wir den Standort Dortmund als Kompetenzzentrum für die Automobilindustrie stärken, das erfahren Sie von Clemens Trachternach, Folke Redam, Volker Smukala und Klaus Janhofer in der neuen Folge unseres Podcast „gekocht, gewalzt, veredelt“.
Antonie Bauer: Bagger und Kräne sind verschwunden. Zwischen den Wegen wächst das Gras in der Sonne, und schon von weitem sehe ich die blauen Türme, die aus einem lang gestreckten, in verschiedenen Grüntönen gestreiften Bau ragen. Ich bin auf dem Weg zur FBA10, der neuen Feuerbeschichtungsanlage von thyssenkrupp Steel auf der Westfalenhütte.
Herzlich willkommen in Dortmund! Herzlich willkommen zur neuen Folge unseres Podcasts „gekocht, gewalzt, veredelt“. Mal angenommen, ich würde jetzt ganz von vorne anfangen und alle Highlights nennen, sie sich hier auf dem traditionellen Gelände der Westfalenhütte zugetragen haben, dann wäre diese Folge ungefähr 100 Mal so lang wie alle anderen.
Mehr als hundertfünfzig Jahre Stahlgeschichte haben sich nämlich hier abgespielt. Wer heute vor dem Werksgelände steht, stellt fest, dass nichts mehr raucht und lärmt, wird hier etwa gar nichts mehr produziert? Weit gefehlt. Hier arbeiten rund 1.400 Mitarbeiter:innen, um die 50 Ausbildungsplätze gibt es hier, es wird rund um die Uhr an sieben Tagen produziert.
Was genau und warum die Westfalenhütte und der moderne, grün-blau gestreifte Neubau für die Zukunft des Stahls und der Region stehen, das werden wir gleich erfahren. Vier Experten sind heute mit mir hier unterwegs in der neuen Anlage und alle kennen sich bestens aus mit dem wieso, weshalb, warum die FBA 10 ein weiteres Highlight in der langen Geschichte dieses Ortes markiert.
Meine Gesprächspartner:innen Heute sind Clemens Trachternach, Teamleiter der FBA 10, Folke Redam, Leiterin Qualität, Volker Smukala aus dem Produktmanagement und Klaus Janhofer, Leiter des Kaltwalzwerkes 3. Ich bin Antonie Bauer und ich freue mich, dass ihr heute mit mir hier seid. Hallo.
Klaus Janhofer: Mein Name ist Klaus, vielen Dank, dass ich hier an der Runde teilnehmen darf.
Volker Smukala: Ja, Volker hier, ich bin auch stolz, dabei sein zu dürfen
Folke Redam: Ich bin Folke Ich freue mich auch, dass ich hier dran teilnehmen darf.
Clemens Trachternach: Ja, ich bin der Clemens, freu mich auch dabei zu sein und willkommen hier in Dortmund.
Antonie Bauer: Starten wir direkt mal mit der ersten Frage. Die Westfalen Hütte hat ja eine sehr bewegte Geschichte. Was bewegt Euch denn persönlich heute, wenn Ihr auf diese neue Anlage schaut?
Clemens Trachternach: Für mich als Teamleiter macht es einen Stolz hier so eine große Investition oder eigentlich die größte Investition von thyssenkrupp seit 20 Jahren hier am Standort Dortmund begleiten zu dürfen und bauen zu dürfen.
Das ist nichts, was man öfter erlebt, sondern das macht einmal in seinem Leben im Regelfall, so eine riesen Anlage zu bauen. Und das ist schon ein anstrengender Job, aber ein sehr schöner Job muss man ganz ehrlich sagen.
Folke Redam: Ja, mir macht das auch viel Freude, dass ich hier den Aufbau mit erleben konnte und demnächst die Qualität mit begleite und verantworte.
Volker Smukala: Ja, Ich finds ganz spannend, der Standort Dortmund mit seiner Forschungsabteilung, hier auch für die Oberflächenentwicklung und dann auch mit den drei großen Oberflächenveredelungsanlagen hier am Standort, also jetzt neu gebaut, die FBA 10, aber auch die etablierte FBA 8 und für die elektrolytische Verzinkung, die EBA 3.
Ein toller Standort hier, um unsere High End-Güten im Prinzip für die Automobilindustrie zu produzieren.
Klaus Janhofer: Die Kompaktheit des Standortes, die Menschen, die hier arbeiten, und die täglichen Herausforderungen, die eben diese Produktionsaggregate mit sich bringen. Und ich denke mal, dass wenn man eine gewisse Leidenschaft entwickelt hat für diese Dinge, dass man einfach gerne hierhinkommt
Antonie Bauer: Wie habt ihr denn die Bauzeit hier in Dortmund erlebt, was gab es da vielleicht auch für Ups & Downs?
Clemens Trachternach: Wir haben im Frühjahr 2019 angefangen, hier mit der Baustelle, mit den ersten Bodenarbeiten und um mal so einen Einblick zu bekommen, was wir denn hier eigentlich jetzt so gebaut haben, mal so: Wir haben hier insgesamt ungefähr 75.000 Tonnen Beton verbaut und ungefähr 17.000 Tonnen Stahl im Maschinenbau und in Stahlbau, also es ist schon eine gewaltige Menge oder auch Kabel, die wir verlegt haben, typischerweise nicht der Durchmesser, den man vielleicht in seinem Haushalt hat, sondern etwas dickere Stromkabel könnten wir also von hier bis zum Gardasee legen, die wir an dieser Anlage verbaut haben. Und eigentlich die größte Herausforderung, muss man ganz ehrlich sagen, War diese Baustelle hier unter auch der Corona-Zeit mit zu absolvieren. Wir haben hier in der Spitze mit 400/500 Personen auf der Baustelle gearbeitet, montiert, gebaut und das ist natürlich schwierig.
Die Corona Pandemie hat totale Störungen allen weltweiten Lieferketten hervorgerufen. Kontaktbeschränkungen, Reisebeschränkungen. Man konnte zu irgendwelchen Werkstattabnahmen nicht fahren, einige Firmen konnten nicht produzieren, konnten das Vormaterial nicht bereitstellen für die Maschinentechnik und auch so eine Inbetriebnahme lebt halt von dem Austausch vor Ort. Und ich sag mal, die Montagemitarbeiter sind klassischerweise nicht Homeoffice fähig, von daher war das schon eine sehr anspruchsvolle Zeit, um das unter dem Gesichtspunkt von Corona hier zu einem Erfolg zu führen. Und es geht dann auch nur, wenn man unter so widrigen Umständen arbeitet, funktioniert das nur durch Engagement.
Das muss man wirklich sagen, also ich bin immer wieder voller Freude, mit wie viel Herzblut meine Mitarbeiter hier auch bei der Sache sind und sich total rein knien und das macht einen echt stolz, wenn man so sieht, was man hier gemeinsam in den letzten drei Jahren so geschaffen hat.
Antonie Bauer: Also wenn jetzt ein paar Mitarbeiter:innen zuhören, das war ein großes Lob, habe ich daraus gehört, vor dem Hintergrund es ist ja auch einfach Wahnsinn, dass das überhaupt dann so jetzt fertig gestellt ist und läuft. Da dürfen sich jetzt alle mal fleißig auf die Schulter klopfen. Gibt es ansonsten noch Anekdoten aus den letzten Jahren, die euch gerade einfallen, die ihr hier vielleicht mal zum Besten bringen könnt?
Volker Smukala: Also für mich, der dann durch Corona im Homeoffice war, war ganz faszinierend, die Anlage im Prinzip erst als Fundament zu sehen, dann kam Corona und danach, jetzt hier die fertige Anlage zu bestaunen in ihrer Größe und Dimension, die man von Fotos gar nicht erfassen kann, die man natürlich während der Corona-Zeit immer wieder bekommen hat, aber jetzt hier das Ganze in Realität zu sehen, ist schon sehr beeindruckend.
Antonie Bauer: Folke, kannst du dich noch so an den erhebendsten Moment erinnern für dich hier auf der Anlage?
Folke Redam: Ja, das war ganz klar der erste Moment oder das erste Mal, als ich gesehen hab, dass die Rollen sich drehen, das Band sich bewegt. Also, da fängt es dann an, richtig spannend zu werden, und dann denkt man schon, wie es weiter geht über den Kaltlauf, dann hinterher zur Warm-Inbetriebnahme und Clemens hat es gerade schon gesagt, Corona war eine lange Zeit. Die Mitarbeiter waren sehr motiviert, sind sehr motiviert und jetzt brennen alle drauf, dass es auch wirklich richtig weitergeht und wir auch zusammen hier mit dem Vertrieb Dr. Smukala in die Approvalphase gehen. Das ist spannend. Darauf freuen uns.
Antonie Bauer: Ja, ich höre da auch raus, dass man sich dann auch auf den Lorbeeren hier nicht ausruht in Dortmund, sondern man ist immer schon mit den nächsten Schritten direkt dabei und schon mit den Gedanken viel weiter. Dann gehen wir doch noch mal kurz in die Vergangenheit.
Klaus Janhofer: Ja, wir befinden uns hier an einem altehrwürdigen Standort, wenn wir in die Geschichte gucken, müssen wir uns 150 Jahre zurück bewegen.
Zu dieser Zeit hat die Familie Hirsch, unter Leitung von Leopold Hirsch, dieses Werk hier gegründet und in den Folgejahren ausgebaut und auch zur damaligen Zeit in eine schlagkräftigen Einheit entwickelt und konnte natürlich die Vorzüge dieser Region hier nutzen. Es gab jede Menge Kohlevorkommen, es gab bereits erste Eisenbahn-Netzwerke und das hat diesen Standort zur damaligen Zeit besonders attraktiv gemacht. Wenn man dann weiter schaut, dann haben wir natürlich auch in der Zeit bis heute einige Rückschläge erlitten. Unter anderem eben der Zweite Weltkrieg, hier hat es verheerende Schäden an dem Standort gegeben und nach Kriegsende war nahezu ein wieder Neuaufbau erforderlich, um dann wieder mit der Produktion starten zu können.
Und im Weiteren haben wir dann eben zwei wichtige Fusionen hinter uns hier an diesem Standort, dass ist einmal in den neunziger Jahren, Anfang der 90er die Fusion mit Krupp und dann die Fusion, die dann mit Thyssen vollzogen ist 1997, die dem Standort hier seine Ausrichtung gegeben hat, nämlich, dass wir ein Kompetenzcenter sind für Automobilproduktion, aber auch eben innovative Entwicklungsprodukte zu haben.
Einmal die Produktionsseite, aber eben auch mit dem damaligen Dortmunder Oberflächen Center, heute in dem Bereich kompetenter Ansprechpartner.
Antonie Bauer: Ja, jetzt haben wir gerade ganz viel über den Aufbau gehört, einen kleinen Ausflug in die Vergangenheit gemacht. Schauen wir jetzt in die Zukunft und sprechen über die neue Feuerbeschichtungsanlage 10, kurz FBA 10.
Was heißt eigentlich Feuerbeschichten, eine Schicht Feuer auf dem Blech? Wo kommen denn die Coils her?
Clemens Trachternach: Also zunächst die Coils. Wir haben hier in der auf der Westfalen Hütte nur noch die sogenannte Kaltbandstufe und die Veredelungsanlagen, also wir bekommen unser Warmband primär aus Duisburg und walzen das dann hier kalt und veredeln das dann auf unseren Beschichtungsanlagen.
Da gibt es zwei klassische Routen. Es gibt die Route der elektrolytischen Beschichtungsanlage, wovon wir auch eine Anlage hier in Dortmund betreiben, und dann gibt es die Route der Feuerbeschichtungsanlage. Im Englischen heißt es schön „hot dip galvanizing“ sind also, man kann es auch übersetzen mit Schmelztauchveredeln und das trifft es eigentlich ganz gut.
Also, wir fahren hier das Band durch ein Bad aus flüssigem Zink, dass dann so bei 450, 460 Grad Celsius ist. Eine schöne, angenehme Temperatur, macht im Sommer die Arbeit auch nicht leichter. Und ziehen das Band also durch dieses Bad von flüssigem Zink und blasen dann überschüssiges Zink mit einem sogenannten Luftmesser ab, ähnlich wie so ein Eingangsbereich von einer Kaufhausschleuse, wo man einmal abgedüst wird, wie ein Luftvorhang und damit können wir dann die Zinkschicht auf die genaue, definierte, gleichmäßige Schichtdicke auftragen, die die Kunden von uns wünschen.
Volker Smukala: Und dieses Zink ist ein ganz wertvolles Element. Dann später auch in der Automobilindustrie, wo es dafür sorgt, dass unsere Autos schlicht und ergreifend nicht wegrosten. So wie man es früher kannte, vor dem TÜV noch schnell am Schweller schweißen, das ist ja seit Jahren vorbei, und dank des Zinks, dank dieses kathodischen Korrosionsschutzes, der aufgebracht wird, wo sich dann das Zink im Prinzip für den Stahl aufopfert, wenn es brenzlig wird und die Karosserie in ihrem Glanz und in ihrer Festigkeit weiter dastehen kann.
Antonie Bauer: Jetzt haben wir beide Schritte einmal gehört oder beide Version, wie die Produktion aussehen kann. Was passiert denn da vor?
Folke Redam: Wenn ich jetzt einen Schritt vor den Zinkpott gehe, da ist ein imposanter Ofen. Und dieser Ofen der dient dazu, die mechanischen Eigenschaften mit voreinzustellen und die Oberfläche auch auf die Verzinkung vorzubereiten.
Das ist ein wesentlicher Unterschied im Vergleich zu der elektrolytischen Verzinkung, das hatte Clemens gerade erwähnt, dass es diese beiden Prozesse gibt. Und dort werden die mechanischen Eigenschaften vor der Verzinkung eingestellt und hier kommt erst der Ofen vor dem Zinkpott und hinterher wird die Feinadjustierung dann noch im Dressiergerüst vorgenommen.
Antonie Bauer: Jetzt haben wir ja schon viel über die Anlage gehört. Wie sieht es denn in punkto Nachbehandlung aus?
Clemens Trachternach: Ja ganz hinten nach dem Dressiergerüst, also wenn die Oberfläche final mechanisch eingestellt wird und Rauheit und Welligkeit, da kommen noch zwei Aggregate einen ein so genannter Chemcoater, wo man also sehr präzise Nachbehandlung auftragen kann, als Beispiel hier so ein Anti-Fingerprint, um die Bleche grundlegend zu schützen vor Verschmutzung und auch die Ölmaschine, wo elektrostatisch auch sehr definiert ein Ölfilm aufgebracht wird, der wird zum einen gebraucht, um einfach einen Schutz der der Oberfläche im Coil selber beim Transport zu Gewährleisten und da auch vor Feuchtigkeit letztendlich zu schützen.
Aber auch Preloops sind auch neueste Generation, sie nennen sich Preloops der zweiten Generation, das sind Umformhilfsmittel so, dass der Kunde am Ende gar kein zusätzliches Öl mehr vor seiner Presse applizieren muss, sondern kann das Blech einfach wie es vom Coil kommt in seine Presse einlegen und die Bauteile herstellen.
Antonie Bauer: Das All inclusive-Produkt quasi
Clemens Trachternach: Genau
Volker Smukala: Wir haben also hier eine Anlage, die dann direkt mehrere Produktionsschritte in einem vereint, also das, was man auf der klassischen elektrolytischen Linie dann in mehrere Anlagen aufteilt. was auch alles wieder Zeit kostet, was Geld kostet, was auch die Liefertermine beim Kunden negativ beeinflussen kann. Das haben wir hier komprimiert in einer Anlage, und das ist jetzt keine wahnsinnig neue Technologie, die gibt es schon seit 20 Jahren, aber sie setzt sich immer mehr durch und kann inzwischen auch die höchste Qualität erzeugen, die unsere Kunden am Markt haben wollen, so dass sich diese Feuerbeschichtungstechnologie in den letzten 10, 20 Jahren immer mehr durchgesetzt hat und immer mehr an Bedeutung gewonnen hat im Vergleich zu der konventionellen Elektrolytischen Beschichtungstechnologie
Clemens Trachternach: Als das Thema aufkam, erinnern wir uns alle noch, ich in meinen Kindertagen, wie dann von der voll verzinkten Karosserie auf einmal die Rede war und Korrosionsschutz von mehreren Jahrzehnten als Werbeargument auch genutzt wurde.
Antonie Bauer: Was macht denn die neueste Anlage auf dem Gelände hier so besonders? Warum braucht es überhaupt eine weitere Feuerbeschichtungsanlage direkt neben der FBA 8?
Folke Redam: Die Anlage ist eine sehr gute Ergänzung zu unserem bestehenden Produktportfolio, das heißt, wir sind hier in der Lage, im Gegensatz zu der Zwillingsanlage ein etwas breiteres Spektrum abzudecken und können damit den Kundenbedarf in diesem Segment zukünftig begleiten.
Und ganz konkret kann Volker auch, kannst du sagen, woher diese Anforderung vom Kunden da kommen?
Volker Smukala: Also die breiten Anforderungen, Folke, Die sind technisch bedingt. Wir sehen den Wandel zur Elektromobilität, wir sehen aber auch den Wandel zu größeren Fahrzeugen. SUVs sind sehr stark gefragt am Markt, und dadurch ergeben sich auch einfach große Bauteildimensionen an diesen Fahrzeugen, zum Beispiel die Seitenwand, als sehr breites Teil.
Dann aber auch für die wirtschaftliche Fertigung.
Doppelteil-Fertigung, Türen in in doppelter Breite, Kotflügel, Radhäuser. Dafür braucht man halt die die Dimension, die FBA 10 hier dann auch wunderbar unterstützt mit ihren 1.850 Millimeter Breite. Hinzu kommen aber auch Aspekte wie der Fußgängerschutz, zum Beispiel ein Kotflügel, ist ein ziemlich hartes Element am Auto und um beim Fußgängeraufprall den Kopfaufprall zu dämpfen sind einfach die Motorhauben entsprechend breit, um hier den Kopf besser abfangen zu können und nicht irgendwie auf harte Elemente des Fahrzeugs aufschlagen zu lassen.
Ja, und gerade die automobile Außenhaut, aber auch Industriebauteile, wie die weiße Ware, eine Waschmaschine, eine Spülmaschine haben alle sehr hohe Anforderungen an die Qualität der Oberfläche. Die soll natürlich frei von Kratzern, frei von Pickeln sein, das ist mal so die Grundvoraussetzung, um ein attraktives Bauteil herstellen zu können, und hinzu kommt ein im Prinzip unsere Premium Außenhautqualität, PrimeTex, mit der wir es zu dem schaffen, dass die Lackwelligkeit möglichst glatt ist, also dass wir Orangenhaut im Prinzip vermeiden und hier die Bauteile noch mehr strahlen lassen.
Antonie Bauer: Die Investition ist also ein weiterer wichtiger Schritt Richtung Zukunft des Unternehmens?
Klaus Janhofer: Die FBA 10 ist für uns hier am Standort eine wichtige Ergänzung in unserem Produktionsportfolio, weil, wie schon vorhin mal angedeutet, wir eben dadurch größere Bandbreiten in einer sehr hohen Qualität in den sogenannten Premiumprodukten eben darstellen können und natürlich ist auch wichtig für unser Gesamtkonzept der Strategie Steel Europe, denn ohne die anderen in dem Verbund, können wir die Dinge, die wir hier vor uns haben, auch nicht bewältigen. Und wir haben natürlich mit den anderen Standorten ein Netzwerk, das uns in die Lage versetzt, ein sicherer Partner eben für unsere Kunden zu sein, wenn es um Qualitätsprobleme, wenn es um Fertigungsthemen geht und das steht dann hier weiter auch im Fokus.
Clemens Trachternach: Warum machen wir das dann gerade in Dortmund?
Dortmund ist halt der Außenhautstandort von thyssenkrupp, also wir haben mit der FBA 8 die bis jetzt noch modernste Feuerbeschichtungsanlage in unserem Konzern, wir haben mit der EBA 3 die beste elektrolytische Beschichtungsanlage bei uns im Konzern und die FBA 10 schließt also diesen Kreis und dieses Dreieck fügt sich hier genau in die Strategie von thyssenkrupp ein. Dortmund als Oberflächenstandort, wo wir auch noch eine Menge Forschungsstellen haben in unserem Oberflächenzentrum passt das halt hier wirklich gut rein.
Antonie Bauer: Über welche Produktionskapazitäten sprechen wir hier, die jährlich dazu kommen durch die neue Anlage?
Folke Redam: Wenn wir die Kapazität mal umrechnen in Fahrzeugen, da müssen wir uns vorstellen, dass wir zusätzlich 600.000 Fahrzeuge mehr mit dem feuerbeschichteten Stahl produzieren könnten.
Antonie Bauer: Das ist ganz schön viel!
Folke Redam: Das ist eine Menge.
Volker Smukala: Ja und 600.000 Tonnen, das sind ungefähr 24.000 Coils. Da sieht man dann auch, was hier an Logistik geleistet werden muss an so einem Standort.
Clemens Trachternach: Ein weiterer Punkt ist halt, der Volker hats gerade gesagt, die Autos werden immer breiter. Wir haben momentan eine Anlage im thyssenkrupp Konzern, die Zink-Magnesium in Außenhautqualität fertigen kann. Das ist hier die FBA 8, die kann aber den breiter werdenden Güten nicht immer Rechnung tragen und breiter werdenden Autos Rechnung tragen.
Da setzt auch die FBA 10 mit ein. Also wir können zwei verschiedene Produkte fahren, wir haben zwei Zinkpötte, zwei Schmelzpötte, in denen wir verschiedene Legierung fahren, das eine ist die klassische Zinklegierung, das zweite ist ein so genannter Zink-Magnesium Topf, da ist also ein bisschen Magnesium mit in dem Zinkbad drin.
Und das ist auch ganz wichtig zum Thema Nachhaltigkeit, denn Zink ist natürlich als Rohstoff sehr teuer, ist aber notwendig, um den Korrosionsschutz gewährleisten zu können und Zink-Magnesium ist noch besser in Hinblick auf Korrosionsschutz, das heißt, man kann eine dünnere Beschichtungsstärke aufbringen, spart somit Ressourcen.
Und hat einen gleich guten Korrosionsschutz. Das ist also wirklich ein Vorteil für den Automobilhersteller, der eine dünnere Auflage bekommt, weil es dann auch wieder beim Schweißen von dem Bauteilen Probleme machen kann, ist aber auch tatsächlich ein Umweltaspekt, indem man weniger von dem ja doch recht teuren Rohstoff, Zink oder auch Magnesium dann verbraucht, um einen gewissen Korrosionsschutz am Fahrzeug herzustellen.
Antonie Bauer: Wir hatten das ja auch gerade schon mal angerissen. Für welche Baugruppen und Bauteile im Auto werden die verzinkten Bleche denn genau gefertigt?
Volker Smukala: Im Prinzip sind die meisten Bauteile am Auto mittlerweile verzinkt, vor allem die, die mit Feuchtigkeit potenziell in Kontakt kommen. Das heißt am gesamten Unterboden, Längsträger, wo vorne das Fahrwerk dran sitzt und der Motor drauf hängt, also der klassische Verbrennungsmotor.
Aber natürlich auch die die gesamte Außenhaut, die ja der der Witterung und dem Salz, was im Winter auf unseren Straßen ist, komplett ausgesetzt ist dafür brauchen wir das verzinkte Blech und die Anwendungen haben wir gerade schon genannt, also die Fahrzeuge, die immer größer werden, das müssen wir gar nicht mehr wiederholen.
Antonie Bauer: Genau, und da gibt es ja auch, glaube ich, auch noch viel Wachstum im Bereich der Elektromobilität, das heißt die Autos sind genauso davon betroffen wie unsere herkömmlichen Verbrenner und da gibt es ja auch eine gewisse Konzentration.
Volker Smukala: Auf jeden Fall, die brauchen den gleichen Crashschutz, um im Falle eines Aufpralls die Insassen zu schützen. Die brauchen die gleiche Außenhaut, um vor den Wettereinflüssen zu schützen, aber natürlich auch, um das Design des Fahrzeugs zu realisieren. Hinzu kommt natürlich der Leichtbauaspekt von Fahrzeugen. Dafür kann die FBA10 sehr breites Gütenspektrum in vielen Festigkeitsklassen abdecken, unterstützt so auch, dass wir die Bleche dünner machen können bei gleicher Bauteilperformance am Ende und somit leichter, was natürlich auch ein wichtiger Umweltaspekt ist.
Antonie Bauer: Bleiben wir dann vielleicht auch noch ein bisschen bei dem Punkt Nachhaltigkeit. Zahlt die Investition denn auch auf die Nachhaltigkeit von Prozessen und Anlagentechnik ein?
Folke Redam: Der Schwerpunkt der liegt hier im Bereich der Ofentechnik. Du hattest vorhin auch gefragt „was hat dich denn so berührt?“ Es waren die treibenden Rollen, aber es war auch dieser Ofen, also wenn man davor steht und man kennt andere Anlagen, der ist noch mal eine Ecke höher, ich weiß nicht, ob ich es richtig in Erinnerung habe sind es 63 Meter oder liege ich da falsch, Clemens?
Clemens Trachternach: Der Verzinkungsturm ist bei bei ungefähr 63 Meter, der Ofen selbst ist ja so bei 38 Meter.
Folke Redam: Also es ist absolut imposant, diese Anlage und du hattest nach Nachhaltigkeit gefragt. Es kommen in dem Ofen regenerative Strahlrohrbrenner zum Einsatz, das heißt, die Abwärme wird für die Vorerwärmung genutzt.
Clemens Trachternach: Es ist die beste am Markt verfügbare Technologie, die wir einbauen, um wirklich die Anlage zukunftssicher zu gestalten und auch in vielen, vielen Jahren immer noch die Emissionsgrenzwerte sicher zu unterschreiten.
Antonie Bauer: Der Standort Westfalenhütte in Dortmund hat sich im Laufe seiner Geschichte also zum Produktions- und Entwicklungsstandort für die Automobilindustrie entwickelt. Welche Anlagen finden wir neben der FBA 10 denn noch so hier?
Klaus Janhofer: Ja, wir starten hier am Standort Dortmund mit dem sogenannten Beiz-Walz-Prozess, und wir bekommen dazu Warmband aus Duisburg eingeliefert, was wir dann hier, über diese erste Prozesskette weiterverarbeiten über die Beiz-Kalt-Walzstraße, werden dann hier am Standort zwei Oberflächen Veredelungsaggregate, heute versorgt, das ist die FBA 8 und EBA 3. Und zukünftig, wenn man natürlich auch schwerpunktmäßig über die Beta Anlage die FBA 10 mit versorgen. Daneben haben wir natürlich um die ganzen internen Prozesse abzuwickeln, auch ein größeres Team, was sich mit Logistik und Adjustage Tätigkeiten beschäftigt. Und so wird das abgerundet dann später mal das Produktionsdreieck hier am Standort Dortmund sein.
Volker Smukala: Und es ist auch optisch ganz schön zu sehen, dass die neue FBA 10 genau zwischen der FBA 8 und der EBA 3 steht, also die wird von ihren etablierten Schwesteranlagen quasi in die Mitte genommen.
Antonie Bauer: Jetzt wird die Anlage in Betrieb genommen, wie viele Menschen arbeiten hier? Sind neue Arbeitsplätze geschaffen worden?
Clemens Trachternach: Wir haben wir von thyssenkrupp aus knapp 100 Arbeitsplätze geschaffen, davon ungefähr 80, die direkt an der Anlage beschäftigt sind. Entweder also wirklich auf der Wechselschicht. Wir haben 12 Mitarbeiter auf der Wechselschicht, die für die eigentliche Produktion zuständig sind, inklusive einer kleinen integrierten Instandhaltung, die anderen dann, ich sag mal in der Tagschicht, die die Produktion, die Qualität, die Instandhaltung verantworten und ein paar wenige Funktionen in den Support, in irgendwelchen Supportbereichen. 12 Mann, 12 Personen pro Wechselschicht ist nicht sehr viel für eine so große Anlage.
Wir haben eine ziemlich vollautomatisierte Anlage an vielen Stellen, wo wenig manuelle Handgriffe gemacht werden müssen im normalen Produktionsprozess, und das stellt natürlich dann auch Ansprüche an die jeweiligen Mitarbeiter, denn ich sag mal der doch relativ komplizierte Produktionsprozess muss dann kontrolliert werden, es muss eingegriffen werden, also wirklich eine hohe Verantwortung, die hier auch auf den Mitarbeitern lastet, um diesen Prozess dann zu begleiten. Aber wir haben die richtige Wahl getroffen, wir haben super Leute, dass kriegen wir schon gemeinsam hin!
Antonie Bauer: Vielen Dank an euch alle für dieses interessante Interview, ich fasse die wichtigsten Fakten noch einmal zusammen.
Erstens: Am Standort Dortmund entsteht eine neue hochmoderne Feuerbeschichtungsanlage.
Zweitens: Kapazitäten für feuerverzinkte Produkte in bester Oberflächenqualität werden ausgebaut, das Gütenspektrum wird abgedeckt auf nahezu alle Festigkeitsklassen und breitere Abmessungen.
Drittens: Mit der Investition werden rund 100 neue Arbeitsplätze geschaffen und der Standort Westfalenhütte als der Produktions- und Entwicklungsstandort für die Automobilindustrie gestärkt.
Viertens: Die FBA 10 ist eine Investition in die Zukunft im Rahmen der Strategie 2030 von thyssenkrupp Steel.
So, das wars für heute. Danke fürs Zuhören, ich hoffe es hat euch gefallen. Und falls ja, abonniert: „gekocht, gewalzt, veredelt“ gern auf Apple Music, Spotify oder einer anderen Podcastplattform und lasst uns auch gerne Feedback da. Zum Beispiel via Mail an: [email protected]
Ich freue mich auf weitere spannende Stahlthemen mit euch. Bis dann!
Folge 6: Auf Klima-Mission – Marie Jaroni über den Weg zum grünen Stahl
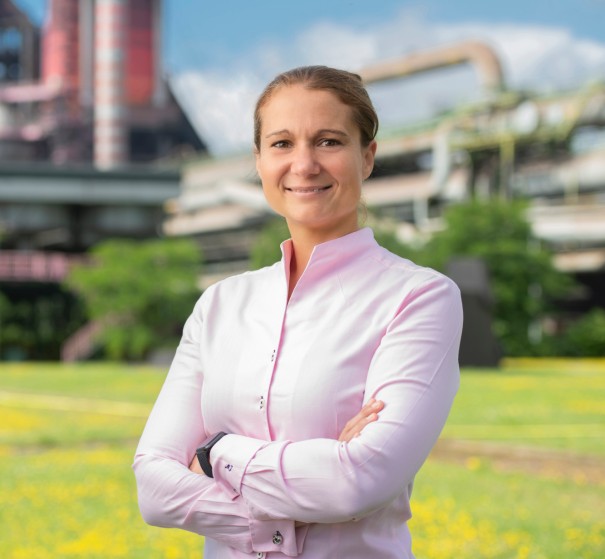
Dr. Marie Jaroni hat den coolsten Industriejob Deutschlands. Als „Head Of Decarbonization & Sustainability” ist sie mitverantwortlich für die Transformation der Stahlherstellung bei thyssenkrupp Steel. Die Umstellung auf klimaneutrale Stahlerzeugung ist eine unglaublich große, aber auch spannende Herausforderung, die sorgfältige Planung und Weitsicht verlangt.
In Folge 6 unseres Podcasts erzählt Marie Jaroni von ihrem Werdegang, ihrer Strategie und den ersten Schritten Richtung Klimaneutralität.
Antonie Bauer: Anfang des 19. Jahrhunderts gründete Friedrich Krupp in Essen eine Fabrik zur Herstellung von Gussstahl. Der Beginn einer langen, traditionsreichen und bewegten Erfolgsgeschichte, die heute an ihrem wohl größten Wendepunkt steht. Denn die Produktion von Stahl soll bis 2045 klimaneutral werden. Aktuell verursacht die Stahlbranche aber noch 7 % aller CO2 Emissionen in Deutschland, davon 20 Millionen allein bei thyssenkrupp. Bereits 2030 sollen 6 Millionen Tonnen CO2 jährlich eingespart werden. Ein ganz schön ambitioniertes Ziel. Und um dieses Ziel zu erreichen, braucht es einen wirklich guten Plan. Einen Transformationsplan. Und den verfolgt Dr. Marie Jaroni. Sie leitet das „Team Decarbonization and Sustainability“ bei thyssenkrupp Steel und soll den Stahl perspektivisch grün machen. Erste Schritte dorthin ist sie mit ihrem Team bereits gegangen und auch die nächsten Etappen sind schon klar. Sie selbst sagt, sie habe den coolsten Industriejob Deutschlands. Was sie an ihrem Job so fasziniert und wie sie bei der Mammutaufgabe „Transformation der Stahlindustrie“ vorgeht, das erzählt Marie Jaroni uns in dieser Ausgabe von „gekocht, gewalzt, veredelt“, dem Stahl Podcast. Mein Name ist Antonie Bauer und ich freue mich, dass ihr zuhört.
Antonie Bauer: Hallo, Marie, schön, dass wir heute miteinander sprechen können.
Marie Jaroni: Hallo Antonie.
Antonie Bauer: Zu Beginn stelle ich natürlich die drei W-Fragen und beginne mit Frage 1: Wann hast du deine Leidenschaft für den Werkstoff Stahl entdeckt?
Marie Jaroni: Wahrscheinlich erst so richtig im Studium. Da sind wir immer wieder auf Exkursionen gefahren weltweit, und haben uns verschiedene Metallurgiestandorte angeguckt, Stahl, aber auch andere Werkstoffe. Und das hat mich immer fasziniert, so richtig zu sehen, wie entsteht eigentlich aus dem eigentlich dreckigen Stein nachher ein tolles Produkt und der ganze Weg dazwischen, der hat mich fasziniert.
Antonie Bauer: Meine zweite W-Frage für dich: Was fasziniert dich an Stahl so sehr?
Marie Jaroni: Eigentlich genau das. Also, dass aus eigentlich sehr groben Werkstoffen und auch einem Prozess, der grob und martialisch wirkt, nachher so ein feiner Stoff rauskommt, so ein genau eingestelltes Produkt, was man wieder zu vielen anderen Produkten weiterverarbeiten kann.
Antonie Bauer: Und drittens Warum glaubst du an die Zukunftsfähigkeit von Stahl und natürlich besonders an den klimaneutralen Stahl?
Marie Jaroni: Also zum einen gibt es eigentlich keine Alternative dazu, dass wir die Klimakatastrophe aufhalten. Ich glaube, da sind wir uns gesellschaftlich ja auch alle einig. Und wir als thyssenkrupp Stahl müssen auch unseren Beitrag dazu leisten. Und dazu gehört es, unsere ganzen Prozesse umzustellen, sodass nachher kein CO2 mehr entsteht und wir kein CO2 mehr emittieren.
Antonie Bauer: Du sagst selbst, du hättest als „Head of tDecarbonization and Sustainability“ bei thyssenkrupp Steel den coolsten Industrieob Deutschlands. Warum?
Marie Jaroni: Ich glaube, da gibt es verschiedene Begründungen. Das eine ist erst mal ist der Impact, den wir hier bei ThyssenKrupp und damit auch ich in der Verantwortung für diesen ganzen Bereich habe, auf die Emissionen, die in Deutschland rausgehen einfach riesig. Wir bei thyssenkrupp Stahl emittieren 2,5 % aller deutschen CO2 Emissionen. Und dadurch, wenn wir das jetzt gut machen und besser machen, dann sind die nicht mehr in der Luft und helfen einfach, dass wir ein besseres Klima haben. Und dieser Impact ist natürlich total reizvoll und es macht einfach Spaß, wenn man so eine Vision vor Augen hat, wenn man tagtäglich zur Arbeit geht.
Antonie Bauer: Jetzt gehen wir mal zurück ins Jahr 2000, als du mit 16 Jahren am Girls Day bei der RWTH in Aachen teilgenommen hast. Hast du da eventuell schon geahnt, dass du heute in dieser Position arbeiten würdest?
Marie Jaroni: Nein, annähernd nicht. Ich wollte mich mal umschauen und habe gedacht Ah, vielleicht Technik, das interessiert mich. Und Naturwissenschaften finde ich ganz spannend. Ich gucke mir das mal an, bin nach Aachen gefahren, bin da durch Zufall auch eher im Metallurgie-Institut gelandet und es war total faszinierend. Da wurde so ein bisschen Metall aufgeschmolzen und dann wurden da Münzen draus gegossen und das hat irgendwie Spaß gemacht. Ich war vorher mit so einem Bereich auch nie in Berührung gekommen und da habe ich mich dann irgendwann bei der Studienwahl wieder daran erinnert und habe mich in Aachen eingeschrieben und habe Metallurgie studiert.
Antonie Bauer: Aber der Girls Day hat zumindest dein Interesse für Metall im Allgemeinen geweckt, oder?
Marie Jaroni: Ja, genau. Hat es geweckt und überhaupt erst mal eröffnet, dass es so was gibt und dass man so was studieren kann und dass das vielleicht auch spannend sein könnte.
Antonie Bauer: Hast du während deines Metallurgie- und Werkstofftechnik Studiums schon gemerkt, da kommt was auf die Industrie zu, da verändert sich was? Und das dann eventuell schon im Hinterkopf gehabt?
Marie Jaroni: Nee, das war ja Anfang der 2000er. Und ehrlicherweise war das da in der metallverarbeitenden und produzierenden Industrie überhaupt noch kein großes Thema. Also wenn wir allein beachten, was die letzten 2-3 Jahre für Schwung und Dynamik in das Thema gebracht haben, ist ja schon enorm. Und wenn man dann 20 Jahre zurückschaut, muss man sagen, da hat die Welt in dem Sinne noch ein bisschen anders getickt, auch in der Metallurgie.
Antonie Bauer: Dann hast du nach deinem Studium ja erst mal was ganz anderes gemacht und lange bei einer Unternehmensberatung gearbeitet. Wie kam es zu dieser Entscheidung?
Marie Jaroni: Also ich wollte dann erst mal nach dem Studium mich noch mal wieder verbreitern. Das ist ja schon ein sehr spezielles Studium, was, was einen auch erst mal fachlich sozusagen weiterbringt. Und dann habe ich gesagt So, jetzt möchte ich so ein bisschen auch noch über den Tellerrand hinausschauen, über das Metallurgiestudium hinausschauen und mich relativ breit mal umgucken. Und das ging in der Unternehmensberatung einfach gut. Ich konnte verschiedene Industrien noch mal kennenlernen, konnte verschiedene Geografien kennenlernen, ein bisschen durch die Welt reisen und arbeiten. Und ja, das habe ich dann auch gemacht.
Antonie Bauer: Das bedeutet, du warst innerhalb der Unternehmensberatung aber schon für dein eigentliches Metier zuständig.
Marie Jaroni: Auch, aber nicht nur. Ich habe auch ganz andere Bereiche gemacht, immer mit Industrie im Fokus, aber nicht nur Metall.
Antonie Bauer: Inwiefern hilft dir diese Erfahrung bei deinem jetzigen Job?
Marie Jaroni: Ich glaube Komplexität zu handlen auf der einen Seite und neue Situationen bearbeitbar zu machen. Das sind Sachen, die ich aus Unternehmensberatung einfach mitbringe und die mir heute auch viel helfen.
Antonie Bauer: Dann lass uns doch mal über den Auftrag bei thyssenkrupp Steel sprechen. Wie transformiert du die Stahlindustrie zur Klimaneutralität? Was ist deine Strategie?
Marie Jaroni: Also wir als ThyssenKrupp haben ja eine Strategie, die ich dann umsetze. Unsere Strategie ist, dass wir Direktreduktionsanlagen bauen und dadurch unsere Hochöfen ersetzen. Diese Direktreduktionsanlagen nutzen als Reduktionsmittel nicht mehr den Kohlenstoff wie in Hochöfen. Und dadurch kommt auch kein CO2 oben raus, sondern es wird Wasserstoff verwendet und der Wasserstoff reduziert das Eisenoxid und dadurch kommt Wasserdampf raus. Somit ersetzen wir das CO2 durch Wasserdampf.
Antonie Bauer: Ist deine Aufgabe eher vom unternehmensberaterischen Aspekt geprägt oder vom metallurgischen Aspekt?
Marie Jaroni: Ich glaube das Schöne ist, es ist die Mischung aus beidem. Es ist auf der einen Seite diese Komplexität zu handlen und bearbeitbar zu machen und auf der anderen Seite aber auch das metallurgische und technische Wissen im Hintergrund zu haben, um zu verstehen, wie die Abläufe eigentlich dann nachher funktionieren müssen, sodass wir hier nachher auch wirklich technisch klimaneutral werden können, nicht nur auf Powerpoint.
Antonie Bauer: In der Anmoderation habe ich ja schon erwähnt, dass erste Schritte bereits getan sind. Kannst du kurz erklären, welche Schritte schon umgesetzt wurden?
Marie Jaroni: Genau, wir haben ja, bevor wir jetzt die Direktreduktionsanlagen bauen, haben wir erste Versuche an Hochöfen oder an einem Hochofen gemacht und haben Wasserstoff eingeblasen in den Hochofen. Um erst mal zu verstehen, wie funktioniert eigentlich so ein Wasserstoff in der Metallurgie? Wie muss man damit umgehen? Bevor wir dann wirklich unsere Technik komplett umstellen, weg vom Hochofen hin zu Direktreduktionsanlagen.
Antonie Bauer: Und gibt es auch schon Schritte die als nächstes geplant sind? Ist da schon was spruchreif?
Marie Jaroni: Wir geben verschiedene Einsatzstoffe noch in den Hochofen wie Schrott HBI, um auch schon heute in dem heute vorhandenen Anlagenpark auch schon CO2 einzusparen. So weit wir es wenigstens können.
Antonie Bauer: Du hast gerade von HBI gesprochen. Kannst du uns diesen Begriff kurz erklären?
Marie Jaroni: Ja, das ist ein vorreduziertes Eisen. Also einfach ein Eisenträger, den man einsetzen kann, um dann weniger CO2 oben aus dem Hochofen rauslassen zu müssen.
Antonie Bauer: Veränderungsprozesse bedeuten immer auch Überzeugungsarbeit, vor allem im Kollegium. Wie werden deine Pläne seitens der Belegschaft aufgenommen und wie überzeugst oder motivierst du deine Kolleginnen und Kollegen, den Prozess mitzugehen?
Marie Jaroni: Die Zukunftsstrategie von thyssenkrupp Stahl wird sehr positiv aufgenommen und ich glaube, die Breite aller Kolleginnen haben einfach verstanden und gehen den Weg auch mit, dass wir uns verändern müssen, dass wir momentan einfach auch viel CO2 in die Luft geben und dass wir daran was ändern müssen. Und ich glaube, das ist allen klar, die Basis ist dafür gelegt und deswegen ist die Unterstützung sehr groß in der Kollegenschaft auch da was dran zu tun und den Weg nach vorne zu gehen.
Antonie Bauer: Gehst du dann auch aktiv rein in die Kommunikation? Wenn sich zum Beispiel jemand Sorgen macht oder ganze Abteilungen sich fragen „Was wird aus uns“? Ist das dann auch deine Aufgabe, den Leuten diese Sorgen zu nehmen und Entscheidungen zu kommunizieren?
Marie Jaroni: Klar, das machen wir, glaube ich, mit der ganzen Führungsmannschaft von ThyssenKrupp Stahl vom Vorstand natürlich, einfach ich auch aus meiner Rolle heraus. Aber auch meine anderen Kollegen, die einfach ihre Mannschaften dann jeweils immer mitnehmen und einfach auch erklären Was machen wir da? Oft ist es ja auch, dass man einfach verstehen muss, was machen wir eigentlich um dann auch zu sagen Ja, das finde ich gut und da gehe ich mit und da helfe ich mit, dass wird ziemlich breit von allen Kollegen auch gemacht.
Antonie Bauer: Lass uns mal über eine Zahl sprechen, die ja irgendwie abstrakt im Raum steht. 6 Millionen Tonnen CO2 sollen bis 2030 jährlich eingespart werden. Kannst du uns mal diese Menge veranschaulichen? Wie viel ist das überhaupt?
Marie Jaroni: Das ist knapp 1 % wenn man es runter rechnet. Nicht ganz, aber fast 1 % der gesamten deutschen Emissionen, die von aller Industrie, von allen Haushalten, von allen zusammen in Deutschland gemacht wird. 1/100 davon können wir jetzt bis 2030 hier einsparen. Und dann können wir immer noch mehr.
Antonie Bauer: ThyssenKrupp Steel will mit Wasserstoff arbeiten. Kannst du erklären, wo dieser Wasserstoff herkommt?
Marie Jaroni: Es gibt verschiedene Ansätze und auch verschiedene Partner, mit denen wir sprechen. Es gibt eigentlich im Grunde drei große Versorgungslinien, würde ich es mal sagen. Das eine ist rundherum. Nearside nennen wir das, rund um unser Werk, wo wir mit kleinen Pipelines, also mit kurzen Pipelines, angeschlossen werden könnten und den Wasserstoff zu uns bringen. Dann gibt es Projekte, die an der europäischen Küste im Norden beispielsweise Niederlande, Deutschland und so weiter liegen, die dann auch durch Pipelines zu unserem Werk angeschlossen werden könnten. Und dann gibt es eine dritte Kategorie. Da kann der Wasserstoff auch weltweit aus verschiedenen Ländern, dann aber per Schiff oder mit sehr langen Leitungen bis zu uns gebracht werden. Also eigentlich drei Kategorien, über die der Wasserstoff zu uns gelangt.
Antonie Bauer: Auch andere Industrien werden zukünftig große Mengen benötigen. Wie kann ThyssenKrupp den eigenen Bedarf sichern? Gibt es da eventuell schon Verträge?
Marie Jaroni: Also wir sind mit verschiedenen Partnern, haben wir auch MOUs und haben sozusagen Vorverträge abgeschlossen. Aber es gibt keine festen Verträge. Aber wir sind dabei, das weiter voranzubringen.
Antonie Bauer: Das klingt alles nach einer riesengroßen Herausforderung, die da auf dich und dein Team zukommt. Bist du dennoch von der Zukunftsfähigkeit von Stahl und seiner klimaneutralen Produktion überzeugt?
Marie Jaroni: Selbstverständlich. Klar, thyssenkrupp Stahl hat eine super klimaneutrale Zukunft und davon bin ich überzeugt. Und dafür gehe ich jeden Tag gern zur Arbeit.
Antonie Bauer: Bevor wir zum Ende kommen, hast du deinen Lieblingsort bei thyssenkrupp Steel? Und wenn ja, warum ist dieser Ort so wichtig für dich?
Marie Jaroni: Ich habe während meines Studiums mal ein Praktikum bei ThyssenKrupp gemacht und das habe ich im Stahlwerk 2, im Ox2 in Beeckerwerth gemacht. Und damals habe ich einfach ein halbes Jahr mit den Ingenieuren gearbeitet, konnte in alle Ecken des Stahlwerks mal reinschauen. Und wenn ich dann heute Besucher durch das Ox2 führe, dann stehe ich da immer gerne, schaue mir an, wie die Konverter befüllt und nachher entleert werden und sehe gern die Hüttenflöhe, das sind so kleine Funken am Boden, wie die dann da her strahlen. Und das macht einfach Spaß. Das freut mich immer wieder.
Antonie Bauer: Hast du zum Schluss noch einen Tipp für interessierte junge Menschen, die sich jetzt diesen Podcast anhören und denken „Wow, das klingt so spannend, das möchte ich auch gern machen“. Welchen Rat kannst du ihnen mitgeben?
Marie Jaroni: Guckt euch das vielleicht mal, ich habe vorhin vom Girls Day gesprochen, guckt euch so was mal an, wenn ihr die Chance habt bevor ihr anfangen zu studieren. Geht man zu einem Girls Day, wenn ihr Mädchen seid oder nehmt so Möglichkeiten bei Unis wahr und guckts euch vorher an. Vielleicht geht ja auch mal irgendwo hin, wo ihr gar nicht vorher denkt Oh, das ist was für mich, sondern einfach mal was ganz Verrücktes. Und vielleicht findet ihr dann das, was euch Spaß macht, wofür ihr Leidenschaft entwickelt und dann einfach machen.
Antonie Bauer: Liebe Marie, vielen, vielen Dank für dieses interessante Interview und ich wünsche dir für Deine spannende Aufgabe natürlich alles Gute.
Bevor wir zum Ende dieser Episode von gekocht, gewalzt, veredelt kommen, möchte ich euch noch unsere kleine neue Rubrik vorstellen. Den Steel Fact. Ab jetzt bekommt ihr zum Schluss jeder Folge immer eine lustige, kuriose oder ungewöhnliche Info rund um das Thema Stahl und ThyssenKrupp. Und unser heutiger Steelfact beginnt mit einer Frage. Was haben Gänse mit Stahl zu tun? Die Antwort geht zurück ins 13. Jahrhundert. Da soll es nämlich einen Schmied namens Wieland gegeben haben, der für seine guten Schwerter bekannt war. Und Wieland war sehr ehrgeizig, wollte noch bessere Produkte herstellen, und so begann er ein bisschen zu experimentieren. Er schmiedete ein Schwert aus dem besten Stück Eisen, das er finden konnte, und als das fertig war, feilte er es in winzige Eisenspäne und mischte die dann seinen hungrigen Gänsen unters Futter. Nachdem die Gänse das Futter verdaut und ausgeschieden hatten, sammelte er den Kot auf und siebte die Eisenspäne wieder raus. Aus diesem Eisen schmiedete er ein neues Schwert, das wesentlich besser und härter war als alle anderen. Soweit die Sage. 1936 wurde dieser Prozess dann aber von einem Forschungslabor in Düsseldorf nachvollzogen und das Ergebnis war das gleiche. Der Stickstoff, der im Gänsekot enthalten ist, hat die Qualität des Stahls verbessert und seinen Härtegrad erhöht. Und anscheinend hat der Schmied Wieland das schon im 13. Jahrhundert erkannt. Heute wird Stickstoff immer noch als Legierungselement zur Festigkeitssteigerung eingesetzt, dank einer weit zurückliegenden Innovation.
Das war'ss für dieses Mal. Vielen Dank fürs Zuhören. Ich hoffe, es hat euch gefallen. Falls ja, abonniert „gekocht, gewalzt, veredelt“ gern auf Apple, Spotify oder einer anderen Podcast Plattform. Und lasst uns auch gern Feedback da zum Beispiel via Mail an [email protected] Ich freue mich auf weitere spannende Stahlthemen mit euch. Bis dann.
Folge 5: Ofenreise – Von alten Öfen zum Hochofen 2.0
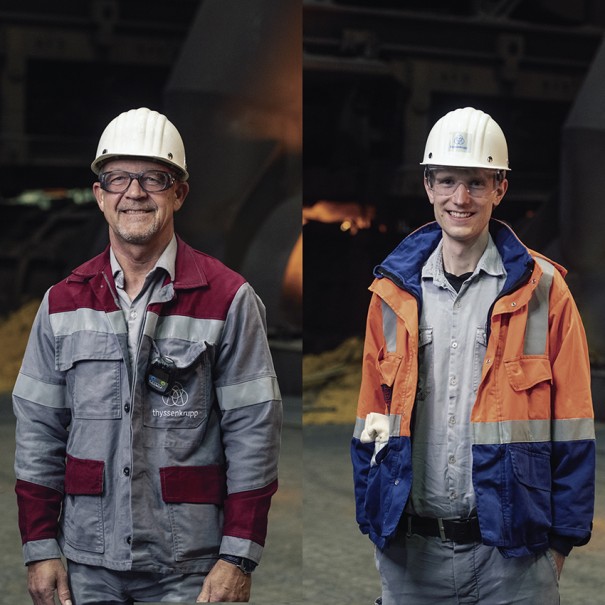
Rund 3,6 Millionen Tonnen Roheisen erschmilzt der Hochofen Schwelgern 1 in Duisburg jährlich. Doch seine Zeit ist quasi "vorbei", seine fünfte Ofenreise endet nach 13 Jahren. Aber was passiert bei einer Ofenreise und was ist das genau? Und wie sieht der Hochofen der Zukunft aus? Denn die klimaneutrale Stahlproduktion schreitet mit schnellen Schritten voran. Dazu spricht unsere Moderatorin Antonie mit Markus Wischermann, Leiter der Operating Unit Hot Metal, und Florian Kremers, der die Transformation in diesem Bereich auf allen Ebenen vorantreibt.
Antonie Bauer: 110 Meter. Mit der Größe wird der Hochofen 1 Schwelgern seinem Namen im wahrsten Sinne des Wortes gerecht. Von dem steh ich gerade und muss meinen Kopf echt in den Nacken legen, um bis nach ganz oben zu schauen. Seit 1973 ist er in Betrieb, also schon ein alter Hase unter den Hochöfen. Er ist einer von insgesamt vier Hochöfen am Standort Duisburg und gehört zu den größeren seiner Art. Und er schmilzt jährlich rund 3,6 Millionen Tonnen Roheisen. Und damit herzlich willkommen bei „gekocht, gewalzt, veredelt“, dem Staat Podcast von thyssenkrupp. Wir reden hier über den Werkstoff Stahl und alles was dazugehört. Mein Name ist Antonie und ich stehe heute vor diesen Riesen, den ich gerade beschrieben habe, weil seine Zeit quasi vorbei ist. Heißt: nach 13 Jahren endet die fünfte Ofenreise des Hochofen 1. Und was so eine Reise überhaupt ist und wie der Hochofen der Zukunft aussieht, darüber spreche ich heute für den Podcast mit Markus Wischermann, Leiter der Operating Unit Hot Metal bei thyssenkrupp Steel, und Florian Kremers, der die Transformation in diesem Bereich auf allen Ebenen vorantreibt. Hallo ihr beiden.
Markus Wischermann: Hallo!
Florian Kremers: Hallo.
Antonie Bauer: Schön, dass ihr heute meine Gesprächspartner seid. Wir wollen euch am Anfang ein bisschen vorstellen, oder ihr macht das viel mehr. Die erste Frage wäre: Was genau machst du als CEO dieser Unit bei thyssenkrupp Steel Europe?
Markus Wischermann: Ich leite hier die Roheisenerzeugung. Das sind die Einheiten der Hochöfen. Wir haben zwei Hochofen-Standorte mit zwei kleineren Hochöfen im Bereich Hamborn und mit den beiden großen Öfen, wo der Ofen 1 auch steht, im Bereich Schwelgern. Dazu gibt es eine sogenannte Sinteranlage, das ist ein Vorprodukt, das wir also aus feinsten Erzen stückiges Erz machen oder stückiges Material machen, was wir in den Hochofen schmeißen. Und dazu gibt es eine Kokerei. Diese Kokerei brauchen wir, um den Koks als Treiber, als Reduktionsmittel, in dem Ofen für den chemischen Prozess einzubringen. Und für die Wärme.
Antonie Bauer: Und da sorgst du dafür, dass alles läuft.
Markus Wischermann: Alleine kann ich das nicht. Aber es gibt genug Leute, die mich da unterstützen. Aber wir sind da, ich sage mal, insgesamt mit vier großen Standorten unterwegs.
Antonie Bauer: Ja, das ist doch die perfekte Überleitung zu dir, Florian. Inwieweit unterstützt du denn den Markus bzw. was machst du?
Florian Kremers: Ja, entsprechend meiner Funktion für die Transformation habe auch ich mich transformiert. Und zwar: in der alten Funktion war ich nämlich tätig bei Markus im Bereich Hot Metal und habe dort als Produktionsingenieur an den Hochöfen, auch am Hochofen Schwelgern 1, gearbeitet. Und jetzt, seit neuestem, bin ich in der Business Unit Decarbonisation und treibe da die Transformation zum Grünstahl voran.
Antonie Bauer: Warum bist du denn heute mein Gesprächspartner?
Florian Kremers: Einerseits wegen dieser Doppelfunktion, die ich ja gerade schon genannt habe: dass ich in der Vergangenheit, also bis vor kurzem, an dem Hochofen Schwelgern, in der Neuzustellung „Schwelgern 1“, beteiligt war. Und auf der anderen Seite, weil ich jetzt in der neuen Funktion die Transformation zum grünen Stahl mit begleiten werde.
Antonie Bauer: Dann auch noch mal an dich [Markus] die Frage, warum du heute mein Gesprächspartner bist.
Markus Wischermann: In so einem Gespräch und in solchen Fragen kann man ja auch schön die herkömmliche, bisher durchgeführte Technik mal kurz erläutern, um dann auch zu zeigen, wohin wir eigentlich diese Technik weiterentwickeln wollen. Das ist eine große Veränderung und das, ich sage mal, das ist eigentlich schön mit der alten Situation anzufangen um dann hinterher zu zeigen: Wo wollen wir eigentlich hin?
Antonie Bauer: Wir haben ja das Glück, dass wir gerade den Abstich beobachten können. Das ist ja der Hammer. Mit wie viel Geschwindigkeit fließt denn jetzt das flüssige Eisen da raus?
Markus Wischermann: Ja, man kann sagen, das Eisen fließt hier so ca. 6 Tonnen, 5 bis 6 Tonnen pro Minute fließt aus Eisen hier raus.
Antonie Bauer: Das ist schon ganz schön schnell.
Markus Wischermann: Und das über knapp zwei Stunden.
Antonie Bauer: Ganz schön viel. Wie viel habt ihr denn so an Tagesproduktion?
Markus Wischermann: Also wir haben eine Gesamtleistung Kapazität von über 30.000 Tonnen pro Tag an Roheisen hier an den Standorten.
Antonie Bauer: Im Hochofen 1 wie viel war es da nochmal?
Markus Wischermann: Hochhofen 1 ist eine Kapazität von 10000 Tonnen pro Tag.
Antonie Bauer: Wow.
Markus Wischermann: Wenn man sagt, dass in einem großen oder mittelgroßen Auto ca. eine Tonne Stahl verbaut ist, dann sind das 10.000 Autos pro Tag ca. Wir könnten innerhalb von einem dreiviertel Tag die gesamte Tonnage des Eifelturms, zum Beispiel, produzieren.
Antonie Bauer: Wow.
Markus Wischermann: Mit siebentausenddreihundert Tonnen, die der Eiffelturm hat, an Stahl. Das schaffen wir locker an einem Tag.
Antonie Bauer: Jeden Tag einen Eiffelturm, warum nicht.
Markus Wischermann: Mindestens.
Antonie Bauer: Wir wollen jetzt mal uns anschauen, was so eine Ofenreise so alles umfasst. Vielleicht magst du, Markus, einmal erklären, was so zu einer Hochofenreise dazugehört.
Markus Wischermann: Bei einer Hochofenreise – also, wenn man einen Ofen, wie jetzt, wieder neu repariert oder zugestellt hat – Hochofen-Sprech – dann hat man das komplette Innenleben des Ofens erneuert oder, in dem Fall, teilerneuert. Innenleben bedeutet, dass sind sogenannte Feuerfeststeine, denn wir haben natürlich im unteren Bereich Temperaturen größerer Größe, das hat 1500 Grad, mit flüssigem Roheisen. Das wir auch jedes Mal regelmäßig entleeren müssen. Und dafür muss natürlich der – nennen wir es mal ganz einfach „Stahleimer“ oder Stahlpanzer nennen wir das – der muss natürlich vor den Temperaturen geschützt werden. Was macht man mit sogenannten Feuerfeststeinen. Das sind extra Steine, die diese großen Temperaturen aushalten können und im Grunde genommen auch den Verschleiß, der sich natürlich im Laufe der Jahre ergibt, weil das Roheisen oder auch das noch nicht flüssige Material an den Ofenwänden, an der Ofenwand, vorbeischrabbt. Dass man das im Grunde genommen mit den Feuerfeststeinen versucht, dann auch abzufangen.
Antonie Bauer: Was ist das denn für ein Gefühl, wenn so eine Ofenreise zu Ende geht?
Markus Wischermann: Erstmal ist es ein spannendes Gefühl, weil natürlich eine Ofenreise nicht abrupt endet, sondern man weiß, wann die Ofenreise endet. Man plant sie ja auch. Man plant auch die danach folgende große Reparatur, die man im Hochofen-Sprech „Zustellung“ nennt. Das ist eine Sache, die man wirklich lange vorher planen muss, meistens ein Jahr lang vorher fängt man schon damit an. Und dann sind natürlich alle immer gespannt. Wenn man den Ofen außer Betrieb nimmt; wenn man das Eisen ablässt, komplett aus dem Ofen; wenn man den Ofen aufmacht; wenn man in dem Ofen inneren nach, ich sage mal immerhin 13 Jahren, jetzt hier reinschauen kann; wie dann so innen alles so ausschaut und wie viel Arbeit man dann natürlich am Anfang erstmal hat, den Ofen innendrin komplett frei zu machen oder, wie wir dazu sagen, auszuräumen.
Antonie Bauer: Und ihr wart live dabei, als es dann soweit war.
Markus Wischermann: Das ist immer wieder ein Erlebnis. Also wenn man das schon, - ich hatte jetzt aufgrund meiner… ich bin ja ein bisschen älter als der Florian - hab das schon ein paar Mal erlebt. Das ist immer wieder ein Erlebnis, wenn man das… wenn man diesen Vorgang eigentlich einleitet, oder er eingeleitet wird. Und wenn man dann sieht, wie das letzte Roheisen quasi aus dem Ofen ausläuft.
Antonie Bauer: Was genau passiert denn, bevor jetzt eine neue Zustellung erfolgt, solange in dem Hochofen? Also was ist die letzten 13 Jahre geschehen an Abläufen?
Florian Kremers: Das, was der Hochofen ja machen soll - also die Ausgangsstoffe, die in den Hochofen zugegeben werden sind ja Eisenoxide, die aus dem Bergbau stammen. Das heißt Eisenoxide FE2O3, viel Siliziumdioxid, Kalziumoxide, Aluminiumoxid und weitere Bestandteile, und wird im Laufe des Prozesses reduziert. Das heißt, das ist ja unser Ziel, Roheisen herzustellen, also reines FE. Und dazu muss der Sauerstoff vom FE2O3 entfernt werden. Das passiert mit Kohlenstoff. Das Ganze ist eine Reaktion, die findet bei hohen Temperaturen statt. Und darüber hinaus wollen wir auch flüssiges Roheisen haben. Das heißt, wir müssen oberhalb der Schmelze Temperatur sein. Das heißt, wir haben einerseits die Verflüssigung des Materials und andererseits die Reduktion. Und das ist das, was 13 Jahre lang in dem Hochofen vonstatten gegangen ist. Das heißt festes Material oben zugegeben, aus dem Bergbau, und unten flüssiges Roheisen abgestochen.
Antonie Bauer: Wie oft kann denn generell so eine Ofenreise stattfinden? Also wie oft kann man einen Hochofen neu zustellen?
Markus Wischermann: Das ist eine gute Frage. Also wenn man sich jetzt mal anguckt, dass der Ofen 1973 gebaut worden ist, als einer der größten Öfen damals hier in Europa - das war ein richtiges Highlight - und jetzt fast 50 Jahre alt ist. Und ich sage mal, wir an der einen oder anderen Stelle zwar immer auch in der Umgebung von dem eigentlichen Ofengefäß auch reparieren - das machen wir natürlich auch schon so seit den letzten zig Jahren - gibt es erstmal keine grundsätzliche Prognose, wann so ein Ofen nicht mehr betreibbar ist. Man muss natürlich ständig auch die einzelne Anlagenteile in Schuss halten. Die Instandhaltung dazu ist regelmäßig, ist geplant, hat auch - bedingt auch - eine Menge Aufwand im Laufe der Zeit und ist wie gesagt immer fortlaufend. Ich würde jetzt keine Prognose wagen wollen, wie lange ein Ofen laufen darf oder laufen kann.
Antonie Bauer: Was umfasst denn so eine Vorbereitung? An was muss man alles denken?
Florian Kremers: Das langwierigste, was eigentlich mal geordert werden muss, ist das Material für die Zustellung. Und im Fokus steht ja das Feuerfest, was erneuert wird. Und da das sehr spezielle und spezifische Produkte sind, die nicht von irgendwelchen x-beliebigen Lieferanten hergestellt werden können, müssen die mit langen Vorlaufzeiten auf dem Weltmarkt geordert werden. Und das ist eigentlich das Hauptaugenmerk, was so eine Planung bedingt. Erst wenn man diese Materialien eingetaktet, für ein gewisses Zeitfenster geordert hat, dann hat man eigentlich auch eine Vorgriffszeit, wann man die Zustellung durchführen kann.
Antonie Bauer: Und wie sieht quasi der Werkzeugkasten aus? Der dürfte auch ein bisschen größer sein in dem Fall. Aber welche Materialien, welche Werkzeuge braucht man für die Zustellung?
Florian Kremers: Das schwierigste ist ja erstmal, dass man den Ofenpanzer durchbohren muss bzw. das Material, das flüssige Material, was noch im Ofen verblieben ist, abführen muss. Dafür braucht man natürlich Bohrmaschinen, die maßangefertigt werden für solche Situationen, die auch geordert werden müssen. Darüber hinaus, wenn das Material, das flüssige Material, aus dem Ofen dann entfernt ist, das über Torpedopfannen abgeführt ist oder die restlichen Materialien am Ende unterm Hochofen aufgefangen werden. Die müssen entfernt werden, die müssen weggebrochen werden. Das heißt, dafür braucht man große Bagger. Dafür braucht man große Kratzer. Und wenn es dann darum geht, den Ofen zu öffnen, also den verbleibenden Koks, der unten im Gestell des Ofens - ist der untere Bereich, wo das flüssige Material immer weiter steht - wenn der auch entfernt werden muss, dann wird eine große Öffnung – wir nennen das „Scheunentor“ - in den Hochofenpanzer geschnitten. Und dafür braucht man Schweißbrenner. Das ist, denke ich mir auch klar. Und wenn dann der Hochofen geöffnet ist, dann braucht man große Bagger und Kretzer, um den flüssigen Koks - den heißen Koks - aus dem Gestell dann rauszuholen. Der wird dann mit Baggern, Caterpillarn, abtransportiert. Und wenn er Hochofen dann leer ist, dann geht es an die eigentliche Zustellung.
Markus Wischermann: Und vielleicht noch als Ergänzung nur um da mal so eine Größenordnung zu haben, so ein sogenanntes Scheunentor, was wir jetzt beim Hochofen aufgemacht haben, das zählt circa vier mal vier Meter.
Antonie Bauer: Du hast dann wahrscheinlich auch schon mal drin gestanden in diesem riesigen Hochofen. Wie war das? Wie hat sich das angefühlt?
Markus Wischermann: Das ist schon gigantisch. Also wenn man in so einem großen Gebäude, in so einem großen Raum steht und dann, wie Florian sagt, 35 Meter nach oben schaut. Ja, und ich sage mal, man kann es nicht beschreiben. Wenn man es mal gesehen hat, wie ich das Glück hatte, dass bei dem Neubau des Ofens 2, 1993, ich da unten mal drin stand - Und da waren noch diese ganzen kühl Elemente, die ja auch seitlich an zig verschiedenen Stellen eingebracht sind, um den Ofenpanzer noch mal zusätzlich zu kühlen, überall so kleine Löcher drin sind - das ist also… wie ein riesen, riesengroßer perforierte Eimer sieht das dann aus. Und man kann sich diese Dimension eigentlich gar nicht so richtig vorstellen. Du bist ja im Grunde genommen da, ich sage mal gerade da in der sogenannten „Gestellebene“, bist du ja bei einem Durchmesser von 14 Metern. Das ist schon gigantisch groß.
Florian Kremers: Ja, es wirkt von innen wie eine Kathedrale. Also es ist wirklich Wahnsinn. Egal, ob man von unten guckt oder von oben guckt. Also das sind Dimensionen und Größenordnungen, die kann man eigentlich gar nicht in Worte fassen. Das ist schon faszinierend.
Antonie Bauer: Ihr habt ja rund um das Thema Hochofen und Roheisenproduktion eine ganz eigene Sprache. Also in der Vorbereitung bin ich über das eine oder andere Wort gestolpert. Was sind denn da eure Lieblingsvokabeln?
Markus Wischermann: Lieblingsvokabeln sind ja in dem Zusammenhang, wenn wir schon über eine Großreparatur spricht, Zustellung spricht, dass ist die „Ofensau“ oder der „Sauabstich“. Das ist einfach das Anbohren des Ofens, in der Regel und zwei oder vielleicht sogar an drei tiefen Stellen, wo man das Restmaterial, Restroheisen, rauslaufen lässt. Das sind natürlich so Begrifflichkeiten, die in der Hochöfener-Welt einfach bekannt sind. Fällt dir [Florian] noch eins ein?
Florian Kremers: Der Fuchs.
Antonie Bauer: Der „Fuchs“ bedeutet dann was genau?
Florian Kremers: Der „Fuchs“ ist einfach nur der Balken, an dem das Roheisen und die Schlacke über die Dichteunterschiede getrennt werden.
Markus Wischermann: Die Schlacke ist ja wesentlich leichter, die schwimmt quasi in dem gesamten Fluss auf dem Roheisen. Und da ist man ja auch ganz pfiffig, mit einem einfachen Verfahren finde ich, dass man im Grunde einen sogenannten „Balken“ in der Ablaufrinne hat, wo ein tieferes Loch ist, wo das Roheisen dann rausgeht. Aber die Schlacke nicht, weil die Schlacke zu leicht ist, die eben oben auf der Oberfläche schwebt. Und die kannst du dann oben, ich sage mal eine Regel seitlich, abführen. Das nennt man „Fuchsbalken“. Joa, das gibt es sonst noch? … „der Ofen hängt“.
Antonie Bauer: „der Ofen hängt“? Was hat es damit auf sich?
Florian Kremers: Der rutscht einfach nicht mehr weiter. Das ist ja eigentlich ein kontinuierlicher Prozess. Das heißt, wir schmelzen unten Material auf, kontinuierlich. Da gibt es eigentlich normalerweise keine Einflüsse, die dazu führen, dass wir nicht mehr aufschmelzen. Das heißt, im Normalfall müsste dementsprechend auch die Möllersäule, die oben drüber steht, kontinuierlich absinken. Wenn „der Ofen hängt“, dann tut sie das nicht mehr. Im Kontext Neuzustellung gibt es noch einen ganz lustigen Begriff und dass ist „der tote Mann“. Also im Hochofen haben wir auch noch den „toten Mann“ - das ist eigentlich genau der Bereich des stehenden Kokses, des Koksgerüstes, der im Normalbetrieb vom Wind nicht durchdrungen wird. Wir geben ja von außen Wind zu um Reduktionsmittel zu bilden. Und der tote Mann ist genau der Bereich im Hochofen, der auch unten im Bereich des Gestells, also der Hochofensau, dann steht, der nicht von dem Wind, bzw. dem Reduktionsgas, durchdrungen wird. Und der „tote Mann“ ist eigentlich genau die Menge an Koks, die wir unten abziehen müssen, wenn wir das Scheunentor geöffnet haben, für die Neuzustellung.
Antonie Bauer: Wir haben jetzt viel vom Hochofen gesprochen, vom alten Hochofen. Heißt auch: es muss einen neuen Hochofen geben. Und dieser Hochofen 2.0 ist die Direktreduktionsanlage. Denn für die klimaneutrale Stahlproduktion ist der Hochofen 2.0 der größte Hebel. Und da steckt unglaublich viel Innovation drin. Und wie genau die Produktion dann in Zukunft abläuft, darüber sprechen wir dann jetzt. Direktreduktion ist immer ein bisschen sperrig als Begriff. Aber dahinter steckt ja echt viel für eine klimaneutrale Stahlproduktion. Was unterscheidet denn den Einschmelzer bzw. die Direktreduktionsanlage vom alten Hochofen?
Florian Kremers: Ziel der Direktreduktion ist ja eigentlich klimaneutral zu werden bzw. Grünstahl herzustellen, welcher am Ende das einbringen oder das Maß an Kohlenstoff bzw. Kohlenstoffdioxid auf das absolute Minimum reduziert, so dass eigentlich die bisherige Hochofenroute, die ja komplett Kohlenstoffbasiert ist, zu einer Wasserstoffbasierten Direktreduktionsroute abgelöst wird.
Antonie Bauer: Vielleicht kannst du bei der Gelegenheit noch mal ganz kurz sagen, warum denn der alte Hochofen so klimafreundlich ist.
Florian Kremers: Das Problem ist ja die Eisenoxide, die einem Hochofen zugegeben werden, also FE2O3 größtenteils, enthalten ja den Sauerstoff, der am Ende vom Eisen entfernt werden muss und Roheisen bzw. Eisen herzustellen, welches dann für die Stahlproduktion herangezogen werden kann. Und dieser Sauerstoff, der wird im alten Verfahren einfach an Kohlenstoff gebunden, das heißt Kohlenstoff plus Sauerstoff ergibt dann am Ende Kohlenstoffdioxid. Und die Menge an Sauerstoff, die abgegeben werden muss, von den Eisenoxiden, bedingt dann automatisch die Menge an Kohlenstoff, die benötigt wird. Zusätzlich kommt dann natürlich noch ein bisschen Heizkohlenstoff dazu für die Temperaturen, über die wir gerade auch schon gesprochen haben. Aber das ist im Grunde genommen einfach der Weg. Das heißt, der Kohlenstoff ist der Energieträger und das Reduktionsmittel, was benötigt wird, um aus Eisenoxiden Eisen bzw. Roheisen zu machen.
Antonie Bauer: Kannst du dann noch mal ganz kleinschrittig vielleicht noch mal erklären, wie denn die Stahlproduktion dann im besten Fall zukünftig abläuft. Also was muss passieren, damit das klimaneutral geschehen kann?
Florian Kremers: Also die Eingangsstoffe, die wir ja aktuell haben in dem Hochofenprozess, werden auch bei der Direktreduktionsroute die gleichen bleiben. Das sind ja weiterhin die Bergbauprodukte, also Eisenoxide, die vielleicht aufbereitet wurden. Und anstelle von Kohlenstoff, der jetzt zur Reduktion herangezogen wird, wird dann einfach Wasserstoff herangezogen. Und Wasserstoff bzw. das Produkt, was aus der Wasserstoffreduktion entsteht, kennen wir ja auch alle: dass ist am Ende Wasserdampf. Das heißt Wasserstoff, der reagiert dann mit dem Sauerstoff von den Eisenoxiden zu Wasserdampf. Und Wasserdampf, ja, ist an der Stelle erst mal kein Problem mehr und führt dann dazu, dass wir den Kohlenstoffeinsatz reduzieren bzw. auf ein Minimum herunterfahren, und haben dann am Ende Grünstahk.
Antonie Bauer: Inwiefern ist denn die Direktreduktion der größte Hebel auf dem Weg zu klimaneutralen Stahl?
Markus Wischermann: Ja gut, wenn man sich vor Augen führt, dass wir hier an diesem Standort, oder tkSE, 2% der CO2 Emissionen im Grunde genommen verursachen, in Deutschland, dann ist das schon ein riesen Hebel. Und ich sag mal, die Hauptmengen kommen eben aus dem Hochofenprozess. Insofern muss man natürlich darum überhaupt einen Schritt in Klimaneutralität gehen. Oder auch in Richtung Grünstahl muss man natürlich da ansetzen, wo die größte Möglichkeit ist. Und das ist am Hochofen.
Florian Kremers: Man muss sich einfach nur vor Augen führen, dass ungefähr für die Produktion von einer Tonne Roheisen über den Kohlenstoff 1,5 Tonnen CO2 emittiert werden. Und das ist schon ein großer Hebel. Wenn man diese 1,5 Tonnen dann drastisch reduzieren kann, über die Wasserstoffreduktion, dann ist das wirklich der Hebel, der dazu führt, dass diese 2% dann gegen Null gehen.
Antonie Bauer: Und dafür gibt es ja sicherlich auch schon einen gewissen Zeithorizont, also vielleicht auch schon ein Startdatum, wann die erste DR-Anlage an den Start gehen soll, wann weitere Anlagen geplant sind. Was könnt ihr mir denn dazu verraten?
Markus Wischermann: Die erste Anlage ist nach unserer Planung 2025 in Betrieb. Und es werden - man muss ja auch dazu sagen, das ist ja ein Ablösen der herkömmlichen Technik in Richtung neuer Technik. Das heißt natürlich, irgendwann wird man natürlich auch die herkömmliche Technik dann nicht mehr benötigen. Und das nennen wir eben halt den Transformationspfad. Dass wir also stückchenweise, schrittweise den Grünstahlprozess langsam hochfahren und gleichzeitig, natürlich ein bisschen zeitversetzt vielleicht, aber ich sage mal vom Prinzip her gegenläufig, dann die herkömmliche Route, dann außer Betrieb nehmen. Das ist das Ziel.
Antonie Bauer: Bei gleichbleibender Qualität, richtig?
Markus Wischermann: Deswegen sind wir ja schlau, ne? Es wird ja schnell mal über Grünstahl gesprochen. Wir erzeugen ja das Vorprodukt für die Stahlerzeugung, das Roheisen. Und die Direktreduktion, die wir hier vorhaben, mit einer sogenannten Einschmelzer, soll eigentlich dazu führen und wird dazu führen, dass wir hinterher aus diesem Prozess Roheisen kriegen, was wir direkt, wie jetzt auch, in den Stahlwerken weiterverarbeiten können. Das ist eigentlich unser Ziel, sodass wir also in der weiteren Route eigentlich nichts anders machen müssen.
Antonie Bauer: Ofenreise. Ein tolles Wort. In der heutigen Podcastfolge haben wir erfahren, was genau das ist und wieso die alten Öfen eben alt sind. Meine Top 2 Erkenntnisse des Tages: Eine Ofenreise ist der Zeitraum von der Abbrandphase bis hin zum Ausklingen der Verbrennung bei einem Hochofen. So eine Reise kann auch schon mal 15 oder über 20 Jahre dauern. In dem Fall heute waren es 13 Jahre. Meine Erkenntnis Nummer 2: Damit in Zukunft Stahl komplett klimaneutral produziert wird, hat thyssenkrupp Steel einiges auf die Beine gestellt. Die Direktreduktionsanlage mit Einschmelzer ist dabei der wichtigste Hebel. Die DR-Anlagen werden mit Gasen betrieben und nutzt man dabei Wasserstoff, arbeiten sie emissionsfrei. Die erste großtechnische DR-Anlage wird thyssenkrupp Steel im Jahr 2025 in Betrieb nehmen. Das war es zu alten und neuen Öfen bei thyssenkrupp Steel und das war es auch mit dieser heutigen Podcastfolge. Also abonniert „gekocht, gewalzt, veredelt“ gerne auf Apple, Spotify oder einer anderen Podcast Plattform. Und lasst uns auch gerne Feedback da. Zum Beispiel per Mail an [email protected]. Ich freue mich auf weitere spannende Stahlthemen in Zukunft und verabschiede mich dann hiermit auch von euch [Markus und Florian]. Vielen Dank, dass ihr heute meine Gesprächspartner wart.
Florian Kremers: Ja, hat uns auch sehr viel Spaß gemacht.
Markus Wischermann: Ja, fand ich auch. War richtig spannend hier in so einem Podcast auch mal zu versuchen, ich sage mal die Dinge möglichst näher oder publikumsnäher mal zu erklären. Das fand ich gut.
Folge 4: Stahl macht mobil – Warum E-Mobilität nur mit Stahl funktioniert
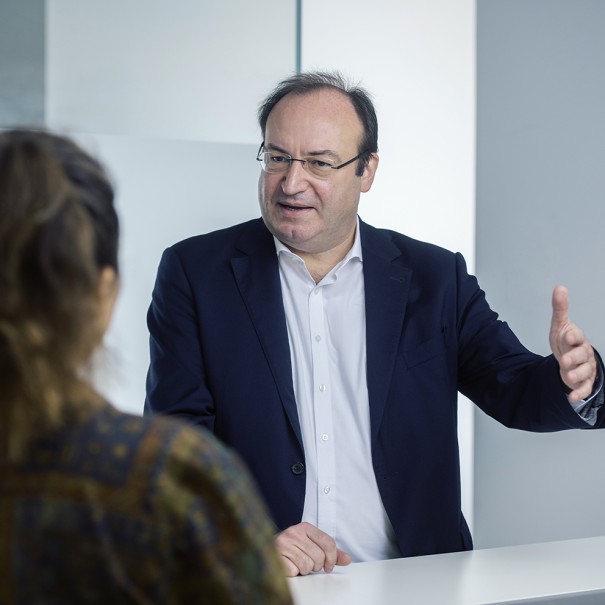
Autos ganz ohne Stahl, das funktioniert nicht. Das wäre wie das Ruhrgebiet ohne die Hütte oder der Schmelzer ohne seinen Silbermantel – nicht nur unvorstellbar, sondern einfach nicht möglich. In unserer 4. Podcast-Folge spricht Moderatorin Toni daher mit André Matusczyk, Direktor des Verkaufsbereichs Automotive. Die beiden diskutieren Fragen wie: Wo kommt der Strom für E-Autos her? Wie kommt er zum Auto? Und was hat Stahl damit zu tun? Das und mehr erfahrt ihr in dieser Podcast-Folge!
Antonie Bauer: Stahl ist heute der erfolgreichste Leichtbauwerkstoff in der Automobilindustrie. Neun von zehn Fahrzeugen in Europa werden in einer stahl-dominierten Leichtbauweise gefertigt. Nur rund zehn Prozent in einer echten Mischbauweise oder als reiner Aluminium-Leichtbau. Aber die Zukunft fährt elektrisch. Was bedeutet das für die Rolle von Stahl im Auto? Ist Stahl hier ausreichend zukunftsfähig? Und wie steht es angesichts schwerer Batterien um den Leichtbau? Eins ist sicher: Autos ganz ohne Stahl, das funktioniert nicht. Das wäre wie das Ruhrgebiet ohne die Hütte oder der Schmelzer ohne seinen Silbermantel – nicht nur unvorstellbar, sondern einfach nicht möglich. Wie wir noch hören werden. Aber das Auto verändert, es entwickelt sich, eigentlich von Beginn an: Elektromobilität ist ein großes und wichtiges Thema. Die Tage des Verbrennungsmotors sind zweifelsfrei gezählt. Und was ist mit Stahl? Klar, der ist auch dabei. Denn Stahl und Elektromobilität, das ist echtes Teamwork. Stellt sich die Frage: Wie verändert Elektromobilität die Art, wie wir Autos bauen und nicht zuletzt unser Leben?
Willkommen zur vierten Folge unseres Podcasts „Gekocht, Gewalzt, Veredelt – der Stahl-Podcast“, in dem wir uns mit dem Werkstoff Stahl auseinandersetzen und mit allem, was dazugehört. Mein Name ist Antonie und ich darf euch durch die Folge führen. In dieser Folge zeigen wir euch, wie wichtig Stahl für die Elektromobilität ist. Wir sprechen darüber, wo Stahl im Elektroauto verbaut wird und welche zentrale und wichtige Rolle er für den Schutz von Fahrer, Beifahrer und Co. im Falle eines Unfalls oder Feuers spielt. Und wir reden über Strom, den Treibstoff für Elektrofahrzeuge. Wo kommt er her? Wie kommt er zum Auto? Und was hat Stahl damit zu tun? Ich finde ja, wir können uns schon als Zeugen der Zeit beschreiben. Überlegt mal, das Auto hat sich in den letzten Jahrzehnten doch total verändert. Der Stahl-Leichtbau hat entscheidend dazu beigetragen, dass die Gewichtsspirale erfolgreich durchbrochen werden konnte. Heute sind Autos viel sicherer, komfortabler und auch größer als früher, aber selten schwerer als ihre Vorgänger oder Vorvorgänger. Mehr noch: Bei E-Autos werden der Verbrennungsmotor und die Abgasanlage zum Beispiel gar nicht mehr gebraucht. Andere Komponenten wie die Batterie sind hinzugekommen. Carl Benz fände das bestimmt eine höchst faszinierende Entwicklung. Das heißt auch, dass Ingenieure, Designer, Techniker und Lieferanten umdenken und Lösungen für neue Herausforderungen finden müssen. Was das für den Stahl im E-Auto bedeutet, erklärt mir heute der Direktor des Vertriebs Auto, André Matusczyk.
André Matusczyk: Hallo, schönen guten Tag! Ich freue mich sehr auf unseren Austausch heute.
Antonie Bauer: Ja, sehr schön, dass Sie hier sind. Damit sich unsere Zuhörer und Zuhörerinnen ein Bild davon machen können, wem Sie hier zuhören, wollen wir mit einer kleinen Vorstellung anfangen. Und dazu habe ich mal drei Fragen mitgebracht - die drei W‘s der Vorstellung. Die erste Frage an Sie ist: Was genau ist Ihre Aufgabe?
André Matusczyk: Bei thyssenkrupp Steel leite ich den Vertrieb Automotive. In unserem Bereich vermarkten wir unsere Flachstahlprodukte an die weltweiten Kunden der Automobilindustrie. In Europa beliefern wir quasi jedes Automobilwerk. Aber unsere Produkte sind auch in Nordamerika, in Asien gefragt. Überall dort, wo Fahrzeuge in großen Stückzahlen produziert werden. Aber unser Anspruch ist es auch, nicht einfach unseren Kunden eine Tonne Stahl zu liefern, sondern für jedes Bauteil die optimale Lösung in Stahl anzubieten. Und zu unseren Aufgaben gehört es natürlich auch, dass wir Trends erkennen, Trends begleiten und mitgestalten. Einer dieser großen Trends, die Elektromobilität, darüber unterhalten wir uns heute. Das ist natürlich wichtig, frühzeitig diese Tendenzen zu erkennen, den Kunden die entsprechenden Produkte anzubieten. Aber natürlich auch von den Kunden ddie Impulse für unser Unternehmen aufzunehmen, um die richtigen Produkte zu entwickeln und auch die richtigen Investitionen anzustoßen.
Antonie Bauer: Den Job kann man wahrscheinlich wirklich nur machen, wenn man auch wirklich sehr fasziniert ist, sowohl vom Stahl als auch von der Elektromobilität. Was genau fasziniert Sie denn?
André Matusczyk: Also erstmal zum Stahl. Das ist eine tolle Frage. Wenn ich die ausführlich beantworte, dann wird das wahrscheinlich die ganze Sendung füllen. Also will ich es mal bei einigen wenigen Punkten belassen. Zum einen ist da natürlich die wahnsinnige Vielfalt, die wir in Stahl gestalten können. Es ist egal, worauf wir gucken, was wir nutzen, Stahl umgibt uns jeden Tag und das rund um die Uhr. Egal ob das Mobilität ist, ob das Häuserbau ist, Infrastruktur. Jede Brücke, die wir überqueren, hat einen hohen Stahlanteil. Hausgeräte, Verpackungen, Konservenbüchsen, alles woran wir denken, umgibt uns mit Stahl. Dann ist natürlich Stahl, ohne Qualitätseinbußen, endlos recycelbar. Ich kann immer wieder aus einem Stahlprodukt ein neues Stahlprodukt machen. Und was mich total beeindruckt, das sind unsere Produktionsaggregate. Ich habe vor über 30 Jahren das erste Mal ein Stahlwerk besichtigt, hier bei uns in Duisburg. Das hat mich tief beeindruckt, und selbst heute gehe ich immer noch tief beeindruckt raus, wenn ich in unserer Produktion war. Also so gigantische Anlagen, in denen man am Anfang aus einem Rohstoff wie Eisenerz, fast in sandförmiger Konsistenz, am Ende ein hochwertiges Produkt hat für die Außenhaut eines Fahrzeugs beispielsweise. Und das in Größenordnungen, die einfach atemberaubend sind. Einfach mal zwei, drei Zahlen: Das Fürstentum Monaco, das passt vier bis fünfmal in unser Werksgelände. Bevor in den 90er-Jahren die Deutsche Bahn privatisiert worden ist, hatten wir hier die längste private Bahnstrecke in Deutschland und wir schütten über 65.000 Tonnen Rohstoffe in unsere Hochöfen. Und das jeden Tag. Seit Beginn der Industrialisierung, vor 250 Jahren, ist Stahl der prägende Werkstoff für die gesamte industrielle Wertschöpfung. Und wenn wir uns einfach mal überlegen, was es seit 250 Jahren an neuen Produkten gibt, an neuen Produktionsprozessen - und das alles hat Stahl begleitet, hat Stahl geprägt. Und auch heute ist Stahl der Werkstoff industrieller Wertschöpfung. Und das wird auch so bleiben, da bin ich mir sicher, weil es in Stahl noch unheimlich viel Potenzial gibt.
Antonie Bauer: Ja, da werden wir auch infolge unseres Gesprächs noch genauer darauf eingehen. Vorher noch einmal meine letzte W-Frage an Sie: Warum Sie heute hier mein Gesprächspartner sind.
André Matusczyk: Ich betreue seit vielen Jahren Kunden der Automobilindustrie und in der Automobilindustrie ist eines der strategischen Themen der Wandel zur Elektromobilität. Von daher bin ich mit vielen meiner Kunden im engen Austausch hierzu. Und wir haben auch schon intern bei thyssenkrupp Steel seit vielen Jahren das Potenzial für Elektromobilität, auch für unsere Produkte, für Stahl, erkannt und sind sehr eng mit diesen Themen befasst. Von daher hoffe ich, dass ich die richtigen Fragen und die richtigen Antworten in der Diskussion aufgreifen kann.
Antonie Bauer: Also fangen wir einfach mal mit der allumfassenden Frage an, die man vielleicht stellen kann oder mit der praktischsten Frage: Wie viel Stahl steckt denn überhaupt in einem Elektroauto und wo genau?
André Matusczyk: Also vom Grundsatz ist erstmal das Konstruktionsprinzip bei einem Elektrofahrzeug und einem konventionellen Fahrzeug gleich. Es gibt eine innere Fahrzeugstruktur, eine Art Gerippe, die dem Fahrzeug Stabilität gibt und - sollte es zu einem Unfall kommen - die Insassen schützt. Dann gibt es da eine Außenhaut, die hat verschiedene Funktionen. Zum einen natürlich ganz offensichtlich, dass wir trocken sitzen und es nicht reinregnet. Aber natürlich darüber hinaus steht die Außenhaut eines Fahrzeugs natürlich für das Fahrzeugdesign, für die Form eines Fahrzeugs und es ist ein ganz wichtiges Mittel für die Marken-DNA des jeweiligen Fahrzeugherstellers. Aber die Außenhaut ist auch die Unterlage, der Untergrund, für hochwertige Lackierungen. Das stellt sehr hohe Ansprüche an unsere Oberflächen. Aber hochwertige Oberflächen helfen natürlich auch bei unseren Kunden, umweltverträglich zu produzieren. Indem man beispielsweise wasserlösliche Lacke einsetzen kann und wir auch mit unseren Produkten einen Beitrag leisten zur Nachhaltigkeit. Darüber hinaus wird natürlich Stahl auch in der Außenhaut zur Stabilität benötigt, wir nennen das Steifigkeit eines Fahrzeugs. Das heißt, dass das Fahrzeug sich nicht verwindet, wenn wir auch mal schräg über die Bordsteinkante fahren.
Antonie Bauer: Also alltagstauglich bis ins Mark.
André Matusczyk: Ganz genau! Und beim Elektrofahrzeugfallen natürlich bestimmte Komponenten weg, der Verbrennungsmotor fällt weg, der Tank, die Auspuffanlage und es kommen andere Aggregate dazu - beispielsweise der elektrische Antriebsmotor, der sogenannte Traktionsmotor, die Elektronik und auch die Batterie. Und gerade die Batterie ist ein sehr empfindliches, auch ein sehr schweres Teil. Was auch durch einen schweren Batteriekasten, durch einen stabilen Batteriekasten, geschützt werden muss. Deswegen sind bei gleicher Größe Elektrofahrzeuge deutlich schwerer als konventionelle Fahrzeuge.
Antonie Bauer: Was heißt das denn ganz genau in Zahlen?
André Matusczyk: In Zahlen? Die Struktur eines aktuellen Elektrofahrzeugs, wie beispielsweise eines ID4, wiegt inklusive das Batteriekastens ca. 440 Kilogramm. Dazu kommen Türen und Klappen, also die Motorhaube oder der Kofferraumdeckel oder die Heckklappe mit noch mal etwa 120 Kilogramm. In der Struktur eines Fahrzeugs bringen alternative Werkstoffe, wie beispielsweise Aluminium, gar keine oder nur sehr geringe Gewichtsvorteile. Von daher finden wir hier vorwiegend Stahllösungen. Das gilt auch für die Anbauteile, wie wir Türen und Klappen auch nennen. Hier finden lediglich in teuren Fahrzeugen der oberen Mittelklasse oder der Oberklasse Aluminiumlösungen Eingang.
Antonie Bauer: Stimmt es, dass die Batteriekästen bisher noch gar nicht immer aus Stahl bestehen, sondern aus Aluminium, glaube ich?
André Matusczyk: Das ist leider richtig. Also bisher hat sich Stahl noch nicht vollständig durchgesetzt. Das hat auch einen sehr einfachen Hintergrund. Und zwar waren die ersten Fahrzeuge, die Fahrzeuge der ersten Generation als Elektrofahrzeuge, im Grunde genommen konventionelle Fahrzeuge, die im Nachgang eine Batterie und Batteriekasten als Komponente ergänzt bekommen haben. Und dieses zusätzliche Gewicht haben die Fahrzeughersteller versucht, durch den Einsatz von Aluminium zu kompensieren. Ich finde das natürlich schade, weil wir nachweisen konnten, in sehr detaillierten Untersuchungen, dass Lösungen in Stahl nur unwesentlich schwerer sind, aber deutlich nachhaltiger und auch deutlich kostengünstiger. Ich bin mir aber sehr sicher, dass wir in zukünftigen Fahrzeuggenerationen, wenn die Batterie und der Batteriekasten schon in der Fahrzeugkonstruktion berücksichtigt werden, wir weitaus mehr Batteriekästen in Stahl oder zumindest mit Mischbauweisen sehen werden. Man kann auch noch einen Schritt weitergehen, dass auch die Batterie und der Batteriekasten ein Teil der Funktionsintegration in zukünftigen Karosserien sind. Beispielsweise beim Seitenaufprallschutz: Auch da kann ein Batteriekasten natürlich eine Rolle übernehmen. Und das sind so die zukünftigen Entwicklungen, die ich sehe.
Antonie Bauer: Warum wird denn im Auto überhaupt Stahl verbaut und kein anderer Werkstoff?
André Matusczyk: Das liegt im Grunde genommen nicht an einer einzelnen Begründung, sondern es gibt ein ganzes Bündel an Ursachen, warum Stahl der führende Werkstoff ist. Zum einen ist Stahl weltweit verfügbar. Das ist natürlich wichtig bei einer globalisierten Produktion wie in der Automobilindustrie. Dann ist die Verarbeitung von Stahl jahrzehntelang erprobt. Es sind sichere Prozesse, vertraute Prozesse für unsere Kunden auch mit einer sehr hohen Produktivität. Denn Stahl ist ein sehr nachhaltiger Werkstoff, kann bei gleicher Qualität recycelt werden, ohne dass es irgendwelche Einbußen gibt. Und man kann eine Stahlkarosserie auch überall auf der Welt reparieren. Das ist bei anderen Konzepten nicht so selbstverständlich - wie zum Beispiel bei faserverstärkten Kunststoffen. Aber es gibt noch einen riesigen Vorteil bei Stahl. Und zwar ist das das Leichtbaupotenzial. Leichtbaupotenzial heißt, dass moderne Stähle sehr hohe Festigkeiten haben. Und durch diese Festigkeit kann ich die Dicke eines Bauteils deutlich reduzieren und trage damit zur Gewichtsreduzierung bei. Und das ist Leichtbau in einem sehr attraktiven Preis-Leistungs-Verhältnis, wir nennen das auch wirtschaftlichen Leichtbau.
Antonie Bauer: Gar nicht so das, was man mit Stahl eigentlich assoziiert, leicht und sauber und recycelbar. Aber ja, das haben wir auch in unserer letzten Folge ja auch schon thematisiert. Und bin immer wieder überrascht, was in diesem Werkstoff alles drinsteckt. Wir haben jetzt also schon gelernt: Stahl ist gut fürs Budget und sicher. Und auf das letzte würde ich gerne noch mal eingehen: Was passiert denn, wenn ein Auto, ein E-Auto in einen Unfall verwickelt wird und sogar anfängt zu brennen?
André Matusczyk: Also zum Glück brennen Fahrzeuge mit oder ohne Batterie nicht in großen Stückzahlen ab. Aber er ist völlig richtig, der Punkt. Eine moderne Hochleistungsbatterie ist eine sehr empfindliche Komponente und es muss alles getan werden, um bei einem Seitenaufprall die Zerstörung oder Beschädigung einzelner Batteriezellen zu verhindern. Auch hier kann, über den Batteriekasten hinaus, Stahl eine Rolle spielen, in der Seitenstruktur. Wir haben eben gehört: moderne Stähle sind mit hohen Festigkeiten versehen. Und auch eine B-Säule, das ist diese Säule zwischen Vorder- und Hintertür oder auch der Schweller, dieses unten längs am Fahrzeug laufende Teil, können natürlich durch hochfeste Stähle eine Sicherheitsfunktion übernehmen. Sollte es trotzdem zu einem Brand kommen, kann natürlich Stahl gegenüber anderen Werkstoffen eine Besonderheit ausspielen. Und das ist der Punkt, dass Stahl erst ab Temperaturen von 1.425 Grad schmilzt. Aluminiumlegierungen dagegen werden bereits ab etwa 500 Grad flüssig. Und das heißt, wenn ich eine entsprechend dimensionierte Abdeckung einer Batterie aus Stahl habe, kann das in einem Brandfall genau die erforderlichen Minuten bringen, um Menschenleben zu retten.
Antonie Bauer: Also unser Batteriegehäuse beweist, also Leichtbau, Sicherheit und Brandschutz lassen sich verbinden und Sie hatten gerade auch noch die Umweltverträglichkeit erwähnt. Was hat es denn damit genau auf sich?
André Matusczyk: Ja, der Bau von Elektrofahrzeugen ist ja kein Selbstzweck. Wir wollen ja bewusst Emissionen aus der Umwelt herausnehmen. Jetzt hat ein Elektrofahrzeug keinen Auspuff mehr, keine lokalen Emissionen. Aber bei der Produktion eines Elektrofahrzeugs entstehen natürlich auch umweltschädliche Emissionen. Und bei diesen sogenannten produktionsbedingten Emissionen ist der Blick auf die Werkstoffauswahl sehr wichtig. Wir nennen das Lifecycle Assessment. Das heißt die Beurteilung von Emissionen von der Produktion eines Fahrzeugs über die Nutzungsphase bis zur Entsorgung. Und auch da ist Stahl ganz weit vorne. Wir haben das beim Batteriekasten nachgewiesen, dass wir bei einem geringen Mehrgewicht die CO2-Emissionen um etwa um 50 Prozent absenken können und das bei deutlich geringeren Kosten.
Antonie Bauer: Das ist ja irre, weil eigentlich heißt es ja immer, die Stahlindustrie ist einer der größten CO2-Emittenten und ja, wie kann dann eine Stahllösung nachhaltig sein?
André Matusczyk: Das ist eine gute Frage. Im Jahr 2019 – das letzte normale Jahr vor Corona, ist ja inzwischen schon fast schon die Zeitenwende vor und nach Corona, also im Jahr 2019 betrug die weltweite Rohstahlproduktion knapp 1,9 Milliarden Tonnen. Demgegenüber wurden in etwa 64 Millionen Tonnen Aluminium erzeugt. Das heißt, weltweit wird etwa 30-mal mehr Stahl als Aluminium produziert. Auf der einen Seite zeigt das natürlich die enorme Bedeutung von Stahl für alle Branchen. Auf der anderen Seite erklärt das natürlich auch, warum die Stahlindustrie in der Liste der CO2-Emittenten sehr weit oben steht. Aber im Fahrzeugbau zählt die individuelle Emission und die individuelle Klimabilanz auf der Bauteilebene und auch da ist Stahl wiederum ganz vorne.
Antonie Bauer: Wir haben jetzt gelernt, dass Stahl wirklich ein hoch leistungsfähiger Allrounder ist. Und ja, trifft das auch auf das Elektroband zu? Und was ist das ganz genau?
André Matusczyk: Ja, Elektroband ist eine spezielle Sorte Stahl mit ganz besonderen magnetischen Eigenschaften. Wir unterscheiden zwei Arten von Elektroband: Kornorientiertes Elektroband und nicht kornorientiertes Elektroband. Ein bisschen vereinfacht kann man sagen: Kornorientiertes Elektroband finden wir in Transformatoren. Transformatoren, zum Teil sehr mächtige Geräte, sorgen dafür, dass wir Spannungen erhöhen oder auch wieder absenken können. Das heißt für den Transport von Strom, für den verlustfreien Transport über große Entfernungen, müssen wir die Stromspannung deutlich erhöhen auf bis zu 550.000 Volt, um sie dann wiederum am Ort des Verbrauches auf die haushaltüblichen 230 Volt zu reduzieren. Und wir sehen auch in der Elektromobilität spielen Transformatoren eine große Rolle - beispielsweise bei Ladesäulen. Entweder habe ich an einer Ladesäule einen Transformator oder ein großer Transformator versorgt mehrere Ladesäulen mit Strom. Das nicht kornorientierte Elektroband, das finden wir überall dort, wo Generatoren Strom erzeugen, in Kraftwerken konventioneller Art, aber auch in Kraftwerken, die auf regenerativer Energie beruhen, mit Windkraft, mit Wasserkraft. Und am Ende der Versorgungskette Strom, also bei den Verbrauchern, bei den Anwendern wird wiederum nicht kornorientiertes Elektroband eingesetzt. Bei den Motoren, in den Produkten, die wir benutzen: Waschmaschine, Fön oder eben auch dem Antriebsmotor in einem Elektrofahrzeug. Aber zusammenfassend kann man sagen, dass sowohl die Energiewende als auch die Mobilitätswende ohne Elektroband nicht möglich ist.
Antonie Bauer: Also neu ist das Elektroband ja offenbar nicht, oder?
André Matusczyk: Nein, Elektroband als Magnetwerkstoff für Motoren, Generatoren und Transformatoren ist ein sehr bewährtes Produkt. Aber die Elektromobilität stellt jetzt noch ein ganz anderes Anspruchsniveau an diesen Werkstoff. Und wir sehen das beispielsweise bei kornorientiertem Elektroband. Wenn wir an die Ladesäulen an Autobahnen denken, an Raststätten, hier werden Batterien mit bis zu 350 Kilowatt geladen. Und das stellt natürlich immense Anforderung an die vorgeschalteten Transformatoren. Hier müssen sehr anspruchsvolle technologische Kennwerte erfüllt werden, um Magnetisierungsverluste, Polarisation, um die gesamte Energieeffizienz in diesem Punkt sicherzustellen. Aber auch bei nicht kornorientiertem Elektroband ist die Effizienz eines Elektromotors von großer Bedeutung, denn wir müssen sehr hohe Gewichte in den Fahrzeugen beschleunigen. Und natürlich ist auch die Reichweite ein wesentlicher Faktor für die Akzeptanz von Elektromobilität. Von daher werden zum Effizienzgewinn die Dicken immer geringer bei sehr hohen Festigkeiten aufgrund der Kräfte bei hohen Drehzahlen - und deswegen sind wir auch weiterhin hier sehr aktiv, um das Produkt weiter genau in diesem Feld zu optimieren.
Antonie Bauer: Und ihr macht euch ja nicht nur über die Qualität und das Gewicht und die Kosten eines Werkstoffs Gedanken, sondern auch über Geräuschreduzierung, was ja vermeintlich gar nicht zu den ach so leisen Elektroautos passt. Was hat es denn damit auf sich?
André Matusczyk: Das ist richtig. Im Grunde genommen ist ein Elektrofahrzeug deutlich leiser als ein Verbrenner. Ich habe keine fauchenden Motoren, keine röhrenden Auspuffanlagen mehr. Aber es gibt auch durchaus in Elektrofahrzeugen Geräusche, die unangenehm sind. Und zwar sind das im Motor oder in der Leistungselektronik ein hochfrequentes Surren. Jeder von uns kennt morgens um drei Uhr den Moskito im Schlafzimmer, der dann so ums Ohr summt, das kann schon ganz schön nervig sein. Aber auch hierfür haben wir ein tolles Produkt mit einer sehr guten Lösung. Das Produkt nennt sich bondal CB. bondal ist ein sogenannter Sandwich-Werkstoff. Der ist auch tatsächlich aufgebaut wie ein Sandwich. Es gibt zwei äußere Stahlschichten und eine innenliegende Kunststoffschicht. Und dieser Aufbau gewährleistet, dass man Schall sehr gut absorbieren kann. Ich habe schon erste Serienanwendungen. Damit können wir den Schalldruck um etwa 20 Dezibel absenken. Das ist eine Reduzierung auf etwa ein Viertel des Ausgangwertes. Von daher haben wir mit einem tollen Werkstoff das Problem gelöst. Einfache Stahl- oder Aluminiumprodukte schaffen das nicht. Es sei denn, man fügt gewichtstreibende, teure Akustikmaßnahmen hinzu. Was wir aber eigentlich nicht wollen.
Antonie Bauer: Sie hatten es jetzt auch gerade schon angedeutet: Elektromobilität ist irgendwo Stand der Technik, aber auch noch nicht ausentwickelt, oder? Welche Herausforderungen kommen da in Zukunft auch noch auf Sie und Ihr Team zu?
André Matusczyk: Ja, wir haben da noch sehr große Potenziale und werden auch viele Dinge noch optimieren. Ich kann mir sehr gut vorstellen, dass wir in Bezug auf Leichtbau weitere Stahlgüten entwickeln, die den Anforderungen für Elektromobilität noch besser gerecht werden. Hierzu sind wir bereits im engen Austausch mit unseren Kunden, um auch hier die zukünftigen Konstruktionsanforderungen von Elektrofahrzeugen mit unseren Produkten weiter zu begleiten. Und das gleiche gilt auch bei Elektroband, kornorientiert und nicht kornorientiert. Auch hier sind weitere Optimierungen möglich. Hier werden wir weiter an der Effizienz arbeiten, sowohl bei kornorientiertem als auch bei nicht kornorientiertem Elektroband. Die Ansprüche, die werden weiter steigen, aber genau diese Produkte wollen wir weiterhin unseren Kunden anbieten, auf neuestem Stand der Technik. Und wir produzieren genau diese Produkte an unseren Standorten in Gelsenkirchen für kornorientiertes Elektroband, in Bochum für nicht kornorientiertes Elektroband. Und da werden wir natürlich weiterhin Vollgas geben, um alle Bedarfe unserer Kunden auch so zu begleiten.
Antonie Bauer: Wenn wir wirklich saubere Mobilität wollen, dann müssen wir auch den Werkstoff Stahl in Zukunft CO2-frei herstellen. Und da haben wir ja auch glaube ich thyssenkrupp-intern große Pläne bzw. ich glaube es nicht nur, ich weiß es, weil sich unsere letzte Folge genau darum drehte. Vielleicht können Sie dazu auch noch ein paar Worte sagen.
André Matusczyk: Das ist richtig. Wenn wir wirklich saubere Mobilität möchten, ist es natürlich auch wichtig, dass der Werkstoff Stahl CO2-frei wird. Wir haben hierfür eine eigene innovative Technologie entwickelt und uns sehr ehrgeizige Ziele gesetzt. Wir wollen im Jahr 2030 schon beträchtliche Mengen CO2-reduziert anbieten und in Summe 30 Prozent unserer CO2-Emissionen rausnehmen. Bis 2050 wollen wir dann komplett CO2-frei sein. Ein Punkt, der wirklich wichtig ist, ist, dass wir stabile Rahmenbedingungen haben für diese Schritte, und zwar nicht nur hier, sondern auch weltweit: Hier, in China, Indien, Russland, auf der ganzen Welt. Wir sind hier nicht auf einer isolierten Insel. Und ein wichtiger Punkt, den man auch nicht verschweigen darf, ist, dass es Umweltschutz und null Emissionen nicht umsonst gibt. Das heißt, die Produktion und der Betrieb CO2-freier Fahrzeuge wird am Ende eine höhere Zahlungsbereitschaft erfordern.
Antonie Bauer: Jetzt kommen wir noch einmal ganz kurz darauf zu sprechen, wie denn die Innovation und die Werkstoffe, die Entwicklung so vonstattengeht. Also muss ich mir das vorstellen, wie: Da sitzen Menschen im Elfenbeinturm und entwickeln vor sich hin oder wie bekommen Sie diese schlauen Köpfe zusammen?
André Matusczyk: Nein, bei uns sitzen natürlich nicht Leute im Elfenbeinturm mit wirrer Haarmähne und tüfteln vor sich hin. Sondern wir haben hochqualifizierte Produktentwicklungsprofis und sind hierzu im sehr engen Austausch mit unseren Kunden, weil uns einfach wichtig ist, dass wir unsere Produktentwicklungen entlang von Kundenbedürfnissen und entlang von Marktbedürfnissen ableiten. Allein in unserem Bereich Innovation haben wir etwa 250 Kolleginnen und Kollegen, die sich mit der Optimierung bestehender Stähle oder mit der Entwicklung neuer, innovativer Stähle beschäftigen. Aber natürlich haben wir auch weitere Bereiche in verschiedenen Produktmanagementbereichen. In meinem Team haben wir einen Bereich Produktmanagement, um die nötigen Impulse zu geben, um hier die Markteinblicke zu haben. Aber wir haben natürlich viele Multiplikatoren entlang unterschiedlicher Abteilungen, auch in der Produktion, die diesen ganzen Prozess unterstützen.
Antonie Bauer: Na klar und man muss ja auch noch mit den Kunden sprechen, […]
André Matusczyk: Das ist die Basis für alles, für unsere Kunden machen wir das.
Antonie Bauer: Die geben ja auch die ganzen Impulse rein.
André Matusczyk: Richtig.
Antonie Bauer: Gut, dann fehlt uns eigentlich noch die wichtigste Frage: Fahren Sie denn selbst auch ein Elektroauto?
André Matusczyk: Ich bin schon verschiedene Elektrofahrzeuge unterschiedliche Hersteller gefahren. Eine wirklich beeindruckende Technologie. Ich selbst fahre noch kein Elektrofahrzeug. Aber jetzt, mit der zunehmenden Verfügbarkeit von Elektrofahrzeugen, plane ich, nächstes Jahr umzusteigen. Vielleicht machen wir da mal eine gemeinsame Probefahrt und gucken, was aus Elektromobilität bis dahin geworden ist.
Antonie Bauer: Ich bin dabei, gar kein Problem.
Stahl ist also der Werkstoff für die Elektromobilität. Darüber haben wir heute einiges erfahren von einem Experten, der ganz nah dran ist, wenn es darum geht, den Wandel der Automobilbranche zu begleiten und zu unterstützen. Ich versuche mal die wichtigsten Punkte zusammenzufassen: Erstens, Stahl ist heute der erfolgreichste Leichtbauwerkstoff im Fahrzeug und verfügt auch für elektrisch angetriebene Autos über optimale Eigenschaften. Zweitens, gefragt sind vor allem wirtschaftliche Leichtbau, Lösungen, um die Mobilitätswende voranzutreiben. thyssenkrupp Steel entwickelt weiterhin auf Hochtouren optimierte Stahllösungen für seine Kunden. Drittens, Stahl ist der Werkstoff, auf den es bei der Mobilitäts- und Energiewende ankommt. Er ist ein unverzichtbarer Basiswerkstoff in der Karosserie und alternativlos im Antriebsstrang sowie der Energiegewinnung und Verteilung. Viertens, hohe Energieeffizienz bei Antrieben und Transformatoren erfordern Hochleistungselektrobänder mit Spitzenwerten in Polarisation und geringen Verlusten. Und fünftens, langfristig muss auch die Stahlproduktion CO2-frei werden. thyssenkrupp Steel verfügt hierzu über geeignete Technologie. Die Transformation kann aber nur im Schulterschluss mit der Politik, den Autoherstellern und den Autokäufer gelingen. Herr Matusczyk, haben Sie dazu noch was hinzuzufügen? War das richtig so?
André Matusczyk: Das war perfekt auf den Punkt gebracht. Vielen Dank für die Gelegenheit, über das Thema hier zu sprechen. Hat mir großen Spaß gemacht.
Antonie Bauer: Vielen Dank, bis dann.
André Matusczyk: Bis dann.
Antonie Bauer: In der nächsten Folge geht es heiß her: Wir nehmen euch mit auf die sechste Hochofenreise des Hochofens Schwelgern 1 und gehen der Stahlherstellung auf den Grund vom Eisenerz zum Roheisen. Uns ist wichtig, eure Meinung zum Podcast und eure Fragen zum Thema Stahl zu hören. Daher schreibt uns gern eine E-Mail an: [email protected]. Lasst uns wissen, wie euch der Podcast gefällt oder welche Themen rund um Stahl wir zukünftig beleuchten sollen. Mehr Stahlwissen, Eindrücke und Stories gibt es übrigens auch auf unseren Social-Media-Kanälen und auf unserer Webseite. Die Links dazu findet ihr in den Shownotes. Das war die vierte Folge von „Gekocht, Gewalzt, Veredelt“. Mein Name ist Antonie und ich freue mich, wenn wir uns bei der nächsten Folge wieder hören. Macht's gut.
Folge 3: Stahl trifft Klima – Wie grün kann Stahl sein?
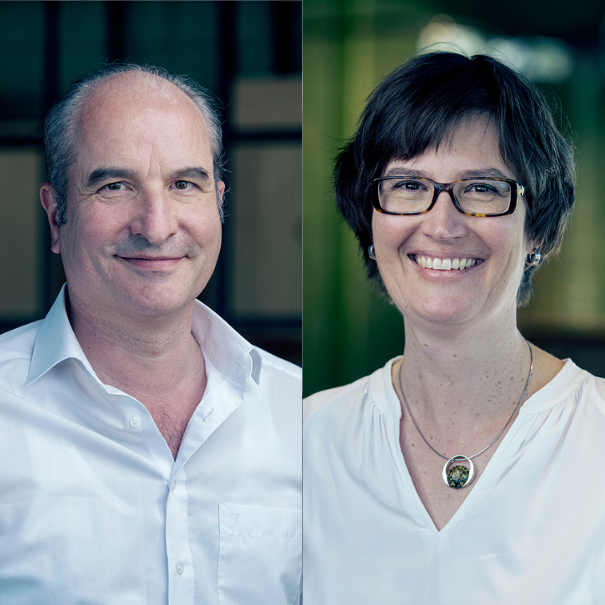
Der Stahl der Zukunft wird klimaneutral produziert. Das ist unser Ziel. Auf dem Weg zur klimaneutralen Stahlproduktion befinden wir uns schon lange. Welche technologischen Innovation wir bereits auf den Weg gebracht haben, was wir noch vorhaben und welche gesellschaftlichen wie politischen Rahmenbedingungen es braucht, darüber sprechen wir im Podcast. Und zwar mit Matthias Weinberg, Leiter Kompetenzcenter Metallurgie, und Roswitha Becker, Teamleiterin CO2-Forschung und alternative Technologien, zwei unserer Klima-Expert:innen.
Antonie Bauer: Es glüht. Es dampft. Es raucht. So kennen wir die Stahlherstellung. Kamine und Schlote aus den Schwaden in den Himmel steigen. Hochöfen, in denen tonnenweise Kohle verbrennt. Stahl ist, müssen wir so sagen, bisweilen ein Klimasünder. Da muss man sich in Zeiten steigender Meeresspiegel und anhaltender Dürren schon fragen: Können wir es uns in Zukunft überhaupt noch leisten, Stahl zu produzieren? Willkommen zur dritten Folge von unserem Podcast. Gekocht, gewalzt, veredelt. Der Stahl-Podcast, indem wir uns mit dem Werkstoff Stahl auseinandersetzen und mit allem was dazugehört. Mein Name ist Antonie und ich darf euch durch die Folge führen.
In dieser Folge beschäftigen wir uns mit der Frage, ob und wie klimafreundlich Stahl eigentlich sein kann. Wir schauen uns an, wie Stahl hergestellt wird und warum dabei so viel Kohlendioxid entsteht. Das Treibhausgas Nr. 1 ist es ja. Wir sprechen darüber, welche Wege es gibt, Stahl auch ohne Treibhausgase herzustellen. Grünen Stahl sozusagen. Dabei werden wir lernen: Das kann funktionieren, bedeutet aber auch einen ziemlichen Bruch in der Geschichte von Stahl. Auch reden wir über die Bedeutung von Stahl für eine klimaneutrale Gesellschaft. In Duisburg, hier sind wir ja auch gerade, steht das größte Stahlwerk Deutschlands. Und allein dieses Werk, erzeugt jedes Jahr 20 Millionen Tonnen CO2. Das hört sich nicht nur nach viel an. Das ist auch viel. 20 Millionen Tonnen sind knapp 2,5 Prozent aller deutschen CO2-Emissionen und in einem Monat so viel, wie alle Flüge innerhalb Deutschlands in einem Jahr verursachen. Dass aus diesen 20 Millionen Tonnen in Zukunft mal null Tonnen werden, darum kümmern sich in Duisburg bei thyssenkrupp mittlerweile ganze Abteilungen. Zwei Mitglieder:innen dieses großen Teams habe ich mir heute an den Tisch geholt. Zum einen ist das Matthias Weinberg, der das Kompetenzcenter Metallurgie leitet und zum anderen Roswitha Becker, die innerhalb dieses Kompetenzcenters den Bereich CO2-Forschung und alternative Technologien verantwortet.
Matthias Weinberg und Roswitha Becker: Hallo
Antonie Bauer: Herzlich willkommen! Schön, dass ihr da seid. Ich werde euch jetzt zu Beginn einmal drei Fragen stellen. Wir nennen es die drei W´s der Vorstellung. Wir beginnen mal mit dir Matthias. Was genau ist deine Aufgabe? Was macht die Faszination „Stahl“ für dich aus? Und warum bist du heute hier?
Matthias Weinberg: Schöne Fragen. Weil ich gelernter Metallurgie bin, hat man mir die Aufgabe angetragen, mich um die CO2-arme oder CO2-freie Stahlherstellung zu kümmern. Das Optimierungskriterium, das waren früher immer Euros oder Qualität. Und heute ist es auf einmal CO2. Und das ist natürlich eine wirklich hochinteressante Aufgabe. Damit ist auch so ein bisschen die Aufgabe der Abteilung umschrieben. Da ist also alles zusammengeführt, was hier in Sachen Metallurgie-Kompetenz mitbringt. Und jeden Tag gibt es neue Herausforderungen. Themen, die wirklich spannend sind, zu diskutieren mit ambitionierten Kollegen. Das macht einfach Spaß. Da vergeht auch die Zeit wie im Flug. Das ist eine Aufgabe, die keine Routine mitbringt.
Antonie Bauer: Roswitha. Siehst du das auch so? Vielleicht kommen wir dann einmal kurz zu dir. Was machst du denn genau? Und wie oder inwiefern fasziniert dich der Baustoff Stahl?
Roswitha Becker: Ja, also mich fasziniert dieser Werkstoff Stahl eigentlich schon von klein auf. Wenn man hier in Duisburg groß wird. Man hat wirklich diese archaisch anmutende Technik, gerade hier in den Heiß-Betrieben. Das ist ja etwas, wo man sich gar nicht vorstellen kann, dass mit so grob wirkender Technik hinterher ein echtes Hightech Produkt entsteht. Und gerade dieses Spannungsfeld, das wird jetzt noch durch eine weitere Facette erweitert. Das ist eben, wenn ich dieses Produkt jetzt auch noch CO2 reduziert, grün anbieten möchte. Weil ich diese Faszination, die spiegelt sich jetzt auch darin wieder, dass wir jetzt mit dem Team, in dem wir arbeiten, wirklich gucken, wie können wir entlang des gesamten Produktionsweges, Möglichkeiten herausarbeiten und bewerten, um CO2 zu reduzieren?
Antonie Bauer: Ja super. Das war jetzt schon sehr gut zusammengefasst, worum es in der Folge noch gehen wird. Perfekt. Genau. Ich habe ja gerade schon mal mit dieser Wahnsinns Zahl gespielt, mit den 20 Millionen Tonnen CO2. Damit ist Stahl einer der CO2 intensivsten Industrien überhaupt. Und fangen wir deshalb mal ganz am Anfang an. Wieso entsteht hier in Duisburg beim Stahl so viel CO2? Wie funktioniert die Stahlherstellung denn genau?
Matthias Weinberg: Ja, da kann ich gerne beantworten. Es gibt also eine chemische Notwendigkeit, dort den Sauerstoff vom Eisenoxid (Erz) zu entfernen. Und ob ich den Sauerstoff nun mit einem Kohlenstoffatom zu CO2 verheirate. Oder aber, wie in dem Fall, den wir hier diskutieren wollen, mit Wasserstoff zu Wasser oder Wasserdampf. Das ist am langen Ende, dem Eisenatom egal. Aber, um diese chemische Notwendigkeit, den Sauerstoff dort abzutrennen, kommt man nicht drum herum.
Antonie Bauer: Stahl wird ja nicht erst seit gestern hergestellt. Wir haben uns ja auch in der ersten Folge schon damit beschäftigt. Aber das Thema CO2, das ist irgendwie trotzdem neu. Wie kommt das?
Matthias Weinberg: neu, kann man nicht wirklich sagen. Es wird ja schon sehr, sehr lange diskutiert. Der Klimawandel ist ja nun in aller Munde und das schon seit Dekaden. Es ist nur unglaublich aufwendig und unglaublich schwierig und da hätte natürlich der Konsument, der zu der Zeit noch nicht so ambitioniert über Klimawandel diskutiert hat, wie heutzutage, hätte er gesagt: Warum soll ich jetzt hier Stahl kaufen, der so viel teurer ist, das ist doch genau wie der andere Stahl – der konventionelle. Es heißt also, um es ganz platt zu sagen, ich glaube, die Gesellschaft war nicht reif für CO2armen Stahl.
Antonie Bauer: Und das ändert sich jetzt nach und nach. Gibt es denn Möglichkeiten, Stahl auch anders herzustellen, als man es jetzt all die Jahrhunderte gemacht hat? Ich frage das natürlich, weil ich weiß, dass es andere Möglichkeiten gibt.
Roswitha Becker: Der Matthias hat es ja gerade schon angesprochen. Wenn wir jetzt die Kohle durch Wasserstoff ersetzen wollen, was möglich ist, dann ist das – du sagtest Matthias. Das ist ein Paradigmenwechsel. Ich empfinde es quasi als Revolution, weil ich glaube, vor 20 Jahren, da wäre man für verrückt erklärt worden. Und das ist ja diese Revolution, die bringen wir jetzt damit quasi auf den Weg. Und es gibt die Technologien. Es gibt sie wahrscheinlich im Kleinen. Aber wir sind jetzt dabei, sie eben auch auf einen größeren Maßstab einfach umzusetzen. Und in Duisburg hier. Da reden wir von, in Summe 10 Millionen Tonnen Stahl, die wir pro Jahr produzieren. Und das ist wirklich ein großer Maßstab.
Antonie Bauer: Weil du gerade Technologien sagtest. Ich habe in der Vorbereitung auf den Podcast, da bin ich über den Begriff „Carbon2Chem“ gestolpert. Inwiefern ist das auch eine Technologie, die angewendet wird?
Matthias Weinberg: Jeder, der technisch ein bisschen Erfahrung hat, weiß, dass die letzten paar Prozente immer die schwersten sind. Die ersten Einsparungen von einem neuen Verfahren, das es klappt, in der Regel, aber die letzten, wirklich die allerletzten Prozentpunkte rauszuholen, ist immer kritisch. Und dafür gibt es „Carbon2Chem“. Das heißt, wenn wir jetzt hier Stahlherstellung auf Wasserstoffbasis etablieren, gehen wir nicht davon aus, dass wir Kohlenstoff komplett vermeiden können. Ich will ein einfaches Beispiel nennen: Ein Kugellager-Stahl zum Beispiel. Wenn Sie so einen Stahl haben wollen, dann muss da circa 1% Kohle drin sein. Ansonsten ist der Stahl zu weich, um daraus ein Kugellager zu machen. Das fordert das Material. Wenn Sie die Kohle in den Stahl reinkriegen wollen, wo sie dann gebunden ist, wird Ihnen das nicht verlustfrei gelingen. Und da gilt dann unsere grundsätzliche Einstellung. An erster Stelle gilt „Vermeidung“ und an zweiter Stelle gilt „Recycling“. Und dafür gibt es hier „Carbon2Chem“. Wir gehen nicht davon aus, dass wir zu 100% jede CO2-Emission vermeiden können. Also recyceln wir den Rest und können daraus z.B. Treibstoffe oder chemische Grundstoffe herstellen.
Antonie Bauer: Was sind denn da so die Herausforderungen, gerade in Bezug auf Wasserstoff? Da ist die Versorgung ja auch ziemlich „Tricky“, würde ich sagen. Was ist denn da die Herausforderung, wenn es um Wasserstoff geht?
Roswitha Becker: Da sind eigentlich mehrere. Wir haben viele Konkurrenten, sowohl im Industriesektor, allerdings auch wenn es um den Verbraucher geht, wenn es um Mobilität geht. Das ist, sagen wir mal, das Positive, weil damit ein Markt für den Wasserstoff geschaffen wird. Andererseits muss dieser Markt auch zu Konditionen geschaffen werden, die für uns dann noch attraktiv sind. Und da können natürlich unterschiedliche Teilnehmer, was diesen Markt angeht, mit anderen Preisen einsteigen. Und wir brauchen an der Stelle, für uns immer noch ein Geschäftsmodell für auch grüne Produkte, die wir damit herstellen wollen.
Antonie Bauer: Auf die Kosten wollen wir auch gleich nochmal zu sprechen kommen. Wie sieht es denn mit der Versorgung durch Wasserstoff aus? Gibt es da jetzt irgendwie, wie muss ich mir das vorstellen? Gibt es schon Wasserstoff-Tankstellen? Gibt's schon Leitungen, die gelegt sind und man muss das nur noch abzapfen?
Matthias Weinberg: Wir haben hier ein Wasserstoffleitungsnetzwerk. Das ist keine richtig große Pipeline. Aber mit der kann man schon mal anfangen. Die läuft also hier vom Chemiepark Marl bis runter in Richtung Köln. Da verbindet ihr also sämtliche Chemie Standorte. Diese Leitungen, die wollen wir benutzen, weil die Mengen an Wasserstoff, die wir hier brauchen, sind, erheblich. Deshalb ist hier der Standort eigentlich ganz gut. Wegen dieser Koexistenz von Stahlindustrie und Chemieindustrie, gibt es hier schon seit der Nachkriegszeit ein ausgedehntes Pipeline-Netz, was wir nutzen können.
Antonie Bauer: wenn wir über Wasserstoff sprechen, über welche Mengen, also welche Mengen muss ich mir vorstellen, die wir, die die Stahlproduktion braucht?
Matthias Weinberg: Für die gesamte Produktion, die wir hier in Duisburg machen, würden wir die komplett auf Wasserstoff umstellen, bräuchten wir circa 700 000 Tonnen jährlich. Wir bräuchten zwei Gasometer, komplett gefüllt mit Wasserstoff. Jede Stunde. Das sind also immense Mengen. Und das, was wir hier an Pipeline-Netzwerk haben, muss natürlich signifikant ausgebaut werden, damit diese Mengen nach hier transportiert werden können.
Antonie Bauer: Die Mengen müssten ja auch erst mal hergestellt werden.
Roswitha Becker: Die Menge ist ja das eine Problem an der Stelle. Das Andere ist, dass auch ein grünproduzierter Wasserstoff vonnöten ist.
Matthias Weinberg: Da muss ich natürlich direkt noch ergänzen, dass man da Ziel und Weg nicht verwechseln darf. Ziel ist selbstverständlich eine klimaneutrale Stahlherstellung. Der Weg dahin. Das kann durchaus Sinn machen, dort mit Zwischenlösungen, wie zum Beispiel grauem Wasserstoff zu arbeiten, um die Technik voranzubringen. Dann kriege ich eigentlich auf der Zeitschiene eine optimale Performance.
Antonie Bauer: kann mir aber vorstellen, dass es trotzdem ein hoher Kostenfaktor ist. Worüber sprechen wir denn da? Und wie wirkt sich das auch auf das Endprodukt, auf den Stahl und nachher aus?
Matthias Weinberg: Die Stahlpreise sind bisher immer auf einem Niveau gewesen, an das wir uns über Dekaden gewöhnt haben, das sehr, sehr niedrig ist. Das alles ist nur möglich, wegen dem großen Maßstab, indem wir das hier produzieren. Klimawandel ist ein gesamtgesellschaftliches Problem. Dann muss natürlich jeder seinen Teil dazu beitragen. Und das wird dann so aussehen, dass sich natürlich der Preis für CO2-armen Stahl erhöht. Anders wird es nicht gehen.
Antonie Bauer: Besteht denn die Gefahr, dass unser Stahl dann so teuer wird, dass ihn keiner mehr kauft und dann einfach woanders einkauft?
Matthias Weinberg: Das ist eine sehr gute Frage. Der Stahlpreis, der resultieren wird, aus den Umstellungen der Verfahren, wird dann zu einem erheblichen Teil durch den Energiepreis bestimmt. Und wenn ich jetzt konkurriere mit Ländern, in denen sehr, sehr preiswert Energien verfügbar sind z.B. Atomstrom, dann habe ich natürlich eine Konkurrenzsituation, in der es schwierig ist zu bestehen. Das muss in einer geeigneten Art und Weise natürlich reguliert werden. Und besonders, natürlich vor dem Hintergrund der deutschen Energiepolitik muss beachtet werden, dass die deutsche Stahlindustrie als Wurzel der industriellen Wertschöpfung nicht hintenüberfällt, weil es hier keine Kernkraft mehr gibt und der Strom vergleichsweise teuer ist.
Antonie Bauer: Was muss sich denn auf politischer Ebene tun, damit grüner Stahl nicht nur ein Zukunftsbild ist, sondern Realität wird?
Matthias Weinberg: Ist eine sehr interessante Frage, weil natürlich unsere augenblicklichen politischen Systeme auch mit einem völlig neuen Set an Anforderungen konfrontiert sind, müssen zahlreiche Regularien verändert werden. Wenn wir CO2-Freiheit als gesellschaftliche Anforderungen diskutieren, dann werden da nicht alle mitziehen. Und das erfordert natürlich einen Regulierungsrahmen, einen gesetzlichen.
Antonie Bauer: Wird sich dieses Endprodukt, von dem wir dann sprechen, wird es nicht eigentlich in irgendeiner Form unterscheiden, von dem Stall, den wir jetzt gerade produzieren?
Roswitha Becker: Das ist ja nun gerade das Ziel, was wir verfolgen, dass wir einen CO2-reduzierten Stahl anbieten, der aber in all seinen anderen Ausprägungen, mechanischen Eigenschaften, Oberfläche, dass er genau in der gleichen hohen Qualität den Kunden erreicht, wie er es bisher gewohnt ist.
Matthias Weinberg: Ja, eigentlich muss man dazu noch sagen, dass eine Qualitätsverschlechterung überhaupt keine Option wäre, weil wir damit nämlich direkt die auf Hightech angewiesene industrielle Wertschöpfung hier in Frage stellen. Was kaum jemandem geläufig ist, dass Stahl mittlerweile Festigkeiten erreicht, die das Vierfache Niveau von Aluminium haben. Das sind Hightech Werkstoffe, die da heute, von uns hierhergestellt werden. Die wären vor 20 Jahren noch undenkbar gewesen,
Roswitha Becker: Wenn ich da vielleicht noch ergänzen darf, dass gerade der Klimawandel, ja auch die Nachfrage nach hochqualitativen Stählen noch einmal extra befeuert. Denn Stahl ist ein Werkstoff, der auch die erhöhte Nachfrage nach Elektro-Mobilität begleitet. Der Stahl wird eingesetzt für Generatoren, für Transformatoren, Elektromotoren. Das ist etwas, wo ich auch wirklich Hightech-Stähle brauche. Und da können keine Qualitätsverlust in Kauf genommen werden.
Antonie Bauer: Die erste neue Anlage bei thyssenkrupp Steel soll in einigen Jahren stehen. Was genau passiert denn, wenn ihr jetzt gleich nach dem Podcast ins Büro fahrt? Was liegt da auf einem Schreibtisch? Was habt ihr zu tun?
Roswitha Becker: Du hattest ja gerade den grünen Stahl angesprochen. Es ist schön, wenn wir uns hier darüber unterhalten und sagen: Er hat die gleichen Eigenschaften, ist aber ansonsten nur CO2-reduziert. Das muss ja auch nochmal belegt werden. Das heißt, es muss von einer unabhängigen Stelle geprüft werden. Und erst, wenn da wirklich ein Stempel drauf ist, der uns bescheinigt, ihr habt sauber gearbeitet, richtig gerechnet, bringt ein grünes, CO2-reduziertes Produkt auf dem Markt. Erst dann hat es auch den nötigen Mehrwert für den Kunden, denn dafür ist es unabdingbar, dass da ein entsprechendes Zertifikat mit verbunden ist. Und das ist das, was mich dann gleich wieder beim Schreibtisch erwarten wird.
Antonie Bauer: Und bei dir, Matthias
Matthias Weinberg: Na, bei mir ist es natürlich auch in Teilen dieselbe Problemstellung. Ich würde es aber noch ein bisschen anders beschreiben, weil für mich eine spezielle Challenge darin besteht, step by step, eine wirklich technisch und wirtschaftlich durchhaltbar Transformation hier gestalten. Und das ist natürlich eine spezielle Herausforderung. Da sage ich immer Jeder kennt das Ziel, aber keiner kennt den Weg. Also es ist ganz interessant, was da alles zu berücksichtigen ist. Das unterschätzt man als Außenstehender vollständig.
Antonie Bauer: Eine Mammutaufgabe, kann man, glaube ich, nicht anders sagen. Ich komme ja selber auch aus dem Pott und ich bin vorhin auch über die Autobahn gekommen. Da fährt man ja quasi auf die Hochofen Skyline zu. Inwiefern wird sich genau diese denn verändern? Durch die Neuerungen.
Matthias Weinberg: Das ist eine super Frage. Das wird Step by Step gehen. Die Anlagen, durch die wir insbesondere den Hochofen, bei dem meisten CO2 entsteht, ersetzen wollen. Die sind viel, viel schlanker und viel viel höher. Es sieht eher aus wie in Chemieanlagen Park als wie ein klassischer Hochofen. Das, was wir hier vorhaben, ist natürlich mit einem möglichst überschaubaren Aufwand, den größten Effekt erzielen. Insbesondere der Hochofen hat aus chemischen Gründen extrem hohe CO2 Emissionen. Also haben wir hier versucht, einen Ansatz zu etablieren, bei dem möglichst nur der Hauptverursacher ersetzt wird. Und das einzige, was wir da ersetzen wollen, ist wirklich der Hochofen, also ein vergleichsweise kleiner, wenn auch komplexer und aufwendiger Punkt, den wir da ersetzen. Wenn ich ein Chirurg wäre, dann würde ich sagen, es ist ein minimalinvasiver Eingriff. Es wird also nur punktuell am Hochofen, kein normales Roheisen mehr hergestellt, sondern wir nennen es Elektroroheisen. Das kann man in die ganz normalen folgenden Verarbeitungsstufen schleusen, wie es heute auch der Fall ist.
Roswitha Becker: Und das ist etwas, was man meiner Meinung nach auch unter diesem Gesichtspunkt der Nachhaltigkeit durchaus betrachten muss. Dass wir hier nicht die Anlagen, die nun hocheffizient laufen, über viele Jahre an ihr Optimum herangeführt wurden. Dass wir die weiter nutzen können, mit der Technologie, die wir halt, wie der Matthias sagte, minimalinvasiv vorsetzen.
Antonie Bauer: Was ist denn jetzt der erste Schritt auf dem Weg zum Ziel?
Roswitha Becker: Ja, der Matthias hatte schon die minimalinvasiven ersten Prozessumbauten angegeben und ich glaube, es ist sehr wichtig, dass wir uns damit auf den Weg machen. Die CO2-Einsparung, die schon sehr deutlich ist, die möchten wir auf ein grünes Produkt bilanzieren, das man sagt. Das, was ich hier einspare. Das wird wirklich ganz speziellen, besonderen Produktlinien zur Verfügung gestellt.
Matthias Weinberg: Vielleicht kann man das noch ein bisschen verdeutlichen. Wenn wir 10% weniger CO2 imitieren, dann können wir auch 10% des Stahls als Emissionsreduziert verkaufen. Das ist für uns extrem wichtig, weil natürlich die Kosten für so eine Prozessumstellung extrem hoch sind. Und wir müssen die refinanzieren. Irgendwo muss das Geld herkommen, weil es wird sich wie gerade schon gesagt, niemand leisten können, ein komplettes Stahlwerk und die komplette Infrastruktur, einer so großen Hütte einfach platt zu walzen und alles neu zu bauen um ein emissionsfreien Produktionsweg zu haben. Das überlebt wirtschaftlich keiner, der hier in Europa Stahl herstellt. Da sind wir uns absolut sicher.
Antonie Bauer: Habt ihr denn auch mal ein paar Zahlen für mich, dass man davon ein bisschen fassen kann? Wie viel können wir einsparen?
Roswitha Becker: Also das erste großes Zwischenziel, was wir uns gesetzt haben, das ist, dass wir bis zum Jahr 2030, 30% unserer CO2-Emissionen einsparen möchten. Das heißt, wir werden dann schon drei Millionen Tonnen grünen Stahl verkaufen.
Antonie Bauer: Wäre es nicht eigentlich am klimaneutralsten, man würde einfach Stahl-Schrott nehmen? Diesen einschmelzen und wiederverwenden, ist ja super recyceln fähig.
Matthias Weinberg: Theoretisch wäre das natürlich möglich, praktisch gestaltet sich das schwierig. Wir haben über Hightech-Stähle hier geredet und Hightech-Stähle fordern eine aufs Millionstel exakt eingestellte Zusammensetzung. Und wenn ich versuche das mit Schrott hinzukriegen, dann weiß ich, was da alles stören könnte. Das heißt also eine High-End-Qualität ausschließlich aus Schrott zu machen. Das wird nicht klappen. Und wenn man dann ein bisschen niedrigere Ansprüche an die Qualität hat, dann ist Recycling eine tolle Sache und man kann damit auch viel CO2 sparen. Nur werden wir, um den Zufluss von frischem, sauberem Material. Um diesen Zufluss werden wir nicht herum.
Antonie Bauer: Ja, was haben wir heute gelernt? Stahl kann grün sein. Darüber haben wir heute einiges erfahren. Von zwei Menschen, die ganz nah dran sind, wenn es darum geht, dass genau das gelingt. Ich versuche mal die drei wichtigsten Punkte zusammenzufassen. Stahl wird seit Jahrhunderten mithilfe von Kohle hergestellt. Die Prozesse sind zwar immer effizienter geworden, aber trotzdem eng mit Kohlenstoff und dadurch auch mit CO2 verbunden. Für klimaneutralen Stahl braucht es deswegen einen ganzen Technologie-Wandel. Ein Paradigmenwechsel. Weg von der Kohle. Im Mittelpunkt wird zukünftig Wasserstoff stehen, der kann die Rolle von Kohle bei der Stahlhersteller übernehmen. Statt CO2 entsteht dann Wasser. Das ist ziemlich gut fürs Klima. Dafür braucht es aber zum Einen neue Anlagen und vor allem Wasserstoff in riesigen Mengen, der zudem auch noch klimaneutral hergestellt werden muss. Stand heute, ist klimaneutrale Wasserstoff sowas wie der Trüffel unter den Energieträgern. Super selten und schweineteuer. Hinzu kommt, dass auch die Investition in die Anlagen alles andere als billig sind. Es braucht also einen echten Kraftakt und Förderung durch die Politik, damit die Wende zur klimaneutralen Industrie gelingen kann. Ja, an der Stelle bleibt mir einfach nur noch zu sagen: Vielen lieben Dank für eure Zeit und für die informativen Antworten. Ich hoffe, es hat euch Spaß gemacht.
Matthias Weinberg und Roswitha Becker: Tschüss.
Antonie Bauer: Bevor wir uns verabschieden, wollen wir auch schon ein Ausblick auf die nächste Folge geben. Ein bisschen wird auch die was mit dem Thema Klima zu tun haben. Es geht nämlich um Mobilität, genauer gesagt um Elektromobilität. Denn auch dort spielt Stahl eine ganz wichtige Rolle. Ohne Stahl kein Elektromotor. Was genau Stahl im Elektroauto tut, das wollen wir uns genauer anschauen. Uns ist wichtig, eure Meinung zum Podcast und eure Fragen zum Thema Stahl zu hören. Daher schreibt uns gerne eine E-Mail an [email protected]. Lasst uns wissen, wie euch der Podcast gefällt oder welche Themen rund um Stahl wir zukünftig beleuchten sollen. Mehr Stahlwissen, Eindrücke und Storys gibt's übrigens auch auf unseren Social-Media-Kanälen und auf unserer Webseite. Die Links dazu findet ihr in den Shownotes. Das war die dritte Folge von gekocht, gewalzt, veredelt. Mein Name war und ist Antonia und ich freue mich, wenn wir uns bei der nächsten Folge wiederhören.
Tschüss.
Folge 2: Ausfahrt Inklusion – Wenn sich die Leistung wandelt
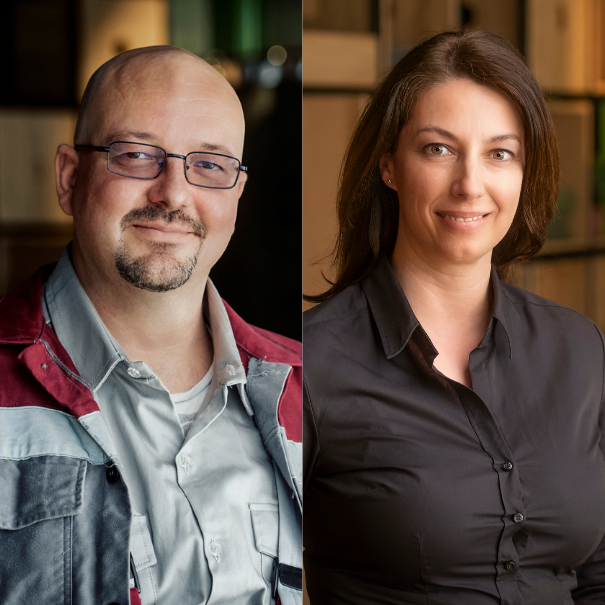
Eine Krankheit, ein Unfall, ein Schicksalsschlag – das Ende der Karriere? Nicht bei uns! Die zweite Podcast-Folge von "gekocht, gewalzt, veredelt" stellt genau das unter Beweis. Zu Gast ist Matthias Werner, der nach einer Krankheit seinem Job im Stahlwerk nicht mehr nachgehen könnte. Mithilfe unserer Inklusionswerkstatt arbeitet er weiterhin für thyssenkrupp Steel in genau den Bereichen, die ihm Spaß machen. Wieso wir das "Leistungswandlung" nennen und welche Rolle die Inklusion bei uns spielt, erklärt Vera Hillen ebenfalls in Folge 2. Als Leiterin der Inklusionswerkstatt weiß sie um die Tradition und Bedeutung des Themas für thyssenkrupp Steel. Eine sehr persönliche Folge, die die Menschen hinter dem Stahl in den Mittelpunkt rückt!
Toni: Ein Schicksalsschlag. Krankheit. Burnout. Jeder kennt jemanden, der nicht mehr so kann wie früher. Oder teilt vielleicht selbst dieses Schicksal. Ist das Leben dann vorbei und man ist kein Teil der Gesellschaft mehr? Absolut nicht. Was das Ganze mit Stahl zu tun hat und wie das Arbeitsleben aussehen kann, wenn man z.B. einen Unfall hatte oder eine schwere Krankheit, darum es in der heutigen Folge.
Schön, dass sie bei der zweiten Podcastfolge von „gekocht, gewalzt, veredelt“ zuhört. Mein Name ist Toni und ich moderiere die heutige Folge. Wir blicken auf ganz besondere Menschen: Mitarbeitende, die durch einen Unfall oder durch eine schwere Erkrankung, zu viel Stress oder wodurch auch immer einfach nicht in der Lage sind, ihren ursprünglichen Beruf auszuüben. Und bei thyssenkrupp bedeutet das nicht, dass diese Kolleginnen und Kollegen nicht mehr Teil der Stahl-Familie sind, sondern hier heißt das Leistungswandlung. Um diese leistungsgewandelten Mitarbeitenden soll es heute gehen. Und wir reden natürlich nicht über sie, sondern mit ihnen. Zum Beispiel mit Matthias. Der sitzt hier vor mir. Er kann uns am besten erzählen, wie man sich davon wieder erholt, wenn das eigene Leben auf den Kopf gestellt wird und gleichzeitig auf links gekrempelt wird und wie man den Mut wiederfindet, um weiterzumachen. Er ist schon 21 Jahre bei Steel und seit sieben Jahren nicht mehr in seinem eigentlichen Beruf tätig. Hi Matthias!
Matthias Werner: Hallo!
Toni: Schön, dass du hier bist. Außerdem spreche ich mit Vera, die bei Steel die Inklusionswerkstatt leitet und uns erzählt, wie wichtig es für Arbeitnehmer und Arbeitgeber ist, die Kolleginnen und Kollegen nicht fallenzulassen, sondern weiterhin zu beschäftigen. Hi Vera!
Vera Hillen: Hallo Toni!
Toni: So, wir fangen einfach mal mit einer kleinen Vorstellungsrunde an, damit unsere Zuhörer und Zuhörerinnen euch ein bisschen näher kennenlernen. Da würde ich gerne mit dir beginnen. Matthias Ich habe drei W-Fragen für dich mitgebracht, die uns so ein bisschen eingrooven. Wir beginnen mal damit, was du genau hier machst bei thyssenkrupp Steel.
Matthias: Ich bin jetzt seit sieben Jahren in der Inklusion tätig, bin seit drei Wochen jetzt auch der Kolonnenführer vom Stahlbau in der Halle Metall. Und wir machen Zuliefererarbeiten für die SGA, z.B. für die Stangengießanlage. Wir haben eigentlich sehr, sehr umfangreiche Arbeiten hier, die wir jeden Tag leisten müssen.
Toni: Und was genau bedeutet dieser Job für dich?
Matthias: Mittlerweile bedeutet der Job natürlich viel für mich. Wenn man länger krank ist und nicht so arbeiten kann, wie man das gewohnt ist, dann weiß man erst, wie wichtig Arbeit wirklich ist. Also anstatt nur zuhause herumzusitzen, sondern auch mal wirklich gesellschaftlich, wenn man das so ausdrücken kann, tätig ist.
Toni: ... und integriert ist. Warum bist du denn heute zum Thema Leistungswandlungen mein Gesprächspartner?
Matthias: Weil ich damals mit 21 an einer Nieren-Erkrankung erkrankt bin. Die wurde auch damals hier beim Betriebsarzt festgestellt. Glücklicherweise. Das heißt im Prinzip, dass mein eigener Körper meine Niere zerstört hat. Beide Nieren. Und im Laufe der Zeit fällt das der Niere immer schwerer, die Giftstoffe auszufiltern und daraufhin auch der Körper nachlässt. Im Prinzip heißt das: Irgendwann sind die Nieren nicht mehr da oder können die nicht mehr arbeiten. Und dass man dann durch die Dialyse künstlich am Leben erhalten wird.
Toni: Und woran hast du das gemerkt? Hast du’s überhaupt gemerkt am Anfang?
Matthias: Nee, ich habe es überhaupt nicht gemerkt. Und das war dann wie gesagt ein schleichender Prozess gewesen, bis sich der Körper dann bemerkbar gemacht hat. Und dann war es einfach nicht mehr möglich gewesen, im Betrieb zu arbeiten.
Toni: Wie ging das vor sich? Du hast die Diagnose bekommen und hast dann direkt Medikamente bekommen und kamst es direkt zur Dialyse oder wie lange muss man sich den Prozess vorstellen?
Matthias: Ja, genau. Die Niere regelt ja auch den Blutdruck. Und wenn die Niere ein bisschen geschädigt ist, geht der Blutdruck halt hoch. Und das geht natürlich aufs Herz. Also wurde ich sofort mit blutdrucksenkenden Mitteln versorgt, was dann auch schon eigentlich ausreichend war; ich dann einen Vorfall auf der Arbeit hatte, sodass ich am Kran war und damals was ganz Banales wie Banane gegessen hatte, mir damals nicht gesagt wurde, dass ich da so drauf aufpassen sollte und das dann auch so weit kam, dass ich dann einen Blutdruck von 240 hatte und ich dann sofort ins Krankenhaus musste. Und ja, das war schon lebensbedrohlich.
Toni: War das die ersten Situation in deinem alten Job und auch vielleicht ein bisschen klargeworden ist: So kann es nicht weitergehen?
Matthias: Ja genau. Also danach konnte ich dann auch nicht mehr zurückgehen, die Tätigkeit nicht machen, weil ich war ja vorher Springer gewesen. Das wurde natürlich immer weniger. Im Heißbetrieb, was Nox 2 ja nun mal ist, war das dann auch nicht mehr so möglich am Converter zu arbeiten, weil die Hitze dann auch wieder schädlich für die Nieren ist. Und ich dann verschiedene Arbeiten einfach nicht mehr ausführen konnte. Bis das dann soweit war, dass ich dahinter wirklich nur noch am Kran sein konnte und dann die Situation, die dann halt passiert ist. Und nachdem ich dann aus dem Krankenhaus kam und wieder zurück im Betrieb, wurde ich dann darauf hingewiesen oder mit mir besprochen, was man jetzt mit mir machen kann. Und dann kam halt auch die Inklusion im Gespräch.
Toni: Also dann ging es auch an die Umstellung von einem Job, den du gelernt hast zur Inklusionswerkstatt. Kannst du dich noch an den Tag erinnern, wo du quasi von deinem Unfall zurpckkamst und alles anders war?
Matthias: Ja, auf jeden Fall. Das war schon ziemlich hart, weil ich wie gesagt auch gern gearbeitet habe. Die ganzen Jungs auch sehr gemocht habe. Und das war schon ziemlich hart gewesen, dann zu hören, dass ich nicht mehr zurückkommen kann. Ja, da hatte ich auch dann zu knabbern gehabt.
Toni: Das glaub ich dir gerne. Und hattest du schon Vorstellungen von dem, was dich in der Inklusionswerkstatt erwartet?
Matthias: Ehrlich gesagt überhaupt nicht. Deswegen war das auch sehr beängstigend, dann die Inklusion zu wechseln.
Toni: Ja, weil du wahrscheinlich auch irgendwo eigene Vorbehalte hattest. Wann haben sich die aufgelöst?
Matthias: Aufgelöst hat sich das eigentlich schon ersten Gespräch mit Frau Meyer. Also das ist die Reha-Patin hier, der ich auch sehr sehr dankbar bin, weil menschlich und fachlich sie einfach großartig war. Und das war natürlich eine schwere Zeit für mich, sie mich auch aufgebaut hat, also nicht einfach nur wie eine Nummer behandelt hatte. Sie hat mir schon sehr geholfen, hier Fuß zu fassen.
Toni: Wer war denn alles in der Zeit so an deiner Seite? Wer hat dich vielleicht auch im Privaten unterstützt?
Matthias: Ich hatte das Glück gehabt, dass ich in der in der Zeit, wo ich im Krankenhaus war, dass meine jetzige Frau dann auch wieder in mein Leben getreten ist. Da bin ich sehr, sehr glücklich drüber.
Toni: Fels in der Brandung.
Matthias: Also sie hat mir das auf jeden Fall – meine Angst, die ich hatte – wesentlich einfacher gemacht.
Toni: Das klingt sehr schön, wenn man jemanden hat. Nicht nur auf der Arbeit, sondern eben auch privat.
Matthias: Ja, ich habe sehr viel Glück gehabt.
Toni: Du hast gerade erzählt, dass dein alter Job dir schon sehr wichtig war. Ist das jetzt mit deinem Neuen nach deiner Genesung? Inwieweit hat der neue Job vielleicht auch zu deiner Genesung beigetragen?
Matthias: Also die Bedeutung von meinem Job hab ich erst gelernt, ehrlicherweise, als ich kurz vor der Dialyse stand und auch 8 Monate nicht mehr arbeiten durfte. Da weiß man erst einmal, wie wichtig es ist, so einen geregelten Tagesablauf zu haben und mit einer Arbeit, die Spaß macht. Das war sehr hilfreich und nachdem ich dann einen Monat Dialyse gemacht hatte, durfte ich dann auch schon wieder arbeiten gehen. Und dann ist da erst einmal so ein bewusst, was das für jemanden bedeutet, wenn man dann auch wieder etwas Produktives machen darf. Und wertschöpfend arbeiten darf.
Toni: Ja, das glaube ich. Du sagst, du sprachst von Dialyse. Du bist dann auch noch durch die Reha gegangen. Inwiefern hat die Inklusionswerkstatt darauf auch reagiert? Inwiefern war das Teil deines Arbeitsalltags?
Matthias: Also die Inklusion hat mir das sehr geholfen. Dadurch, dass ich dreimal die Woche für circa fünf bis sechs Stunden in eine Dialyse musste, war das möglich gewesen, dass ich auch anderthalb Stunden vorher gehen konnte, damit ich auch den Termin einhalten kann. Das wurde mir auch angeboten. Ich habe ja gar nicht erst nachgefragt, das wurde mir einfach angeboten. Und das hat mir auch schon viel bedeutet, dass man dann auch richtig auf meine Bedürfnisse, die ich dann zu der Zeit hatte, auch eingeht.
Toni: Man hat ja auch dann ganz andere Dinge im Kopf als jetzt unbedingt die Arbeit. Man muss sich auf sich selbst konzentrieren, uns gesund werden. Was hat das für einen Einfluss auf dich, hier zu arbeiten, in der Inklusionswerkstarr?
Matthias: Mittlerweile hat das natürlich großen Einfluss auf mich. Mittlerweile konnte ich mich auch ein bisschen weiterentwickeln und bin jetzt sogar Kolonnenführer geworden und hoffe, in der nächsten Zeit dann auch die Vorreiterschule machen zu dürfen.
Toni: Das heißt, du hast hier richtig Perspektive, um dich weiterzuentwickeln und einfach neue Fähigkeiten vielleicht auch zu entdecken.
Matthias: Ganz genau.
Toni: Wie würdest du sagen, wie geht es dir jetzt?
Matthias: Also mir geht‘s im Moment sehr gut. Ich hatte das Glück gehabt, dass ich transplantiert werden konnte. Mein bester Freund hat mir seine Niere gegeben. Das ist natürlich unbeschreiblich und dadurch ist mir auch sehr viel Zeit geschenkt worden. Vor allen Dingen mit meiner Tochter und mit meiner Frau. Und durch die Transmutation gehts mir jetzt auch wieder so gut, dass ich auch wieder leistungsstärker werde. Man ist jetzt hier nicht leistungsgebunden, man macht so viel wie man kann, aber wenn dann auch mal schlechte Tage sind, ist das hier auch kein Problem und da reißt auch kein Einkommen ab.
Toni: Erst mal vielen Dank Matthias, dass du uns da so ehrlich und offen von erzählt hast. Vielen Dank dafür. Bevor wir mit Vera sprechen, der Leiterin der Inklusionswerkstatt, hören wir doch mal, was die Kolleginnen und Kollegen im Betrieb zum Thema Leistungswandlung sagen. Wir haben nämlich auf der Hütte nachgefragt.
Christian: Mein Name ist Christian Papitz, bin 35 Jahre alt, bin als Geräteführer tätig gewesen und ja, dann fing der Krankheitsverlauf halt an. Man weiß nicht, wie es weitergehen soll. Wo man bleibt und wie es weitergehen soll. Bin dann in der Inklusionswerkstatt gekommen. Ab Mai 2017. Für mich ist dann am Ende rausgekommen: Ich würde gerne ins Büro gehen. Uso ist es dann halt auch gekommen. Ja, man fühlt sich wieder wertgeschätzt sozusagen. War ein toller Moment auf jeden Fall. Dass man weiß, dass man irgendwo aufgefangen wird und nicht fallengelassen wird. Nein, ich denke mal, draußen in anderen Firmen wäre es nicht so gelaufen wie hier bei thyssenkrupp.
Toni: Okay, Vera, dann auch an dich nochmal schön, dass du hier bist. Und auch dir möchte ich die drei Vorstellungsfragen stellen, die W-Fragen, damit unsere ZuhörerInnen dich etwas besser kennenlernen können. Was genau machst du bei thyssenkrupp?
Vera: Meine Aufgabe hier ist die Leitung der Inklusionswerkstatt. Ich leite die Werkstatt in Duisburg. Ich habe noch einen Kollegen, der das in Dortmund macht. Zu der Inklusion gehören auch die allgemeinen Service-Betriebe. Die Werkstätten haben vor Ort Beschäftigung für leistungsgewandelte Mitarbeiter und die allgemeinen Service-Betriebe machen mehr so mobile Sachen wie Reinigungsarbeiten oder sowas. Und hier innerhalb der Werkstatt habe ich eigentlich drei Hauptaufgaben. Das ist einmal natürlich die Organisation. Dazu muss man wissen, dass wir innerhalb der Inklusion sechs verschiedene Gewerke haben. Dazu gehört unter anderem die Schreinerei, Schlosserei, aber auch eine Textilwerkstatt, eine Druckerei. Und wir betreuen auch den Bereich Sicherheitsgeräte, indem sämtliche Wartungsarbeiten für die Hütte gemacht werden. Also der wesentliche Auftrag der Inklusionswerkstatt hier ist, den Betrieben so viel wie möglich an Arbeiten abzunehmen oder ihnen zuzuarbeiten.
Toni: Wow, total vielfältig!
Vera: Genau, das ist der eine Teil. Dazu kommt dann noch das ganze Personalmanagement. Also welcher Kollege kann an welchem Ort bestmöglich eingesetzt werden? Ich habe 80 Mitarbeiter und da schauen wir natürlich, dass wir immer denjenigen da hinsetzen, der das gerne macht und auch gut. Ja und der dritte Punkt ist genau die Unterstützung des Reha Teams, das die Brücke darstellt. Wenn wir feststellen, ein Kollege ist im Betrieb nicht mehr einsetzbar, dann wird das Reha Team eingeschaltet und man versucht natürlich erst mal eine andere Beschäftigung im Betrieb zu finden. Und die Inklusionswerkstatt ist quasi erst dann wirklich spruchreif, wenn es keine andere Alternative gibt. Und damit die herausfinden können die Kollegen und auch der Mitarbeiter selbst was kann er eigentlich noch und was nicht. Dafür stellen wir hier auch die Möglichkeiten dar. Und dazu gibt es auch am Ende vom Reha Team eine Beurteilung. Und die wird den Betrieben und der Personalabteilung dann gezeigt. Und dann können Sie gucken: Mit den neuen Erkenntnissen haben wir vielleicht doch noch etwas im Betrieb. Und wenn das nicht klappt, dann haben wir hier in der Inklusionswerkstatt immer für jeden eine Lösung.
Toni: Du erzählst schon sehr enthusiastisch darüber, was du hier machst. Vielleicht daran angeschlossen die Frage, was der Job für dich bedeutet?
Vera: Ich habe angefangen in meinem Berufsleben im Krankenhaus zu arbeiten und hatte dort starken Fokus auf das Thema Menschen und Helfen. Und habe dann Arbeitspsychologie studiert und habe Veränderungsbegleitung in den Stahlwerken hier bei thyssenkrupp gemacht. Und tatsächlich ist das so: Die Arbeit hier verbindet beides. Ich habe die Arbeit mit den Menschen. Aber ich muss trotzdem dafür sorgen, dass es gut läuft, dass hier auch die Ruhe entsteht, die die Menschen brauchen. Trotzdem wollen wir wertschöpfend und produktiv arbeiten und das ist eine total spannende Herausforderung, dass beides immer miteinander zu vereinen. Deswegen macht es mir sehr viel Spaß.
Toni: Super! Ja, damit hat sich meine dritte Frage schon fast beantwortet, warum du heute meine Gesprächspartnerin bist. Also ich wüsste jetzt nicht, wer hier sonst sitzen sollte. Aber ja, vielleicht magst du es doch nochmal ganz kurz umreißen. Es gibt ja auch eine gewisse Historie in diesem Unternehmen. Was das Thema Leistungswandlung angeht, was weißt du dazu?
Vera: Ich selber bin ein Kind von Menschen aus dem Ruhrgebiet und das Ruhrgebiet ist geprägt von August Thyssen und Alfred Krupp, die hier den Stahl produziert haben schon viele Jahre. Und den beiden Firmengründern und auch die Firma Hoesch, die ja auch zu uns dann irgendwann gehörte, denen war es immer wichtig, eine soziale Sicherheit für all ihre Mitarbeiter und deren Familien sicherzustellen. Es war immer der Anspruch, einen starken sozialen Aspekt zu unterstützen und das wird weiterhin fortgeführt. Das finde ich auch eine extrem gute Haltung.
Toni: Du hast gerade von den verschiedenen Teilen der Inklusionswerkstatt deines Arbeitsbereiche gesprochen. Über wie viele Menschen reden wir denn da eigentlich? Über wie viele Mitarbeitende? Und kannst du sagen, aus welchen Altersschichten die kommen?
Vera: Insgesamt sind wir etwa 400 Mitarbeiter, die in der Inklusion Zwergstaat arbeiten, hier in Duisburg. In der Werkstatt sind es 80. Leistungsgewandelt hüttenweit sind es aber durchaus 10 % der Belegschaft, also etwa 2500 Mitarbeiter, die leistungsgewandelte Arbeitsplätze einnehmen.
Toni: Das liegt ja wahrscheinlich auch daran, dass die Mitarbeitenden hier ne recht lange Karriere bei thyssenkrupp haben, teilweise über Jahre und Jahrzehnte hier arbeiten und dann auch durch verschiedene Lebensphasen gehen. Welche Gründe gibt es noch, dass Mitarbeitende zu leistungsgewandelten werden?
Vera: Leistungswandlung betrifft also jeden und das zum einen übers Alter. Und hier in der Stahlwerken, wir haben Wechselschicht, wir haben zum Teil harte körperliche Arbeit, da ist das Thema Mobilität ein Faktor. Und dann haben wir noch, wie bei Matthias, die eine Erkrankung hinnehmen müssen. Das kann einen jederzeit in jedem Alter treffen. Wir haben auch einen großen Teil an psychischen Erkrankungen, weil das Thema Wechselschicht halt gravierend ist.
Toni: Aber auch für mich jetzt nochmal: Eine Wechselschicht, das scheint mir echt ein Megathema zu sein. Also könnt ihr auch gerne beide zu antworten, was das so stressig macht.
Matthias: Stressig macht das einfach, dass man keinen vernünftigen Schlafrhythmus hat. Also ist man auch übermüdet. Also so war das bei mir z.B. die Frühschicht war für mich immer sehr, sehr schwer gewesen. Das hat schon immer gedauert, auch die Umstellung dann hierhin zur Frühschicht hat auch eine lange Zeit gedauert, bis ich mich dann wirklich dran gewöhnt habe. Und ich hab nur zehn Jahre gemacht. Manche Leute machen das ja wirklich schon 40, 45 Jahre.
Vera: Wechselschicht hat Einfluss auf das Herz-Kreislauf-System in jedem Fall. Und je nachdem, wie gut man da organisiert ist, belastet das den Körper auf Dauer.
Toni: Ja, jetzt kommen wir nochmal so ein bisschen zurück. Wenn jemand merkt, auf der Arbeit irgendwie, es läuft irgendwie nicht mehr oder es ist wirklich ein einschneidender Moment im Leben. Wie läuft das dann? Rufe ich dich dann an, Vera, und du hilfst mir dann oder wie geht das dann vonstatten?
Vera: Also sobald ein Mitarbeiter quasi erkrankt und eine sogenannte Leistungswandlung vorliegt, ruft das Personal einen runden Tisch ein und schaut erst mal mit dem Betrieb: Können wir ihnen in einer anderen Aufgabe einsetzen, vor Ort? Das ist dann immer so der erste Punkt. Wenn man merkt, das wird schwierig. Kommt das Reha Team dazu und dann überlegt man: Kann man in einen anderen Betrieb wechseln, oder – und dann kommt halt eben der dritte Punkt – doch in die Inklusionserkstatt? Oder können wir noch gar nicht sagen, wo es hingeht und wir nehmen mal so eine systematische Arbeitserprobung zu Hilfe und schauen nochmal an was kann der Mitarbeiter alles, wovon wir noch gar nicht wissen, dass er es vielleicht sogar kann? Und wenn das Zeugnis oder die Beurteilung nach zwölf Wochen besagt, er kann aber noch das und das und Tätigkeiten am Rechner oder Übererwachungstätigkeiten machen, dann kommt er quasi auf so eine Art Vermittlungsposition und dann wird er möglichst wieder in den Betrieb zurückgegeben. Es gibt aber auch Fälle, da ist das an keiner Stelle möglich. Insbesondere bei psychischen Erkrankungen ist öfter eine zeitintensive Betreuung der Führungskräfte erforderlich. Das können die Kollegen in den Betrieben aber nicht leisten. Das ist dann oft ein Grund, warum die Kollegen hier bleiben. Weil hier haben wir die Möglichkeit, uns Zeit zu nehmen. Wir haben auch sonderpädagogisch ausgebildete Führungskräfte, die Meister sind das. Meine Kollegen und ich sind das. Und da kann man dem Menschen besser gerecht werden. Es wird vorher wirklich erstmal alles andere versucht. Tatsächlich haben wir ja auch nur ein begrenztes Kontingent an Plätzen und ich kann sagen, auch wenn man das erstmal nicht so denkt. Es ist heiß begehrt hier.
Toni: Das hört sich alles sehr individuell auf den Menschen abgestimmt an geht das denn überhaupt, dass man dafür vorgefertigte Prozesse entwickelt oder bestimmte Schritte einhält? Wie machst du das?
Vera: Doch das mit den Prozessen, das geht gut, das muss man auch so machen. Es hängen da ja auch noch Themen dran, wie eine Rentenversicherung, wie eine Krankenversicherung. Also auch die müssen ihre Prozesse haben und ihre Rückmeldungen haben und Einschätzungen. Der Betriebsarzt ist dabei, auch der Betriebsrat. Bei all den Gesprächen ist der Mensch, den es betrifft, ist immer dabei. Also um den dreht es sich auch. Es gibt quasi Rahmen, Prozesse, aber die Fälle sind sehr individuell. Das stimmt.
Toni: ja. Aber höchste Transparenz, so wie ich das wahrnehme und auch zukunftsweisend irgendwo, was den Begriff Leistungswandlung ja auch dann nochmal prägt. Ja, auch eine Frage, die sich vielleicht auch Zuhörer und Zuhörerinnen stellen: Warum so viel Aufwand? Warum nimmt man sich die Zeit in der Werkstatt für die Mitarbeiter?
Vera: Ja, da würde ich erst einmal die Frage stellen: Was ist eigentlich eine angemessene Personalpolitik? Und genau das ist es. Es ist zeitgemäß. Dazu kommt, dass das auch ein Erbe unserer Unternehmensgründer ist, dass wir diese soziale Verantwortung sehr ernst nehmen und dass ein Mitarbeiter von Anfang bis Ende seiner Arbeitszeit 100 % einsatzfähig ist, passiert ja nirgendwo. Also deswegen man muss da vernünftig mit umgehen. Und ich finde, das machen wir hier sehr gut. Wir machen das sogar so gut, dass wir wertschöpfend auch leistungsgewandelte Mitarbeiter einsetzen können, wo wir unsere Betriebe unterstützen mit Dingen, die wir sonst fremd vergeben müssten.
Toni: Ja, das heißt, es bleibt viel mehr im Haus und ich kann mir vorstellen, dass das auch eine große Motivation ist für Mitarbeitenden, wenn sie wissen: Im Zweifelsfall bin ich damit nicht alleine.
Matthias: Ja, das war natürlich damals, als ich krank wurde, natürlich Existenzängste, weil ich ja wusste, was auf mich zukommt und ich das damals auch noch nicht wusste mit der Inklusion und dass ich so aufgefangen werde in der Zeit. Ich war viel krank gewesen, musste natürlich auch über langen Zeitraum krankgeschrieben werden und das wäre beim Kleinunternehmen überhaupt nicht gegangen. Und die Angst wurde mir dann aber auch genommen. Das war damals schon sehr wichtig gewesen.
Toni: Ja, kann ich mir gut vorstellen. Und motivierte Mitarbeiter sind die besseren Mitarbeiter. Du hattest auch nochmal das Stichwort Wertschöpfung gerade genannt. Wie wichtig ist das für dich als Mitarbeitenden, Matthias, dass du eine wertschöpfende Tätigkeit hast und nicht beschäftigt wirst?
Matthias: Das ist immer wichtig; Arbeit arbeiten zu machen, die auch produktiv ist und nicht einfach nur eine Beschäftigung ist. Wenn ich weiß, dass das z.B. jetzt die Arbeit die ich zurzeit macht, auch wirklich dann ins Stahlwerk zurückgehe, wo ich mal gearbeitet habe, ist das schon interessant und auch wichtig, dann auch wirklich Arbeiten zu machen, die dann auch wieder im Betrieb ankommen und verarbeitet werden.
Toni: Ja, und du sagtest auch, dass dir das auch während deiner Krankheit erst mal bewusst geworden ist, wie wichtig das eigentlich ist. Vera, vielleicht auch nochmal das Wort an dich, inwieweit Wertschöpfung und Inklusion zusammenbringt. Kannst du dich noch an andere Mitarbeitenden erinnern, die vielleicht einen ähnlichen Prozess durchgemacht haben und für die es auch sehr wichtig war, eben über die Inklusionswerkstatt etwas Wertschöpfendes zu tun und dafür auch Wertschätzung zu erhalten?
Vera: Es ist ja erst erstmal so, wenn man aus einem Betrieb kommt und das nicht mehr machen kann, was man eigentlich mal gelernt hat, dann könnte es sein, dass man sich ein bisschen weniger wert fühlt. Und das ist ein Thema, was wir hier aufgreifen und was wir sofort beheben können. Indem die Menschen verschiedene Gewerke ausprobieren und dabei dann auch feststellen, dass sie neben dem eigentlichen Beruf, den sie gelernt haben, auch noch ganz andere Dinge können. Also es gab dann mal den Elektriker, der eine Tasche genäht hat und auf einmal gemerkt hat: Wow, das macht mir unheimlich viel Spaß und da auch Kreativität entwickeln konnte. Und das ist das, was die Menschen zufrieden macht. Und wenn wir Menschen haben, die zufrieden sind bei der Arbeit, sind die auch zufrieden in der Gesellschaft. Und so wirkt sich das dann halt auf alle aus.
Toni: Inwieweit trifft das auf dich zu, Matthias? Hast du auch vielleicht was Neues an dir entdeckt, seitdem du hier bist?
Matthias: Ja, ja, tatsächlich schon. Ich durfte das Lager von steelworks aufbauen, also komplett neu aufbauen mit System und ausdenken, wie man das alles organisieren kann. Und dann noch august und alfred, die Label-Marke von thyssen; da durfte ich dann auch das Lager aufbauen, wahrscheinlich weil ich das so gut gemacht habe, da durfte ich dann gleich weitermachen. Also da hab ich auch nicht mit gerechnet, dass ich so was kann. Oder dass ich auch mal da rankommen an sowas, dass ich mal die Möglichkeit hab, auch außerhalb meiner Arbeitstätigkeit etwas zu erschaffen.
Toni: Naja, klingt nach einer totalen Horizonterweiterung. War das auch schon mal so, dass ihr bei Leistungsgewandelten dann Talente entdeckt habt und gesagt habt: Hey, daraus kann schon mal was machen? Ich weiß nicht, wie august und alfred z.B. entstanden ist, aber ich kann mir vorstellen, dass jemand dann mit einem Talent vorangegangen ist und das aufgegriffen habt. Wie läuft das dann?
Vera: Also die Mitarbeiter haben dann Ideen und machen dann, weil sie das ja auch dürfen, einfach mal ein Probestück und zeigen das dann. Daraus erwuchs zumindest august und alfred dann: Okay, können wir das nicht sogar irgendwie mit einem anderen nützlichen Thema verbinden? Da hatten wir die alten Schmelzermäntel, die lagen da rum. Die durften ihre eigentliche Funktion nicht mehr wahrnehmen, die waren defekt zum Teil. Dann haben wir überlegt: Was können wir damit machen? Und dann kam die Idee, dass uns daraus doch mal eine Tasche nähen oder eine Grill-Schürze. Und das haben die Mitarbeiter dann ausprobiert. Und daraus ist dann tatsächlich so ein Upcycling-Projekt entstanden. Und das ist ein Beispiel dafür. Und ich habe hier ein Beispiel von einem Mitarbeiter erlebt. Der hatte vor drei Wochen seinen allerletzten Arbeitstag. Er ist 51 Jahre hier auf der Hütte gewesen und hat die letzten drei Jahre hier bei uns Fahr-Tätigkeiten übernommen und ein bisschen den Service. Und der geht mit einem guten Gefühl in die Rente und das ist der Vorteil der Inklusionswerkstatt. Man hat vielleicht auch einen etwas sanfteren Ausstieg aus dem Arbeitsleben.
Toni: Ja, Matthias, ich glaube, du hast ja noch ein paar Jahre. Aber was wünscht du dir vielleicht auch für die nähere Zukunft, die du hier noch Inklusionswerkstatt verbringst?
Matthias: Ja, ich hoffe, dass ich bei thyssen noch in Rente gehen kann. Das wäre schon mal ein sehr, sehr großer Wunsch von mir. Dann hätte ich ja schon einige Jahre auf dem Buckel.
Toni: Du wirst ja dann in deiner Zeit ja auch noch weitere Mitarbeitende erleben, die hier neu ankommen. Und was kannst du aus deiner persönlichen Erfahrungen diesen Mitarbeitenden mitgeben? Oder vielleicht auch schon mal für Ängste nehmen?
Matthias: Also die Ängste, die ich auf jeden Fall schon mal nehmen kann, ist, wenn man krank wird, dass man hier fallengelassen wird. Und das ist nun mal so, dass man durch die Inklusion oder aber auch durch die Reha, durch das Reha Team, auch aufgefangen wird und auch andere Möglichkeiten aufgezeigt werden, die ja nicht unbedingt schlechter sein müssen als das, was man jetzt macht. Genau das ist die wichtigste Botschaft, dass man hier wirklich nicht fallen gelassen wird und dass man Rückhalt spürt, auch wenn man dann denkt, es geht nicht mehr weiter. Weiter geht‘s immer.
Toni: Das ist eine gute Botschaft!
Vera: Ich bin stolz, dass es, dass wir das im Unternehmen haben. Und ich weiß, dass wir hier das Fangnetz darstellen. Also da geht uns keiner durch die Lappen, der es nicht will.
Toni: Keiner geht uns durch die Lappen. Wenn das mal keine schönen Schlussworte für unser zweites Folgen sind. Ja, zusammenhalten war und ist nicht nur das Motto der Corona Pandemie augenscheinlich, sondern grundsätzlich auch beim Stahl. Das hat diese Folge erst mal richtig gezeigt. Drei Statements, die mir jetzt so im Kopf geblieben sind, sind einmal, dass bei thyssenkrupp Mitarbeitende, die durch Unfall, Krankheit oder andere Ursachen ihren ursprünglichen Job nicht mehr machen können, Leistungsgewandelte sind. Dieser positive Begriff unterstreicht, dass ich zwar die Art der Arbeit ändert, aber eben nicht ihr Wert. Das kann man ich so mal festhalten. Und zweitens: Inklusion und Verantwortung haben in der Stahlindustrie eine lange Tradition; vom Aufbau der Sozialversicherungen über den Bau diverser Wohnviertel für die Mitarbeitenden schon im 19. Jahrhundert. Und auch der Bau des Alfred Krupp Krankenhauses ist eine Tradition, die wir gerne weiterführen wollen. Und ja, was irgendwo auch der Purpose von der Inklusionswerkstatt ist. Und zuletzt: Inklusion nützt den Mitarbeitenden und natürlich auch dem Unternehmen. Also wer sich weiterhin einbringen kann, bleibt motiviert und leistet einen Beitrag zur Wertschöpfung. Und das ist ja wohl mal die Win-Win-Situation schlechthin. Letztendlich weiß ja niemand, was das Schicksal für ihn oder sie bereithält. Und jeder von uns könnte jederzeit in Matthias Situation geraten – und dann jemanden zu haben wie Vera und ihr Inklusionsteam, die einem die Hand reichen und beim Aufstehen helfen, ist ja die halbe Miete. Beim Stahl halten wir zusammen und machen zusammen weiter.
In der nächsten Folge wird es umweltfreundlich. Da dürft ihr schon mal gespannt sein. Es geht nämlich um die Transformation der Stahlherstellung hin zu grünem Stahl.
Liebe Zuhörer und Zuhörerinnen, wie immer gilt: Der Podcast lebt von eurem Feedback. Uns ist wichtig, eure Meinung zum Podcast und eure Fragen zum Thema Stahl zu hören. Daher schreibt uns gerne eine E-Mail an [email protected]. Denn die ersten Themenwünsche wurden uns bereits geschickt und werden auch schon eingeplant. Also seid gespannt auf die nächste Folge. Übrigens: Mehr Stahl-Wissen, -Eindrücke und -Storys gibt's natürlich auch auf unseren Social-Media-Kanälen und auf unserer Webseite. Die Links dazu findet ihr in den Shownotes. Das war die zweite Folge von „gekocht, gewalzt, veredelt“, durch die ich, Toni, euch führen durfte. Mir hat es Spaß gemacht. Ich hoffe euch auch und dass wir uns beim nächsten Mal wieder hören. Bis bald und tschüss!
Matthias: Tschüss – und bleibt gesund!
Vera: Tschüss. Bleibt gesund!
Folge 1: Stahl – Altes Eisen oder Zukunft?
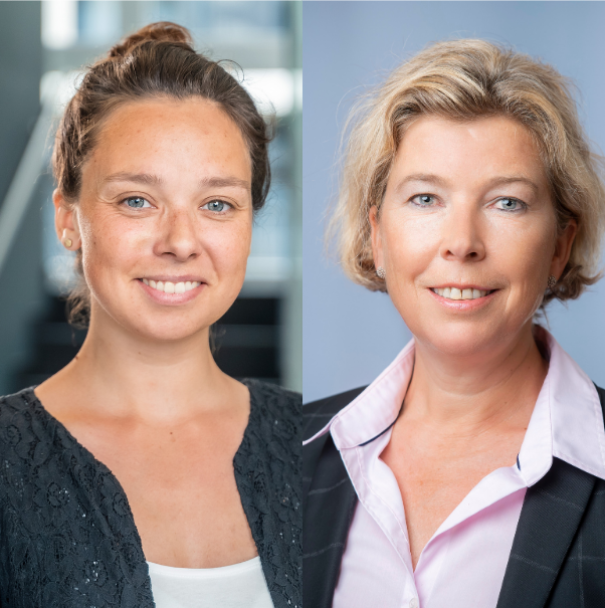
Brauchen wir Stahl überhaupt noch? Dieser Frage geht unsere Moderatorin Toni in der ersten Podcast-Folge von „gekocht, gewalzt, veredelt“ nach. Dabei greift sie auf die geballte Expertise von Heike Denecke-Arnold zurück. Sie ist CEO sowie CTO der thyssenkrupp Hohenlimburg GmbH und seit Jahrzehnten in der Stahlindustrie tätig. Wer noch ein paar überzeugende Zahlen für den nächsten Smalltalk baucht oder lebensnahe Beispiele für die Vielfältigkeit von Stahl, sollte einschalten!
Folge 1 in Schriftform
Antonie Bauer: Stahl ist alt. Ein Werkstoff, den es schon seit Jahrtausenden gibt. Deshalb könnte man auch sagen: Es ist ein ziemlich altes Eisen. Aber ob es deshalb auch Geschichte ist? Ich glaube nicht. Und das werden wir auch in dieser Folge heute zeigen. Herzlich willkommen zur allerersten Folge vom Podcast „gekocht, gewalzt, veredelt: Der Stahl-Podcast“, indem er uns mit dem Werkstoff Stahl auseinandersetzen und mit allem, was da so zugehört. Mein Name ist Antonie und ich führe euch durch die heutige Folge.
In dieser ersten Folge blicken wir zurück, weit zurück. Aber wir blicken auch nach vorn, schauen auf die Anfänge der Produktion von Stahl und auf seine Entwicklung. Und außerdem blicken wir in die Zukunft und was noch drinsteckt in diesem vermeintlichen „Methusalem-Werkstoff“. Denn Stahl, so viel kann ich euch schon mal verraten, ist alles mögliche, aber bestimmt kein altes Eisen. Und um uns Stahl zu nähern, zu erklären, was Stahl ist und war und wieso jeder Einzelne von uns jährlich im Schnitt fast achtmal so viel Stahl braucht wie Kartoffeln, spreche ich mit Heike Denecke-Arnold. Hallo Heike!
Heike Denecke-Arnold: Hallo Toni!
Antonie Bauer: Wenn jemand Stahl-Expertise hat, dann du. Denn du steckst mittendrin in der Stahl-Wirtschaft. Du bist CEO und CTO bei der thyssenkrupp Hohenlimburg GmbH, also der Business Unit Precision Steel. Bevor wir dazu kommen, was genau dein Tagesgeschäft ist, würde ich dir direkt gerne die Frage aller Fragen stellen: Inwiefern fasziniert dich der Werkstoff Stahl? Was ist daran so besonders für dich?
Heike Denecke-Arnold: Am Werkstoff Stahl fasziniert mich am allermeisten, dass er so irre vielfältig ist. Er kann uns beschützen. Ich kann schöne Dinge mit ihm darstellen. Nützliche Dinge. Er hilft mir dabei, mich fortzubewegen. Ich finde ihn in meinem täglichen Umfeld. Und das Faszinierende daran ist, je nachdem, wie ich ihn herstelle, also welches „Kochrezept“ ich wähle, kommen am Ende ganz unterschiedliche Dinge dabei raus, die auf der einen Seite groß und stark sind und auf der anderen Seite vielleicht auch ganz dünn und ganz filigran.
Antonie Bauer: Also überall wo du hinschaust, siehst du irgendwo Teil deiner täglichen Arbeit. Ja, was genau ist denn deine Arbeit? Was machst du so den ganzen Tag?
Heike Denecke-Arnold: Du hast ja eben gesagt, wo ich arbeite. Und ich bin dort in der Geschäftsführung tätig und in der Rolle verantwortlich für die Produktion, den Vertrieb und die Qualität. Und das heißt, wir stellen ein warmgewalztes Produkt her. Das wird veredelt, weiterverarbeitet und am Ende des Tages soll es natürlich auch verkauft werden. Das heißt, es gibt dort eine Vertriebsmannschaft, die das Produkt dann an die Kunden verkauft und verhandelt. Und damit sie das möglichst gut machen können, brauchen wir natürlich auch eine ausgezeichnete Qualität. Das heißt, da gibt's dann auch Bereiche, die kümmern sich darum, dass das, was wir herstellen, auch qualitativ in Ordnung ist.
Antonie Bauer: Heike Ich habe in der Vorbereitung eine Zahl gelesen, die mich ehrlich gesagt ein bisschen umgehauen hat. 420 Kilo Stahl verbrauchen wir in Deutschland pro Kopf pro Jahr. Um das mal in Relation zu setzen: Das ist mehr, als wir an Obst, Gemüse und Fleisch zusammen pro Kopf zu uns nehmen. Und im Gegensatz dazu kann man Stahl zwar nicht essen, aber was meinst du, woher kommt dieser Hunger auf diesen Werkstoff?
Heike Denecke-Arnold: Ich glaube, der Hunger kommt daher, dass ich ihn genauso brauche, wie ich täglich meine Nahrung brauche und meine Getränke brauche. Es geht morgens schon damit los auf dem Weg zum Kühlschrank. Der Kühlschrank ist schon aus Stahl hergestellt. Für die, die sich dann vielleicht in ein Auto reinsetzen, sie bewegen sich in etwas, was aus Stahl hergestellt wurde. Oder die, die vielleicht öffentlichen Verkehr nutzen; Verkehrsmittel, die Schienen. Ich fahre jeden Tag über Brücken rüber, die aus Stahl gefertigt sind. Oder aber in der Mittagspause; Ich habe vielleicht Durst und nehme eine Getränkedose, dann ist die auch ganz oft aus Stahl gefertigt. Wir haben alle vielfältigste Dinge in unserem Leben, die wir als selbstverständlich wahrnehmen, einfach brauchen und Sachen, die wir sehen, die wir nutzen. Aber ich glaube wir machen uns nie bewusst Gedanken drüber, woraus sie eigentlich gefertigt sind.
Antonie Bauer: Wissen deine Freunde oder deine Familie, wo Stahl überall drinsteckt? Redet ihr im Freundeskreis auch oft darüber, was Stahl so kann und macht, so wie wir jetzt hier darüber reden? Wie erklärst du in deinem Freundeskreis, was Stahl kann und wozu er fähig ist?
Heike Denecke-Arnold: An ähnlichen Beispielen. Wir diskutieren viel darüber, vielleicht fast eher noch in der Familie, weil meine Brüder in ganz anderen Branchen tätig sind, als ich es bin und ich immer wieder versuche zu erklären, was ich eigentlich mache. Das kommt oft auch daher, dass die Stahlindustrie irgendwie den Ruf hat, dreckig zu sein und alt zu sein oder auch gar nicht mehr zu existieren in Deutschland. Was ja überhaupt nicht stimmt, wenn man hier aus dem Fenster schaut. Man sieht es ja leibhaftig. Sie ist da, sie ist real. Stahl ist nach wie vor präsent in Deutschland und auch in der Welt. Und ich versuche immer an praktischen Beispielen zu zeigen, wo es jeder nutzt. Es gibt vor allem in Autos beispielsweise so viele Komponenten, die funktionieren müssen, die uns schützen sollen, wenn man mal einen Unfall baut, die die Energie des Unfalls aufnehmen.
Antonie Bauer: Ist denn Stahl als Werkstoff, der uns an so vielen Ecken und Enden begegnet, dann irgendwie auch in einer gewissen Weise alternativlos?
Heike Denecke-Arnold: Völlig alternativlos ist er nicht. Das ist immer ein Abwägen, was ich damit machen möchte. Stahl halt den großen Vorteil, dass er sehr leicht zu verarbeiten ist. Ich kann ihn formen. Ich kann ihn fügen. Ich kann ihn schweißen. Und er ist zu 100 Prozent recyclingfähig. Das ist natürlich auch ein ganz großer Vorteil, dass er irgendwann wieder, wenn er mal alt und ausgedehnt ist, als Schrott weiter nutzen kann und wieder verarbeiten kann.
Antonie Bauer: Jetzt kommen wir mal so ein bisschen weg vom Werkstoff Stahl an sich und gehen mehr in die Produktion. Also alleine hier am Standort Duisburg, wo wir aufnehmen: Da fährt man erst einmal an 100 Metern Werk vorbei. Oder auch wenn ich von der Autobahn abbiege, dann sehe ich ja schon von weitem die Hochöfen und eine ganz eigene Atmosphäre, die dadurch entsteht, dass das hier so große Dimensionen hat. Hast du da vielleicht noch ein paar mehr Zahlen für unsere Zuhörer und Zuhörerinnen, die vielleicht noch nicht an so einem Standort waren, die sich das vielleicht noch nicht so vorstellen können?
Heike Denecke-Arnold: Ich glaube, beim Besten kann man es festmachen an der Fläche des Standortes hier, dass das allein 10 Quadratkilometer sind. Ein Schienennetz, was nur im Werk alleine, also nicht außen rum, fast 500 Kilometer lang ist. Ich glaube, da bekommt man ein Gefühl für die Dimensionen. In der ganzen Einheit Steel arbeiten rund 27.000 Mitarbeiter. Das zeigt einfach auch nochmal, was für eine Bedeutung die Stahlindustrie auch als Arbeitgeber hat. Es sind unglaublich viele Menschen in dieser Industrie beschäftigt. Und sie werden auch gebraucht für den ganzen Prozesse. Produktionsanlagen brauchen Menschen, die die Anlagen betreiben und bedienen. Ich brauche viele Kaufleute, sei es im Vertrieb oder im Rechnungswesen oder im Controlling. Und das ergibt sich allein aus der schieren Größe der Anlagen, dass man auch so viele Mitarbeiter braucht.
Antonie Bauer: Dann vielleicht nochmal ganz genau die Frage Woher kommen diese riesigen Dimensionen bei der Stahlproduktion?
Heike Denecke-Arnold: Man muss sich überlegen, das allein nur hier bei thyssenkrupp Steel pro Jahr zehn Millionen Tonnen Stahl produziert werden. Zehn Millionen Tonnen. Das sind gigantische Mengen. Und das ist ja am Beispiel Kartoffeln festgemacht. Man braucht Stahl, es ist fast ein Massenprodukt. Wir brauchen ihn für die zahlreichen Dinge, wo Stahl Verwendung findet, und das ist dann auch logisch, dass ich entsprechend große Aggregate brauche, um diese gigantischen Tonnage dann noch herstellen zu können.
Antonie Bauer: Die Produktion ist – zumindest denkt man das, wenn man es hört – schmutzig, laut, heiß, staubig. Also ist nicht schön oder kein angenehmer Ort. Aber wer schon mal ein Stahlwerk besucht hat, der weiß da ist noch mehr. Also gleichzeitig kann Stahl ja auch sehr modern und sehr clean sein. Wie passt das für dich zusammen? Wie passt Stahl vielleicht auch mit neuen Technologien zusammen für dich.
Heike Denecke-Arnold: Ich glaube, das beste Beispiel ist im Moment die Elektromobilität. Das geht mit Stahl gut. Ich kann Leichtbau-Konzepte begleiten, die dann aber trotzdem möglich machen, dass es auch wirtschaftlich bleibt, weil am Ende des Tages steht immer ein Kunde, der auch bereit ist, nur einen gewissen Preis zu zahlen. Ein ganz tolles Beispiel, wie Stahl einfach auch für die Zukunft wirklich nützlich sein kann und uns auch hilft, Ressourcen zu schonen. Weg von der Kohle, hin zu alternativen Energien.
Antonie Bauer: Da bist du dann mittendrin beim Weiterforschen, Ausprobieren. Und das passt perfekt zu meiner nächsten Frage. Weil wir jetzt auch den Terminus Klimawandel schon öfter hatten. Vielleicht kannst du ja nochmal ganz genau sagen, wie Stahl einen Teil der Lösung sein kann; mit Blick auf den Klimawandel für die Probleme, die wir gerade schon haben.
Heike Denecke-Arnold: Da gibt's zwei Wege oder Möglichkeiten, die beide genutzt werden. Das eine ist, dass ich Produkte entwickle, die ich jetzt brauche für diesen Trend, der sich da draußen im Markt abzeichnet. Und das andere ist, dass man sich sehr intensiv Gedanken darüber macht: Wie kann ich bei der Stahlhersteller von der Kohle zu Wasserstoff kommen? Das heutige Verfahren ist so, dass das viel Kohle eingesetzt wird. Ich brauche sie einfach, um das Eisenerz zu reduzieren. Was heißt, das Eisen kommt in der Natur nicht als reines Eisen vor, sondern immer ein oxidischer Form. Und die Kohle brauche ich, um dem Eisenerz sozusagen den Sauerstoff zu klauen. Das funktioniert mit dem Wasserstoff genauso wie mit der Kohle. Ich brauche also irgendwas, was dem Eisen den Sauerstoff klaut. Und das wird jetzt hier an dem Standort ganz massiv vorangetrieben; es werden industrielle Konzepte entwickelt. Das heißt letztendlich auch, dass es zum kompletten Umbau der der Stahlindustrie kommt. Also das ist wirklich fast wie eine industrielle Revolution, was da stattfindet. Ich meine, diese Aggregate, die da draußen stehen, gibt es seit vielen, vielen Jahren. Und jetzt gehe ich sozusagen an das Herzstück dran und baue es einmal komplett um.
Antonie Bauer: Ich versuche mir vorzustellen, wie das aussieht, wenn sich hier einiges tut oder umgebaut wird. Vielleicht hast du da nochmal ein genaueres Bild als ich jetzt.
Heike Denecke-Arnold: Ich glaube, es wird gar nicht so viel anders aussehen. Von den Fertigungsabläufen her, was sich massiv verändern wird, ist die Art und Weise, wie ich den Rohstahl, also das anfängliche Produkt, herstellen werde. Das wird sich gravierend verändern. Vorausgesetzt auch, wir bekommen die entsprechende Unterstützung aus der Politik. Die technischen Ideen sind da. Es ist auch möglich, das zu tun, aber es kostet unglaublich viel Geld und das kann keiner alleine stemmen. Und da sind wir dann auch auf die Unterstützung der Politik angewiesen, dass man diesen Weg weiter oder gemeinsam geht. Vielleicht auch mal als ein Beispiel: Wenn ich das tun wollte, hier die die komplette Produktion auf eine Produktion mit Wasserstoff umzustellen, brauche ich 720.000 Tonnen Wasserstoff. Und wer das Gasometer in Oberhausen kennt: Es ist 23.000 Mal dieses Gasometer allein vom Volumen her. Und das zeigt einfach, wie gigantisch dieser Veränderungsprozess werden wird.
Antonie Bauer: Ja, so wie wir angefangen haben, hören wir jetzt auch wieder auf mit beeindruckenden Zahlen, mit großen Dimensionen. Vielen lieben Dank, Heike, dass du uns diese Einblicke heute mitgebracht hast. Und ich würde jetzt unser Gespräch gerne einmal auf drei Erkenntnisse nochmal konzentrieren.
Damals wie heute Stahl war und ist essentiell für unsere Wirtschaft und ist auch irgendwie überall drin. Sowohl in den Kleinen als auch in den großen Dingen. Das ist Punkt 1.
Punkt 2: Stahl ist moderne Technologie. Die Hütte mag alt sein, aber sie ist noch lange kein Relikt und sie kann ein Ort der Zukunft werden. Denn auch die Stahlproduktion entwickelt sich ständig weiter und Stahl erfindet sich praktisch immer wieder neu.
Ja und was den Klimawandel angeht, das ist Punkt 3: Klimaneutrale Stahlproduktion kann und soll auch Realität werden. Und in neuen Technologien steckt Stahl auch jetzt schon drin, wie z.B. der Elektromobilität.
Bevor wir uns verabschieden, hab ich hier schon mal einen Ausblick auf die nächste Folge: Stahl ist hart, aber Stahlkocher sind noch härter im Nehmen und deswegen sprechen wir in der nächsten Folge mit Kolleginnen und Kollegen aus dem Stahl-Bereich über das Hinfallen und Aufstehen und darüber, dass Aufgeben gar keine Lösung ist.
Eure Meinung zum Podcast und eure Fragen zum Thema Stahl sind uns wichtig. Also schreibt uns gerne eine E-Mail an [email protected] und lass uns da auch gerne wissen, wie euch der Podcast gefallen hat oder welche anderen Themen wir zukünftig beleuchten sollen. Das war die erste Folge von gekocht, gewalzt, veredelt. Mein Name war und ist Antonie und ich freue mich, wenn wir uns bei der nächsten Folge wiederhören. Bis dann!