As part of the series of tests started in 2016, the experts from thyssenkrupp Steel continuously determined the forming capacity and hardening potential of various hot-rolled steels during flow-forming at a test facility in Duisburg. The result: “The materials from thyssenkrupp Steel occupy pole position among flow-forming steels,” explains Thomas Flöth, Senior Engineer in the Application Technology department. “The extensive tests have shown that the selection of suitable materials and flow-forming parameters for certain applications opens up new possibilities for saving on heat treatments,” continues Flöth. “There are also components where flow-forming can save up to 30 percent in weight - this is particularly important in view of the requirements of electromobility.” The higher-strength hot-rolled strip steels from the established product families perform® and perdur® as well as the hardenable boron steels TBL and precidur® HBL from thyssenkrupp Steel achieved particularly good results on the test line.
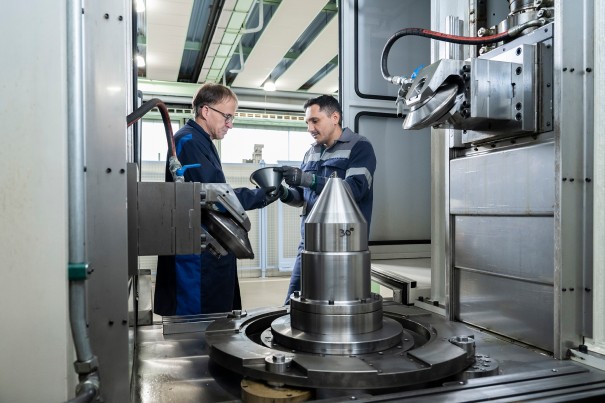
In the future, flow-forming as an innovative process in combination with the right material can make a significant contribution to the sustainable production of geometrically demanding components in the automotive and industrial sectors (see info box). Due to the low tool costs, the very high degree of forming and the possibility of producing even complex geometries with undercuts, flow-forming is also a good alternative to traditional deep drawing or forging. The know-how gained through intensive research in recent years will give Duisburg's application technology a unique selling point in the future when it comes to material differentiation for flow-forming. Like no other supplier in the European steel industry, Thomas Flöth's team is able to provide its customers with comprehensive advice and support individual product development with new processes and grades.