Premium quality and outstanding service
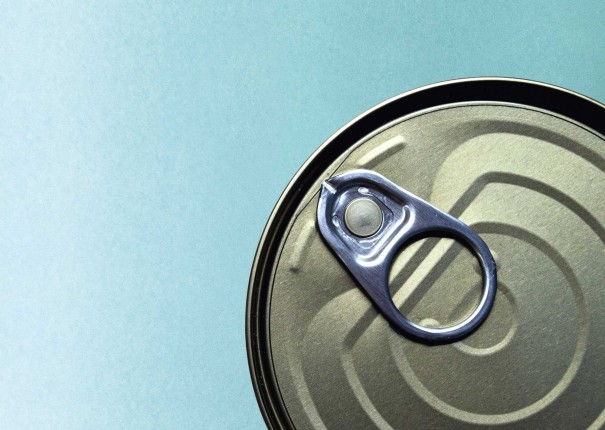
This property is particularly important in the production of food cans that are opened using a pull tab. The “rivet” is what is essential here. This component connects the lid to the pull tab and should not detach as soon as you pull it. At the same time, the packaging steel has to be malleable and pliable enough for the rivet to be formed from the very same piece of material as the lid and for the lid to be effortlessly pulled from the can. This means that the material has to be both solid and flexible – or in other words, “Solidflex!”
2. A safe material
Alongside the aforementioned cans for foodstuffs with full tear-off lid („easy open end“, to use the technical term), rasselstein® Solidflex is particularly suitable for manufacturing aerosol cans. The specially designed bottoms and lids of spray cans are ideal applications for this material from Andernach.
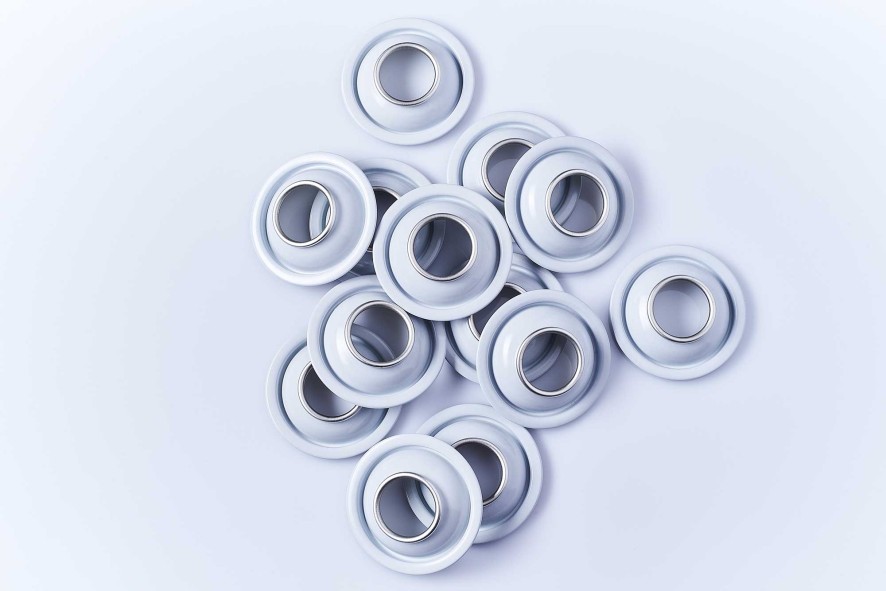
From deodorant and hairspray, to spray bottles for perfume and room scents, right through to spray foam for ovens and acrylic paint for furniture and cars – tinplate packaging is an essential part of everyday life. However, manufacturers may only bring aerosol cans on the market under special conditions according to EU law. Depending on the product that is being sold, it stipulates the exact pressure the spray can has to ensure before it “fails.”
This “deformation pressure” is desirable, as it serves as a warning for the consumer. It can be seen from the lid and bottom of the can slowly – but safely – bulging outward. This means that you don’t have to worry about cans exploding, as the consumer’s safety takes top priority.
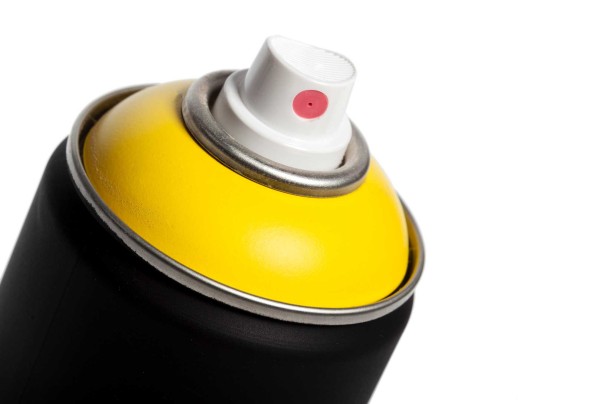
3. A sustainable material
rasselstein® Solidflex is considerably stronger than the material that has been used for spray cans up to this point. Its expansion behavior is different from conventional material. Its higher strength makes its components more stable and means that they can be produced from thinner material. This allows more cans to be produced using the same quantity of tinplate.
Not only that, but spray cans made from rasselstein® Solidflex are lighter than conventional aerosol cans. This results in a weight reduction of up to 14 percent compared to standard spray cans.
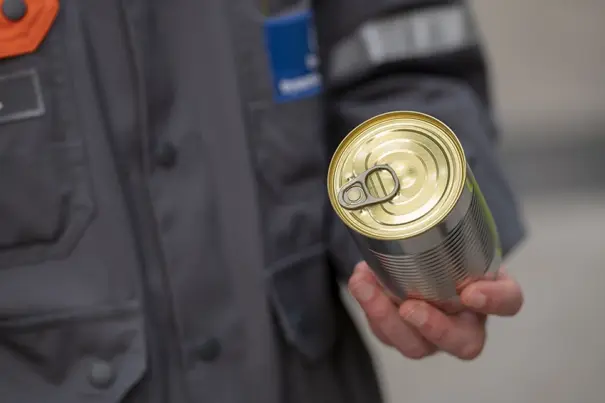
A reduced material requirement and lower weight also make for an improved CO2 carbon footprint. thyssenkrupp Steel therefore commissioned a study from Sphera Solutions that calculated and substantiated precisely that. The results of the external study conducted by Sphera Solutions were subsequently verified and confirmed in a critical review conducted by TÜV Süd. "Sphera Solutions conducted the study in line with the requirements of ISO 14040 and ISO 14044. The study covers the production of the packaging steels under consideration according to the cradle-to-gate principle: that means starting with the mining of the ore and ending with the finished packaging steel at our plant gate, as well as the use of the material in the can," explains Dr. Linda Kerkhoff, a development engineer in Materials Technology.
In terms of scope, the study considered, for one thing, commercially available food cans with a filling volume of 425 grams, a diameter of 72 millimeters and a height of 110 millimeters. It also focused on aerosol cans with a rim-full volume of 378 milliliters, a diameter of 52 millimeters and a height of 190 millimeters. Result: comparing the baseline and optimization scenarios clearly showed the potential for CO2 emission savings.
rasselstein® Solidflex reduces weight
In a first step, the thickness of the Easy Open End of food cans was reduced in the calculations using rasselstein® Solidflex. The total weight of the food can was thus reduced from 48.45 grams to 47.49 grams. This represents a 1.98 percent weight reduction. In a second step, the thicknesses of the body and bottom of the can were additionally reduced by using suitable innovative packaging steel grades. This allowed an even higher difference to be achieved: in absolute figures, a weight reduction of 6.55 grams thanks to the use of rasselstein® Solidflex in the Easy Open End.
The results in the optimization scenario for aerosol cans were similarly impressive with the weight of the can demonstrated to be reduced by more than 14 percent. Many of the customers produce very high volumes of the cans that were under consideration. Using rasselstein® Solidflex means that significantly less material is required in the manufacture of these cans. The overall material savings are therefore enormous, and that without compromising on the important quality features of safety and stability.
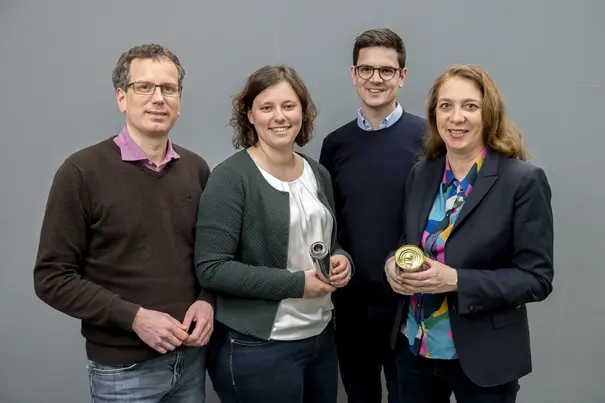
In the short term, the aspect of CO2 savings going hand in hand with the lighter weight enabled by rasselstein® Solidflex is already set to become a decisive factor in the industry. "Thanks to the innovative material, we are not only reducing weight but also improving the carbon footprint of each can," explains Dr. Blaise Massicot, development engineer at thyssenkrupp Rasselstein. The Sphera study shows that CO2 savings of 2.14 percent have already been achieved in the first optimization scenario for food cans – i.e. simply by using rasselstein® Solidflex in the Easy Open End. "In the second optimization scenario – when innovative packaging steel grades are used for the entire food can – the figure was as high as 13.52 percent. This corresponds to a reduction of 18.435 grams of CO2 per can. Looking at this value, you can imagine the level of CO2 emissions that can be saved given the number of cans that are produced every year." The study also showed significant savings of more than 14 percent in CO2 emissions for aerosol cans. This corresponds to a reduction of 21.955 grams of CO2 per can.
It reduces the weight of the spray can, while keeping it stable, safe, and, of course, sustainable. This is made possible by a new extremely strong material that also boasts very good forming properties. Thinner material thicknesses can be used, while stability remains consistent.