The decoiler serves to unwind the coil, it is suitable for coils with an inside diameter of 600 to 880 mm.
Hot strip cut-to-length line
All production steps on the state-of-the-art hot strip cut-to-length line are perfectly matched to allow plate to be cut from coils of high-strength, wear resistant steel.
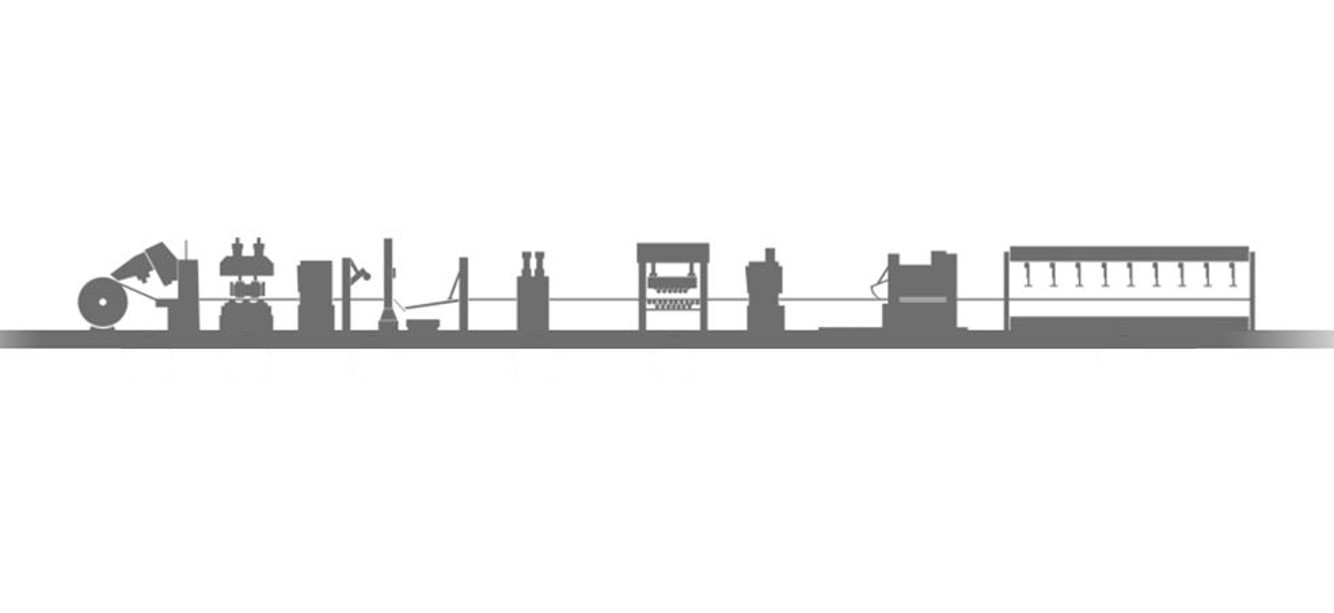
The first leveling operation ensures the finished plates display good flatness and low residual stresses.
The first brushing machine is used to remove loose scale. This serves to reduce dust so as to prevent indentations in the surface during the precision leveling process.
Here scrap material is removed from the ends of the coil.
The double trimming shear serves to trim the coil edges. A width tolerance of 2 mm can be achieved.
Three leveler cassettes with different roll diameters and roll numbers are available for different thicknesses and grades. They are used to ensure the finished plates are flat and stress-free.
The second brushing machine is used to remove loose scale after precision leveling. Reducing the steel dust optimally prepares the plates for laser processing.
Here the coil is cut into plates of 1,000 to 16,000 mm in length. Closer than standard length tolerances can also be agreed.
The stacker is used to stack the plates into packs. A vacuum lifter transfers the plates from roller table to stack to avoid magnetization and guarantee an outstanding, scratch-free surface.