Decommissioning the casting-rolling line and replacing it with new equipment during the conversion work is like open-heart surgery and has far-reaching effects on the entire production network. At the same time, it demonstrates the top performance of the entire team, which ensures that the new systems are completed smoothly and on time.
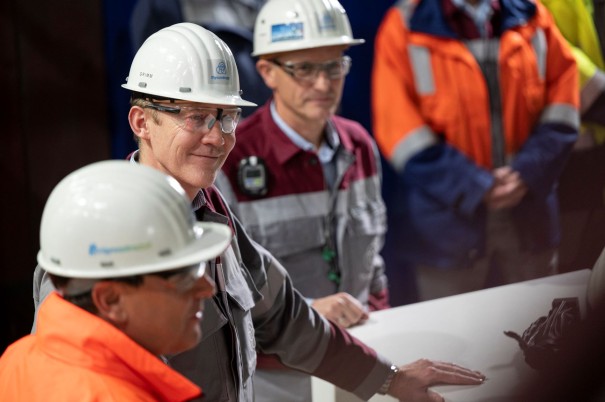
“As planned, we are continuing to make targeted investments to strengthen our Duisburg site,” explains Dennis Grimm, Spokesman of the Executive Board of thyssenkrupp Steel. “With the fundamentally modernized hot strip mill 4 and the conversion and new construction of continuous casters 3 and 4, we are setting the course for our future viability, especially in terms of efficiency and profitability. By separating and converting our casting-rolling line, we are making our production network more flexible and increasing the availability of our systems. We are thus preparing ourselves for the future requirements of our customers in target markets that are important to us, such as mobility and energy.”
By optimizing the production network, thyssenkrupp Steel is further aligning its product portfolio to future markets and profitable premium products. These include multiphase steels and lightweight steels as well as grades with high surface quality. In addition, the production of high-quality electrical steel grades, which are indispensable for the energy and mobility transition, will be strengthened.
Technical details and innovations
On 2 April 1999, the casting-rolling line produced the first coil and on 20 August 2024 - just over 25 years later - it reached the 40 million tons of steel mark. The material was used, among other things, in the magnetic rails of the Transrapid in Shanghai, which were built entirely from GWA material. In future, thyssenkrupp Steel will continue to produce a large proportion of dynamo and transformer material for NO and GO grades in the new WBW 4. GWA also stands for scalur® - the pickled hot-rolled strip with extremely narrow thickness tolerances, which will also be produced at WBW 4 in the future. In addition, the hot strip mill will take over the high-strength grades from Bochum.