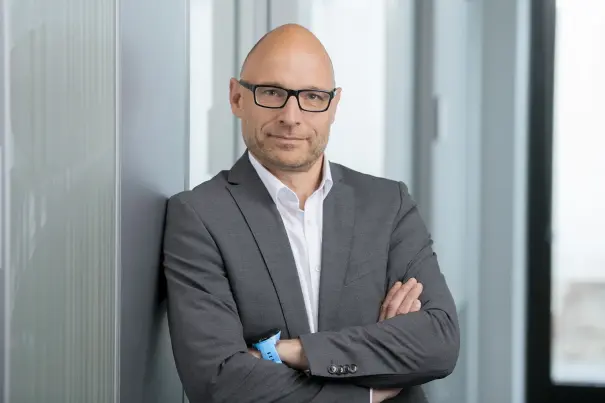
The production of green hydrogen is a central component of the energy transition. Just this summer, the German government reaffirmed the key role of electrolysis in its adapted National Hydrogen Strategy: by 2030, Germany is expected to possess 10 gigawatts of installed electrolysis capacity to meet the growing demand for green energy, at least in part from its own production. 2030 is an ambitious target in terms of time, says Dr. Jens Mathiak, Head of Sales for green hydrogen at thyssenkrupp nucera: "In plant engineering, we start planning big projects four to five years in advance. So there's a maximum of three years left to lay the groundwork for achieving 10 gigawatts."
Strong sales growth
The electrolysis specialist from Dortmund knows what he is talking about. For more than 50 years now, thyssenkrupp nucera – the former Electrolysis division of thyssenkrupp Uhde – has been planning and implementing projects with its partners worldwide. The many years of experience gained in chloralkali electrolysis form the basis for the second major area of activity: alkaline water electrolysis, in which water is split into hydrogen and oxygen by applying electrical voltage.
Business is booming: for example, sales in the water electrolysis sector increased almost tenfold in the first nine months of the year compared with the same period of the previous year. The stock market newcomer has already signed binding contracts for more than three gigawatts of capacity. This includes a plant with more than 2 gigawatts in Saudi Arabia, one of the world's largest projects for the production of green hydrogen. And in Germany? "Here, we are still in the starting blocks," says Jens Mathiak. "Large plants in particular are currently being implemented in countries where green energy sources can be developed cheaply and without too much red tape, and where there is little demand for electricity."
Favorable locational conditions
Nevertheless, the expert thinks Germany offers potential as well, because the ideal location for water electrolysis should fulfill two factors: proximity to the green power source and proximity to the consumer. "These were the very principles that made the steel and chemical industry so big in the Rhine-Ruhr region. Energy-intensive industries were located where the energy was available." Today, in the age of decarbonization, the industrial center of North Rhine-Westphalia benefits from its proximity to the Dutch ports with their convertible LNG terminals, a growing network infrastructure for future hydrogen transportation, and the wind farms of the Netherlands and northern Germany. In addition, the construction of local electrolyzers will become more attractive as plant and operating costs fall.
Powerful standard modules
Companies are already benefiting from the high scaling effects and standardization of thyssenkrupp nucera's electrolysis technology. "Manual labor was yesterday, today we're ready for product-oriented mass production," says Jens Mathiak. "This is what our cost-effective Scalum® standard module stands for. Not only does it have a high current density, it can also be scaled as desired." Scalum® is currently one of the largest electrolysis modules available on the market. A single module has an output of 20 megawatts and is designed to be easy to install and connect. In this way, thyssenkrupp nucera's electrolyzers are not only suitable for very large projects, but also harmonize with supply concepts that are close to the consumer, such as in the "Carbon2Chem" project.
That leaves the question of operating costs. For Jens Mathiak, one thing is clear: for electrolysis projects to be realized in Germany in the future, the prices paid by industry for green electricity will have to fall. Meanwhile, the company is working flat out to expand its own production capacity – from the current one gigawatt to five gigawatts per year.