Direct reduction plant: New building is uncharted territory
The people working in various positions at thyssenkrupp Steel to prepare for the transition to hydrogen-based steel production are well aware of the scale of the undertaking. One of them is Markus Wischermann. He is an engineering graduate, and was previously responsible for hot metal production at thyssenkrupp Steel. In spring 2023, he took over project management for the building of the first direct reduction plant. Markus Wischermann likes to step into uncharted territory. Ensuring that the new-build project, which is so important for the future of the steel industry, is well planned and coordinated with the various sections from the very beginning is right up his street.

"Specifically, we are currently coordinating the preparatory work on the construction site. This includes the official permits we need so that we can lay the foundations of the plant soon," says Wischermann. "Above all, our task is to bring everyone involved in the project together consistently and regularly, and to fit the giant project into a very focused process structure. In this way, we'll make sure that everyone involved knows exactly what to do during the peak phase."
Speaking of the peak phase ... ... it takes a bit of imagination to grasp the pace with which construction of the first direct reduction plant at the harbor site in Duisburg-Walsum will proceed from January 2024 onward. Within three years, an industrial complex will be built on the huge brownfield site on the bank of the Rhine, which at its highest point will almost rival the spires of Cologne Cathedral. However, the grayish-brown soil still dominates the scenery here between the striking cooling tower of the nearby power plant and the extensive Schwelgern steelworks site. Only a few excavators can be seen digging up and removing the last remnants of the former slab warehouse.
Transformation: Planning is the be-all and end-all
That will change in 2024: up to 1500 people from a range of companies will then be working in parallel on the construction site for three years. "Those are the SMS group employees who will be responsible for building the plant and designing the technological details. That company is also the prime contractor who not only lays the foundations, but also plans and implements all other buildings on the site. And then they are joined by colleagues from our own companies who, for example, plan roadways and warehouses to supply the plant with energy and materials," says Markus Wischermann. "Coordinating these people and making sure that every single step is well planned out in advance is a daunting task, just as much as making certain that everything runs smoothly in terms of occupational safety, too."
Markus Wischermann also needs a good imagination: Where exactly will the required material be landed at the harbor? What will be stored temporarily? What maintenance processes need to be considered when it comes to designing the roadways and buildings? The coordinator participates in the regular meetings that are held in the Green Transformation Office in order to answer all these questions not only at an early stage, but also competently. This is where teams from different departments meet to coordinate and keep each other up to date. To accompany this, thyssenkrupp Steel keeps the neighborhood informed about the progress of the project in regular citizen meetings.
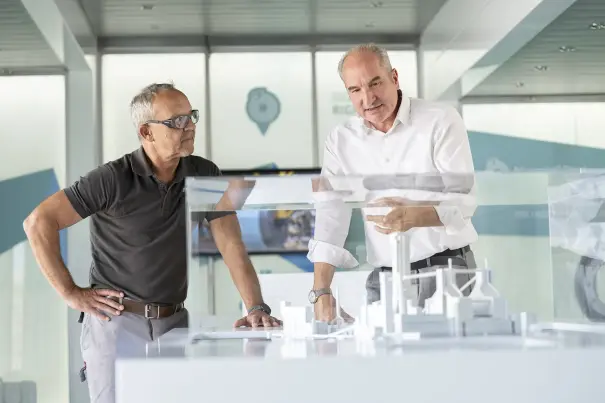
Dr. Matthias Weinberg represents the technological perspective in the transformation project. The head of the Metallurgy Competence Center and his staff are working on the fundamentals for hydrogen-based operation of the DR plant, and the connected melting units. The fact that the eleven colleagues are primarily known in-house as "Ocean's Eleven" shows Matthias Weinberg that the HR department did a very good job in selecting the team members. "We bring together a fair bit of expertise, including chemistry, metallurgy, general engineering, process and electrical engineering," explains the materials specialist. "This broad perspective is very important in answering novel and complex procedural questions."
At its core is the question of how the hydrogen behaves in the reactor. To this end, the experts are conducting extensive series of tests to determine the influence of different charge materials on the reaction rate, and ultimately on the quality of the end products. "You have to remember that a direct reduction plant of this size has never been run on hydrogen before," the metallurgist reminds us. thyssenkrupp Steel calls it the "first of its kind", as this is the first time that this combination of DR plant with melters is being implemented anywhere in the world.
The DR plant technology itself, on the other hand, has been in use all over the world for decades already. In the 1980s, thyssenkrupp Steel, too, operated a direct reduction plant which produced 100,000 metric tons of hot metal every year. It ran on natural gas. "Hydrogen has always been considered an expensive energy carrier, and has therefore only been used in academic research," says Weinberg. "Consequently, for some time now we have been looking into all the conceivable risks associated with the development that operation with hydrogen could entail. We are investigating some of these issues in our in-house laboratories. For others, we need a larger scale, because that's the only way to get transferable results. Until our own test facility is up and running, we are working with partners on whose facilities we are able to run specific test series in real operation."
Specific knowledge of hydrogen required
Another focus of the team's work is to transfer findings from the use of melters to hot metal production. In this case too: the melting process itself is not new, but the context in which it is used is. Matthias Weinberg: "Unlike traditional electric arc furnaces, which are operated in batch mode, we are dealing here with the continuous melting of directly reduced iron using electricity. Tapping of the molten metal and slag will also be required, like in the blast furnace."
In non-ferrous metallurgy, one of the applications of the process involves producing alloys from different metals, including ferro-nickel or ferro-manganese. These latter are compounds that produce a significantly higher proportion of slag, among other things, compared with the iron ores from the direct reduction plant. In other words: when melting hot metal, essential process parameters have to be readjusted. Matthias Weinberg is nevertheless convinced: there is no better solution than the combination of direct reduction and melting units chosen by thyssenkrupp Steel. This is because, compared to other processes, slags do not cause problems for the smelters. This in turn means that the compact units can cope with different grades of iron ore. "Consequently, we are not dependent on buying only particularly high-quality iron pellets.
And that's good news, because there's already a bottleneck looming in this market which is ramping up the price pressure." Rather than investing in special ores, the steel producer is devoting resources to building up special expertise. "We need people to work out the fundamentals and boundary conditions for the new process to be used efficiently," says the head of the Metallurgy Competence Center. "Smart people who can work as pioneers and are skillful enough to approach new challenges in a systematic way. Above all, however, we need engineers and technicians who are good at passing on their knowledge to others. After all, working with hydrogen is a demanding challenge and everyone in the company needs specific knowledge for this. From the Executive Board right through to the colleagues in the control room who are responsible for the day-to-day operation of the plant."
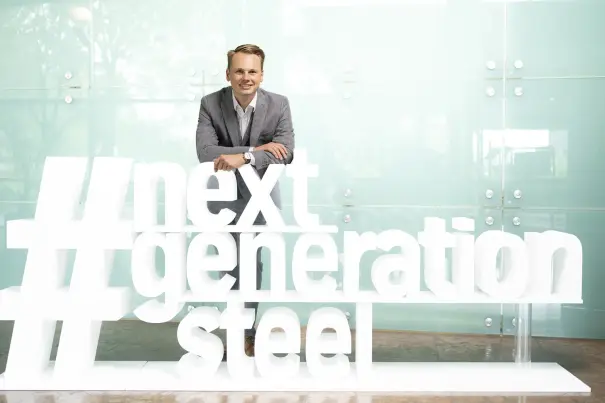
Hydrogen. The energy carrier of the future already plays a central role in Henning Weege's day-to-day work. As Head of Hydrogen & Green Energy, one of his tasks is to meet his employer's hydrogen needs by purchasing as many of the green molecules as possible. The official tendering phase will start shortly at thyssenkrupp Steel. "Our goal is to sign binding contracts next year. Then, the suppliers have a good three years to build up the corresponding production and transport capacities," says Henning Weege.
When changing over, thyssenkrupp Steel will be able to exploit its locational advantage in the heart of the Rhine-Ruhr industrial triangle. Here, energy producers and consumers have been working hand in hand for decades close to former coal mines. Consequently, there is already an extensive network of natural gas pipelines in the region, through which hydrogen will also be piped to customers in the future. "The first publicly accessible hydrogen network in Germany is currently being created here under the name GET H2," says Henning Weege. "It runs from Lingen in Lower Saxony to Gelsenkirchen. In the future, wind and solar power will be used for producing green hydrogen at the starting point, which will then be transported to industrial customers in the Ruhr region."
GET H2 (see info box) is just one building block in the Germany-wide core hydrogen network which is currently being designed by the transmission system operators, and will be formally approved by the German government in the fall of 2023. The network is expected to connect all major hydrogen infeed sources to their industrial consumers by 2032, and 60% of it is expected to consist of converted natural gas pipelines. Gaps are being filled by new construction projects. This also includes the DoHa hydrogen pipeline: a 25-mile pipeline between Dorsten and Duisburg-Hamborn, which thyssenkrupp Steel is integrating into the new regional hydrogen network. Less than four years have been scheduled for its implementation, DoHa is expected to enter operation in 2027. The timetable dovetails with the commissioning of the DR plant, which is planned to run on 100 percent green hydrogen from 2029 onwards, after a gradual conversion phase.
Hydrogen economy: "We've got to start now"
In the meantime, the rules of the game for hydrogen supply must also be established. Among other things, there is a need to clarify the level of the grid fees as well as the question of who bears the risks in the area of grid build-up. Henning Weege: "Just as we have no guarantee that the market will actually buy our green steel, the network operators are now obliged to put their money on the table in advance. This requires regulatory rules of the game that make the market fair and transparent for all participants alike." For himself and his colleagues, the strategist hopes above all that there will be a steady and stable supply of hydrogen. This in turn means that there must be sufficient storage capacity within the infrastructure to compensate for fluctuations in the production of green energy. "Otherwise, we would have to switch to blue hydrogen during the transition to compensate for the volatility."
Despite the imponderables of the planning process, Henning Weege is pleased with the many small and large steps he has already taken together with his colleagues in the Green Transformation Office. Will everything run as smoothly as planned? Of course it won't. "But I'm convinced that we've got to start now if we're going to see all the upcoming problems at an early stage, and find solutions," he says, optimistically. "We're very well prepared for that."