For the first time, customers are now also being offered scalur®+Z as a climate-friendly bluemint® variant. The advantage: by using the CO2-reduced climate steel, customers can count the reductions achieved in production towards their Scope 3 emissions and offer their customers more sustainable products. And they can do so without restrictions, as there is no change to the production routes, the outstanding product quality and the proven processing procedures. In addition, thyssenkrupp has invested in new simulation tools around roll forming. "The computer-aided processes provide designers with information on, for example, which geometries are feasible and how thick or strong a material needs to be for the planned further processing and production properties," explains Roger Hannig, Team Leader Technical Customer Support SSC automotive at thyssenkrupp Steel. And all this without having to carry out time-consuming and costly real-life tests prior to practical use.
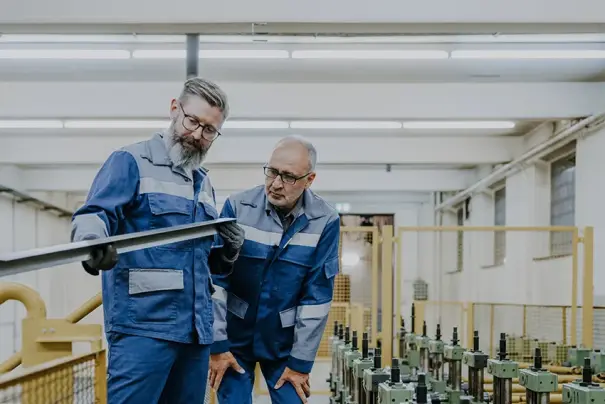
Steffen Jaekel, development team leader at furniture hardware manufacturer Hettich, which sources its materials – including most recently sustainable scalur®+Z in bluemint® quality – from, among others, the steel service center Flachstahl Werl of thyssenkrupp Steel, explains why these characteristic values are so important: "In order to optimize our products, we need to know exactly how a material behaves under certain conditions. In order to simulate this reliably, we need, above all, precise material characteristic values. This is the only way we can guarantee the process accuracy in production that is crucial for our business." After all, as a renowned supplier to the kitchen industry, Hettich cannot afford any errors. The company's customers include well-known brand-name manufacturers, some of which deliver more than 5,000 kitchens per week. Ten or more drawer and runner systems designed by Hettich per kitchen quickly add up – high-quality and precisely processed materials are the be-all and end-all.
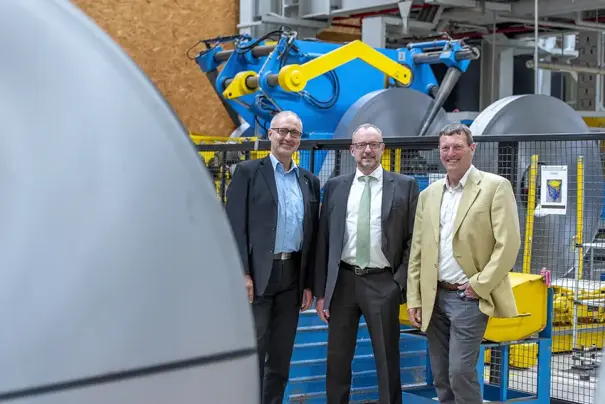
Hettich's optimized and efficient production processes owe much to the characteristic values for simulation generated at thyssenkrupp Steel. A circumstance to which the traditional family business from Kirchlengern itself has contributed a great deal. Both companies have been working together for many years in the field of materials analysis and product development. Specialist departments, simulation teams and materials professionals are in close contact. "Some time ago, we were struggling with cracks in the material of our drawer guides in the rails," recalls Steffen Jaekel. To find out the reason, Hettich and thyssenkrupp Steel set up targeted joint analysis processes at that time.
In the course of this, it was first possible to find the cause of the problems, which were then later successfully rectified. The project was the prelude to the cooperation that continues to this day and benefits all parties involved. Jaekel: "The cooperation – and in particular the determination of characteristic values at thyssenkrupp Steel – gives us a better calculation basis for product development. That has helped us enormously. Even though we at Hettich have positioned ourselves very well in terms of simulation over the past ten years: We don't have the capabilities of thyssenkrupp Steel with its gigantic test lab like this."
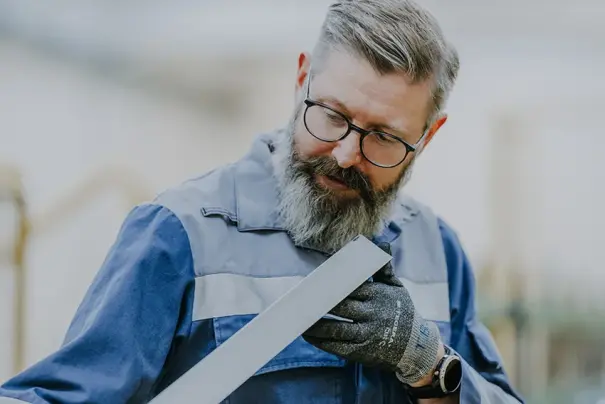
An additional competitive advantage for Hettich's roll-formed telescopic rails is the fact that the slit strip supplier Flachstahl Werl (FSW-Industrials) means another partner is involved in the process chain at an early stage. FSW divides the supplied steel into narrow strips for subsequent processing, thus forming an important link between steel production and subsequent finishing. "Because we are in continuous close coordination with thyssenkrupp Steel with regard to Hettich's special requirements, we can provide highly specific slit strip products at the time of delivery that differ in quality from conventional products," explains Sascha Zimmermann, sales manager at Flachstahl Werl. Zimmermann continues: "This three-way constellation, in which thyssenkrupp Steel, FSW and Hettich work hand in hand, has proven its worth and developed successfully in recent years. Last but not least, this also benefits the furniture industry's end customers."