Daily press, Trade press, 2014-10-20, 08:00 am
Europe’s biggest blast furnace relit: “Schwelgern 2” producing iron again
Continuous caster also modernized – Economics minister Duin: “Positive signal for NRW”
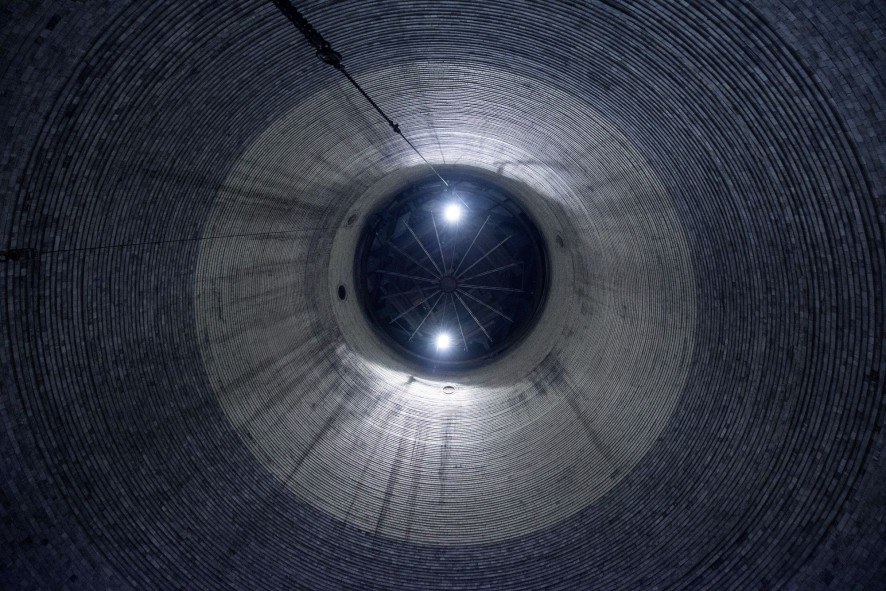
The fire is lit, blast furnace No. 2 in Duisburg-Schwelgern is back in operation. For three months production had been halted to carry out necessary modernization work. Now the furnace hearth has been filled with wood and coke and relit, and iron production in Europe’s biggest blast furnace has been gradually ramped up. Continuous caster No. 1 in Beeckerwerth, one of three continuous casters in the north of Duisburg, has also been modernized. Its revamp took place in parallel with the work on “Schwelgern 2” in order to minimize disruptions to the production chain. Now both units are back in operation.
Second campaign has begun
Up to the production stoppage in June “Schwelgern 2” had produced around 78 million tons of iron since it started operation 21 years ago, making it one of the top ten blast furnaces in the world. The major modernization process included replacing the furnace’s roughly two meter thick refractory lining, requiring more than 7,000 tons of refractory material. In addition the furnace cooling system was optimized, the cast house was renovated and repairs were carried out to the hot blast stoves, gas cleaning system, slag granulator and expansion turbine.
The relining was a logistical tour de force. At times 1,000 ThyssenKrupp and contractor employees were working in parallel on the site. The modernization involved investment of around 200 million euros in total. Now blast furnace No. 2 has begun its second campaign, producing around 12,000 tons of iron a day at temperatures of more than 2,000 degrees. Twenty years from now it will be time for a new reline.
Minister Duin emphasizes importance for Duisburg and NRW
“The relighting of blast furnace Schwelgern 2 by ThyssenKrupp is a positive signal for North Rhine-Westphalia. The extensive investment needed to modernize the blast furnace and other production units like the continuous caster shows that the company is committed to NRW and to Duisburg, Europe’s biggest steelmaking city,” said NRW economics minister Garrelt Duin at the relighting ceremony.
Modern cooling system on continuous caster improves slab quality
Together with the blast furnace in Schwelgern, continuous caster No. 1 in Duisburg-Beeckerwerth has also restarted production following a 90 million euro modernization. This project had to be carried out while a blast furnace was out of operation as otherwise the production losses would have been too great. The iron produced in the blast furnace is converted into steel in the melt shop, which is subsequently cast continuously into rectangular slabs and then further processed. The modernization included the replacement of the complete casting machine and investment in a new ladle turret and tundishes plus tundish cars. The aim is to optimize the cleanness of the steel and meet the increased requirements of customers such as auto manufacturers.
In addition a new technology for cooling the hot steel strands has been introduced. The new air/water cooling system allows much more precise and gentler cooling of the slabs than the water-only system previously used. Thanks to close temperature control, edge defects in the slabs, a major challenge in continuous casting, can now be reduced to a minimum, resulting in better surface quality both of the slabs and of the coils produced from them.
Modernization projects improve competitiveness and sustainability
“With the revamp of blast furnace No. 2 and the modernization of continuous caster No. 1, we now have two state-of-the-art units back at our disposal,” says Dr. Herbert Eichelkraut, member of the executive board of ThyssenKrupp Steel Europe responsible for production. The measures have not changed the production capacity of the two units. “We have achieved major improvements in efficiency and in the quality of our products, which will further strengthen our competitiveness and sustainability,” he says. In addition to necessary maintenance measures, ThyssenKrupp Steel Europe is making investments that will help differentiate it through innovative products and intelligent solutions and so open up attractive markets and applications with promising growth opportunities.
“Our employees deserve great credit for their enormous efforts in making these two challenging projects a success,” says Dr. Eichelkraut. “Considering the number of people on the site it is also particularly pleasing that no significant accidents occurred.”
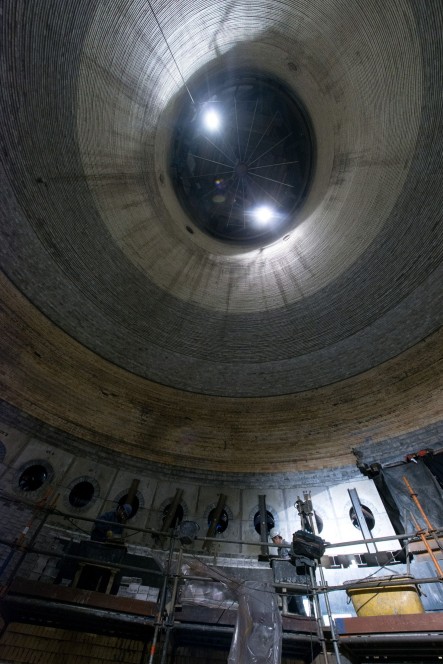
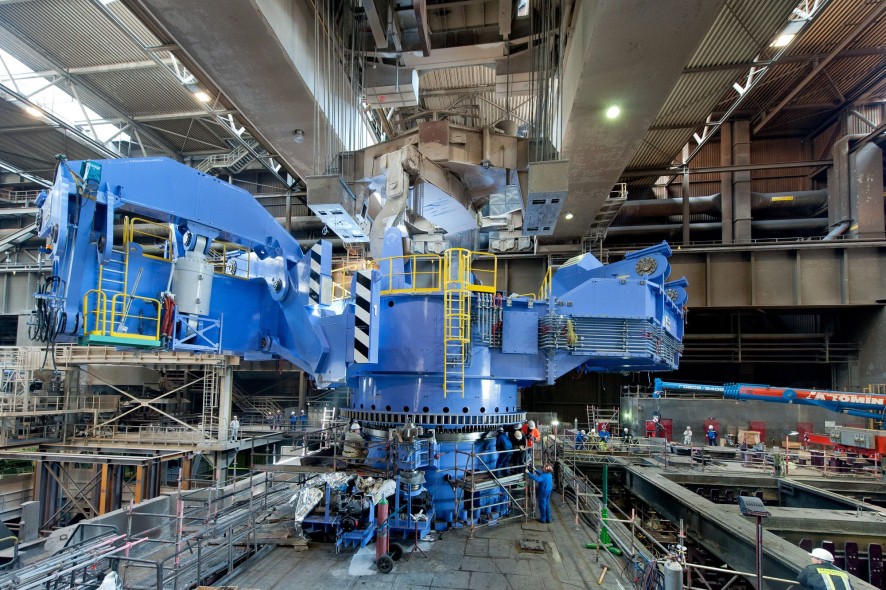