Daily press, 2019-09-27, 10:30 am
Forever young: thyssenkrupp’s BOF meltshop in Duisburg turns 50
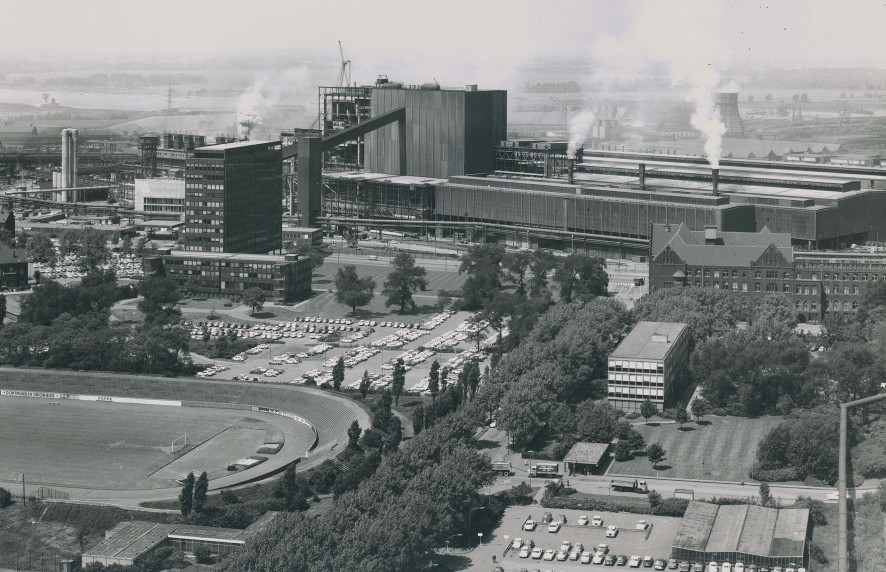
Innovation, entrepreneurial vision and forward-looking technology: on September 29, 1969 the Duisburg-Bruckhausen basic oxygen steelmaking plant began operation as one of the world’s biggest and most advanced meltshops – a milestone in modern steel production. Constructed on the same site where company founder August Thyssen built his first open hearth furnace in 1891 and first basic Bessemer plant shortly afterwards, it is still in operation today. Since its first heat the plant has produced almost 190 million tons of steel, enough to build around 21,000 Eiffel Towers.
Quality, quantity and profitability
The BOF meltshop in Bruckhausen was built with the aim of producing large quantities of high-quality steel cost efficiently. Using innovative technology the two top-blown oxygen converters produced steel of outstanding quality at high levels of productivity and profitability. “Our predecessors showed great vision, investing 50 years ago in the steel of today,” says Thorsten Brand, head of crude steel operations at thyssenkrupp Steel. “From the very start the Bruckhausen meltshop was regarded as one of the most advanced in the world. Then as now it stood for continuous adaptation to rising quality demands and changing customer requirements.” Bruckhausen broke records, producing roughly 380 tons of crude steel every 40 minutes – unparalleled at the time.
Continuous modernization for greater safety and energy efficiency
Since 1969 the Bruckhausen plant has been regularly modernized through targeted investment. In 1979 it was expanded to include a continuous caster, which was upgraded in 1996. A casting-rolling line, ladle furnace and new hot metal desulfurization unit went into operation in 1999 – investments worth the equivalent of 450 million euros. The two original converters, the heart of steel production, were replaced in 2013 and 2014. “This made the blowing process even more stable,” explains Thorsten Brand. “Through precise control of chemical analysis we are consistently improving the quality of our products, which ultimately benefits our customers.”
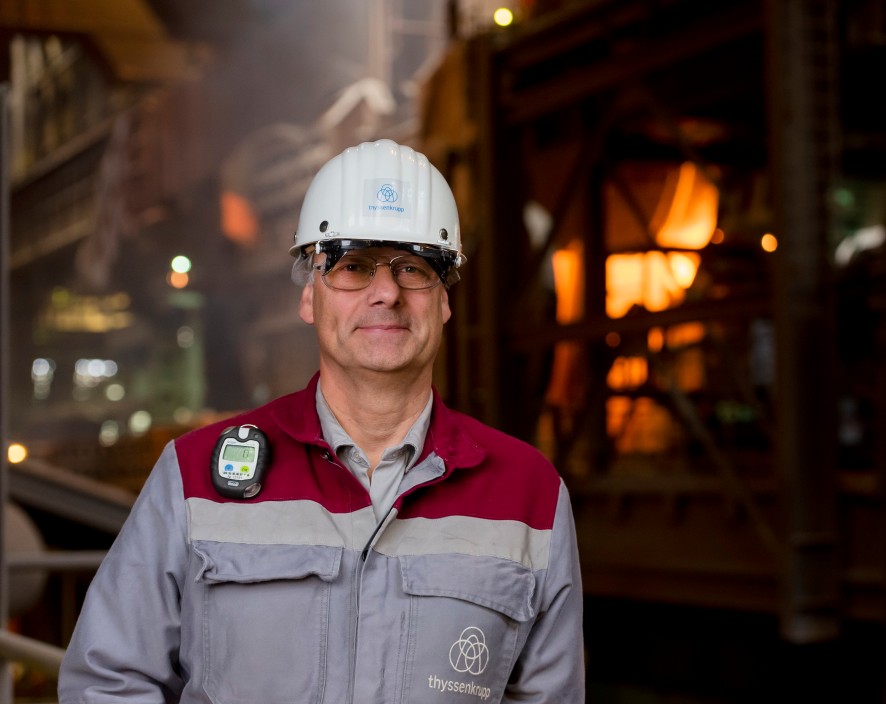
Entrepreneurial vision
The Duisburg steel manufacturer has always had a feel for global megatrends. The potential of digitization and automation was recognized early on. Back in the mid-1980s computer technology was introduced for process control, enabling a decisive leap forward in product quality. Sustainability was also an early focus. When the plant was commissioned, the company opted for a new technology for dust control. The slags arising during the production process were used from an early stage as fertilizers in agriculture or as fillers for road construction. The process gases from the converters are reused, partly to generate steam, partly to produce electricity in the company’s own power plants.
Furnace operator in Bruckhausen: from heavy laborer to process manager
Digitization and automation also improved working conditions in the plant. Until the 1980s, the furnace operators had to do a great deal of heavy physical work under conditions of extreme heat and dust. With automation, the focus of their work shifted to computer-aided control and monitoring of production. This made their work much safer, but also required completely new skills and the willingness to take on more responsibility. In short, the furnace operator’s job profile changed rapidly. Training today is very demanding and has virtually nothing in common with the furnaceman’s apprenticeship of 50 years ago.
Adaptable steel plant: always the right products
Uncompromising adjustments to production to meet changing market and customer requirements were also key to the successful development of the site. Product innovations and new technologies changed the shape of the plant’s customer industries, and customer requirements for steel changed accordingly: new products and production processes demanded – and enabled – more nuanced steel grades with reliable, consistent quality. Production in Bruckhausen became ever more differentiated with more and more customized products. Today, the plant produces around 400 different steel grades. The focus is on tinplate for the food and beverage industry (e.g. for beverage cans and food tins) and high-tech steel for the automotive industry to serve as structural components protecting passengers or to provide high-grade surfaces. The plant also produces precursors for electric steel, a basic material for e-mobility and renewable energies. 50 years after its commissioning, the Bruckhausen plant with its 475 employees is still a central part of steel production at thyssenkrupp.
Facts and figures
Commissioning: September 29, 1969
Construction period: 18 months
Employees*: 475
Capacity*: 5.2 million tons/year
Average heat size*: 375 tons
Equipment*: 2 converters, 2 argon stirring units for secondary metallurgy, 1 RH vacuum unit, 1 ladle furnace, 1 CAS-OB (LTS unit), 1 continuous caster, 1 casting-rolling line
* As at September 2019
Good to know: How pig iron becomes steel
The blast furnaces in Hamborn and Schwelgern supply the pig iron for the DuisburgBruckhausen basic oxygen steel plant. The material is transported to the converters in charging ladles. Pig iron still contains unwanted tramp elements such as silicon, sulfur and phosphorus. The sulfur is removed from the pig iron in an upstream process. In the converters, the other unwanted elements are then removed by top-blowing of oxygen via a water-cooled lance. Steel scrap is added for cooling and the pig iron is “refined” at temperatures of more than 2,500 degrees Celsius. Within about 20 minutes, the iron has turned into steel, still at a temperature of 1,650 to 1,720 degrees. This crude steel is either processed in a continuous caster into slabs or on a casting-rolling line into strip, which is later used, for example, in the automotive industry.