Trade press, Daily press, 2018-11-08, 10:00 am
Major investment project at thyssenkrupp Steel nearing completion: New ladle furnace in the steelworks is now in the trial phase.
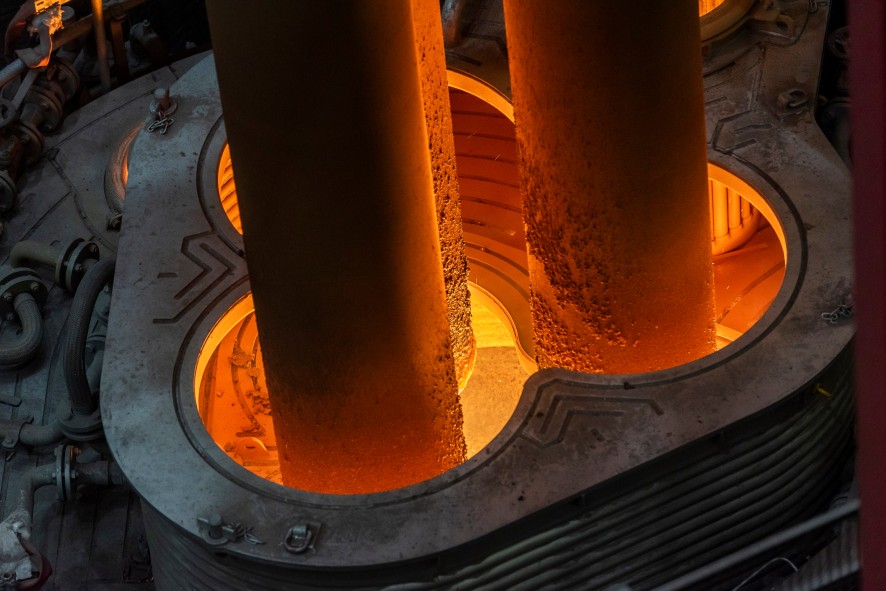
- Strategic investment for the production of high-quality steel grades with optimised degrees of purity
- Signal for the future of the Duisburg location
- Total investment in the high double-digit million range
After a scheduled construction period of a year, the moment has arrived: Smelting is successfully underway at the new thyssenkrupp Steel ladle furnace in Duisburg. A key milestone has thus been reached in this strategically important investment in the steelworks sector. The new double ladle furnace has a capacity of 265 tonnes per smelting process. It is used to produce highest quality, high-alloy steel grades with optimised degrees of purity. "The new ladle furnace will help us to permanently enhance our competitive position," emhasises Dr. Arnd Köfler, Executive Board member for Production at thyssenkrupp Steel Europe. "With the new plant, we are filling a gap in our production network and positioning ourselves even more strongly, especially for premium grades such as those required for high-strength car components and safety features."
Higher process efficiency at lower costs
The ladle furnace was installed in the thyssenkrupp oxygen steelworks 2 and is positioned in the production process between the converter and the continuous casting line. In secondary metallurgy, the aggregate is initially required for alloying and heating the molten mass as well as for desulphurisation. "However, with the ladle furnace project we have achieved much more than just these core requirements," explains Dr. Thorsten Brand, head of steel production at thyssenkrupp Steel. "The plant also contributes to cost optimisation and increased process efficiency throughout the steeworks. In this way, we can reduce the costs of converter operation by enabling higher scrap input, in other words by making the production process more cost-oriented and flexible. Since the molten mass can be heated up or reheated in the ladle furnace, we also save on the refractory lining in the converter because we can lower the tapping temperature. For the same reason, we are able to reduce the afterblow rate in the converter. Finally, we will be able to increase our direct tapping rate, since it is now possible to readjust the melted masses in the ladle furnace using digitally networked data. All in all, the project represents a rejuvenation treatment for the entire steelworks," Brand says in conclusion.
Successful project partnership with plant manufacturer Inteco
thyssenkrupp awarded the contract to build the ladle furnace to... INTECO, the plant builder, who as the general contractor will hand over the turnkey plant. Dr. Harald Holzgruber, CEO of the INTECO Group: "This order marks a milestone in our 45-year company history. We are proud that we have been able to complete this project successfully and on schedule alongside our partners from thyssenkrupp. The plant is equipped with all the technical innovations suitable to help thyssenkrupp remain competitive. In addition, in order to further improve working conditions, the ladle furnace has been completely enclosed with soundproofing panels for sound insulation purposes." In the coming weeks, the new ladle furnace will be specifically tested and comprehensively analysed during trial casting and tested for its functionalities. The plant will then officially become the responsibility of thyssenkrupp.