Trade press, Daily press, 2016-11-28, 04:27 pm
New 100 meter tall stack installed with special crane: thyssenkrupp building world’s biggest sinter plant filter unit in Duisburg
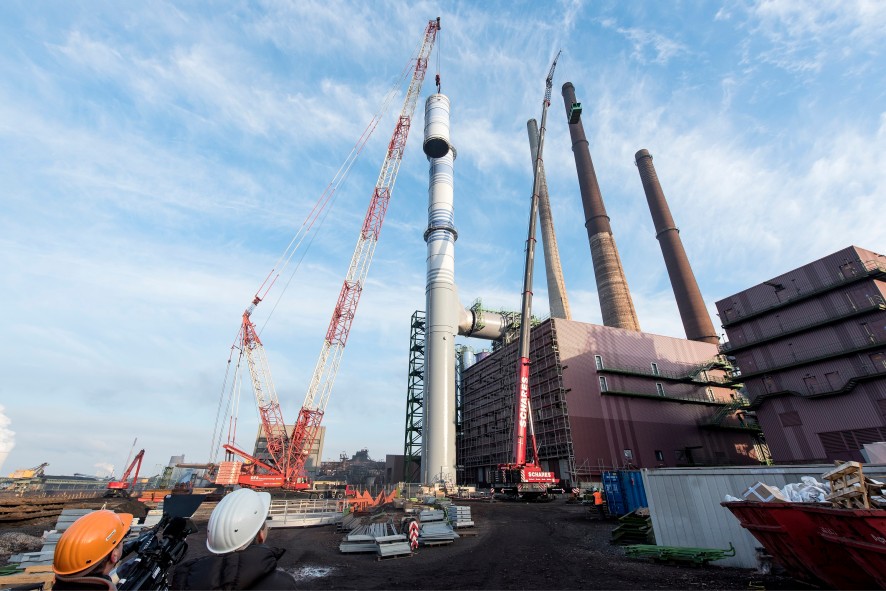
The steel division of thyssenkrupp began building a further modern fabric filter unit at the end of last year. In the future it will provide additional dust collection capacity and further improve the environmental situation in Duisburg. When it goes into operation in early 2017 the new facility will be the world’s biggest sinter plant filter unit. A milestone on the road there has now been reached: the installation of an almost 100 meter tall stack. Split into four pieces weighing a total of around 400 tons, the stack was delivered to the site by ship. A special crane was used to erect the blue and white striped tower. “Our cooperation with the stack manufacturer, the crane builder and the transport company worked so well that we were able to complete the installation on time and without major difficulties,” said Henri Wetzling, process technology project leader at thyssenkrupp in Duisburg. “It means the overall project remains on schedule.”
Four segments weighing a total of 400 tons delivered by ship
Large components for the new dust collector weighing several hundred tons in total have been delivered to the site on several occasions over the past few months. This time it was the stack, which was transported from Emsland in four parts. Due to the size of the segments – each 27 meters long and almost six meters in diameter – transport by road was out of the question. Even the journey by ship was tricky in parts due to bridge heights. Upon arrival at Schwelgern port the steel components were unloaded and assembled on site. Due to the huge height of the stack the boom of the 70 meter special crane had to be extended. The stack is part of a dust collector currently being built for the biggest of the three sinter belts in the Schwelgern works unit. When the fabric filter unit goes into operation in 2017, the new stack, which will be hardly visible outside the thyssenkrupp site, will replace a more than 250 meter high brick tower in the north of Duisburg.
New dust collector further improves environmental situation in Duisburg
The modern fabric filter unit will further reduce dust pollution in the area. It will be capable of capturing almost 99.99 percent of the sinter dust, which means the air behind the filters will be really clean and there will be less dust in Duisburg and the surrounding area. The unit is attached to the sinter plant, in which fine iron ores are mixed with coke, lime and other materials and heated to form a sinter cake. The mixture is crushed and then cooled. Because of its permeability the finished sinter is ideal for charging in the blast furnace, where it is melted together with other materials to produce pig iron. Making the ore-coke cake requires suction air, which subsequently contains dust. Up to now this dust has been captured by several conventional electrostatic precipitators, preventing it from escaping into the atmosphere. There is already one downstream fabric filter for the smallest of the three belts in the Schwelgern sinter plant. There the air which has previously passed through an electrostatic precipitator flows through around 15,000 three meter long extremely fine fabric bags, which capture even very fine dust. This fabric filter went into operation in fall 2011 and cleans up to 450,000 cubic meters of waste air per hour. By 2014 the steelmaker was already emitting around 20 percent less dust than in 2010.
46 million euro investment – third fabric filter to follow
Based on its good experience with the first fabric filter the steel division of thyssenkrupp is now installing filters using the same technology for the two other sinter belts. With the installation of the stack, the construction of the filter for the biggest sinter belt has moved a big step forward. thyssenkrupp is investing around 46 million euros in the project, which will reduce dust emissions substantially. The third fabric filter is scheduled for completion by the year 2020.